- お役立ち記事
- Tips for Optimizing Compression Molding Techniques
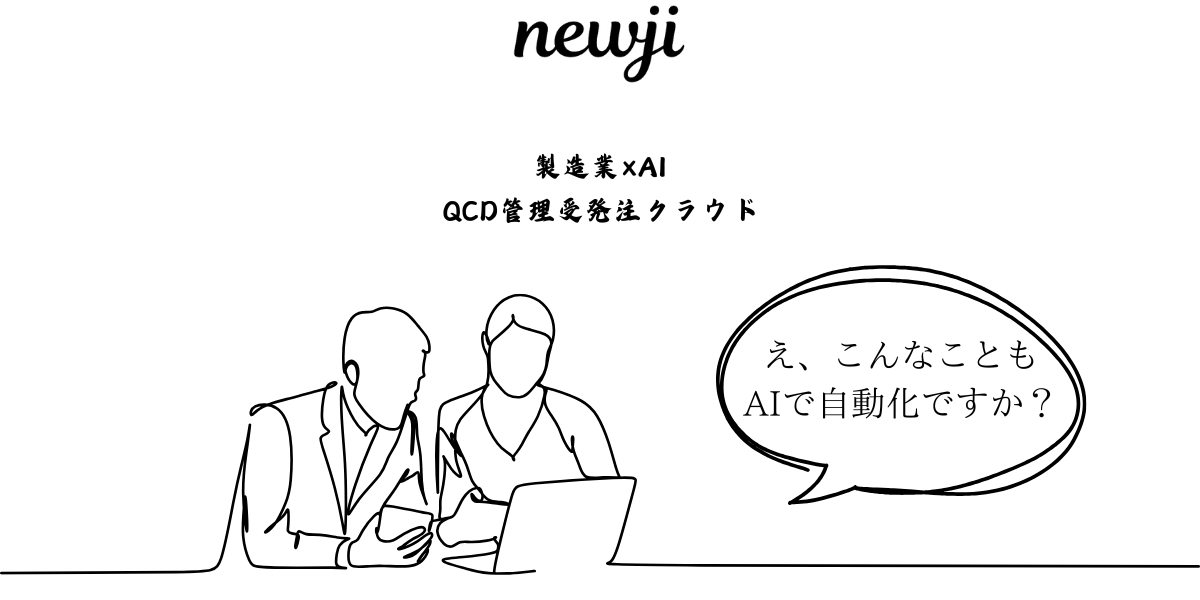
Tips for Optimizing Compression Molding Techniques
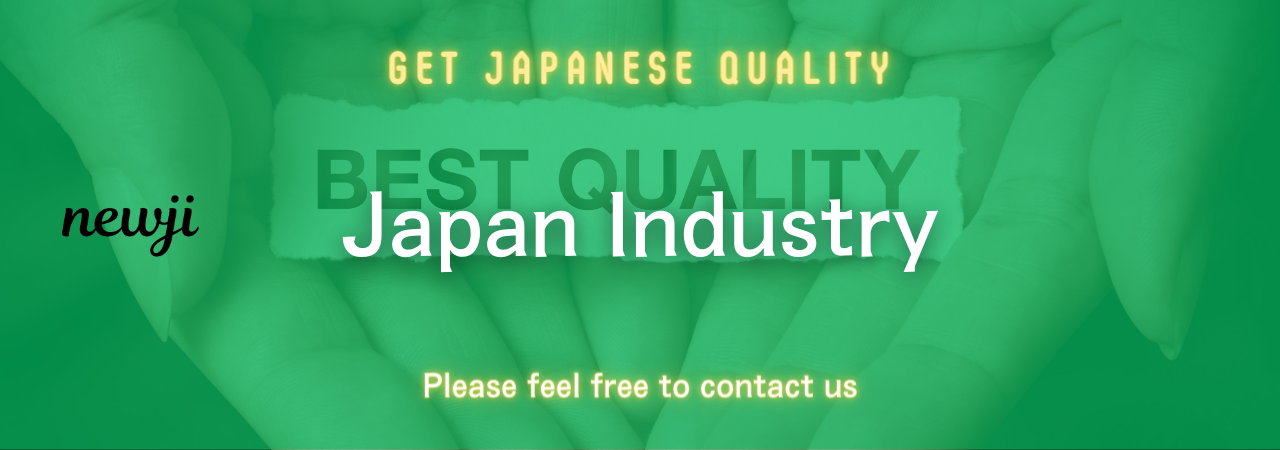
目次
Understanding Compression Molding
Compression molding is a manufacturing process that transforms raw materials into durable and usable components.
It’s widely used in industries like automotive, aerospace, and consumer goods due to its cost-effectiveness and ability to produce complex shapes with high precision.
The process involves placing a pre-measured amount of material, often in the form of a pellet or a sheet, into a mold cavity.
The mold is then closed, and pressure is applied to ensure the material conforms to the mold’s shape.
Heat may be applied to ensure that the material cures properly.
Once molded, the component is cooled and ejected from the mold.
This technique is particularly effective for materials like thermosetting polymers and composites.
Understanding how to optimize this process can lead to better product quality and more efficient production, resulting in overall cost savings.
