- お役立ち記事
- Toyota style quality control method and quality creation
Toyota style quality control method and quality creation
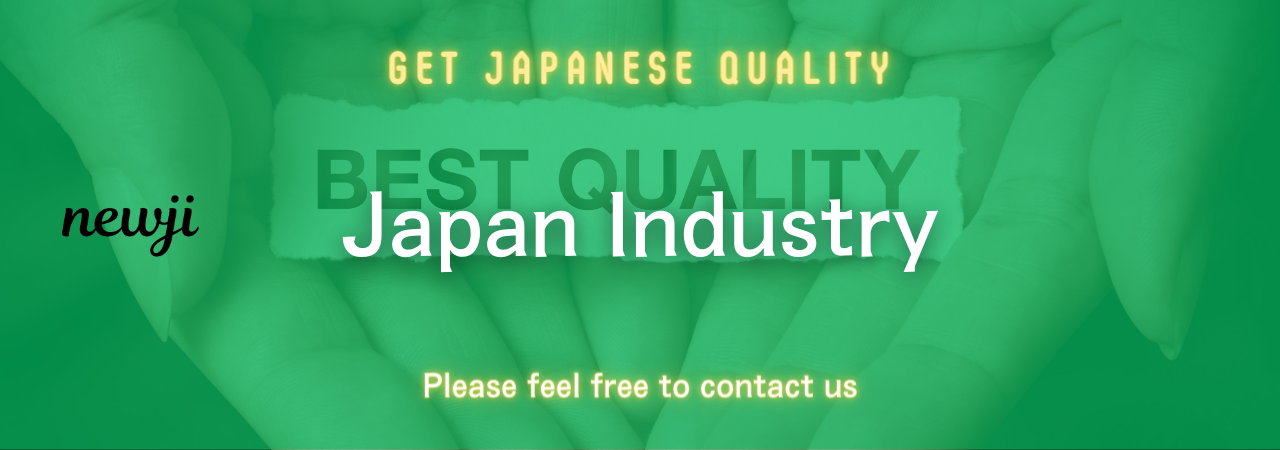
目次
Understanding Toyota’s Quality Control Method
Toyota has long been recognized as a leader in the automotive industry, not only for its innovation but also for its consistent quality control measures.
The company’s success can be largely attributed to its unique approach to quality management, which has set a benchmark for other manufacturers around the globe.
Toyota’s style of quality control is deeply rooted in its organizational culture and operational philosophy, often encapsulated in the Toyota Production System (TPS) and its renowned principle of continuous improvement, known as “Kaizen”.
The Toyota Production System (TPS)
At the heart of Toyota’s quality control lies the Toyota Production System (TPS).
TPS is an integrated approach that combines elements of just-in-time production, lean manufacturing, and a strong focus on eliminating waste.
Through TPS, Toyota strives to achieve efficiency in production by reducing excess inventory, minimizing waste, and ensuring every part of the manufacturing process adds value to the final product.
One of the critical components of TPS is Jidoka, which refers to the automation with a human touch.
This principle empowers workers to stop the production line when they encounter a defect or anomaly in the process.
By addressing quality issues as they arise, Jidoka allows for immediate problem-solving, preventing defects from affecting the final product.
Another essential aspect of TPS is just-in-time production.
This involves producing only what is needed, when it is needed, and in the amount needed.
By aligning production schedules with market demand, Toyota minimizes excess inventory and creates a more efficient production process.
Kaizen: The Pursuit of Continuous Improvement
Kaizen, or continuous improvement, is a fundamental principle that drives Toyota’s quality control strategy.
This philosophy encourages all employees, from line workers to executives, to constantly seek ways to improve operations and eliminate inefficiencies.
Kaizen fosters an environment where suggestions for improvement are not only welcomed but actively sought out.
Small, incremental changes are accumulated over time to significantly enhance the overall processes and product quality.
Toyota’s commitment to Kaizen means that the company is always pushing the boundaries of efficiency and quality, ensuring that its vehicles remain competitive and reliable.
Quality Circles
Another tool Toyota uses to achieve stellar quality control is the implementation of quality circles.
These are small groups of employees who come together regularly to identify, analyze, and resolve work-related issues.
By empowering workers at all levels to contribute to solving problems, Toyota harnesses the collective expertise and creativity of its workforce.
