- お役立ち記事
- Tips for effectively promoting TPM activities that managers of equipment maintenance departments should keep in mind
Tips for effectively promoting TPM activities that managers of equipment maintenance departments should keep in mind
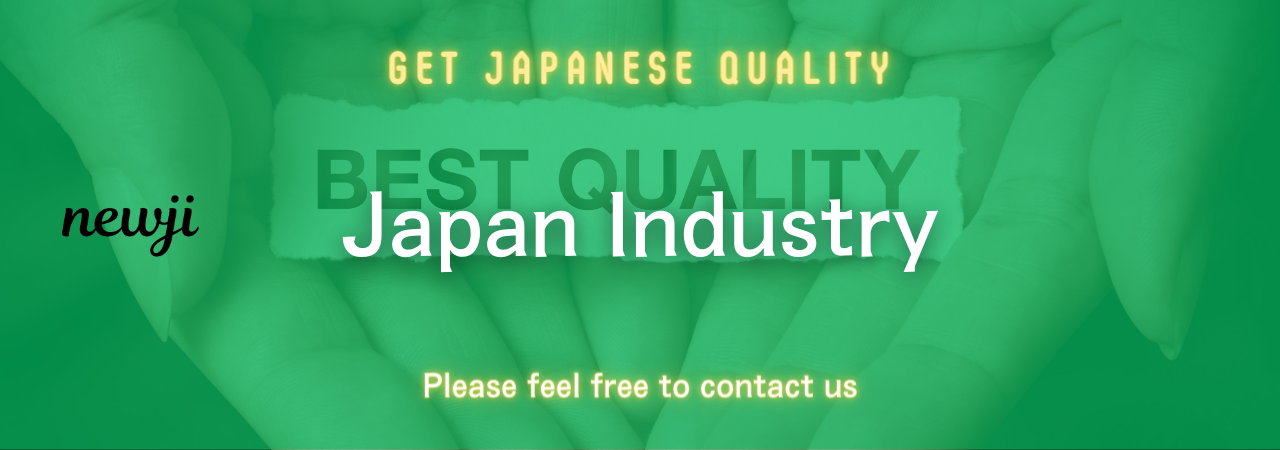
目次
Understanding Total Productive Maintenance (TPM)
Total Productive Maintenance (TPM) is a holistic approach to equipment maintenance that strives to achieve perfect production with minimal downtime and defects.
This innovative method involves everyone in the organization, from top management to front-line engineers, to share responsibility for equipment performance.
Its primary goal is to enhance productivity and efficiency by empowering teams to conduct maintenance activities routinely.
TPM is built on eight pillars: autonomous maintenance, planned maintenance, quality maintenance, focused improvement, early equipment management, training and education, safety, health, and environment, and TPM in administration.
Each pillar addresses a specific area to optimize productivity and efficiency.
For managers of equipment maintenance departments, understanding and promoting these aspects can lead to considerable improvements in operational results.
The Role of Managers in Promoting TPM
Managers of equipment maintenance departments play a crucial role in driving TPM activities.
Their responsibilities include setting goals, fostering a supportive culture, and ensuring all team members are aligned with TPM objectives.
Creating an environment that encourages feedback and communication is vital for the successful implementation of TPM practices.
Effective promotion of TPM also involves continual assessment of equipment efficiency, monitoring progress, and making informed decisions based on data analysis.
By focusing on clear communication, consensus-building, and skill development, managers can maximize the benefits of TPM.
Building a Strong TPM Culture
One of the primary tasks for equipment maintenance managers is establishing a robust TPM culture.
This involves transforming the organizational mindset to prioritize proactive maintenance over reactive solutions.
Managers should actively demonstrate their commitment to TPM principles, providing consistent support and resources to their teams.
Building this culture requires regular training sessions to upskill workers, fostering a sense of ownership by recognizing and rewarding achievements, and engaging workers in problem-solving activities.
Furthermore, integrating TPM philosophies into weekly meetings, reports, and evaluations can ensure that TPM remains a focus in everyday operational activities.
Engaging All Levels of Staff
TPM requires the engagement of the entire workforce, from top executives to line operators.
It’s essential for managers to communicate the benefits and objectives of TPM clearly at all levels.
