- お役立ち記事
- Tips for Optimizing Shot Size to Enhance Productivity
月間76,176名の
製造業ご担当者様が閲覧しています*
*2025年3月31日現在のGoogle Analyticsのデータより
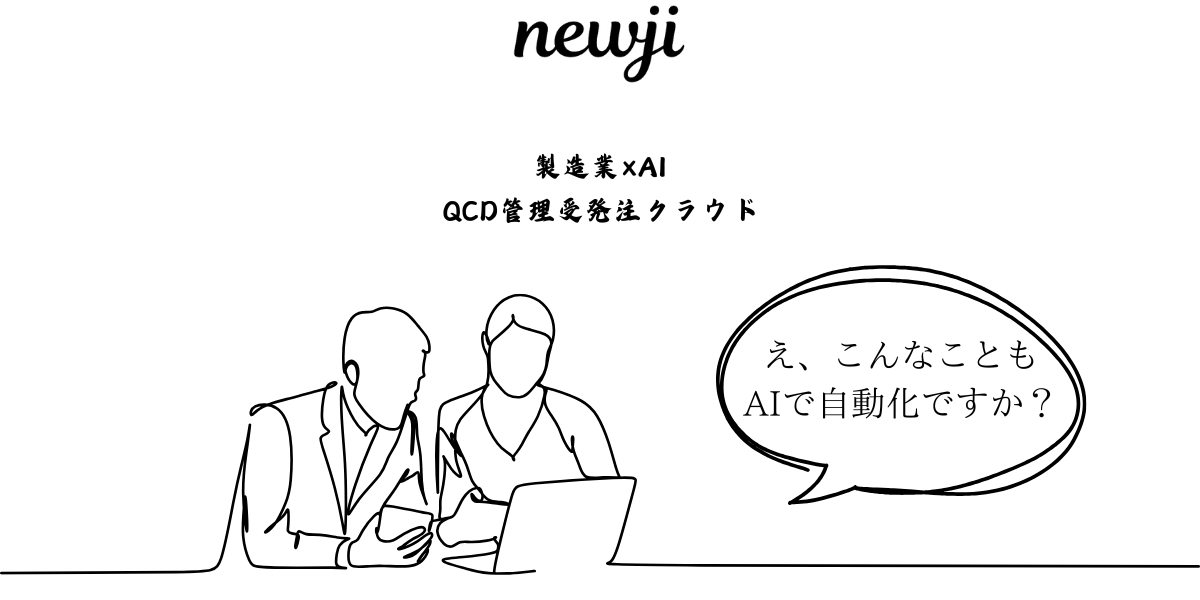
Tips for Optimizing Shot Size to Enhance Productivity
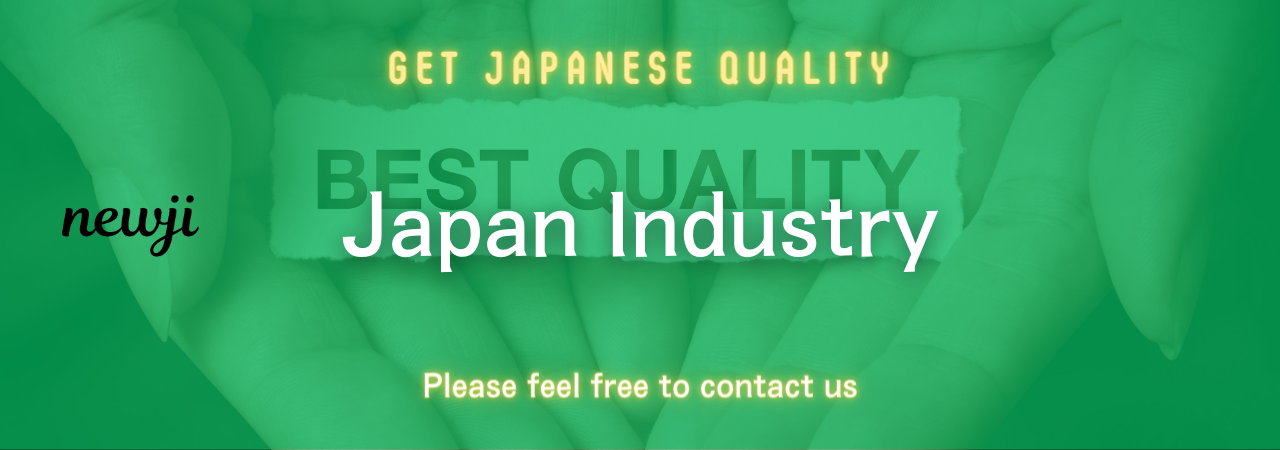
目次
Understanding Shot Size
Shot size refers to the quantity or volume of material injected or processed in one cycle, especially in manufacturing settings such as injection molding or die-casting.
Optimizing shot size is integral in these industries, as it directly affects productivity, waste, and the quality of the finished product.
When the shot size is too large or too small, it can lead to defects, irregularities, and increased operational costs.
Thus, understanding and managing the shot size is critical to achieving efficient production.
The Impact on Productivity
Productivity in any manufacturing process is influenced by a variety of factors, with shot size being a significant one.