Quality circles not only improve operational efficiency but also foster a culture of teamwork and ownership.
By involving employees directly in the process of quality control, Toyota ensures that everyone feels responsible for the company’s success.
Poka-Yoke: Mistake-Proofing
To prevent human error during the manufacturing process, Toyota employs a methodology known as “Poka-Yoke,” which translates to mistake-proofing.
Poka-Yoke involves designing workplace processes and equipment in a manner that makes errors virtually impossible or immediately detectable.
For example, in Toyota’s assembly lines, tools may only fit in one orientation or sequence, ensuring that components are attached correctly.
By eliminating the possibility of mistakes, Poka-Yoke enhances product reliability and reduces the need for rework.
Standardization and Flexibility
Standardization is another cornerstone of Toyota’s quality control methodology.
By establishing clear, precise procedures for every process, Toyota ensures consistency and reliability in its production line.
This approach not only reduces variability but also fosters easier problem identification and corrective actions when deviations occur.
Despite the emphasis on standardization, Toyota maintains flexibility in its operations.
The company values adaptability and ensures that procedures can be tweaked as necessary to meet evolving market demands and technological advancements.
This balance between consistency and flexibility allows Toyota to maintain high-quality standards while responding efficiently to change.
Supplier Relationships
Toyota’s commitment to quality extends beyond its production lines to include its suppliers.
Strong, collaborative relationships with suppliers are integral to Toyota’s quality control strategy.
Toyota works closely with its suppliers to ensure that they adhere to the same principles and practices, including quality standards and continuous improvement methodologies.
By establishing long-term relationships and fostering trust, Toyota enables suppliers to contribute more effectively to the production process.
These partnerships play a crucial role in maintaining the high quality of parts and materials used in Toyota vehicles.
Impact on the Automotive Industry
Toyota’s quality control methods have significantly influenced the automotive industry.
Many manufacturers have adopted elements of the Toyota Production System, recognizing the benefits of efficiency and quality it delivers.
The company’s focus on continuous improvement, worker involvement, and mistake-proofing has become a benchmark for operational excellence.
As the automotive industry faces challenges such as technological advancement and market fluctuations, Toyota’s approach to quality control continues to provide a roadmap for sustainable success.
Companies looking to improve their quality outcomes can learn from Toyota’s systematic and people-centered strategies.
Conclusion
In conclusion, Toyota’s style of quality control and quality creation reflects a deep-seated commitment to excellence within all facets of its operations.
Through the Toyota Production System, Kaizen, and innovative concepts like Jidoka and Poka-Yoke, Toyota has set the standard for manufacturing quality.
Its methodologies emphasize continual improvement, employee engagement, and robust supplier relationships, ensuring durable and innovate vehicles.
The significant impact Toyota has had on the automotive industry underscores the importance of these practices, serving as a guiding model for future advancements in manufacturing quality worldwide.
Emulating Toyota’s strategies can help other organizations enhance their own production processes and meet the growing expectations of consumers for quality, reliable products.
資料ダウンロード
QCD調達購買管理クラウド「newji」は、調達購買部門で必要なQCD管理全てを備えた、現場特化型兼クラウド型の今世紀最高の購買管理システムとなります。
ユーザー登録
調達購買業務の効率化だけでなく、システムを導入することで、コスト削減や製品・資材のステータス可視化のほか、属人化していた購買情報の共有化による内部不正防止や統制にも役立ちます。
NEWJI DX
製造業に特化したデジタルトランスフォーメーション(DX)の実現を目指す請負開発型のコンサルティングサービスです。AI、iPaaS、および先端の技術を駆使して、製造プロセスの効率化、業務効率化、チームワーク強化、コスト削減、品質向上を実現します。このサービスは、製造業の課題を深く理解し、それに対する最適なデジタルソリューションを提供することで、企業が持続的な成長とイノベーションを達成できるようサポートします。
オンライン講座
製造業、主に購買・調達部門にお勤めの方々に向けた情報を配信しております。
新任の方やベテランの方、管理職を対象とした幅広いコンテンツをご用意しております。
お問い合わせ
コストダウンが利益に直結する術だと理解していても、なかなか前に進めることができない状況。そんな時は、newjiのコストダウン自動化機能で大きく利益貢献しよう!
(Β版非公開)