Managers should encourage participation by organizing cross-functional teams responsible for different aspects of TPM, thereby rotating the leadership roles to build trust and team spirit.
By promoting a participative approach where everyone’s ideas and insights are valued, workers naturally become invested in the success of TPM initiatives.
Implementing a Step-by-Step TPM Plan
The implementation of TPM should follow a structured plan with clear steps.
Managers should begin by conducting a thorough assessment of current maintenance practices to identify areas of improvement.
From there, setting achievable goals and developing specific plans of action for each TPM pillar is crucial.
Start with autonomous maintenance by educating operators on routine checks and maintenance tasks they can perform themselves.
Progressively, move to planned maintenance by scheduling non-disruptive maintenance activities, thereby preempting potential breakdowns.
Monitoring and Assessment
Continuous monitoring and assessment are vital for the successful implementation of TPM.
Managers should establish key performance indicators (KPIs) to monitor the effectiveness of TPM activities.
Such metrics may include rates of downtime, quality of production, operator efficiency, and compliance with planned maintenance schedules.
Regular audits and feedback sessions should also be conducted to assess areas that require further improvement.
It is imperative to conduct root cause analyses when issues arise to tackle the problem at its source.
Encouraging Continuous Learning and Improvement
The essence of TPM involves continuous improvement, often referred to as kaizen in operational management.
Managers must instill a culture of ongoing education and development among their teams.
Offering regular training workshops, seminars, or access to online courses can keep teams at the cutting edge of maintenance strategies.
Additionally, fostering a learning environment where employees feel encouraged to experiment with new ideas or techniques can lead to innovative solutions to maintenance challenges.
Sharing Success Stories
Recognizing and broadcasting successful TPM initiatives can significantly boost morale and motivation within the team.
Managers should showcase the achievements of employees who excel at TPM activities, as well as share success stories across the organization.
This not only reinforces the importance of TPM but also inspires others to contribute towards similar goals and objectives.
Increasing the visibility of successful TPM practices can demonstrate the tangible benefits the organization can reap, further motivating the collective workforce.
Leveraging Technology in TPM Activities
The implementation of modern technologies can significantly enhance the effectiveness of TPM activities.
Managers should consider investing in predictive maintenance technologies and advanced data analytics tools to anticipate equipment failures before they occur.
The integration of IoT devices and sensor technology can support real-time monitoring and predictive diagnostics, offering valuable insights into equipment performance.
Moreover, utilizing mobile applications and digital platforms can facilitate better communication, easier access to maintenance schedules, and instant reporting of issues, empowering teams to act swiftly.
Conclusion
In conclusion, effectively promoting TPM activities requires a committed, informed, and strategic approach from managers of equipment maintenance departments.
Through strong leadership, establishment of a robust TPM culture, structured implementation plans, continuous learning, and the application of advanced technology, managers can unlock significant productivity and efficiency gains.
Encouraging a collaborative environment where communication and shared objectives thrive will ensure long-term success in TPM initiatives and drive the organization towards a sustainable future.
資料ダウンロード
QCD調達購買管理クラウド「newji」は、調達購買部門で必要なQCD管理全てを備えた、現場特化型兼クラウド型の今世紀最高の購買管理システムとなります。
ユーザー登録
調達購買業務の効率化だけでなく、システムを導入することで、コスト削減や製品・資材のステータス可視化のほか、属人化していた購買情報の共有化による内部不正防止や統制にも役立ちます。
NEWJI DX
製造業に特化したデジタルトランスフォーメーション(DX)の実現を目指す請負開発型のコンサルティングサービスです。AI、iPaaS、および先端の技術を駆使して、製造プロセスの効率化、業務効率化、チームワーク強化、コスト削減、品質向上を実現します。このサービスは、製造業の課題を深く理解し、それに対する最適なデジタルソリューションを提供することで、企業が持続的な成長とイノベーションを達成できるようサポートします。
オンライン講座
製造業、主に購買・調達部門にお勤めの方々に向けた情報を配信しております。
新任の方やベテランの方、管理職を対象とした幅広いコンテンツをご用意しております。
お問い合わせ
コストダウンが利益に直結する術だと理解していても、なかなか前に進めることができない状況。そんな時は、newjiのコストダウン自動化機能で大きく利益貢献しよう!
(Β版非公開)