- お役立ち記事
- Titanium alloy rolling technology and its application to the high-precision equipment market
月間77,185名の
製造業ご担当者様が閲覧しています*
*2025年2月28日現在のGoogle Analyticsのデータより
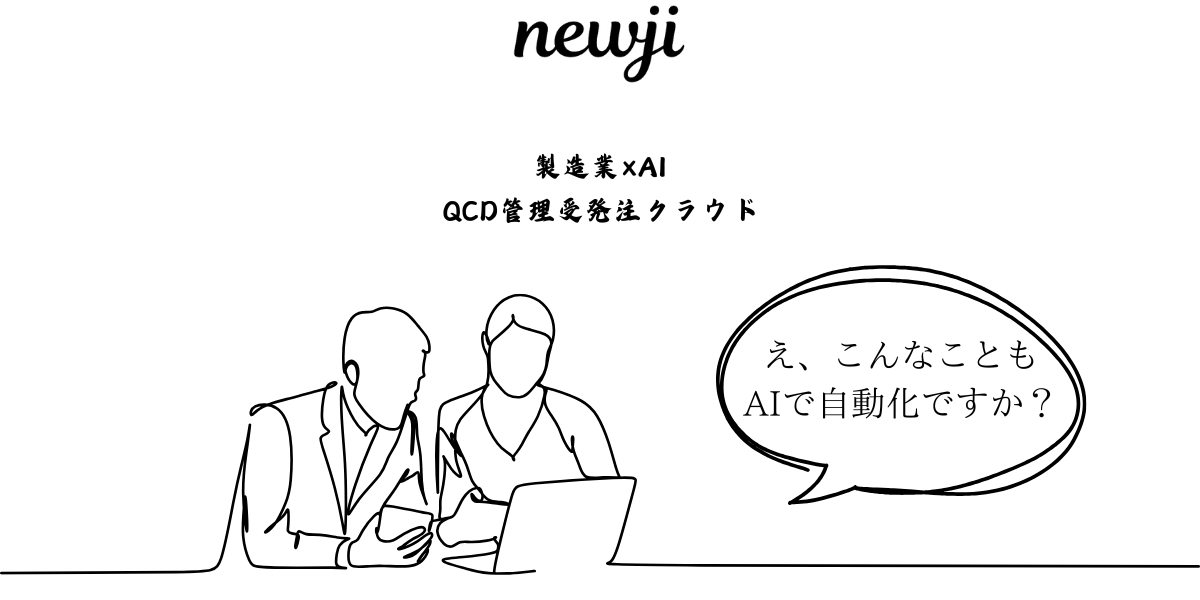
Titanium alloy rolling technology and its application to the high-precision equipment market
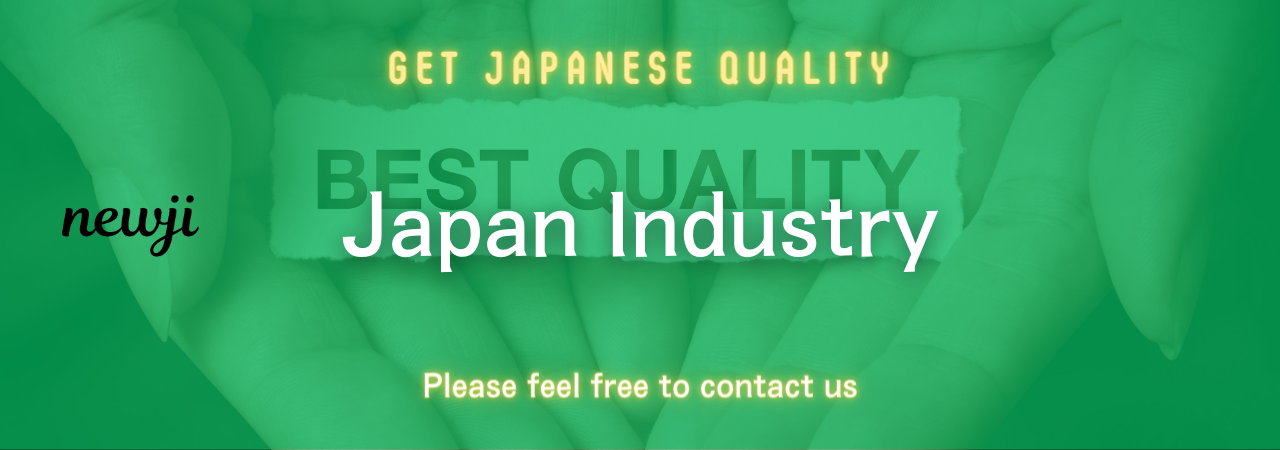
目次
Introduction to Titanium Alloys
Titanium alloys are renowned for their exceptional strength-to-weight ratio, corrosion resistance, and biocompatibility.
