- お役立ち記事
- Torque control technology for automatic screw tightening machines and examples of its introduction in the automated manufacturing industry
月間77,185名の
製造業ご担当者様が閲覧しています*
*2025年2月28日現在のGoogle Analyticsのデータより
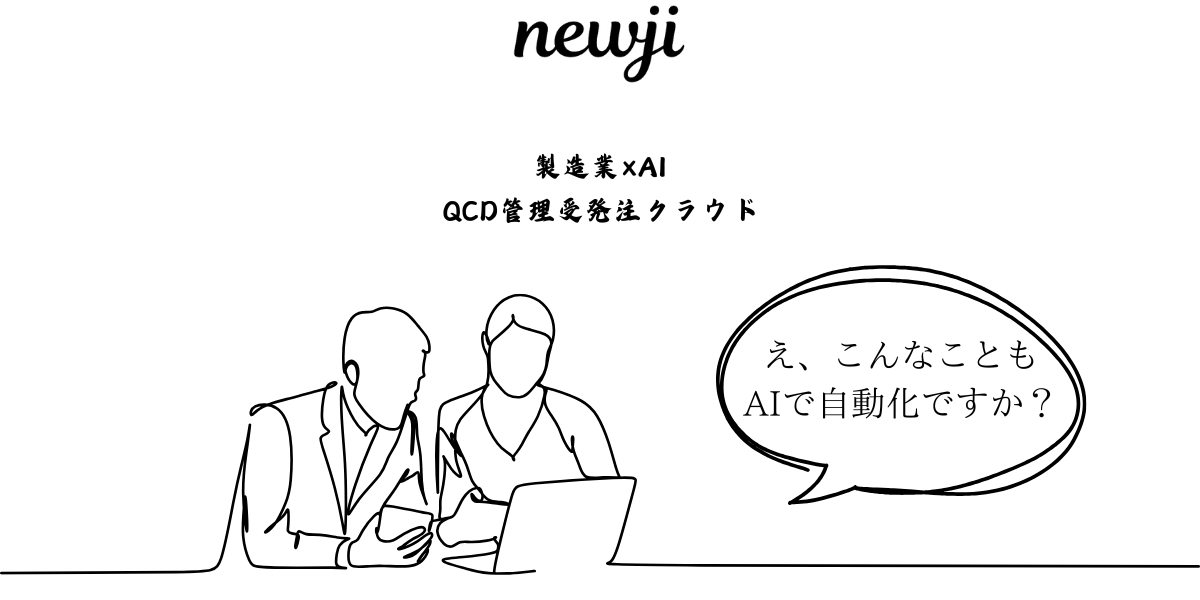
Torque control technology for automatic screw tightening machines and examples of its introduction in the automated manufacturing industry
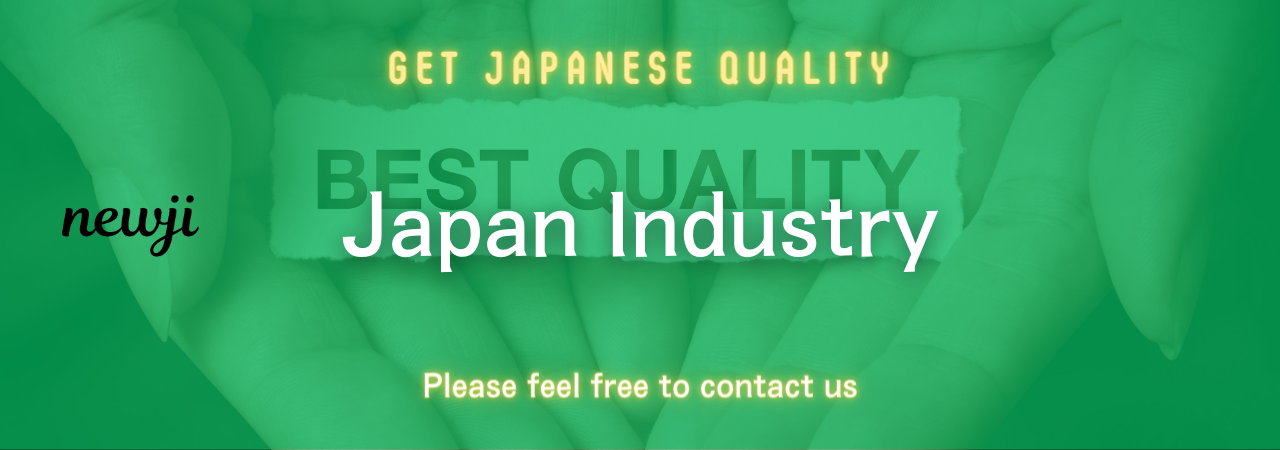
目次
Understanding Torque Control Technology
Torque control technology is an advanced system used in automatic screw tightening machines to ensure that screws are tightened with the precise amount of force necessary for proper assembly.
This technology is fundamental in the automated manufacturing industry, where the efficiency and precision of assembly processes are crucial.
Manufacturers use these machines to maintain consistency, reduce downtime, and improve the quality of assembled products.
Torque control systems are designed to measure and regulate the torque applied to screws, ensuring they are neither under-tightened nor over-tightened.
