- お役立ち記事
- Tips for Optimizing Hold Pressure Processes to Reduce Molding Defects
月間76,176名の
製造業ご担当者様が閲覧しています*
*2025年3月31日現在のGoogle Analyticsのデータより
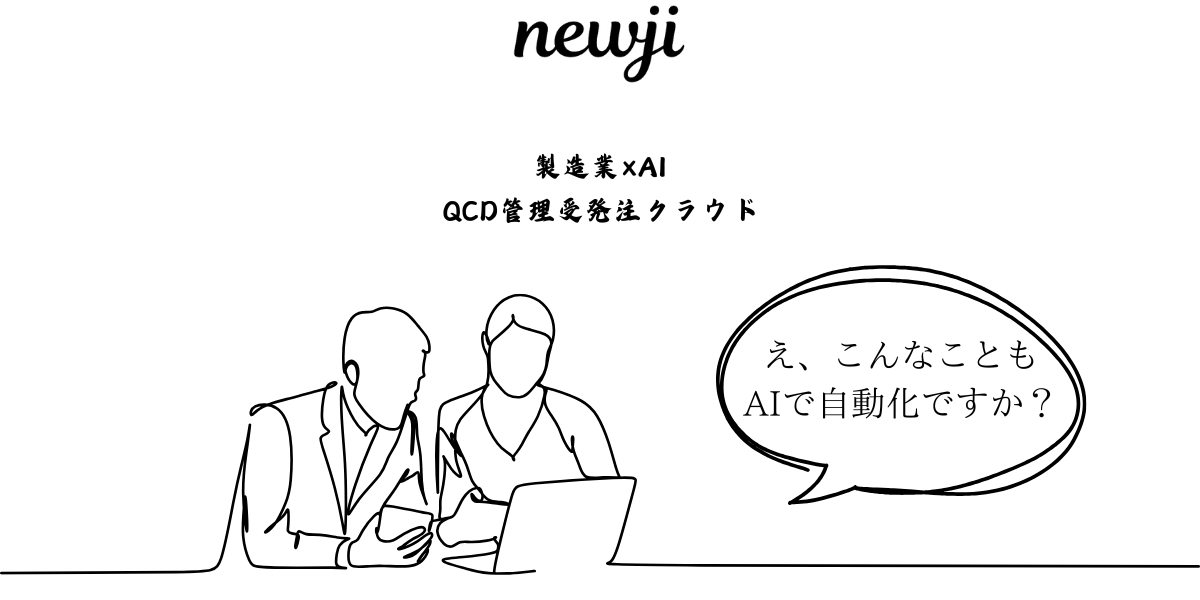
Tips for Optimizing Hold Pressure Processes to Reduce Molding Defects
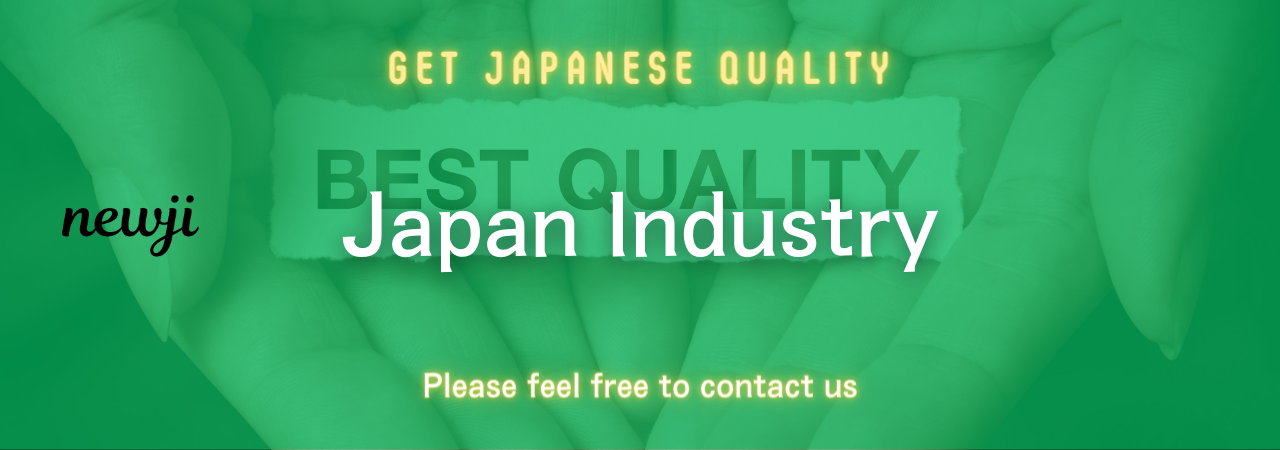
When it comes to plastic injection molding, optimizing the hold pressure process is essential in reducing defects during manufacturing.
Understanding and fine-tuning this stage can vastly improve product quality, efficiency, and cost-effectiveness in production.
