- お役立ち記事
- Training for Immediate Effectiveness in Manufacturing: Basic Manufacturing Practices
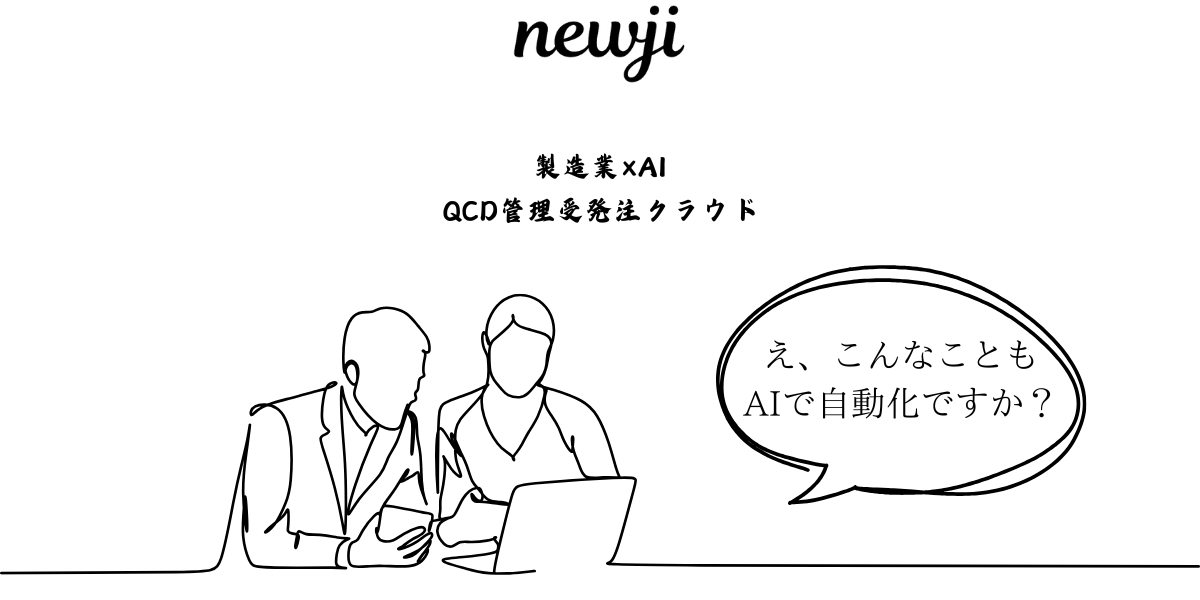
Training for Immediate Effectiveness in Manufacturing: Basic Manufacturing Practices
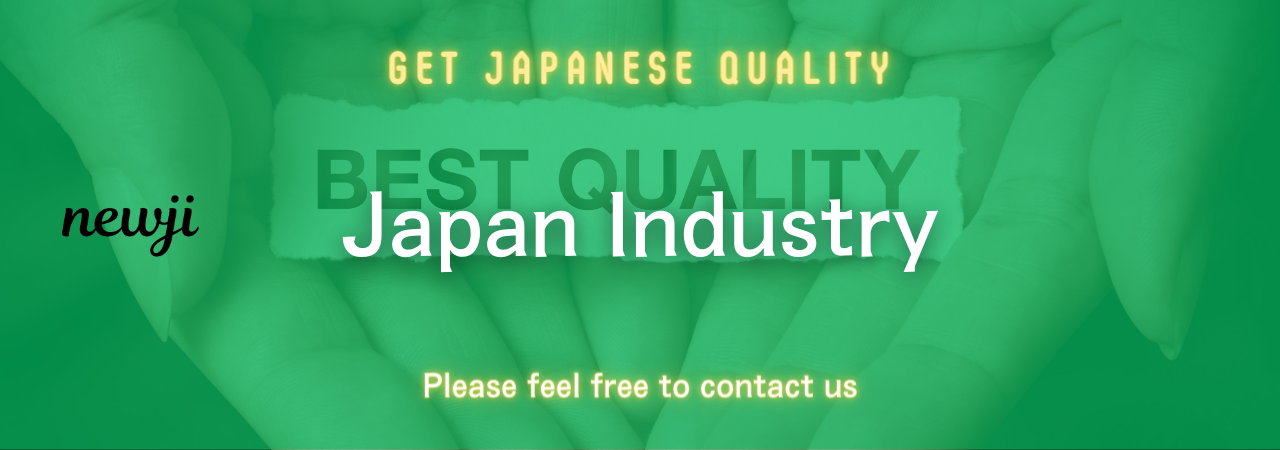
Manufacturing is a critical component of today’s economy, and understanding basic manufacturing practices is essential for improving productivity and efficiency in the industry.
For employees and managers alike, training focused on immediate effectiveness can lead to significant improvements in performance.
This article delves into several fundamental concepts and techniques that drive success in the manufacturing sector.
目次
Importance of Training in Manufacturing
Effective training programs in manufacturing are crucial for ensuring that employees are well-equipped to handle their tasks.
Proper training helps in maintaining safety standards, boosting productivity, and enhancing the overall quality of the products being manufactured.
When workers are knowledgeable about the basics, they can contribute more effectively to the company’s goals.
Safety First
One of the primary focuses of training in manufacturing is safety.
Employees must be trained on the correct use of machinery, personal protective equipment (PPE), and emergency procedures.
