- お役立ち記事
- “Toyota-style problem-solving method” and practical points for field leaders
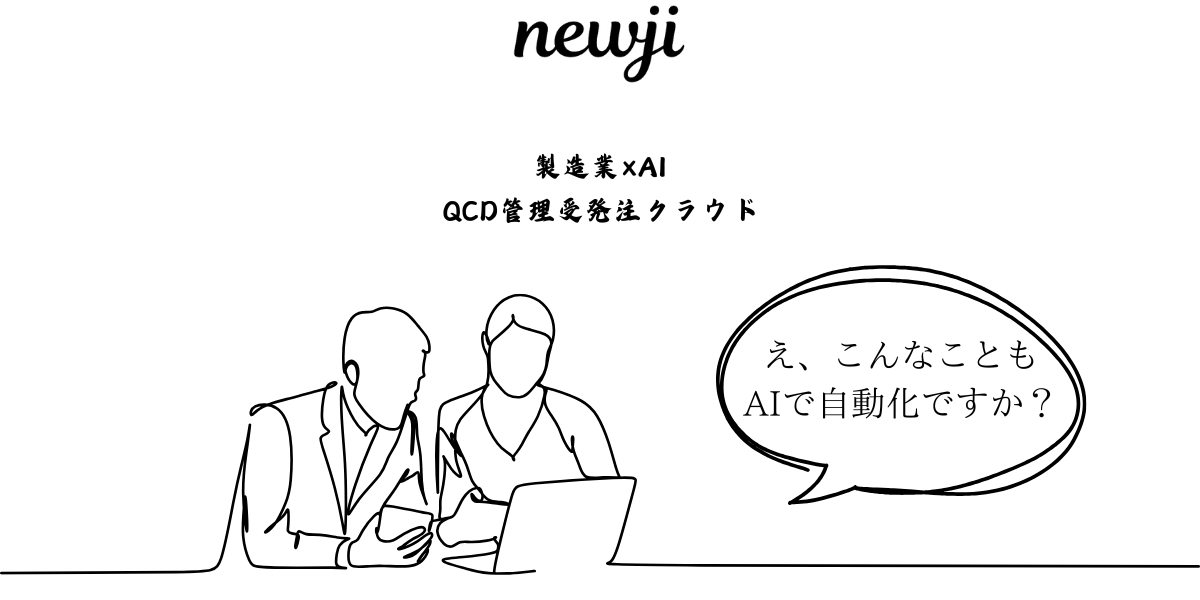
“Toyota-style problem-solving method” and practical points for field leaders
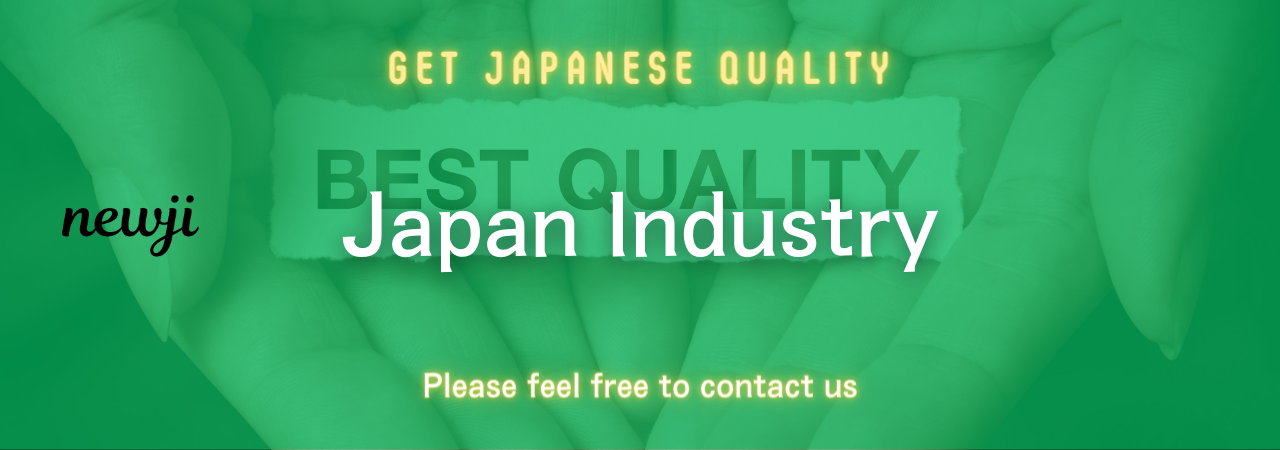
目次
Introduction to Toyota-Style Problem-Solving
Problem-solving is an essential skill in any industry or organization.
At the heart of efficiency and continuous improvement is the ability to address issues as they arise and refine processes for better results.
Toyota, a company renowned for its innovative approach to manufacturing and management, has developed a distinctive problem-solving method that has earned acclaim worldwide.
