- お役立ち記事
- Tips for dealing with die casting defects and defects
月間77,185名の
製造業ご担当者様が閲覧しています*
*2025年2月28日現在のGoogle Analyticsのデータより
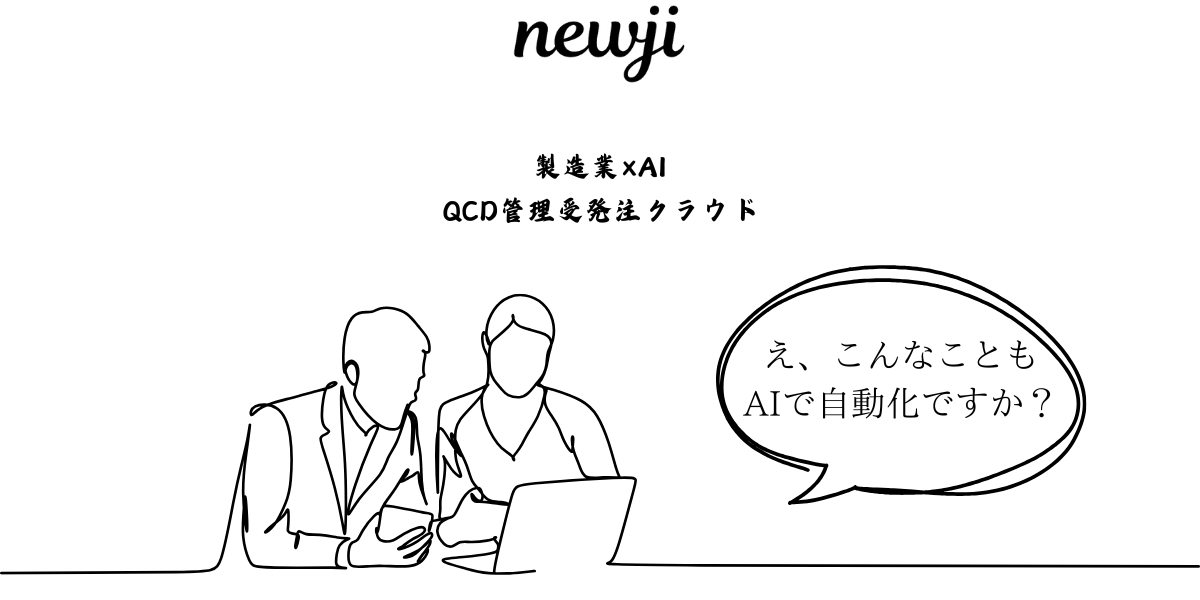
Tips for dealing with die casting defects and defects
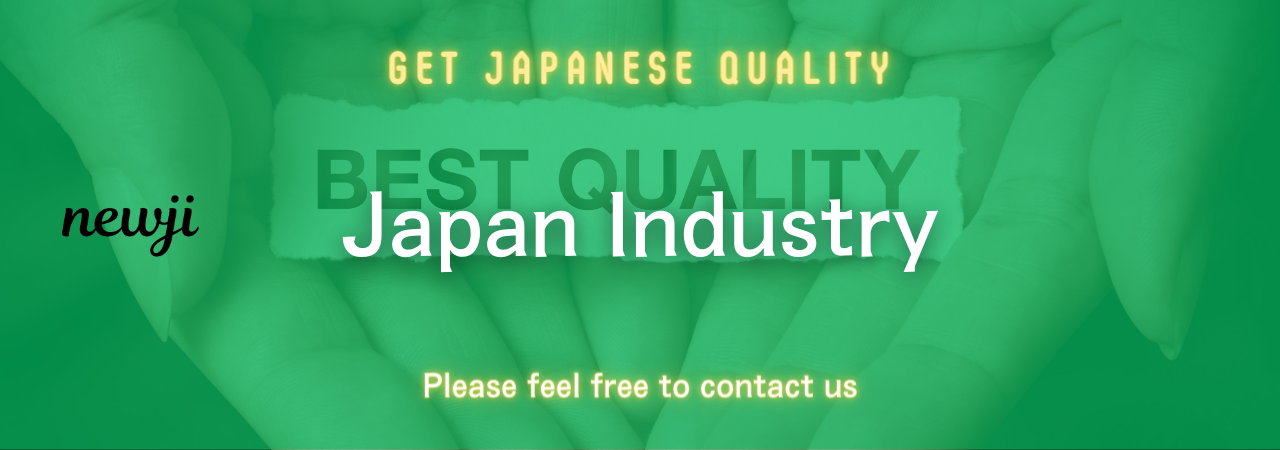
目次
Understanding Die Casting and Its Importance
Die casting is a popular manufacturing process used to produce metal parts with complex shapes and tight tolerances.
It involves forcing molten metal under high pressure into a mold cavity.
This process produces high-quality products with excellent dimensional accuracy, surface finish, and strength.
Die casting is widely used in various industries, including automotive, aerospace, electronics, and consumer goods, due to its efficiency and ability to produce parts in large volumes.
However, like any manufacturing process, die casting is not immune to defects and imperfections.