Regular safety drills and updates on new safety protocols are necessary to keep everyone informed and prepared.
A strong emphasis on safety not only protects workers but also minimizes costly accidents and downtime.
Quality Control
Another critical aspect of manufacturing training is quality control.
Employees should understand the standards and specifications that products must meet.
Training programs should include instructions on how to inspect products, identify defects, and take corrective actions.
Maintaining high-quality standards is essential for customer satisfaction and long-term success.
Core Manufacturing Concepts
In addition to safety and quality control, several core manufacturing concepts are integral to effective training programs.
These include lean manufacturing, the 5S methodology, and Just-In-Time (JIT) production.
Understanding and implementing these concepts can lead to improved efficiency and reduced waste.
Lean Manufacturing
Lean manufacturing is a systematic approach to minimizing waste without sacrificing productivity.
It involves identifying and eliminating non-value-added activities in the production process.
Training employees on lean principles, such as value stream mapping and continuous improvement, can help in creating a more efficient and cost-effective operation.
5S Methodology
The 5S methodology is a workplace organization technique that stands for Sort, Set in order, Shine, Standardize, and Sustain.
Training employees in 5S helps create a clean, organized, and efficient work environment.
This not only improves productivity but also enhances safety and quality.
By maintaining an orderly workplace, employees can perform their tasks more efficiently and with fewer disruptions.
Just-In-Time (JIT) Production
Just-In-Time (JIT) production is a strategy that focuses on producing only what is needed, when it is needed, and in the quantity needed.
Training employees on JIT principles can help in reducing inventory costs and improving production flow.
This approach minimizes waste and ensures that resources are used efficiently.
Practical Training Techniques
To effectively convey these manufacturing concepts, a combination of training techniques should be used.
These techniques include hands-on training, simulations, and continuous learning opportunities.
Hands-On Training
Hands-on training is essential for helping employees understand the practical application of manufacturing concepts.
By working directly with machinery and equipment, workers can gain valuable experience and confidence.
This type of training is particularly effective for demonstrating safety procedures and troubleshooting techniques.
Simulations
Simulations are an excellent way to provide realistic training scenarios without the risks associated with real-life operations.
They allow employees to practice their skills in a controlled environment, where mistakes can be made and corrected without consequences.
Simulations can be used to teach everything from machine operation to emergency response procedures.
Continuous Learning
Manufacturing is an ever-evolving field, and continuous learning is necessary to keep up with new technologies and practices.
Employers should provide opportunities for ongoing education and skills development.
This could include regular workshops, online courses, or attendance at industry conferences.
By promoting a culture of continuous improvement, companies can ensure that their workforce remains knowledgeable and adaptable.
Measuring the Effectiveness of Training
It’s important to measure the effectiveness of training programs to ensure they are meeting their goals.
This can be done through various methods, such as performance evaluations, feedback surveys, and production metrics.
Performance Evaluations
Regular performance evaluations can help in assessing the impact of training on individual employees.
These evaluations should consider factors such as safety compliance, quality of work, and productivity levels.
By identifying areas where employees excel or need improvement, employers can tailor future training efforts to address specific needs.
Feedback Surveys
Feedback surveys provide valuable insights into how employees perceive the training programs.
They can highlight areas of the training that are particularly effective or areas that may require adjustment.
Surveys should be conducted anonymously to encourage honest responses.
Production Metrics
Tracking production metrics before and after training can provide concrete data on the effectiveness of the training programs.
Metrics such as defect rates, production times, and downtime can indicate whether training has led to improvements in the manufacturing process.
Regular analysis of these metrics helps in maintaining a focus on continuous improvement and achieving operational goals.
Conclusion
Training for immediate effectiveness in manufacturing is essential for achieving high levels of safety, quality, and productivity.
By focusing on core manufacturing concepts, utilizing practical training techniques, and measuring the effectiveness of training programs, companies can ensure that their workforce is well-prepared to meet the demands of the industry.
A well-trained workforce is a crucial asset in any manufacturing operation, driving success and growth in a competitive market.
資料ダウンロード
QCD調達購買管理クラウド「newji」は、調達購買部門で必要なQCD管理全てを備えた、現場特化型兼クラウド型の今世紀最高の購買管理システムとなります。
ユーザー登録
調達購買業務の効率化だけでなく、システムを導入することで、コスト削減や製品・資材のステータス可視化のほか、属人化していた購買情報の共有化による内部不正防止や統制にも役立ちます。
NEWJI DX
製造業に特化したデジタルトランスフォーメーション(DX)の実現を目指す請負開発型のコンサルティングサービスです。AI、iPaaS、および先端の技術を駆使して、製造プロセスの効率化、業務効率化、チームワーク強化、コスト削減、品質向上を実現します。このサービスは、製造業の課題を深く理解し、それに対する最適なデジタルソリューションを提供することで、企業が持続的な成長とイノベーションを達成できるようサポートします。
オンライン講座
製造業、主に購買・調達部門にお勤めの方々に向けた情報を配信しております。
新任の方やベテランの方、管理職を対象とした幅広いコンテンツをご用意しております。
お問い合わせ
コストダウンが利益に直結する術だと理解していても、なかなか前に進めることができない状況。そんな時は、newjiのコストダウン自動化機能で大きく利益貢献しよう!
(Β版非公開)