- お役立ち記事
- Tolerance design and processing cost optimization method for mechanical parts
Tolerance design and processing cost optimization method for mechanical parts
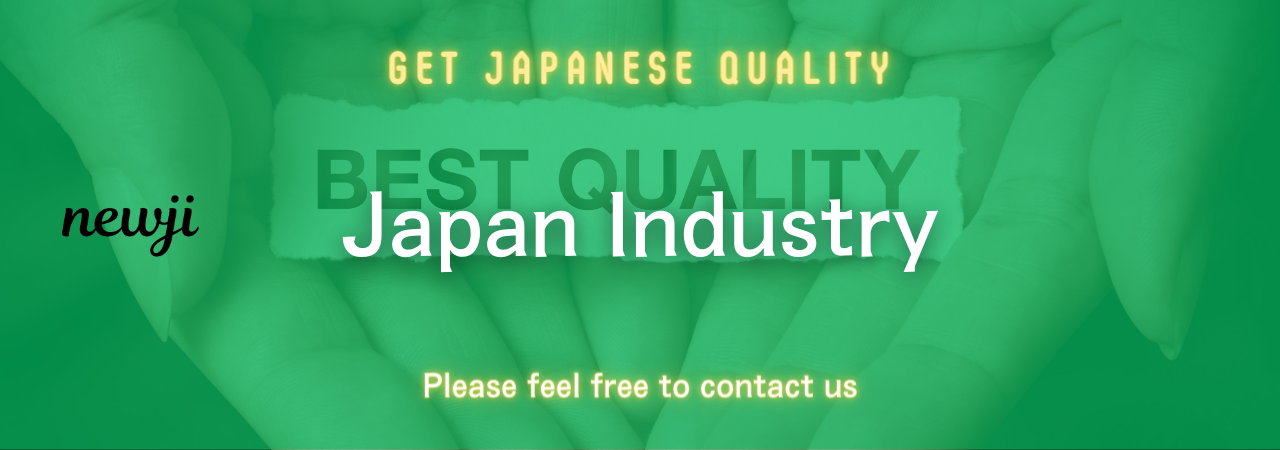
目次
Understanding Tolerance Design
Tolerance design plays a crucial role in the production of mechanical parts.
When manufacturing components, it’s essential to specify the acceptable limits within which parts can vary.
These are known as tolerances.
They ensure each part functions correctly in the assembly without compromising performance.
Tolerances help balance functionality, quality, and cost, making them a critical aspect of design and manufacturing.
There are two primary types of tolerances: dimensional and geometric.
Dimensional tolerances relate to the size of parts, such as length, width, and height.
Geometric tolerances, on the other hand, focus on the shape and form of the components, including aspects like flatness and roundness.
Together, they determine how well components fit and work together.
The Importance of Tolerances in Mechanical Parts
Mechanical parts often undergo rigorous conditions during operation.
Tight tolerances ensure that each part can withstand these conditions, maintaining reliability and safety.
For example, in the automotive industry, even a slight deviation in tolerance can lead to engine failure or reduced fuel efficiency.
Moreover, tolerances help minimize waste during production.
When parts are made to a specific tolerance, there’s less chance for errors and rework, which reduces material loss and energy consumption.
This ultimately lowers production costs and environmental impact.
Optimizing Processing Costs
While tolerances are vital, they also affect manufacturing costs.
Tighter tolerances often require more precise machines and processes, increasing production expenses.
Optimizing processing costs without compromising quality is a balancing act.
By analyzing tolerance requirements, manufacturers can determine which parts require tight tolerances and which can be more flexible.
This approach helps allocate resources efficiently.
Furthermore, incorporating advanced technologies, such as computer-aided design (CAD) and computer-aided manufacturing (CAM), can significantly reduce production costs.
These tools enhance precision and speed, allowing for efficient modification and testing of designs.
Design for Manufacturability
Design for manufacturability (DFM) is a practice that emphasizes ease of manufacturing parts during the design stage.
