- お役立ち記事
- Torque Sensors: Technology and Applications in Manufacturing
月間76,176名の
製造業ご担当者様が閲覧しています*
*2025年3月31日現在のGoogle Analyticsのデータより
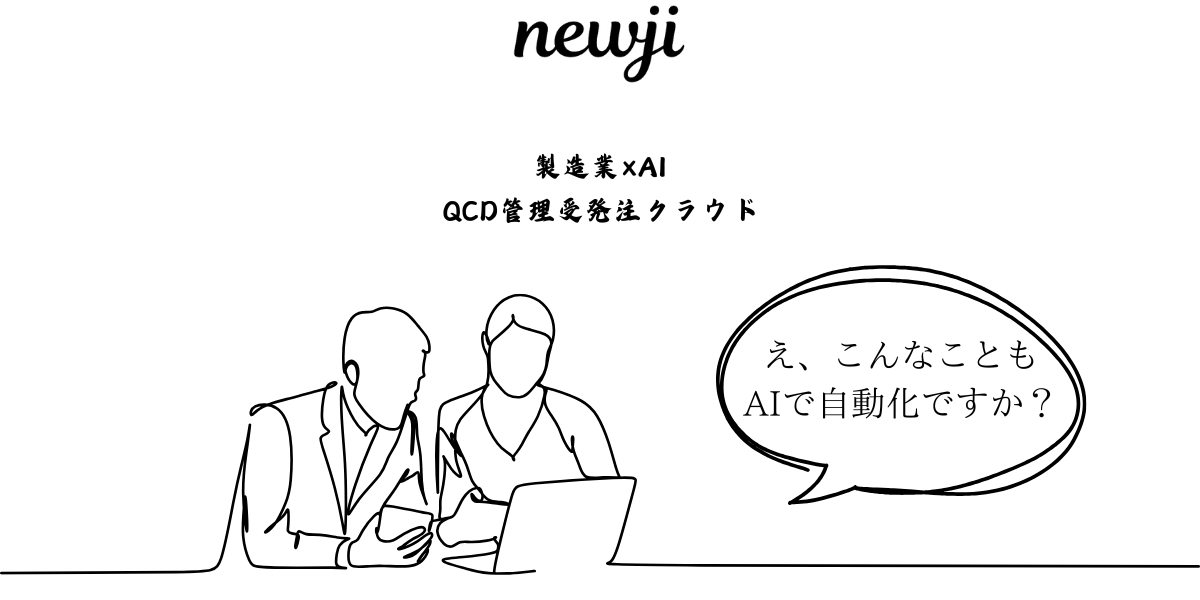
Torque Sensors: Technology and Applications in Manufacturing
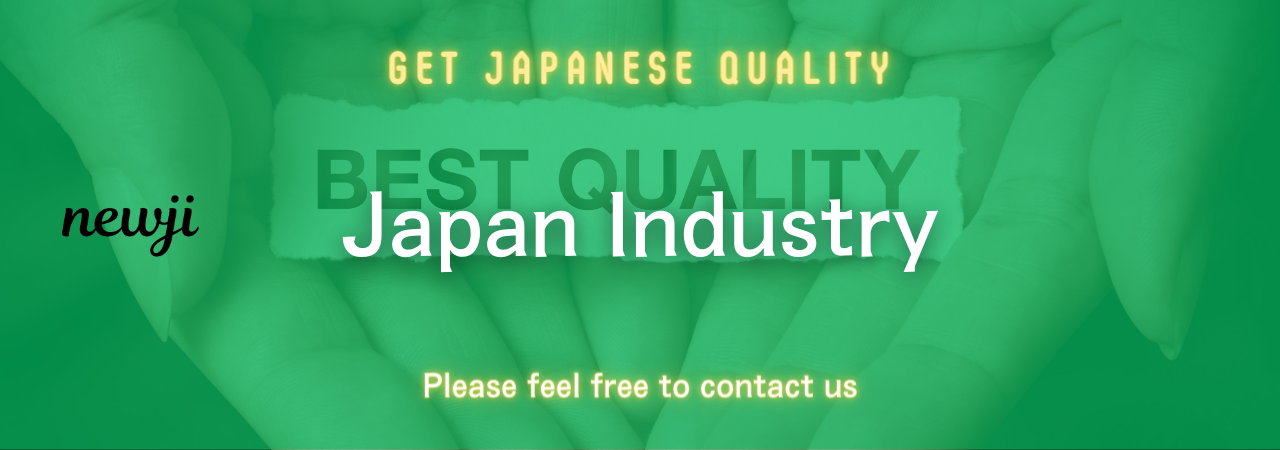
目次
Understanding Torque Sensors
Torque sensors, also known as torque transducers or torque meters, are devices used to measure the amount of torque applied to an object.
This measurement is critical in various industrial and manufacturing processes because it ensures that machinery operates within its designed mechanical limits.
By accurately measuring torque, these sensors help prevent equipment failures and optimize productivity.
Torque sensors are classified into two main types: reaction torque sensors and rotary torque sensors.
Reaction torque sensors measure static torque, meaning they capture torque without the shaft in rotation.
In contrast, rotary torque sensors measure dynamic torque, where the shaft is in motion.
The Technology Behind Torque Sensors
Torque sensors utilize several technologies to measure torque, including strain gauge, piezoelectric, and magnetoelastic principles.
Strain Gauge Torque Sensors
Strain gauge technology is one of the most common methods used in torque sensors.
