- お役立ち記事
- Tips for Managing Injection Speed to Prevent Molding Defects
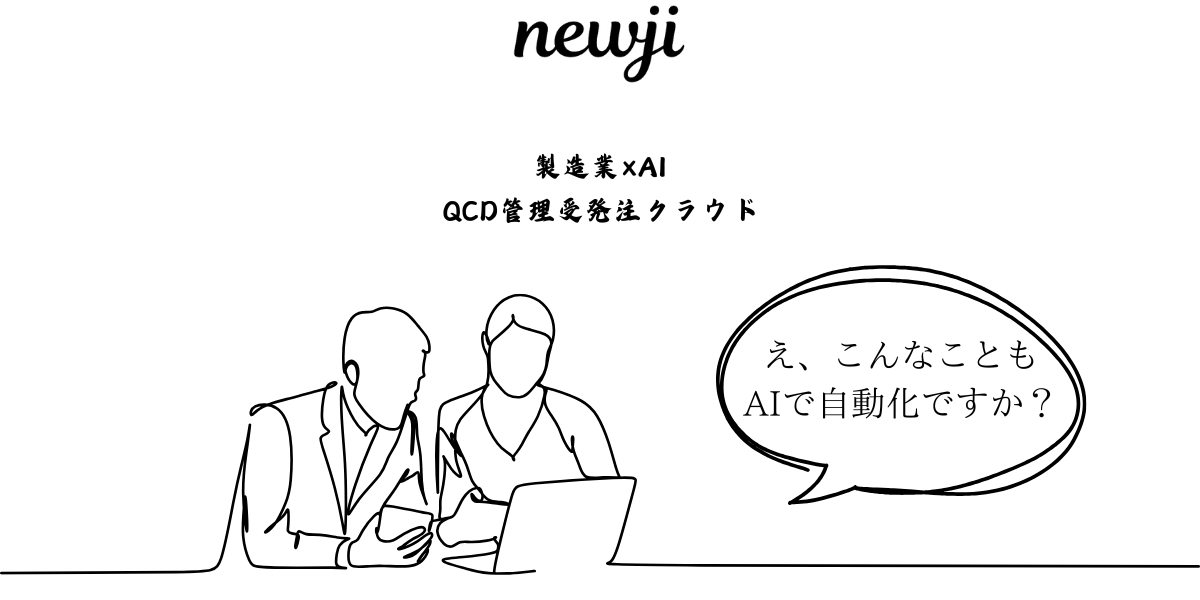
Tips for Managing Injection Speed to Prevent Molding Defects
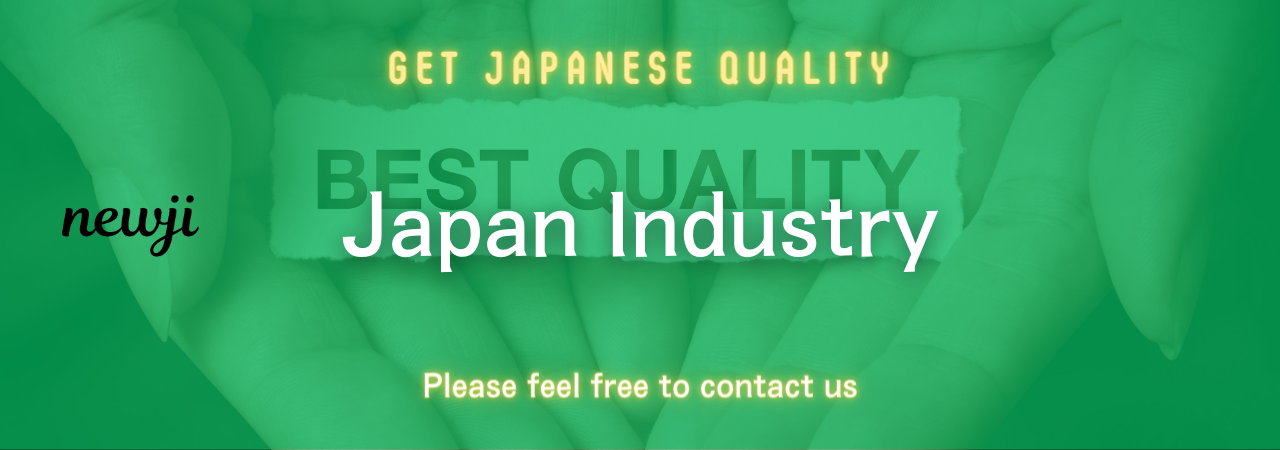
目次
Understanding Injection Speed
Injection speed is a critical parameter in the molding process that significantly affects the quality of the final product.
It refers to the rate at which the molten material is injected into the mold cavity.
Properly managing this speed is essential to achieving high-quality molding outcomes and preventing defects.
The right injection speed ensures that the material fills the mold completely without leaving any voids or imperfections.
The Impact of Injection Speed on Molding
The injection speed can influence a variety of factors in the molding process.