This control is vital because incorrect torque can lead to defective products, safety hazards, or equipment failures.
How Torque Control Works
Automatic screw tightening machines utilize sensors and software to monitor the torque applied during the screwing process.
These machines are equipped with advanced electronics that can adjust the torque in real-time, accommodating changes in materials, temperature, or other variables that might affect the required torque.
The sensors detect the resistance of the screw as it is tightened and relay this information to the machine’s controller.
Based on this data, the controller adjusts the power applied to reach the desired torque setting accurately.
Operators can program these machines with specific torque values for different screw types and materials, ensuring consistent results across various applications.
Benefits of Torque Control Technology
The implementation of torque control technology brings numerous advantages to the manufacturing industry.
Firstly, it enhances product quality by ensuring all screws are tightened to the correct specifications.
This consistency reduces the risk of defects and improves the reliability of the final product.
Secondly, torque control increases production efficiency.
Automatic screw tightening machines operate faster than human hands, reducing the time needed for assembly processes.
Moreover, the reduction in human error leads to less rework and waste, ultimately decreasing production costs.
Another significant benefit is the enhancement of workplace safety.
By automating the screwing process, manufacturers can minimize the involvement of workers in potentially hazardous tasks, reducing the risk of injury from repetitive strain or accidents.
Applications in the Automated Manufacturing Industry
Torque control technology is widely used across various sectors within the automated manufacturing industry.
One prominent example is the automotive industry, where every part of a vehicle needs to be carefully assembled to ensure safety and performance.
Automatic screw tightening machines equipped with torque control are essential in assembling engines, chassis, and other critical components.
In the electronics sector, precision is crucial, especially when dealing with delicate components like circuit boards.
Torque control ensures that screws are tightened just enough to secure these components without damaging them.
This precision is essential for maintaining the functionality and longevity of electronic products.
Additionally, in the aerospace industry, where the stakes are incredibly high, the reliability of components is non-negotiable.
Torque control technology ensures that fasteners in aircraft are tightened with exact precision, maintaining the integrity of the aircraft and ensuring passenger safety.
Examples of Successful Implementation
Numerous companies have successfully integrated torque control technology into their production lines, showcasing the impact of this innovation.
For instance, a leading automotive manufacturer implemented torque control systems in their assembly lines, resulting in a significant decline in product recalls due to loose screws.
This not only saved the company substantial costs but also improved their brand reputation.
Similarly, an electronics firm adopted torque control technology for assembling consumer gadgets.
The precise tightening of screws led to fewer returns under warranty, as the products met the high standards expected by customers.
This implementation has enhanced customer satisfaction and loyalty.
In another case, an aerospace company integrated torque control systems in their assembly line for aircraft components.
This investment resulted in improved safety compliance, as well as cost savings by reducing maintenance needs and extending the lifecycle of aircraft parts.
Choosing the Right Torque Control System
Selecting the appropriate torque control system is crucial for manufacturers looking to incorporate this technology into their operations.
Factors to consider include the type of screw materials, required torque ranges, and the specific industry standards that need to be met.
Manufacturers should also choose machines from reputable suppliers to ensure reliability and support in case of technical issues.
Consulting with experts and analyzing production needs helps in selecting a system that aligns with operational goals.
Regular maintenance and calibration of torque control systems are essential to ensure their continued accuracy and performance.
This maintenance, in turn, supports efficient production processes and consistent product quality.
Conclusion
Incorporating torque control technology in automatic screw tightening machines offers prolific benefits across the automated manufacturing industry.
By ensuring precise tightening, manufacturers can enhance product quality, boost efficiency, reduce costs, and improve safety.
As industries continue to automate and innovate, torque control systems will remain an integral component in bolstering the reliability and quality of assembly processes.
Embracing this technology not only propels operational efficiency but also fortifies the competitiveness of businesses in today’s rapidly changing industrial landscape.
資料ダウンロード
QCD管理受発注クラウド「newji」は、受発注部門で必要なQCD管理全てを備えた、現場特化型兼クラウド型の今世紀最高の受発注管理システムとなります。
ユーザー登録
受発注業務の効率化だけでなく、システムを導入することで、コスト削減や製品・資材のステータス可視化のほか、属人化していた受発注情報の共有化による内部不正防止や統制にも役立ちます。
NEWJI DX
製造業に特化したデジタルトランスフォーメーション(DX)の実現を目指す請負開発型のコンサルティングサービスです。AI、iPaaS、および先端の技術を駆使して、製造プロセスの効率化、業務効率化、チームワーク強化、コスト削減、品質向上を実現します。このサービスは、製造業の課題を深く理解し、それに対する最適なデジタルソリューションを提供することで、企業が持続的な成長とイノベーションを達成できるようサポートします。
製造業ニュース解説
製造業、主に購買・調達部門にお勤めの方々に向けた情報を配信しております。
新任の方やベテランの方、管理職を対象とした幅広いコンテンツをご用意しております。
お問い合わせ
コストダウンが利益に直結する術だと理解していても、なかなか前に進めることができない状況。そんな時は、newjiのコストダウン自動化機能で大きく利益貢献しよう!
(β版非公開)