The Toyota-style problem-solving method is not just a technique; it’s a philosophy that emphasizes understanding the root cause of a problem, involving every level of an organization, and fostering a culture of relentless improvement.
This approach has become a cornerstone of the Toyota Production System (TPS) and offers valuable insights for field leaders looking to enhance operational efficiency.
The Essence of the Toyota-Style Problem-Solving Method
The Toyota-style approach prioritizes structured thinking to solve problems effectively and sustainably.
Central to this method is the Plan-Do-Check-Act (PDCA) cycle, which provides a framework for iterative problem-solving.
It involves careful planning, implementing solutions, reviewing outcomes, and making necessary adjustments.
Plan: Identify and Analyze the Problem
The first phase of the Toyota-style method focuses on identifying and understanding the problem clearly.
Toyota emphasizes the importance of grasping the actual conditions on the ground – a philosophy known as “Genchi Genbutsu,” or “go and see for yourself.”
This involves direct observation and analysis, often using tools like the “Five Whys” to explore the root causes beyond surface-level symptoms.
Do: Develop and Implement a Solution
After thoroughly understanding the problem, the next step involves brainstorming possible solutions.
The aim is to devise effective measures that address the problem’s root causes rather than symptoms.
Implementation follows a structured plan where solutions are put into practice on a small scale to test their viability.
Check: Evaluate the Results
Evaluation is crucial in the Toyota-style problem-solving method.
After implementing the solution, it’s vital to measure and analyze its effectiveness.
This involves comparing actual results against the expected outcomes to determine the solution’s success.
Act: Refine and Standardize
If the solution proves effective, the next crucial step is to standardize it.
Documenting the process ensures that the improvement becomes part of regular operations.
If the solution doesn’t meet expectations, the cycle begins anew, using insights gained to develop better alternatives.
Practical Points for Field Leaders
Implementing the Toyota-style problem-solving approach can bring significant benefits to leaders in various industries.
Here are some actionable tips on how field leaders can integrate these methods effectively.
Foster a Culture of Continuous Improvement
The Toyota philosophy thrives in environments that value ongoing development and learning.
Encouraging a culture where every team member is empowered to identify and resolve issues is crucial.
Leaders should foster an atmosphere where employees feel valued for their contributions to improving processes.
Encourage Collaboration and Team Involvement
Effective problem-solving often requires diverse perspectives.
Field leaders should encourage collaboration across different teams and departments.
By involving individuals with various expertise, it’s possible to gain insights that one might not have recognized alone.
Empower Employees with Training
The success of the Toyota-style problem-solving method depends on the skill and knowledge of those implementing it.
Training programs should be established to ensure that all employees are well-versed in the techniques and principles vital for effective problem-solving.
Utilize Visual Management Tools
Visual tools like charts and graphs can be incredibly useful in problem-solving.
They bring data to life and can help in quickly understanding complex information.
Field leaders should encourage the use of visual aids to simplify information sharing and decision-making.
Evaluate and Adjust Regularly
Field leaders should regularly review processes and solutions to ensure they remain effective.
Flexibility is key; adjustments may be required as new information becomes available or as conditions change.
Such evaluations help in maintaining a high standard of operations.
Conclusion
The Toyota-style problem-solving method is a comprehensive and thoughtful approach that brings people, processes, and innovation together.
For field leaders, incorporating this method can lead to substantial improvements in operational efficiency and team collaboration.
By following the structured steps of the PDCA cycle and fostering a proactive culture, leaders can ensure ongoing success and drive continuous progress within their organizations.
Understanding and applying these principles offers a pathway to not only resolving issues but transforming the way challenges are approached.
Leaders who are committed to mastering these techniques will find them invaluable in achieving long-term excellence and sustainable success.
資料ダウンロード
QCD調達購買管理クラウド「newji」は、調達購買部門で必要なQCD管理全てを備えた、現場特化型兼クラウド型の今世紀最高の購買管理システムとなります。
ユーザー登録
調達購買業務の効率化だけでなく、システムを導入することで、コスト削減や製品・資材のステータス可視化のほか、属人化していた購買情報の共有化による内部不正防止や統制にも役立ちます。
NEWJI DX
製造業に特化したデジタルトランスフォーメーション(DX)の実現を目指す請負開発型のコンサルティングサービスです。AI、iPaaS、および先端の技術を駆使して、製造プロセスの効率化、業務効率化、チームワーク強化、コスト削減、品質向上を実現します。このサービスは、製造業の課題を深く理解し、それに対する最適なデジタルソリューションを提供することで、企業が持続的な成長とイノベーションを達成できるようサポートします。
オンライン講座
製造業、主に購買・調達部門にお勤めの方々に向けた情報を配信しております。
新任の方やベテランの方、管理職を対象とした幅広いコンテンツをご用意しております。
お問い合わせ
コストダウンが利益に直結する術だと理解していても、なかなか前に進めることができない状況。そんな時は、newjiのコストダウン自動化機能で大きく利益貢献しよう!
(Β版非公開)