- お役立ち記事
- Tips for Mold Design to Manufacture High-Precision Products Using Multi-Injection Molding
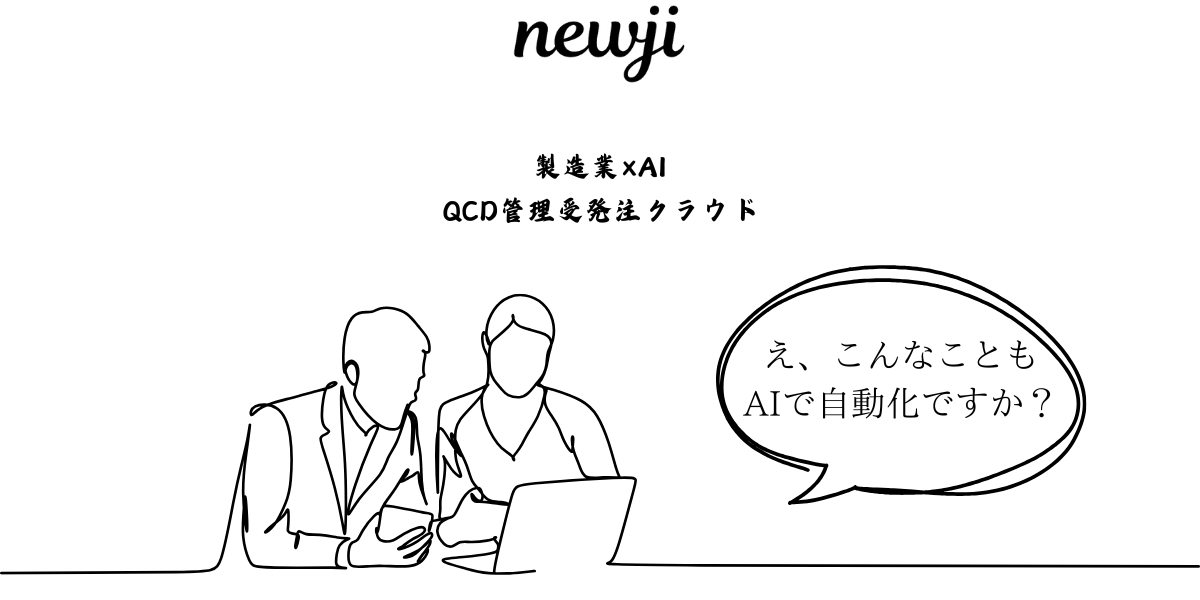
Tips for Mold Design to Manufacture High-Precision Products Using Multi-Injection Molding
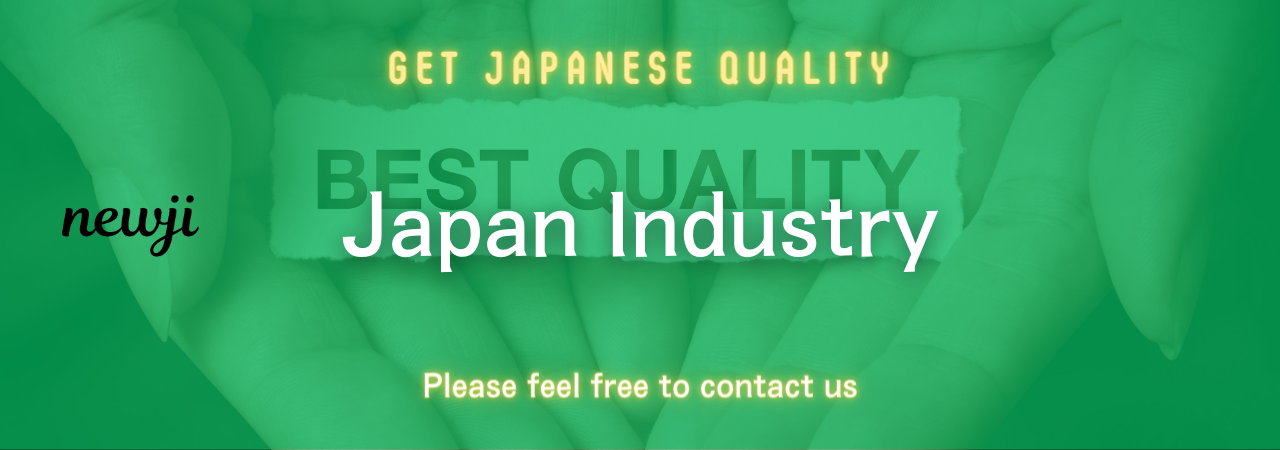
目次
Understanding Multi-Injection Molding
Multi-injection molding is a sophisticated manufacturing process that allows for the production of high-precision products in a single cycle.
This process involves the injection of two or more different materials or colors into the same mold, creating complex and multi-textured components.