Too fast or too slow speed can lead to several defects.
Fast injection speeds can cause issues such as flashing, where excess material leaks out of the mold and creates unwanted extensions.
It can also lead to the formation of air pockets that result in incomplete filling, commonly known as short shots.
On the other hand, slow injection speeds might cause shrinkage, warping, or sink marks due to material cooling and hardening before it fully occupies the mold cavity.
Tips for Managing Injection Speed
1. Understand the Material Properties
Before adjusting injection speed, it’s crucial to understand the properties of the material being used.
Different materials respond differently to injection speeds.
For instance, thermoplastic materials often require higher speeds compared to thermoset plastics.
Having a deep understanding of your material’s flow characteristics and viscosity can guide appropriate speed settings for optimal performance.
2. Monitor the Temperature
The material’s temperature directly affects how it flows within the mold.
Ensure the molten material maintains a consistent temperature to achieve uniform flow and prevent defects.
If the temperature is too high, it might necessitate a faster injection speed to avoid premature cooling; if too low, a slower speed might be better to allow for steady mold filling.
3. Use a Multi-Stage Process
Implementing a multi-stage injection process can significantly enhance control over the material flow.
Begin with a slower speed to reduce resistance and ensure the material aligns correctly.
Once the material has begun to fill the mold adequately, increase the speed to ensure full and efficient filling, then slow down again towards the end to minimize potential overshooting and flashing.
4. Consistent Pressure Level
Maintaining a constant pressure during injection helps manage speed more effectively.
Fluctuating pressure during the fill phase can disrupt speed settings and lead to defects.
Using advanced control systems can help regulate pressure and maintain the desired injection speed throughout the process.
5. Regularly Inspect Equipment
Frequent equipment checks are crucial.
Over time, wear and tear can affect machines’ ability to maintain consistent injection speeds.
Conduct routine inspections and calibrations of injection molding machines to ensure they operate within desired specifications.
Address any mechanical issues that might influence speed control before beginning a new production cycle.
Identifying Molding Defects
Recognizing Common Defects
Understanding different types of defects can help in troubleshooting issues related to injection speed.
Common defects include:
– **Short Shots**: Occurs when the mold cavity doesn’t fill completely.
– **Flashing**: Excess material found outside the mold cavity, often due to excessive speed or high pressure.
– **Sink Marks**: Indentations caused by uneven cooling of the thicker parts of a molded item.
– **Warping**: Distortions that result from inconsistent cooling and stress distribution.
Optimizing the Injection Molding Process
Continuous Improvement
The key to managing injection speed is a continuous process of reviewing and improving the steps involved in the molding process.
Utilize feedback from production runs to adjust and tweak injection speeds as necessary, ensuring they align with the specific material and design requirements of each project.
Training and Education
Equip your team with the necessary knowledge and skills to understand and manage injection speed effectively.
Regularly updated training sessions on the latest technologies and techniques in injection molding can keep your staff informed and adept at handling various materials and molds.
Utilizing Technology and Software
Leveraging advanced technologies and software can also help optimize injection speed management.
Modern injection molding machines often come equipped with sophisticated software that assists in fine-tuning and maintaining the desired speed throughout the injection process.
These systems can provide invaluable data insights and analytics to further refine the molding process efficiency.
In conclusion, managing injection speed in molding is a crucial aspect that requires careful attention and constant monitoring.
By understanding material properties, temperature effects, and utilizing a multi-stage approach, manufacturers can significantly reduce molding defects.
Regular equipment maintenance and employee training play equally critical roles in achieving optimal molding conditions.
With the right practices and technologies in place, producing high-quality, defect-free molded products can become a more consistent and achievable goal.
資料ダウンロード
QCD調達購買管理クラウド「newji」は、調達購買部門で必要なQCD管理全てを備えた、現場特化型兼クラウド型の今世紀最高の購買管理システムとなります。
ユーザー登録
調達購買業務の効率化だけでなく、システムを導入することで、コスト削減や製品・資材のステータス可視化のほか、属人化していた購買情報の共有化による内部不正防止や統制にも役立ちます。
NEWJI DX
製造業に特化したデジタルトランスフォーメーション(DX)の実現を目指す請負開発型のコンサルティングサービスです。AI、iPaaS、および先端の技術を駆使して、製造プロセスの効率化、業務効率化、チームワーク強化、コスト削減、品質向上を実現します。このサービスは、製造業の課題を深く理解し、それに対する最適なデジタルソリューションを提供することで、企業が持続的な成長とイノベーションを達成できるようサポートします。
オンライン講座
製造業、主に購買・調達部門にお勤めの方々に向けた情報を配信しております。
新任の方やベテランの方、管理職を対象とした幅広いコンテンツをご用意しております。
お問い合わせ
コストダウンが利益に直結する術だと理解していても、なかなか前に進めることができない状況。そんな時は、newjiのコストダウン自動化機能で大きく利益貢献しよう!
(Β版非公開)