- お役立ち記事
- Tips for supplier evaluation and long-term contracts used by global companies
Tips for supplier evaluation and long-term contracts used by global companies
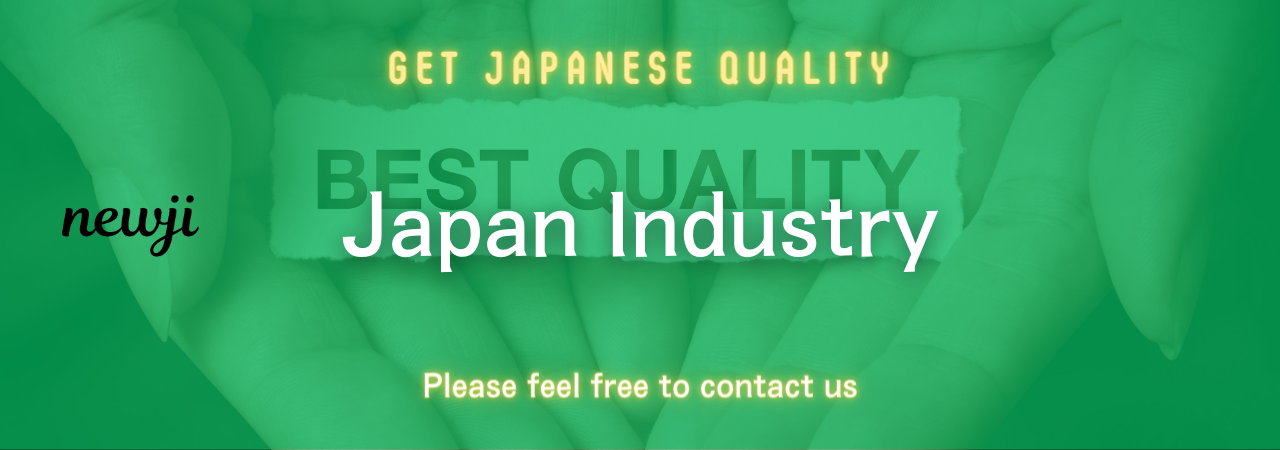
目次
Understanding Supplier Evaluation
Supplier evaluation is a crucial process for companies engaged in global trade.
It involves assessing and analyzing suppliers to ensure they can meet the organization’s standards and requirements.
This process is vital as it helps businesses maintain quality, reduce risks, and ensure reliability in their supply chain.
By conducting thorough evaluations, companies can identify potential weaknesses in their supplier network and address them proactively.
Global businesses, in particular, benefit greatly by ensuring their suppliers adhere to international standards and best practices.
Key Criteria for Supplier Evaluation
There are several important criteria that global companies use when evaluating suppliers.
These criteria include quality, reliability, cost efficiency, and ethical practices.
Quality is paramount; companies must ensure that the products or services provided by a supplier meet or exceed the specified standards.
Reliability involves assessing the supplier’s ability to consistently deliver products or services on time.
Cost efficiency looks at the overall cost-effectiveness of the supplier, balancing price with quality and service.
Finally, ethical practices have gained prominence, ensuring that suppliers comply with environmental standards, labor laws, and fair trade practices.
Quality Assessment
When evaluating suppliers, assessing the quality of goods and services is critical.
Companies often employ quality control measures such as testing samples from a production line or reviewing a supplier’s quality control processes.
ISO certification and other quality management standards can be excellent indicators of a supplier’s commitment to maintaining high-quality standards.
Using data and feedback from previous contracts can also help assess a supplier’s quality performance over time.
Reliability and Delivery Performance
Reliability is a key factor in supplier evaluation, especially for global companies where timely delivery can impact the entire supply chain.
Companies assess delivery times, track record, and ability to handle any unforeseen delays.
Good communication with suppliers can facilitate smoother operations and help address potential issues before they escalate.
Technological tools like supply chain management software can track and monitor supplier performance consistently, contributing to better decision-making.
