- お役立ち記事
- Tool diagnosis technology for machine tools and its application to improving predictive failure life
月間76,176名の
製造業ご担当者様が閲覧しています*
*2025年3月31日現在のGoogle Analyticsのデータより
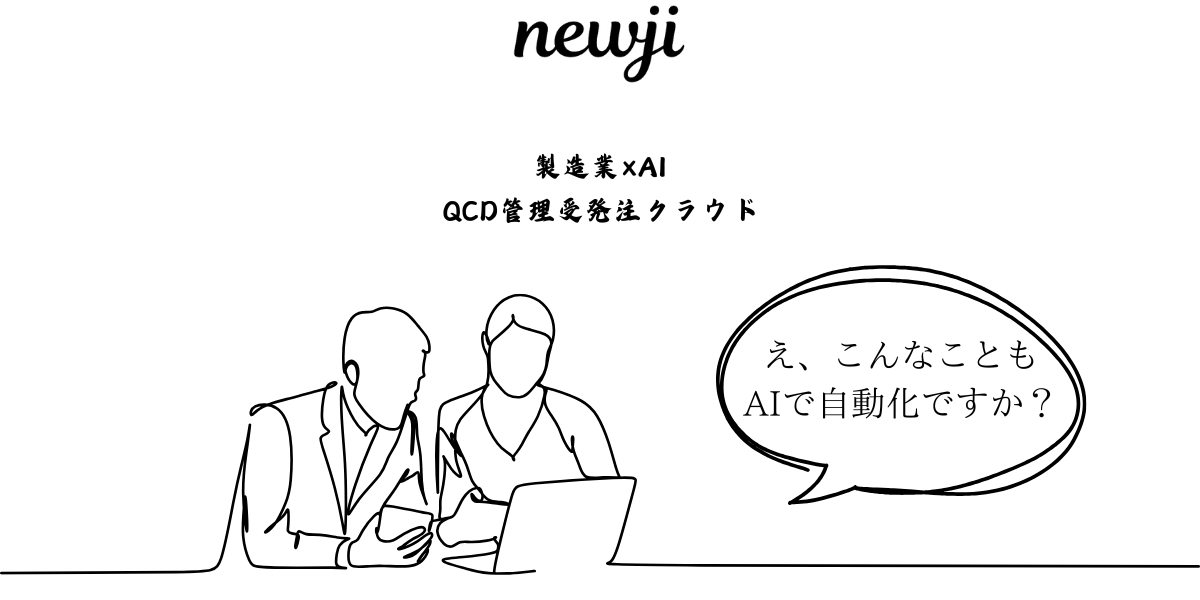
Tool diagnosis technology for machine tools and its application to improving predictive failure life
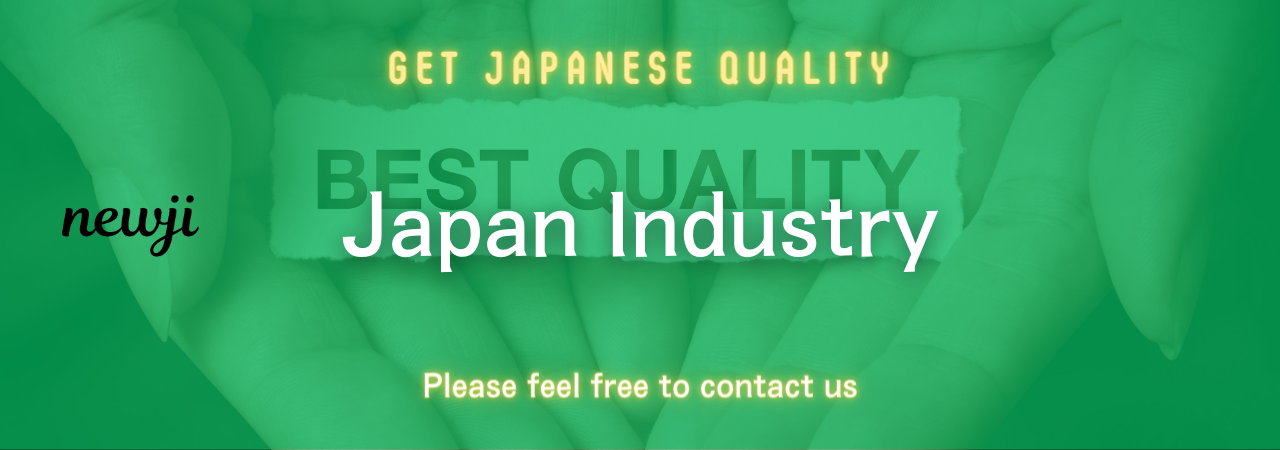
目次
Understanding Tool Diagnosis Technology
Machine tools are fundamental to the manufacturing sector, enabling the production of everything from intricate components to large machinery.
The health and efficiency of these tools are crucial, making tool diagnosis technology a critical area of focus.
Tool diagnosis technology refers to the methods and systems used to assess the condition and performance of machine tools.
This technology encompasses a wide range of techniques, including vibration analysis, acoustic emission measurements, and temperature monitoring, among others.
One of the primary goals of tool diagnosis technology is to predict potential failures before they occur.
By understanding the health of a tool, manufacturers can schedule maintenance proactively, thereby avoiding unexpected downtime and costly repairs.
