- お役立ち記事
- Toaster OEM Manufacturing: Creating High-Quality Kitchen Appliances
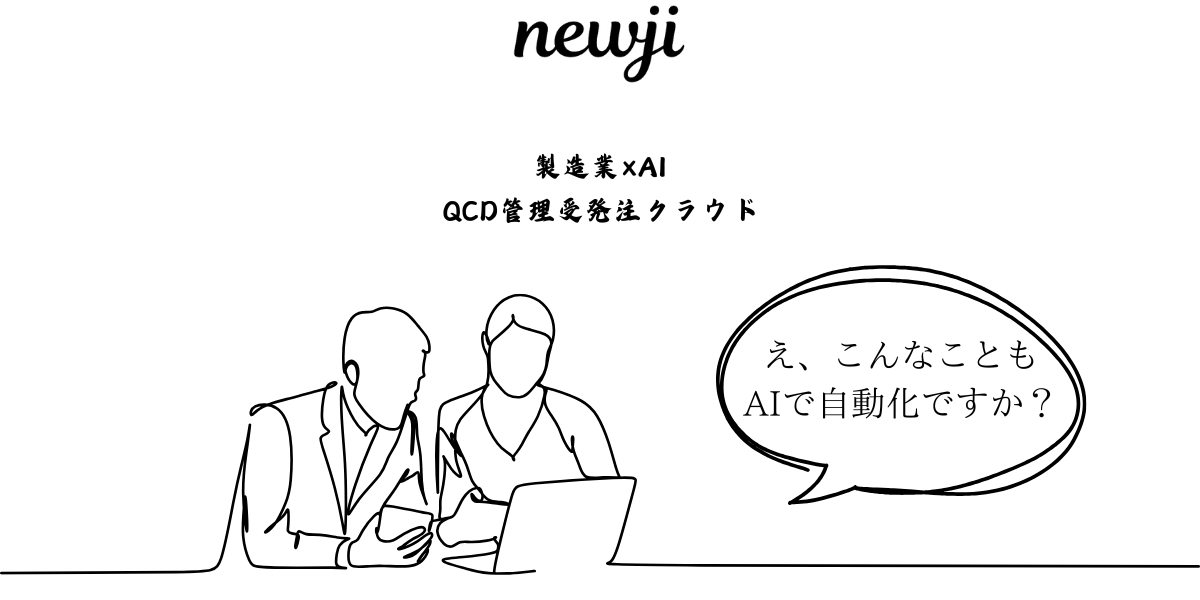
Toaster OEM Manufacturing: Creating High-Quality Kitchen Appliances
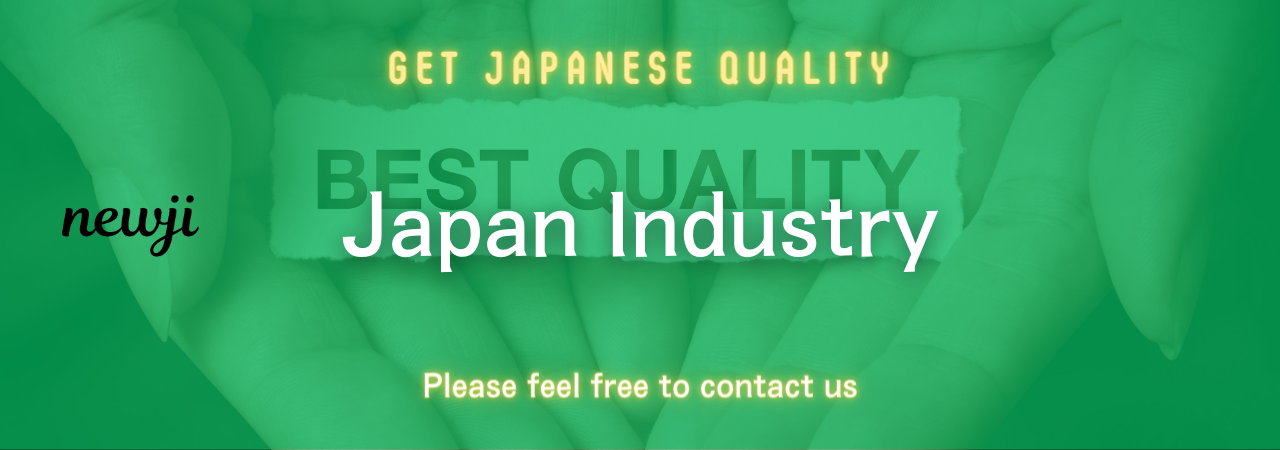
目次
Understanding OEM Manufacturing
OEM stands for Original Equipment Manufacturer.
It refers to companies that produce parts or equipment that another company markets.
In the context of toasters, an OEM manufacturer would make toasters that another company would brand and sell.
OEM manufacturing allows businesses to focus on their strengths.
For example, a company that excels in marketing can focus on promoting and selling toasters without worrying about the complexities of manufacturing.
Why Choose OEM for Toasters?
OEM manufacturing offers several distinct advantages.
Firstly, it reduces the need for investing heavily in manufacturing infrastructure.
This is particularly beneficial for startups or smaller businesses, helping them get up and running with less capital.
Secondly, leveraging the expertise of an OEM manufacturer can ensure high-quality products.
OEM manufacturers often have years of experience and specialized knowledge.
