- お役立ち記事
- Traceability System Design for Food Production Lines
Traceability System Design for Food Production Lines
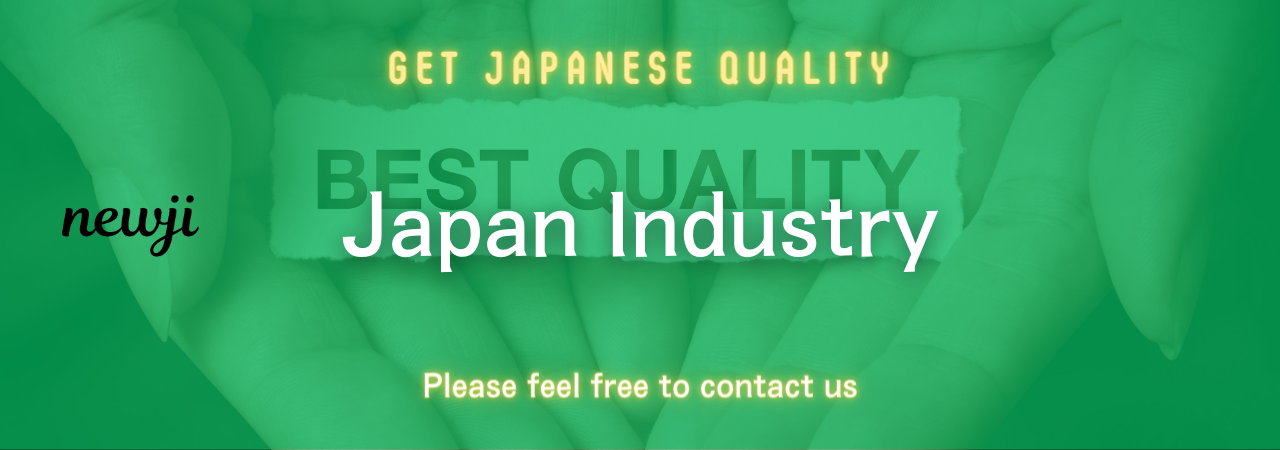
In today’s global market, ensuring the quality and safety of food products has become paramount.
One pivotal method to achieve this is through an efficient traceability system design for food production lines.
A robust traceability system not only ensures food safety but also boosts consumer confidence and complies with regulatory standards.
This article delves into the essential components of an effective traceability system and provides insights on achieving an optimal design.
目次
Understanding Traceability in Food Production
Traceability in food production refers to the ability to track and trace the movement of food products through various stages of the supply chain.
This includes tracking from raw material procurement to processing, packaging, distribution, and finally, to the consumer’s table.
By implementing a thorough traceability system, food producers can quickly identify and address any issues that may arise, ensuring that only safe and high-quality products reach consumers.
Why Is Traceability Important?
Traceability is crucial for several reasons.
First and foremost, it significantly enhances food safety.
By monitoring each stage of production, companies can identify contamination sources, isolate defective batches, and prevent further distribution of contaminated products.
Additionally, traceability allows for swift and efficient recalls, minimizing health risks and potential legal liabilities.
Another advantage is the boost in consumer confidence.
When consumers know that a company has a reliable traceability system, they are more likely to trust the brand and its products.
This trust can translate into increased sales and a stronger market position.
Finally, traceability ensures compliance with both local and international food safety regulations.
Authorities worldwide have stringent standards in place, and non-compliance can lead to significant fines and reputational damage.
Key Components of a Traceability System
Developing an effective traceability system involves several critical components, each playing an integral role in the overall functionality.
1. Data Collection
The first step in traceability system design is comprehensive data collection.
Accurate and detailed records of every stage in the production process are essential.
This includes information on raw materials, processing methods, packaging details, and distribution channels.
Automated systems and barcoding technology can help streamline data collection, ensuring accuracy and minimizing human error.
2. Record-Keeping
Once data is collected, it must be meticulously recorded and stored.
Digital record-keeping systems are preferred over manual ones due to their efficiency and reliability.
These systems should be capable of managing large volumes of data and providing easy access when needed.
3. Unique Identification
Unique identifiers, such as barcodes or QR codes, are pivotal in linking data to specific products.
These identifiers must be consistently applied to ensure seamless tracking through every stage of the supply chain.