These properties make titanium alloys highly sought after in various industries, especially in aerospace, medical, and high-precision equipment.
The unique characteristics of titanium alloys have driven advancements in manufacturing technologies, particularly in rolling technology that enhances material properties and reduces production costs.
Understanding Titanium Alloy Rolling Technology
Rolling technology is a metal forming process where metal stock, in this case, titanium alloy, is passed through one or more pairs of rolls to reduce thickness, based on desired material properties.
There are several rolling methods, including cold rolling and hot rolling, each producing different impacts on the titanium alloy.
Cold Rolling Process
Cold rolling involves processing the titanium alloy at room temperature.
This method enhances the material’s strength and surface finish.
With the absence of heating, the risk of thermal distortion is minimized, ensuring tighter tolerances, which is essential for producing high-precision components.
Hot Rolling Process
On the other hand, hot rolling involves processing the titanium alloy at elevated temperatures.
Heating the material before rolling allows it to be shaped more easily, reducing the power required.
However, the resulting surface finish may require additional processing to meet the high standards of the precision equipment market.
Technical Advancements in Titanium Alloy Rolling
Recent innovations have integrated sensors and artificial intelligence into rolling technology, optimizing process parameters in real-time for improved consistency and efficiency.
Moreover, the development of computer-aided design (CAD) software allows precise modeling, predicting the behaviors of titanium alloys during rolling.
These technological advancements have significantly impacted the industry by reducing lead times and improving the quality of the final products.
Quality Control and Precision
Quality control is integral in the rolling process of titanium alloys, ensuring each product meets stringent industry standards.
Advanced non-destructive testing techniques are utilized to assess the mechanical properties and detect imperfections.
By leveraging real-time data analytics, manufacturers can identify and rectify issues meticulously, ensuring that the titanium alloy components are flawless and reliable.
Application of Titanium Alloys in High-Precision Equipment
The aerospace industry is one of the largest consumers of titanium alloys, leveraging their lightweight nature and ability to withstand extreme conditions.
In aircraft, titanium is used in engines, frames, and fasteners, contributing to fuel efficiency and durability.
Similarly, in the medical field, titanium alloys are vital in the production of surgical instruments, joint replacements, and dental implants, owing to their biocompatibility and strength.
Industrial Advantages
The application of titanium alloy in high-precision equipment extends to the automotive industry, where components such as engine valves and suspension springs benefit from its superior properties.
Even in the energy sector, titanium’s resistance to corrosion at high temperatures makes it ideal for applications in power plants and offshore drilling.
Market Trends and Future Prospects
The demand for titanium alloys is on the rise, fueled by the continuous development of high-precision equipment.
Markets are gradually shifting towards more sustainable and efficient manufacturing processes, with titanium alloys playing a crucial role in this transformation.
Furthermore, the ongoing research and development into new titanium alloy compositions and processing techniques promise to expand their application even further, addressing challenges like cost and environmental impact.
Conclusion
Overall, titanium alloy rolling technology is a fundamental pillar in the advancement of high-precision equipment manufacturing.
Its application across various industries signifies the broad potential and adaptability of titanium alloys, providing an unmatched balance of strength, weight, and durability.
As technology progresses, these alloys are expected to become even more integral to innovative, precise, and sustainable solutions, driving the future of high-precision markets globally.
資料ダウンロード
QCD管理受発注クラウド「newji」は、受発注部門で必要なQCD管理全てを備えた、現場特化型兼クラウド型の今世紀最高の受発注管理システムとなります。
ユーザー登録
受発注業務の効率化だけでなく、システムを導入することで、コスト削減や製品・資材のステータス可視化のほか、属人化していた受発注情報の共有化による内部不正防止や統制にも役立ちます。
NEWJI DX
製造業に特化したデジタルトランスフォーメーション(DX)の実現を目指す請負開発型のコンサルティングサービスです。AI、iPaaS、および先端の技術を駆使して、製造プロセスの効率化、業務効率化、チームワーク強化、コスト削減、品質向上を実現します。このサービスは、製造業の課題を深く理解し、それに対する最適なデジタルソリューションを提供することで、企業が持続的な成長とイノベーションを達成できるようサポートします。
製造業ニュース解説
製造業、主に購買・調達部門にお勤めの方々に向けた情報を配信しております。
新任の方やベテランの方、管理職を対象とした幅広いコンテンツをご用意しております。
お問い合わせ
コストダウンが利益に直結する術だと理解していても、なかなか前に進めることができない状況。そんな時は、newjiのコストダウン自動化機能で大きく利益貢献しよう!
(β版非公開)