If the shot size is optimized, machines operate smoothly, leading to faster production times and minimal defects.
A well-adjusted shot size ensures that the right amount of material feeds into the mold, reducing the likelihood of defects such as warping or incomplete filling.
On the other hand, an incorrect shot size can lead to frequent interruptions, machine downtimes, and increased waste as defective parts need to be reprocessed or discarded.
By focusing on shot size, manufacturers can reduce cycle times and increase the output rate, enhancing overall efficiency.
How to Determine the Ideal Shot Size
To determine the optimal shot size, several factors must be considered.
These include the material type, mold design, and the specifications of the machine being used.
Material Considerations
Different materials behave differently under pressure.
Thus, understanding the specific properties of the material being used is pivotal.
For example, some materials may expand significantly when heated, requiring compensatory adjustments in the shot size.
Manufacturers should work closely with material suppliers to understand these properties.
Testing and experimentation are often required to find the sweet spot for each material regarding shot size.
Mold Design
The design and complexity of the mold also play a crucial role.
Complex molds with intricate designs may require smaller, more controlled shot sizes to ensure complete filling without causing defects.
Attention should be paid to the number of cavities in a mold, as this also affects the volume of material needed.
More cavities typically require larger shot sizes, but this increase must be calculated precisely to avoid overfilling and material waste.
Machine Specifications
Machines come with their own sets of limitations and capabilities.
Each machine has a maximum and minimum shot size, and operators must ensure that their settings fall within this range.
Furthermore, machines need to be regularly calibrated.
Over time, wear and tear can affect their performance, leading to inaccurate shot sizes.
Routine maintenance and recalibration can prevent such issues.
Techniques for Optimizing Shot Size
Several techniques can help in optimizing shot size to enhance productivity.
Trial and Error Testing
One of the most straightforward methods is trial and error.
While it may seem rudimentary, systematically adjusting and testing different shot sizes can provide functional insights.
Beginners should start at the manufacturer-recommended settings and modify in small increments.
Documenting the effects of each adjustment helps in understanding the relationship between shot size and production quality.
Utilizing Advanced Technology
Today’s manufacturing environments can leverage technologies such as simulation software.
These tools can model the injection process, providing visual insights into how different shot sizes will perform without necessitating actual trials.
Additionally, AI-driven systems can automatically adjust shot sizes in real-time, responding to variables like temperature fluctuations or changes in material viscosity.
These systems can significantly enhance productivity by reducing human error and optimizing processes on-the-go.
Involving Experienced Personnel
In any manufacturing setup, the most valuable assets are often the personnel at the helm.
Experienced operators possess an intuitive understanding of machinery and materials that can be invaluable in fine-tuning processes.
Investing in training and involving seasoned staff in the adjustment and monitoring processes can lead to notable improvements in overall efficiency.
Monitoring and Maintenance
Continuous monitoring and timely maintenance are vital aspects of maintaining optimal shot size settings.
Regular Inspections
Regular machine inspections help identify potential issues that may lead to discrepancies in shot size.
Checking for wear in injectors, leaks, or blockages ensures that machines function correctly and consistently produce the desired shot size.
Data Analysis
Modern manufacturing units often employ data analysis tools to track production metrics.
Analyzing data trends can spotlight inefficiencies related to shot size, allowing for prompt corrective measures.
Setting up alerts for deviations from expected performance can also prevent prolonged periods of inefficiency.
Scheduled Maintenance
Preventive maintenance schedules are crucial for ensuring machine longevity and reliability.
Adhering to routine machine servicing intervals helps maintain calibration and prevents unexpected breakdowns, keeping shot sizes accurate.
Conclusion
Optimizing shot size is a commitment to enhancing productivity in the manufacturing realm.
Understanding the underlying principles, experimenting with different techniques, leveraging technology, and maintaining machinery all contribute to finding that perfect balance.
As industry standards and technologies evolve, staying informed and adaptable ensures that manufacturers remain competitive in a rapidly changing environment.
資料ダウンロード
QCD管理受発注クラウド「newji」は、受発注部門で必要なQCD管理全てを備えた、現場特化型兼クラウド型の今世紀最高の受発注管理システムとなります。
ユーザー登録
受発注業務の効率化だけでなく、システムを導入することで、コスト削減や製品・資材のステータス可視化のほか、属人化していた受発注情報の共有化による内部不正防止や統制にも役立ちます。
NEWJI DX
製造業に特化したデジタルトランスフォーメーション(DX)の実現を目指す請負開発型のコンサルティングサービスです。AI、iPaaS、および先端の技術を駆使して、製造プロセスの効率化、業務効率化、チームワーク強化、コスト削減、品質向上を実現します。このサービスは、製造業の課題を深く理解し、それに対する最適なデジタルソリューションを提供することで、企業が持続的な成長とイノベーションを達成できるようサポートします。
製造業ニュース解説
製造業、主に購買・調達部門にお勤めの方々に向けた情報を配信しております。
新任の方やベテランの方、管理職を対象とした幅広いコンテンツをご用意しております。
お問い合わせ
コストダウンが利益に直結する術だと理解していても、なかなか前に進めることができない状況。そんな時は、newjiのコストダウン自動化機能で大きく利益貢献しよう!
(β版非公開)