Cost Efficiency and Financial Stability
Cost efficiency does not mean selecting the cheapest supplier; it involves a balance between cost and quality.
Evaluating the total cost of ownership, which includes shipping, handling, and potential tariffs, provides a clearer picture of the supplier’s value.
Financial stability is another critical aspect, as it determines the supplier’s long-term viability.
Reviewing the supplier’s financial statements or credit ratings can provide insights into their economic health.
Ethical and Sustainable Practices
In today’s business climate, ethical and sustainable practices by suppliers are more important than ever.
Companies evaluate potential suppliers on their adherence to labor laws, environmental policies, and ethical sourcing standards.
Sustainability assessments might include examining how suppliers manage waste or reduce carbon emissions.
Ethical audits can also be conducted to ensure compliance with industry regulations and social responsibility commitments.
Building Long-term Supplier Relationships
After evaluating suppliers, fostering long-term relationships is vital for continuous success.
Establishing clear communication channels and having open dialogues about expectations can lead to more collaborative partnerships.
Regular performance reviews and feedback sessions can help suppliers align with the company’s goals and objectives.
Incentivizing excellent performance through bonuses or increased order volumes can motivate suppliers to maintain high standards.
Negotiating Long-term Contracts
Once a reliable supplier is identified, negotiating a long-term contract can provide stability in the supply chain.
Long-term contracts often include fixed pricing or discounts, protecting against market fluctuations.
They also outline expectations regarding delivery schedules, quality metrics, and compliance requirements.
Contracts should be flexible enough to adapt to changing market conditions but firm enough to ensure consistent performance.
Utilizing Technology in Supplier Management
Technology plays a significant role in supplier evaluation and management.
Many global companies use specialized software to handle supplier assessments, track performance, and manage contracts.
These tools can automate data collection, making it easier to analyze and report on supplier metrics.
By leveraging technology, companies can conduct more comprehensive evaluations with greater efficiency and accuracy.
Continuous Improvement and Adaptation
Successful supplier management requires continuous improvement and adaptation to new challenges.
As the global market evolves, companies should regularly update their evaluation criteria and management practices.
Staying informed about industry trends and emerging technologies can provide a competitive advantage.
By fostering a culture of innovation and flexibility, businesses can ensure they are prepared for future changes in the supply chain landscape.
In conclusion, supplier evaluation and long-term contract management are integral components of successful global operations.
By focusing on quality, reliability, cost efficiency, and ethical practices, companies can build strong supplier relationships that support their strategic goals.
Leveraging technology and committing to continuous improvement can further enhance these efforts, ensuring a robust supply chain resilient to global challenges.
資料ダウンロード
QCD調達購買管理クラウド「newji」は、調達購買部門で必要なQCD管理全てを備えた、現場特化型兼クラウド型の今世紀最高の購買管理システムとなります。
ユーザー登録
調達購買業務の効率化だけでなく、システムを導入することで、コスト削減や製品・資材のステータス可視化のほか、属人化していた購買情報の共有化による内部不正防止や統制にも役立ちます。
NEWJI DX
製造業に特化したデジタルトランスフォーメーション(DX)の実現を目指す請負開発型のコンサルティングサービスです。AI、iPaaS、および先端の技術を駆使して、製造プロセスの効率化、業務効率化、チームワーク強化、コスト削減、品質向上を実現します。このサービスは、製造業の課題を深く理解し、それに対する最適なデジタルソリューションを提供することで、企業が持続的な成長とイノベーションを達成できるようサポートします。
オンライン講座
製造業、主に購買・調達部門にお勤めの方々に向けた情報を配信しております。
新任の方やベテランの方、管理職を対象とした幅広いコンテンツをご用意しております。
お問い合わせ
コストダウンが利益に直結する術だと理解していても、なかなか前に進めることができない状況。そんな時は、newjiのコストダウン自動化機能で大きく利益貢献しよう!
(Β版非公開)