Implementing Globally Unique Identifiers (GUIDs) can further enhance traceability by providing a standard reference.
4. Data Integration
An effective traceability system requires seamless integration of data across various stages of production.
This often involves integrating systems like Enterprise Resource Planning (ERP) and Warehouse Management Systems (WMS).
These systems should communicate efficiently to maintain a continuous flow of information.
5. Real-Time Monitoring
Real-time monitoring allows for immediate detection of issues and swift response.
Implementing sensor technology and IoT devices can provide real-time data on various parameters such as temperature, humidity, and location, ensuring optimal conditions are maintained throughout the production process.
Steps to Design an Effective Traceability System
Now that we understand the key components, let’s discuss the steps involved in designing an effective traceability system for food production lines.
1. Define Objectives
The first step in designing a traceability system is defining clear objectives.
Identify what you aim to achieve with the system, whether it’s ensuring product quality, enhancing food safety, or complying with regulatory standards.
Having a clear understanding of your goals will guide the design process.
2. Assess Current Processes
Analyze your existing production processes to identify any gaps or inefficiencies.
Evaluate your current data collection, record-keeping, and monitoring practices.
This assessment will give you a clear understanding of areas that need improvement and help determine the best approach for system integration.
3. Choose the Right Technology
Selecting the appropriate technology is crucial for the effectiveness of your traceability system.
Consider solutions that offer automated data collection, digital record-keeping, and real-time monitoring.
Evaluate various software options and choose one that suits your specific needs and budget.
Ensure the technology you choose is scalable and can adapt to future growth.
4. Implement Unique Identification
Implementing unique identifiers across your production line is essential for seamless tracking.
Ensure that these identifiers are consistently applied and integrated into your system.
Barcoding and QR codes are popular options due to their reliability and ease of implementation.
5. Train Your Team
A traceability system is only as effective as the people operating it.
Conduct thorough training sessions to ensure your team understands the system and their roles in maintaining it.
Regular training updates are also essential to keep your team informed about new processes and technologies.
6. Test and Validate
Before full-scale implementation, conduct thorough testing and validation of your traceability system.
Simulate various scenarios to ensure the system accurately tracks and manages data.
Make any necessary adjustments to address any issues that arise during testing.
7. Continuous Improvement
Traceability systems require continuous improvement to remain effective.
Regularly review your system’s performance and make necessary updates to keep pace with technological advancements and changing regulatory requirements.
Solicit feedback from your team and incorporate their insights into your improvement processes.
Conclusion
Designing a traceability system for food production lines is a complex but essential task.
A well-implemented system not only ensures food safety but also builds consumer trust, enhances operational efficiency, and ensures regulatory compliance.
By focusing on key components such as data collection, record-keeping, unique identification, data integration, and real-time monitoring, food producers can achieve a robust traceability system.
Following a structured approach, from defining objectives to continuous improvement, will enable companies to effectively track and trace their products.
In today’s demanding market, investing in a reliable traceability system is not just a compliance requirement; it’s a strategic advantage that can set your business apart.
資料ダウンロード
QCD調達購買管理クラウド「newji」は、調達購買部門で必要なQCD管理全てを備えた、現場特化型兼クラウド型の今世紀最高の購買管理システムとなります。
ユーザー登録
調達購買業務の効率化だけでなく、システムを導入することで、コスト削減や製品・資材のステータス可視化のほか、属人化していた購買情報の共有化による内部不正防止や統制にも役立ちます。
NEWJI DX
製造業に特化したデジタルトランスフォーメーション(DX)の実現を目指す請負開発型のコンサルティングサービスです。AI、iPaaS、および先端の技術を駆使して、製造プロセスの効率化、業務効率化、チームワーク強化、コスト削減、品質向上を実現します。このサービスは、製造業の課題を深く理解し、それに対する最適なデジタルソリューションを提供することで、企業が持続的な成長とイノベーションを達成できるようサポートします。
オンライン講座
製造業、主に購買・調達部門にお勤めの方々に向けた情報を配信しております。
新任の方やベテランの方、管理職を対象とした幅広いコンテンツをご用意しております。
お問い合わせ
コストダウンが利益に直結する術だと理解していても、なかなか前に進めることができない状況。そんな時は、newjiのコストダウン自動化機能で大きく利益貢献しよう!
(Β版非公開)