This expertise guarantees a toaster that not only works well but also adheres to safety and quality standards.
Ensuring Quality Control
When using OEM services, maintaining quality is paramount.
High-quality toasters are essential for customer satisfaction and brand loyalty.
OEM manufacturers usually have stringent quality control measures in place.
These measures include multiple checks at various production stages.
Materials are tested before production begins.
The final products undergo rigorous testing to ensure they meet industry standards.
Customizing Your Toaster
One of the highlights of OEM manufacturing is the ability to customize.
Businesses can work closely with manufacturers to create toasters that align with their brand.
Customization options may include design, color, and additional features.
For instance, a company could request unique heating elements that toast bread more evenly.
They could also opt for a stylish design that stands out on kitchen countertops.
These customizations help in creating a unique product that appeals to specific target audiences.
The OEM Manufacturing Process
Understanding the OEM manufacturing process is helpful for businesses considering this route.
Let’s break down the process into simpler steps.
Initial Consultation and Planning
The first step involves discussions between the business and the OEM manufacturer.
During this phase, both parties discuss the desired specifications and features of the toaster.
A detailed plan is laid out, covering everything from design to production timelines.
Prototyping
Once the plans are in place, the manufacturer creates a prototype.
This initial model serves as a sample for what the final product will look like.
Businesses can evaluate the prototype and request any necessary changes.
Production
After finalizing the prototype, mass production begins.
The manufacturer’s team assembles the toasters, ensuring that each unit meets the agreed-upon specifications.
Various production techniques may be used, ranging from automated assembly lines to manual craftsmanship.
Quality Assurance
During and after production, quality checks are performed.
These checks ensure that the toasters are functioning correctly and are safe to use.
Any defective units are identified and corrected before shipping out.
Shipping and Delivery
Once the toasters pass all quality checks, they’re prepared for shipment.
The OEM manufacturer handles the logistics, ensuring the products reach their destination safely and on time.
Businesses then receive the toasters, ready for branding and retail.
Challenges in OEM Manufacturing
Like any business model, OEM manufacturing presents certain challenges.
One of the main challenges is maintaining consistent quality across large production runs.
To mitigate this, choosing an experienced and reputable OEM manufacturer is crucial.
Another challenge is communication.
Clear and precise communication prevents misunderstandings and ensures both parties are on the same page.
Regular updates and meetings help in keeping the project on track.
Costs and Budgeting
Budgeting is another critical aspect.
While OEM manufacturing can be cost-effective in the long run, initial costs for custom designs and prototypes can be high.
Proper budgeting helps manage finances effectively and prevents overspending.
Supply Chain Management
Effective supply chain management is essential.
Any delays in the supply chain can affect production timelines and delivery schedules.
Choosing an OEM manufacturer with a robust supply chain network can help mitigate such risks.
Future Trends in Toaster OEM Manufacturing
The future of OEM manufacturing for toasters looks promising with several emerging trends.
A significant trend is the increasing focus on eco-friendly and energy-efficient toasters.
Consumers are becoming more conscious of their environmental footprint and prefer appliances that are sustainable.
Smart Toasters
Another trend is the integration of smart technology.
Smart toasters with features like Wi-Fi connectivity, app controls, and customized toasting settings are gaining popularity.
OEM manufacturers are investing in research and development to bring these advanced features to market.
Innovative Designs
Design innovation continues to be a focus area.
Sleek, modern designs with advanced features appeal to a tech-savvy audience.
These designs not only perform well but also enhance the aesthetics of a modern kitchen.
Increased Collaboration
Collaboration between OEM manufacturers and businesses is becoming more in-depth.
There’s a growing trend towards co-creation, where businesses and manufacturers work together throughout the product development process.
This collaborative approach ensures that the final product perfectly meets market demands.
OEM manufacturing offers a pathway for businesses to create high-quality, customized toasters without the need for an extensive manufacturing setup.
By understanding the process and effectively managing challenges, businesses can leverage OEM manufacturing to bring innovative and desirable products to market.
資料ダウンロード
QCD調達購買管理クラウド「newji」は、調達購買部門で必要なQCD管理全てを備えた、現場特化型兼クラウド型の今世紀最高の購買管理システムとなります。
ユーザー登録
調達購買業務の効率化だけでなく、システムを導入することで、コスト削減や製品・資材のステータス可視化のほか、属人化していた購買情報の共有化による内部不正防止や統制にも役立ちます。
NEWJI DX
製造業に特化したデジタルトランスフォーメーション(DX)の実現を目指す請負開発型のコンサルティングサービスです。AI、iPaaS、および先端の技術を駆使して、製造プロセスの効率化、業務効率化、チームワーク強化、コスト削減、品質向上を実現します。このサービスは、製造業の課題を深く理解し、それに対する最適なデジタルソリューションを提供することで、企業が持続的な成長とイノベーションを達成できるようサポートします。
オンライン講座
製造業、主に購買・調達部門にお勤めの方々に向けた情報を配信しております。
新任の方やベテランの方、管理職を対象とした幅広いコンテンツをご用意しております。
お問い合わせ
コストダウンが利益に直結する術だと理解していても、なかなか前に進めることができない状況。そんな時は、newjiのコストダウン自動化機能で大きく利益貢献しよう!
(Β版非公開)