Understanding common die casting defects and finding ways to address them is key to maintaining product quality and ensuring customer satisfaction.
In this article, we will look at tips for dealing with these defects and ensuring the smooth operation of the die casting process.
Common Die Casting Defects
There are several types of defects that can occur in die casting.
Some of the most common ones include porosity, cold shuts, misruns, flash, and soldering.
Each of these defects can affect the quality and functionality of the final product.
Porosity
Porosity refers to the presence of trapped air or gas bubbles within the metal part.
It can weaken the structural integrity of the component, causing it to fail or break under stress.
Porosity can be caused by poor gating design, inadequate venting, or improper metal flow.
Cold Shuts
Cold shuts happen when two or more streams of molten metal meet in the die but fail to fuse together properly.
This results in a visible line on the surface of the part, which can affect both its appearance and strength.
Cold shuts are often caused by low metal temperatures or slow injection speeds.
Misruns
Misruns occur when the molten metal solidifies before completely filling the mold cavity.
This leads to incomplete or missing sections of the part.
Misruns can result from insufficient metal flow, low metal temperature, or inadequate die venting.
Flash
Flash is the excess metal that leaks out during the die casting process, forming thin projections along the edges of the part.
While flash can often be removed in post-processing, it is best to minimize its occurrence to reduce time and costs.
Flash occurs when there is too much pressure, a misalignment in the die, or excessive lubrication.
Soldering
Soldering refers to a defect where the surface of the casting sticks to the mold, causing surface imperfections when removed.
It typically occurs due to inadequate cooling or insufficient lubrication of the die, resulting in regions of the part melting and adhering to the die surface.
Tips for Preventing and Addressing Die Casting Defects
Now that we have a better understanding of common defects, let’s explore some practical tips to prevent and address these issues.
Optimize Mold Design
One of the most effective ways to prevent defects is to ensure the mold design is optimized for the specific part and materials used.
Consider using computer-aided design (CAD) and simulation software to evaluate and refine mold designs before production.
This can help identify potential problem areas in the design and improve metal flow, cooling, and venting.
Control Process Parameters
Careful control of process parameters, such as temperature, pressure, and speeds, is critical to achieving high-quality die castings.
Ensure that the molten metal is at the correct temperature before injection and maintain consistent pressure throughout the filling process.
Adjusting injection speed can help prevent defects like cold shuts and misruns by ensuring complete cavity fill.
Regularly Maintain and Inspect Equipment
Regular maintenance and inspection of die casting machines, dies, and auxiliary equipment can prevent defects caused by mechanical issues.
Ensure dies are free of wear, damage, and build-up by routinely cleaning and lubricating them.
Keeping your equipment in good working condition will improve process stability, reduce downtime, and enhance product quality.
Choose the Right Materials
Selecting appropriate materials for both the die and the casting metal plays a significant role in preventing defects.
Ensure compatibility between the die material and the molten metal to minimize soldering and other surface-related defects.
Using high-quality alloys that are suited to the specific application requirements can also improve the final product’s properties and reduce defect rates.
Implement Robust Quality Control Measures
Quality control is essential to detect and address defects early in the production cycle.
Implement robust inspection and testing procedures to monitor critical dimensions, surface finish, and overall part integrity.
Consider incorporating non-destructive testing techniques to identify internal defects such as porosity or voids without damaging the parts.
Conclusion
Dealing with defects in die casting is crucial for ensuring high-quality products and maintaining customer satisfaction.
By understanding the common types of defects and implementing preventive measures, manufacturers can significantly reduce the incidence of such issues.
Optimize mold designs, control process parameters, maintain equipment, choose the right materials, and apply stringent quality control measures to achieve the best outcomes in die casting operations.
With careful planning and execution, die casting can continue to be a reliable and efficient method for producing complex metal parts.
資料ダウンロード
QCD管理受発注クラウド「newji」は、受発注部門で必要なQCD管理全てを備えた、現場特化型兼クラウド型の今世紀最高の受発注管理システムとなります。
ユーザー登録
受発注業務の効率化だけでなく、システムを導入することで、コスト削減や製品・資材のステータス可視化のほか、属人化していた受発注情報の共有化による内部不正防止や統制にも役立ちます。
NEWJI DX
製造業に特化したデジタルトランスフォーメーション(DX)の実現を目指す請負開発型のコンサルティングサービスです。AI、iPaaS、および先端の技術を駆使して、製造プロセスの効率化、業務効率化、チームワーク強化、コスト削減、品質向上を実現します。このサービスは、製造業の課題を深く理解し、それに対する最適なデジタルソリューションを提供することで、企業が持続的な成長とイノベーションを達成できるようサポートします。
製造業ニュース解説
製造業、主に購買・調達部門にお勤めの方々に向けた情報を配信しております。
新任の方やベテランの方、管理職を対象とした幅広いコンテンツをご用意しております。
お問い合わせ
コストダウンが利益に直結する術だと理解していても、なかなか前に進めることができない状況。そんな時は、newjiのコストダウン自動化機能で大きく利益貢献しよう!
(β版非公開)