Why Optimize Compression Molding?
Optimizing compression molding techniques has several advantages.
Firstly, it enhances product quality.
Proper optimization reduces defects such as warping, voids, or incomplete fills, ensuring each component meets high standards of consistency and performance.
Secondly, it can significantly reduce production costs.
By optimizing the process, manufacturers can minimize material waste and reduce cycle times, leading to more efficient use of resources and increased production capacity.
Lastly, optimizing compression molding can improve environmental sustainability.
By reducing waste and energy consumption, manufacturers can minimize their carbon footprint, aligning their operations with environmental standards and contributing to corporate social responsibility goals.
Key Factors for Optimization
To optimize compression molding techniques, several key factors need consideration:
Material Selection
The first step in optimizing compression molding is choosing the right material.
Different materials have unique characteristics that affect how they respond to heat and pressure.
Understanding these properties ensures the chosen material is suitable for the specific application and can be processed efficiently.
For instance, thermosetting polymers require careful handling as they need precise temperature control during curing.
Mold Design
The design of the mold plays a critical role in the optimization process.
A well-designed mold minimizes defects and ensures uniform pressure distribution across the material.
Considerations such as the mold’s shape, surface finish, and cooling channels are essential to facilitate efficient production.
Process Parameters
Controlling the parameters of the compression molding process is crucial for optimization.
Factors such as temperature, pressure, and curing time must be precisely controlled to ensure the material fills the mold correctly and retains its intended properties.
Implementing advanced control systems and monitoring tools can help maintain consistency and reduce deviations in production.
Processing Equipment
The efficiency and performance of the equipment used in compression molding are vital for optimization.
Regular maintenance and calibration of machinery ensure they operate at peak efficiency, reducing the likelihood of breakdowns and production delays.
Investing in modern equipment with enhanced capabilities can lead to better control over the molding process.
Strategies for Effective Optimization
There are several strategies manufacturers can adopt to optimize their compression molding techniques effectively:
Implement Advanced Simulation Techniques
Using computer-aided engineering (CAE) and simulation tools can help predict potential issues and optimize the molding process.
These tools simulate different scenarios, enabling manufacturers to test various parameters and make informed decisions before actual production.
Continuous Monitoring and Feedback Loops
Establishing continuous monitoring systems and feedback loops aids in real-time data collection and analysis.
This approach allows for immediate adjustments to the process when deviations are detected, ensuring consistent product quality.
Advanced sensors and data analytics platforms can provide valuable insights into the process’s efficiency and areas needing improvement.
Training and Skill Development
Ensuring personnel involved in the compression molding process are properly trained is essential for optimization.
Ongoing training programs and skill development initiatives equip workers with the knowledge and skills necessary to handle advanced technologies and techniques effectively.
Skilled operators are better able to manage process parameters and troubleshoot issues as they arise.
Collaboration and Innovation
Encouraging collaboration between different departments within a manufacturing facility can spark innovation and lead to process improvements.
Sharing insights and best practices across teams can help identify new opportunities for optimization, fostering a culture of continuous improvement.
The Future of Compression Molding Optimization
As technology continues to evolve, the future of compression molding optimization looks promising.
Innovations such as the use of artificial intelligence (AI) and machine learning (ML) are set to revolutionize the process, enabling manufacturers to predict outcomes more accurately and adapt processes in real-time.
These advancements will allow for even higher precision and efficiency in production.
Furthermore, the adoption of sustainable materials and processes will likely continue to grow.
Manufacturers will increasingly seek ways to integrate environmentally friendly practices into their operations, further enhancing the sustainability of compression molding.
In conclusion, optimizing compression molding techniques offers substantial benefits in terms of quality, cost, and sustainability.
By considering key factors and implementing effective strategies, manufacturers can stay competitive and meet the growing demands of various industries.
Embracing technological advancements and fostering a culture of continuous improvement will be crucial for success in the future.
資料ダウンロード
QCD調達購買管理クラウド「newji」は、調達購買部門で必要なQCD管理全てを備えた、現場特化型兼クラウド型の今世紀最高の購買管理システムとなります。
ユーザー登録
調達購買業務の効率化だけでなく、システムを導入することで、コスト削減や製品・資材のステータス可視化のほか、属人化していた購買情報の共有化による内部不正防止や統制にも役立ちます。
NEWJI DX
製造業に特化したデジタルトランスフォーメーション(DX)の実現を目指す請負開発型のコンサルティングサービスです。AI、iPaaS、および先端の技術を駆使して、製造プロセスの効率化、業務効率化、チームワーク強化、コスト削減、品質向上を実現します。このサービスは、製造業の課題を深く理解し、それに対する最適なデジタルソリューションを提供することで、企業が持続的な成長とイノベーションを達成できるようサポートします。
オンライン講座
製造業、主に購買・調達部門にお勤めの方々に向けた情報を配信しております。
新任の方やベテランの方、管理職を対象とした幅広いコンテンツをご用意しております。
お問い合わせ
コストダウンが利益に直結する術だと理解していても、なかなか前に進めることができない状況。そんな時は、newjiのコストダウン自動化機能で大きく利益貢献しよう!
(Β版非公開)