For industries that demand precision, such as automotive, electronics, and medical devices, multi-injection molding offers significant benefits.
These include reduced production time, material efficiency, and the ability to create intricate designs without secondary operations.
Benefits of Multi-Injection Molding
The primary advantage is the ability to produce parts with multiple materials or colors in one cycle.
This reduces the need for post-processing and additional assembly, thereby saving time and cost.
Another benefit is the enhancement of product functionality and aesthetics.
Products can have soft-touch surfaces combined with rigid structures, which is particularly useful in products like toothbrushes or automotive dashboards.
Moreover, multi-injection molding can lead to stronger bonds between different materials, enhancing the durability of the end product.
Key Factors in Mold Design for Precision
When designing molds for multi-injection molding, several critical factors must be considered to ensure the production of high-precision products.
Material Compatibility
Choosing the right combination of materials is crucial in multi-injection molding.
Incompatible materials can lead to defects such as delamination or weak bonds.
It’s essential to understand the chemical and thermal properties of each material being used, ensuring they complement each other when injected.
Mold Layout and Design
The design of the mold is integral to the success of multi-injection molding.
Molds must be designed to handle multiple injections, often requiring complex feeder systems to deliver the materials efficiently.
Additionally, the positioning of gates and runners should be strategically planned to ensure smooth and even material flow.
Tolerances and Precision
To manufacture high-precision products, maintaining tight tolerances in mold design is crucial.
This means the design must account for material shrinkage, ensure accurate alignment of different layers, and guarantee uniform thickness.
Failure in any of these aspects can result in products that do not meet high-quality standards.
Cooling Systems
Effective cooling systems are essential in preventing warping and ensuring that the molded part retains its intended shape and dimensions.
Cooling systems need to be meticulously planned to work in harmony with the injection process, allowing for quick and even cooling.
Common Challenges and Solutions
Despite its advantages, multi-injection molding introduces unique challenges that can impact the precision of products.
Material Flow
Achieving a consistent material flow can be challenging with multiple materials.
To address this, mold designers must carefully plan the injection sequence and optimize temperatures and pressures for each material.
Complex Mold Construction
Multi-injection molds are inherently more complex, increasing the risk of defects.
A solution is to invest in high-quality mold components and utilize advanced simulation software to predict potential issues before actual production begins.
Machine Capabilities
Not every injection molding machine can handle multi-injection processes.
Ensuring that the machine used is capable of precise control over multiple materials and that it can switch between them efficiently is critical.
Steps to Optimize Mold Design
To maximize the effectiveness of multi-injection molding, specific steps can be taken during the mold design phase.
Utilize Simulation Software
Using advanced simulation software allows designers to create virtual models of the mold and test different scenarios.
It helps in foreseeing possible defects and understanding how various materials will interact in the mold.
Collaborate with Material Experts
Involving material specialists in the early stages of mold design can provide valuable insights into material behavior.
This collaboration aids in making informed decisions about material combinations and their expected performance.
Conduct Thorough Testing
Before full-scale production, conducting pilot runs and thorough testing of the mold setup will reveal any design flaws or unexpected challenges.
This step is vital for making adjustments and ensuring the mold works as intended.
Conclusion
The precise design of molds is crucial in the manufacturing of high-precision products using multi-injection molding.
Understanding the intricacies of the process, being aware of the challenges, and taking strategic steps in mold design can significantly enhance the quality and efficiency of the final product.
As technology continues to evolve, so will the capabilities of multi-injection molding, making it an exciting field for innovation and growth in precision manufacturing.
資料ダウンロード
QCD調達購買管理クラウド「newji」は、調達購買部門で必要なQCD管理全てを備えた、現場特化型兼クラウド型の今世紀最高の購買管理システムとなります。
ユーザー登録
調達購買業務の効率化だけでなく、システムを導入することで、コスト削減や製品・資材のステータス可視化のほか、属人化していた購買情報の共有化による内部不正防止や統制にも役立ちます。
NEWJI DX
製造業に特化したデジタルトランスフォーメーション(DX)の実現を目指す請負開発型のコンサルティングサービスです。AI、iPaaS、および先端の技術を駆使して、製造プロセスの効率化、業務効率化、チームワーク強化、コスト削減、品質向上を実現します。このサービスは、製造業の課題を深く理解し、それに対する最適なデジタルソリューションを提供することで、企業が持続的な成長とイノベーションを達成できるようサポートします。
オンライン講座
製造業、主に購買・調達部門にお勤めの方々に向けた情報を配信しております。
新任の方やベテランの方、管理職を対象とした幅広いコンテンツをご用意しております。
お問い合わせ
コストダウンが利益に直結する術だと理解していても、なかなか前に進めることができない状況。そんな時は、newjiのコストダウン自動化機能で大きく利益貢献しよう!
(Β版非公開)