A strain gauge operates on the principle that an elastic body changes its electrical resistance when deformed.
In a torque sensor, these gauges are often bonded to the shaft or housing that experiences the torque.
Changes in resistance due to deformation are then converted into an electrical signal proportional to the torque applied.
Piezoelectric Torque Sensors
Piezoelectric torque sensors use crystals that generate an electrical charge in response to mechanical stress.
These sensors are known for their high sensitivity and ability to measure rapid changes in dynamic torque applications.
Their drawback, however, lies in their limited ability to measure static torque.
Magnetoelastic Torque Sensors
Magnetoelastic torque sensors exploit the properties of ferromagnetic materials that change magnetic field properties under mechanical stress.
These sensors are robust and can operate in harsh environments, making them ideal for automotive and industrial applications.
They provide contactless measurement, which prevents wear and tear, thus extending the sensor’s lifecycle.
Applications of Torque Sensors in Manufacturing
Torque sensors are pivotal in the manufacturing sector due to their diverse applications, which include quality control, maintenance, and performance assessment.
Assembly Line Monitoring
In assembly lines, torque sensors ensure that joints are fastened correctly by measuring the torque applied to bolts and screws.
This monitoring helps maintain product quality and reduces the risk of loose fittings, which could lead to product failures.
Machine Maintenance
Monitoring the torque output from motors and gearboxes helps detect anomalies that indicate potential mechanical failures.
Early detection of such issues through torque measurement can significantly reduce downtime and maintenance costs.
Robotics
In robotics, torque sensors play an essential role in force control, which allows robots to perform tasks requiring precision and delicacy, such as assembling delicate parts or handling fragile materials.
This capability enables manufacturers to automate complex tasks that were once manual, increasing both efficiency and safety.
Automotive Industry
In the automotive industry, torque sensors are used extensively in engine and transmission testing.
They help ensure that components endure under specified loads, providing insights into the performance and durability of engines.
Furthermore, torque measurement is vital in developing electric vehicles where motor control requires accurate torque feedback for optimal performance.
Advantages of Using Torque Sensors
The integration of torque sensors in manufacturing comes with several benefits:
Improved Precision
Torque sensors provide accurate measurements that lead to higher precision in machinery operation.
This precision enhances product quality and reduces the likelihood of errors in assembly processes.
Increased Efficiency
By providing real-time data, torque sensors enable quick decision-making, allowing for immediate adjustments in manufacturing processes.
This data-driven approach minimizes downtime and speeds up production lines.
Enhanced Safety
Torque sensors help maintain equipment within its operational limits, preventing accidents caused by overloading machinery.
This monitoring safeguards both the equipment and the personnel operating it.
Cost Savings
By reducing the risk of equipment failure and optimizing maintenance schedules, torque sensors contribute to significant cost savings over time.
The predictive maintenance enabled by these sensors ensures that resources are spent judiciously.
Challenges and Considerations
While torque sensors offer numerous advantages, their integration and operation come with specific challenges.
Firstly, selecting the appropriate type of sensor for a given application necessitates a thorough understanding of both the manufacturing process and sensor capabilities.
Improper selection can lead to inaccurate readings or sensor damage.
Moreover, installing torque sensors can be complex, especially in existing machinery where integration requires modifications.
This complexity can sometimes deter manufacturers from adopting torque sensors despite their benefits.
Additionally, environmental factors such as temperature, humidity, and electromagnetic interference can affect sensor accuracy.
Therefore, it’s vital to choose sensors that withstand the specific conditions of the intended application.
The Future of Torque Sensors in Manufacturing
As technology continues to evolve, the future of torque sensors in manufacturing looks promising.
Advancements such as wireless sensors and miniaturization are making torque sensors more versatile and easier to implement across various applications.
The rise of the Internet of Things (IoT) is also enhancing the capabilities of torque sensors.
With IoT, these sensors can integrate into broader networks, offering real-time data analysis and remote monitoring.
In conclusion, torque sensors are crucial tools in modern manufacturing, providing data that enhances product quality, operational efficiency, and safety.
As industries continue to adopt smart manufacturing techniques, the demand for precise and reliable torque measurement will likely grow, driving further innovation in sensor technology.
資料ダウンロード
QCD管理受発注クラウド「newji」は、受発注部門で必要なQCD管理全てを備えた、現場特化型兼クラウド型の今世紀最高の受発注管理システムとなります。
ユーザー登録
受発注業務の効率化だけでなく、システムを導入することで、コスト削減や製品・資材のステータス可視化のほか、属人化していた受発注情報の共有化による内部不正防止や統制にも役立ちます。
NEWJI DX
製造業に特化したデジタルトランスフォーメーション(DX)の実現を目指す請負開発型のコンサルティングサービスです。AI、iPaaS、および先端の技術を駆使して、製造プロセスの効率化、業務効率化、チームワーク強化、コスト削減、品質向上を実現します。このサービスは、製造業の課題を深く理解し、それに対する最適なデジタルソリューションを提供することで、企業が持続的な成長とイノベーションを達成できるようサポートします。
製造業ニュース解説
製造業、主に購買・調達部門にお勤めの方々に向けた情報を配信しております。
新任の方やベテランの方、管理職を対象とした幅広いコンテンツをご用意しております。
お問い合わせ
コストダウンが利益に直結する術だと理解していても、なかなか前に進めることができない状況。そんな時は、newjiのコストダウン自動化機能で大きく利益貢献しよう!
(β版非公開)