By considering manufacturing processes from the outset, engineers can make informed decisions about tolerances that impact production efficiency and costs.
For instance, standardizing parts with common tolerances simplifies assembly and reduces tooling expenses.
Additionally, DFM promotes the use of less complex manufacturing techniques, which can result in faster production times and lower costs.
Choosing the Right Materials
The choice of materials also impacts tolerance design and associated costs.
Materials with consistent properties allow for more straightforward manufacturing and better adherence to specified tolerances.
However, it’s crucial to balance material costs with performance needs.
For example, opting for a more expensive material might be justified if it offers longer part life and reduced failure rates.
Engineers should evaluate the trade-offs between material costs and tolerance requirements thoroughly to optimize overall expenses.
Leveraging Advanced Manufacturing Techniques
Incorporating advanced manufacturing techniques is another effective strategy for optimizing processing costs.
Technologies such as additive manufacturing (3D printing) and precision machining offer enhanced control over tolerances, enabling the production of highly accurate parts.
Additive manufacturing, in particular, allows for complex geometries and intricate designs that would be challenging through traditional methods.
This reduces the need for additional machining, lowering overall production costs.
Precision machining, too, provides excellent control over tight tolerances, minimizing waste and rework.
These techniques not only enhance quality but also streamline processes, reducing time and costs.
Implementing Robust Quality Control
Effective quality control measures are essential for maintaining desired tolerances and reducing processing costs.
By identifying defects early in the manufacturing process, companies can avoid widespread issues and costly rework.
Utilizing statistical process control (SPC) and automated inspection methods ensures consistent quality.
SPC involves monitoring and controlling the production process through statistical analysis.
This helps identify trends or deviations from standards, allowing for quick adjustments.
Automated inspections, using technologies such as laser scanning and machine vision, ensure accurate measurements and detect any deviations from specified tolerances.
The Role of Data Analysis
Data analysis plays a significant role in optimizing both tolerance design and processing costs.
By collecting and analyzing data from manufacturing processes, companies can identify patterns and areas for improvement.
This information enables better decision-making and continuous improvement initiatives.
Predictive analytics, for example, can forecast potential issues before they arise, allowing for proactive measures.
Additionally, using data to track performance metrics helps set more realistic tolerance goals and refine manufacturing strategies over time.
Conclusion
Tolerance design and processing cost optimization are vital components of producing high-quality mechanical parts.
By understanding and implementing effective tolerance strategies, manufacturers can ensure reliable, efficient production while minimizing expenses.
Balancing these elements requires a comprehensive approach, incorporating advanced technologies, informed material choices, and robust quality control.
Ultimately, optimizing these factors leads to improved performance, customer satisfaction, and competitive advantage in the marketplace.
資料ダウンロード
QCD調達購買管理クラウド「newji」は、調達購買部門で必要なQCD管理全てを備えた、現場特化型兼クラウド型の今世紀最高の購買管理システムとなります。
ユーザー登録
調達購買業務の効率化だけでなく、システムを導入することで、コスト削減や製品・資材のステータス可視化のほか、属人化していた購買情報の共有化による内部不正防止や統制にも役立ちます。
NEWJI DX
製造業に特化したデジタルトランスフォーメーション(DX)の実現を目指す請負開発型のコンサルティングサービスです。AI、iPaaS、および先端の技術を駆使して、製造プロセスの効率化、業務効率化、チームワーク強化、コスト削減、品質向上を実現します。このサービスは、製造業の課題を深く理解し、それに対する最適なデジタルソリューションを提供することで、企業が持続的な成長とイノベーションを達成できるようサポートします。
オンライン講座
製造業、主に購買・調達部門にお勤めの方々に向けた情報を配信しております。
新任の方やベテランの方、管理職を対象とした幅広いコンテンツをご用意しております。
お問い合わせ
コストダウンが利益に直結する術だと理解していても、なかなか前に進めることができない状況。そんな時は、newjiのコストダウン自動化機能で大きく利益貢献しよう!
(Β版非公開)