Let’s delve into some effective strategies for enhancing hold pressure processes in order to minimize molding defects.
目次
Understanding Hold Pressure in Molding
Hold pressure, often referred to as packing pressure, is the pressure applied to the molten plastic inside the mold cavity after the initial injection phase.
This step is critical as it compensates for material shrinkage and ensures that the final product has the correct dimensions and is free from major defects.
By maintaining the right level of hold pressure, manufacturers can reduce common issues such as sink marks, voids, and warping.
Importance of Optimizing Hold Pressure
Optimizing hold pressure is essential for several reasons:
1. **Improved Product Quality**: Proper hold pressure can significantly reduce the likelihood of defects, leading to higher-quality outcomes.
2. **Cost-Reduction**: Minimizing defects reduces waste and lowers production costs.
3. **Consistency**: Adhering to optimal parameters ensures consistent product quality across production batches.
4. **Customer Satisfaction**: High-quality products lead to better customer satisfaction and business reputation.
Key Parameters in Hold Pressure Optimization
To effectively optimize hold pressure, it is vital to focus on several key parameters:
– **Pressure Level**: The level of pressure applied during the holding phase should be sufficient to pack the material properly but not too high to cause other defects.
– **Hold Time**: The duration for which the pressure is applied must be carefully calculated to allow for the desired cooling and solidification.
– **Pressure Profile**: Gradual changes in pressure can help in achieving a more uniform density and surface appearance in the final product.
Strategies for Optimizing Hold Pressure
Here are some practical strategies to optimize hold pressure during the injection molding process:
1. Conducting Trials and Tests
Performing controlled trials and tests can help in determining the ideal pressure settings for different materials and molds.
By monitoring the outcomes of these tests, operators can adjust their parameters to enhance quality and efficiency.
2. Utilizing Simulation Software
Modern simulation software can predict the behavior of materials under various conditions.
Using such tools can aid in visualizing how changes in hold pressure affect the final product, thus allowing for better parameter optimization.
3. Monitoring and Adjustment
Continuously monitoring the effects of hold pressure during production enables timely adjustments.
Automated systems can provide real-time data, making it easier to modify settings and avoid defects.
4. Understanding Material Properties
Different materials respond differently under pressure.
Understanding the specific properties of the material at hand is crucial for setting appropriate pressure levels.
5. Operator Training
Well-trained operators can make informed decisions regarding the optimization of hold pressure.
Regular training and updates on best practices enable them to maintain high standards of production quality.
Common Molding Defects and Their Solutions
Recognizing common defects that result from improper hold pressure can guide optimizations:
Sink Marks
– **Cause**: Insufficient hold pressure or hold time can result in sink marks.
– **Solution**: Increasing either the pressure or duration can help counteract this issue.
Voids
– **Cause**: Voids occur due to cosmetic or density variations often caused by improper packing.
– **Solution**: Adjusting pressure and other parameters can help fill void spaces more effectively.
Warping
– **Cause**: Uneven cooling due to inadequate hold pressure leads to warping.
– **Solution**: Ensuring uniform distribution of pressure across the mold can minimize this defect.
Final Thoughts
Optimizing hold pressure processes is a vital step in reducing molding defects and enhancing product quality.
Understanding the dynamics of hold pressure and its impact on the molding process can greatly benefit manufacturers by minimizing waste, reducing costs, and improving overall production efficiency.
By implementing these strategies and maintaining vigilant oversight, companies can ensure that their plastic products are of the highest quality, which in turn leads to better customer satisfaction and business success.
資料ダウンロード
QCD管理受発注クラウド「newji」は、受発注部門で必要なQCD管理全てを備えた、現場特化型兼クラウド型の今世紀最高の受発注管理システムとなります。
ユーザー登録
受発注業務の効率化だけでなく、システムを導入することで、コスト削減や製品・資材のステータス可視化のほか、属人化していた受発注情報の共有化による内部不正防止や統制にも役立ちます。
NEWJI DX
製造業に特化したデジタルトランスフォーメーション(DX)の実現を目指す請負開発型のコンサルティングサービスです。AI、iPaaS、および先端の技術を駆使して、製造プロセスの効率化、業務効率化、チームワーク強化、コスト削減、品質向上を実現します。このサービスは、製造業の課題を深く理解し、それに対する最適なデジタルソリューションを提供することで、企業が持続的な成長とイノベーションを達成できるようサポートします。
製造業ニュース解説
製造業、主に購買・調達部門にお勤めの方々に向けた情報を配信しております。
新任の方やベテランの方、管理職を対象とした幅広いコンテンツをご用意しております。
お問い合わせ
コストダウンが利益に直結する術だと理解していても、なかなか前に進めることができない状況。そんな時は、newjiのコストダウン自動化機能で大きく利益貢献しよう!
(β版非公開)