- お役立ち記事
- Transforming Japanese Manufacturing: Success Stories of Supply Chain BPR
Transforming Japanese Manufacturing: Success Stories of Supply Chain BPR
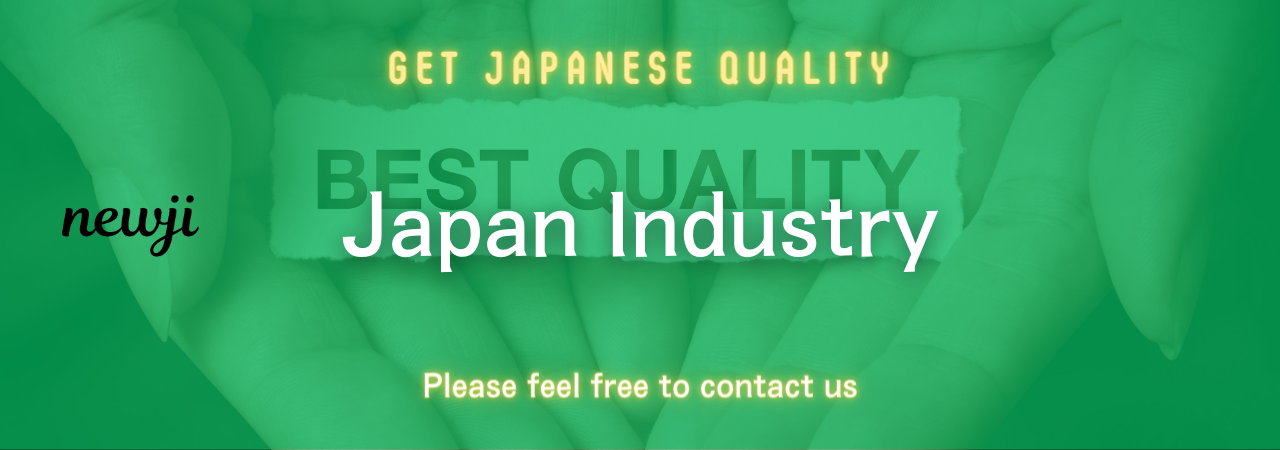
目次
Introduction
Japanese manufacturing has long been revered for its stellar quality, commitment to innovation, and dedication to precision.
For decades, Japanese companies have set the benchmark in various industries, from automotive to electronics, creating a blueprint for excellence.
A crucial aspect that has underpinned this success is the robust and efficient supply chain management system.
A specific practice that stands out is Business Process Re-engineering (BPR), which has been a transformative tool for many Japanese manufacturers, offering significant improvements in efficiency, cost-effectiveness, and adaptability to market changes.
This article will delve into the success stories of supply chain BPR in Japanese manufacturing.
We’ll explore practical content from procurement and purchasing perspectives, the advantages and disadvantages of BPR, supplier negotiation techniques, market conditions, and best practices directly from the field.
Understanding Business Process Re-engineering (BPR)
Before diving into specific success stories, it’s essential to understand what BPR involves.
Business Process Re-engineering is a strategic approach where companies rethink and redesign their existing processes to achieve significant improvements in critical performance measures such as cost, quality, service, and speed.
Unlike incremental improvements, BPR aims for radical changes that can provide a substantial leap in efficiency and effectiveness.
The Key Components of BPR
Identifying Processes for Re-engineering:
Not all processes warrant BPR.
Companies must identify which processes are crucial and which have the most potential for drastic improvement.
Focusing on Outcomes:
The aim should be to achieve specific, measurable outcomes.
These could include reduced costs, shorter cycles, or higher customer satisfaction.
Breaking Traditional Practices:
BPR often requires breaking away from traditional business practices and hierarchies.
This can mean adopting new technologies, re-allocating resources, and fostering a culture of innovation.
Success Stories in Japanese Manufacturing
Toyota’s Just-in-Time (JIT) System
One of the most iconic success stories in Japanese manufacturing is Toyota’s Just-in-Time (JIT) inventory system.
Developed in the 1970s, this approach revolutionized the way companies handle their inventories and supply chains.
The fundamental principle of JIT is to receive goods only when needed in the production process, which minimizes inventory costs and reduces waste.
Advantages:
The JIT system significantly reduces holding costs and enhances flexibility in production.
It also fosters stronger relationships with suppliers since frequent deliveries require close collaboration.
Challenges:
Implementing JIT requires highly reliable suppliers who can deliver on time, every time.
Fluctuations in demand or supply chain disruptions can severely impact production.
Panasonic’s Lean Manufacturing Initiatives
Panasonic has implemented numerous BPR initiatives under the umbrella of Lean Manufacturing.
The company focused on eliminating waste, improving process efficiency, and continuously improving production methods.
These efforts have enabled Panasonic to maintain a competitive edge in the global market.
Advantages:
Lean Manufacturing has led to significant cost savings, improved quality, and faster production times.
The emphasis on continuous improvement has enabled Panasonic to adapt to market changes quickly.
Challenges:
Lean Manufacturing requires a cultural shift within the organization.
Employees must be committed to continuous improvement, and this often requires ongoing training and education.
The Field Perspective: Procurement and Purchasing
In the field of procurement and purchasing, BPR can offer profound benefits.