This predictive capability is vital in maintaining the smooth operation of manufacturing processes.
The Importance of Predictive Maintenance
Predictive maintenance is an approach that uses the data gathered through tool diagnosis technology to predict when a machine tool is likely to fail.
This form of maintenance is based on real-time data, which provides insights into the tool’s operating conditions, allowing for smart decision-making.
Traditional maintenance strategies often fall into two categories: reactive and preventive.
Reactive maintenance responds to breakdowns as they happen, leading to potential disruptions in production workflow.
Preventive maintenance, on the other hand, involves routine checks and maintenance based on a predetermined schedule, which may not adequately account for unforeseen wear and tear.
Predictive maintenance offers a more effective alternative by ensuring maintenance is performed only when necessary.
This targeted approach not only prolongs the life of machine tools but also optimizes resource allocation in terms of labor and parts replacement.
Applications of Tool Diagnosis Technology
Tool diagnosis technology has a wide range of applications across various industries.
In the automotive industry, for instance, ensuring the optimal performance of machine tools is crucial given the high precision required for components.
The aerospace sector similarly depends on the reliability of tools for safety-critical parts.
In the electronics industry, where precision and speed are critical, tool diagnosis technology helps in maintaining the high standards necessary for successful production.
This technology is also applied in heavy machinery and infrastructure, where the failure of machine tools can lead to significant operational and financial repercussions.
Real-World Usage
A practical application of tool diagnosis technology can be seen in real-world manufacturing scenarios.
Companies that have integrated these technologies into their operations report noticeable improvements in efficiency and reduction in downtime.
For instance, by employing advanced diagnostics, a manufacturer can detect unusual vibrations in a CNC (Computer Numerical Control) machine that may indicate an imminent bearing failure.
Once the issue is identified, they can schedule a replacement bearing to be installed during scheduled downtime, thus avoiding an unexpected halt in production.
Technological Advancements Driving Tool Diagnosis
The advancement of sensor technology has greatly enhanced the capabilities of tool diagnosis systems.
Modern sensors can capture extensive data in real-time, providing insights that were previously unattainable.
These sensors are embedded in machine tools, providing continuous monitoring of various parameters such as temperature, pressure, and vibration.
Another significant advancement is the use of machine learning algorithms.
These algorithms analyze historical data and ongoing operational metrics to predict future tool failures with high accuracy.
Machine learning enables continuous improvement in predictive models, making them more reliable and effective over time.
The Role of Big Data
Big data plays a critical role in tool diagnosis technology.
The immense volume of data collected from machine tools needs to be processed and analyzed to extract meaningful insights.
Big data analytics involves complex computations and sophisticated algorithms, helping to convert raw data into actionable intelligence.
Through big data analytics, patterns and trends in tool wear and tear can be identified, allowing for better predictions and maintenance planning.
For manufacturers, this means enhanced efficiency, reduced costs, and improved longevity of their equipment.
Future Prospects of Tool Diagnosis Technology
The future of tool diagnosis technology is promising, with ongoing research and innovations continually pushing boundaries.
One area of potential growth is the integration of Internet of Things (IoT) technology.
IoT can connect all machine tools within a manufacturing facility, providing comprehensive monitoring and diagnostics across the entire production line.
Moreover, advances in artificial intelligence are expected to enhance the predictive capabilities of tool diagnosis systems further.
AI, coupled with IoT, could lead to fully autonomous maintenance regimes, where systems proactively address issues without human intervention.
Another exciting development is the incorporation of blockchain technology for data integrity and security.
Blockchain can ensure that the data collected from machine tools is tamper-proof and reliable, a critical factor for industries where data authenticity is paramount.
Conclusion
Tool diagnosis technology is revolutionizing the way industries maintain and optimize their machine tools.
By harnessing predictive maintenance strategies, manufacturers can significantly improve operational efficiencies, decrease costs, and extend the life expectancy of their tools.
As technology continues to evolve, the capabilities of tool diagnosis systems are only set to become more sophisticated, paving the way for a more reliable and efficient manufacturing future.
資料ダウンロード
QCD管理受発注クラウド「newji」は、受発注部門で必要なQCD管理全てを備えた、現場特化型兼クラウド型の今世紀最高の受発注管理システムとなります。
ユーザー登録
受発注業務の効率化だけでなく、システムを導入することで、コスト削減や製品・資材のステータス可視化のほか、属人化していた受発注情報の共有化による内部不正防止や統制にも役立ちます。
NEWJI DX
製造業に特化したデジタルトランスフォーメーション(DX)の実現を目指す請負開発型のコンサルティングサービスです。AI、iPaaS、および先端の技術を駆使して、製造プロセスの効率化、業務効率化、チームワーク強化、コスト削減、品質向上を実現します。このサービスは、製造業の課題を深く理解し、それに対する最適なデジタルソリューションを提供することで、企業が持続的な成長とイノベーションを達成できるようサポートします。
製造業ニュース解説
製造業、主に購買・調達部門にお勤めの方々に向けた情報を配信しております。
新任の方やベテランの方、管理職を対象とした幅広いコンテンツをご用意しております。
お問い合わせ
コストダウンが利益に直結する術だと理解していても、なかなか前に進めることができない状況。そんな時は、newjiのコストダウン自動化機能で大きく利益貢献しよう!
(β版非公開)