However, it requires a strategic approach and a deep understanding of market conditions and supplier dynamics.
Advantages and Disadvantages
Advantages:
Cost Reduction: Re-engineering procurement processes can lead to significant cost savings.
This includes negotiating better terms with suppliers, optimizing inventory levels, and reducing procurement cycle times.
Improved Supplier Relationships: BPR often involves closer collaboration with suppliers.
By working closely with suppliers, companies can achieve better quality and more reliable deliveries.
Increased Flexibility: Streamlined procurement processes enable companies to respond more quickly to market changes and customer demands.
Disadvantages:
Implementation Cost: The initial cost of implementing BPR can be high.
This includes investment in new technologies, training, and potential disruptions during the transition phase.
Resistance to Change: Employees and suppliers may be resistant to change.
Overcoming this resistance requires effective change management strategies and constant communication.
Supplier Negotiation Techniques
Negotiation plays a crucial role in the success of BPR initiatives in procurement.
Here are some field-tested techniques:
Collaborative Approach: Adopt a win-win approach to negotiations.
Fostering a long-term relationship with suppliers often yields better results than aggressive tactics.
Data-Driven Decisions: Use data analytics to understand market trends, supplier performance, and cost structures.
This information can be a powerful tool during negotiations.
Clear Communication: Articulate your requirements, expectations, and timelines clearly.
Misunderstandings can lead to delays and quality issues, which can derail BPR initiatives.
Market Conditions and Their Impact on BPR
Understanding market conditions is vital for the successful implementation of BPR in supply chain management.
Here are some key considerations:
Global Supply Chain Dynamics
Japanese manufacturers often source components and materials globally.
This globalization has its pros and cons.
While it opens up opportunities for cost savings and access to diverse resources, it also introduces complexities related to logistics, tariffs, and geopolitical risks.
BPR must take these factors into account to ensure supply chain resilience.
Technological Advancements
Technological advancements in areas such as artificial intelligence, blockchain, and IoT are transforming supply chain management.
BPR initiatives should leverage these technologies to enhance transparency, traceability, and efficiency.
Consumer Expectations
Consumers today expect faster deliveries, greater customization, and higher quality.
BPR in supply chain management must be geared toward meeting these expectations without compromising on cost or efficiency.
Best Practices for Implementing BPR
Effective implementation of BPR in supply chain management requires careful planning and execution.
Here are some best practices:
Executive Sponsorship
Securing executive sponsorship is critical for the success of BPR initiatives.
Leadership support ensures that the necessary resources are allocated, and it helps in driving the cultural shift required for BPR.
Cross-Functional Teams
Form cross-functional teams that include members from procurement, production, logistics, and IT.
This ensures a holistic approach to re-engineering processes and fosters collaboration.
Continuous Monitoring and Improvement
BPR is not a one-time project; it requires continuous monitoring and improvement.
Set up metrics to track performance and make data-driven adjustments as needed.
Change Management
Effective change management strategies are essential to overcome resistance and ensure smooth implementation.
Communicate the benefits of BPR clearly to all stakeholders, and provide necessary training and support.
Conclusion
The success stories of supply chain BPR in Japanese manufacturing highlight its transformative potential.
From Toyota’s JIT system to Panasonic’s Lean Manufacturing initiatives, BPR has enabled Japanese companies to achieve significant improvements in efficiency, cost-effectiveness, and adaptability.
However, the journey is not without challenges.
Implementing BPR requires a strategic approach, deep understanding of market conditions, effective supplier negotiation techniques, and a commitment to continuous improvement.
By following best practices and leveraging the experiences of successful companies, other manufacturers can harness the power of BPR to transform their supply chains and achieve unparalleled success.
In conclusion, BPR in supply chain management is not just a tool but a strategic asset that can redefine manufacturing excellence.
Japanese manufacturers have demonstrated this through their innovative approaches and unwavering commitment to improvement.
As global market dynamics continue to evolve, the lessons learned from these success stories will remain invaluable for companies looking to make their mark in the world of manufacturing.
資料ダウンロード
QCD調達購買管理クラウド「newji」は、調達購買部門で必要なQCD管理全てを備えた、現場特化型兼クラウド型の今世紀最高の購買管理システムとなります。
ユーザー登録
調達購買業務の効率化だけでなく、システムを導入することで、コスト削減や製品・資材のステータス可視化のほか、属人化していた購買情報の共有化による内部不正防止や統制にも役立ちます。
NEWJI DX
製造業に特化したデジタルトランスフォーメーション(DX)の実現を目指す請負開発型のコンサルティングサービスです。AI、iPaaS、および先端の技術を駆使して、製造プロセスの効率化、業務効率化、チームワーク強化、コスト削減、品質向上を実現します。このサービスは、製造業の課題を深く理解し、それに対する最適なデジタルソリューションを提供することで、企業が持続的な成長とイノベーションを達成できるようサポートします。
オンライン講座
製造業、主に購買・調達部門にお勤めの方々に向けた情報を配信しております。
新任の方やベテランの方、管理職を対象とした幅広いコンテンツをご用意しております。
お問い合わせ
コストダウンが利益に直結する術だと理解していても、なかなか前に進めることができない状況。そんな時は、newjiのコストダウン自動化機能で大きく利益貢献しよう!
(Β版非公開)