- お役立ち記事
- Transforming Japanese Manufacturing: The Impact of 3D CAD on Innovation and Efficiency
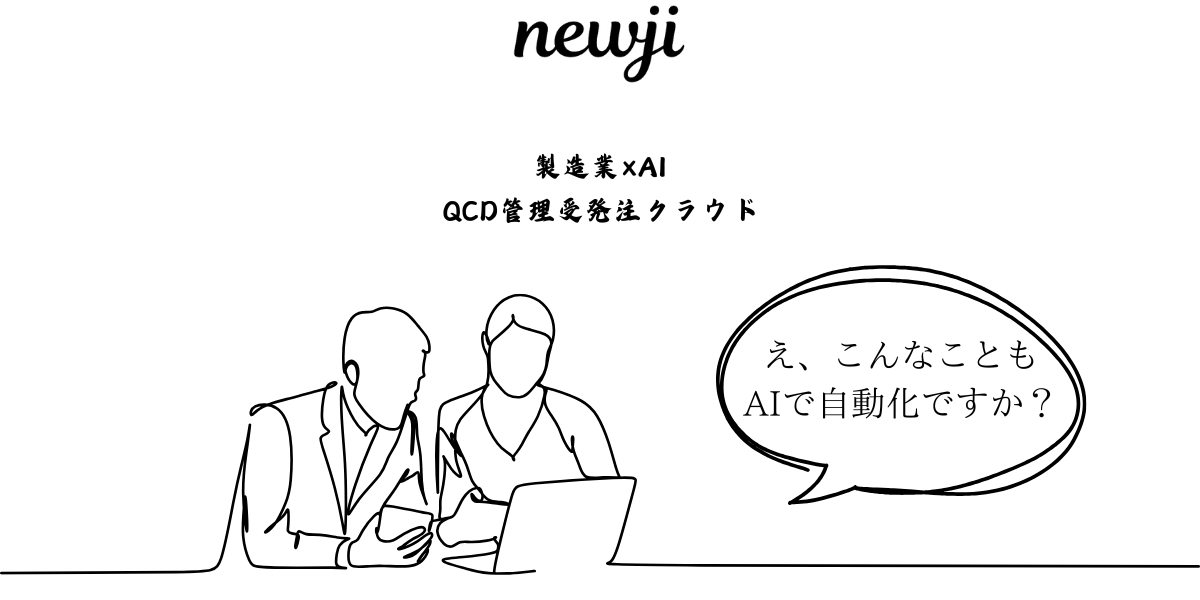
Transforming Japanese Manufacturing: The Impact of 3D CAD on Innovation and Efficiency
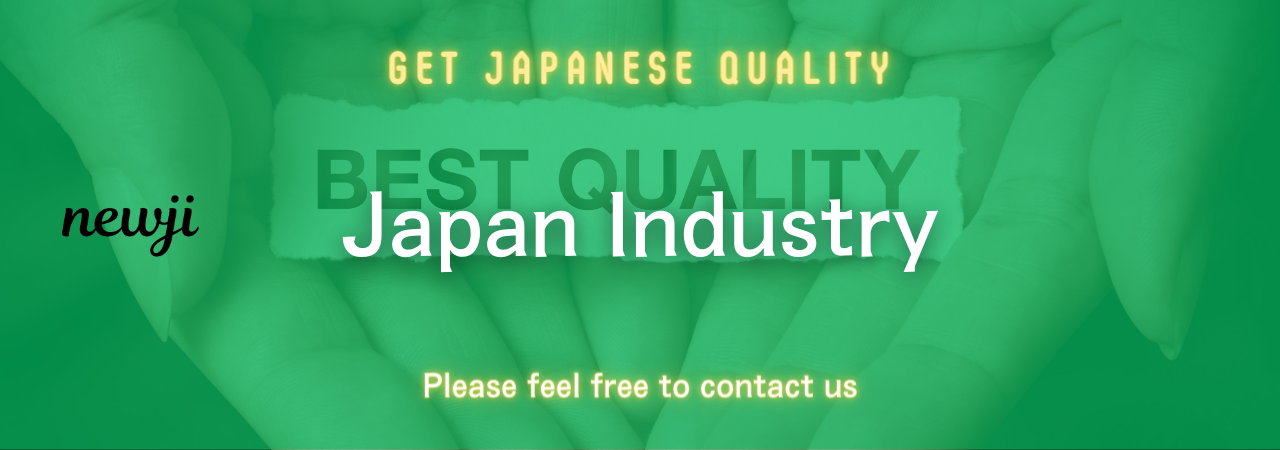
目次
Introduction to 3D CAD in Japanese Manufacturing
The integration of 3D Computer-Aided Design (CAD) has revolutionized Japanese manufacturing, enhancing both innovation and efficiency. As a cornerstone of modern design and production processes, 3D CAD technology enables manufacturers to visualize, design, and modify products with unprecedented precision and speed. This transformation is particularly significant in Japan, where manufacturing excellence and technological advancement are paramount.
Enhancing Innovation Through 3D CAD
Accelerated Product Development
3D CAD allows Japanese manufacturers to accelerate the product development cycle. By enabling rapid prototyping, companies can iterate designs quickly, reducing the time from concept to market. This agility fosters innovation, allowing businesses to respond swiftly to market demands and emerging trends.
Improved Design Accuracy
The precision of 3D CAD minimizes errors in the design phase, ensuring that products meet exact specifications. This accuracy is crucial in industries where tight tolerances are essential, such as automotive and electronics. Enhanced design accuracy leads to higher quality products and reduces the need for costly revisions.
Facilitating Collaboration and Creativity
3D CAD platforms often include collaborative tools that enable teams to work together seamlessly, regardless of their physical location. This collaboration fosters creativity, as diverse perspectives contribute to more innovative solutions. In Japanese manufacturing, where teamwork and collective problem-solving are valued, 3D CAD enhances these cultural strengths.
Boosting Efficiency in Manufacturing Processes
Streamlined Production Planning
3D CAD integrates seamlessly with other manufacturing systems, such as Computer-Aided Manufacturing (CAM) and Enterprise Resource Planning (ERP). This integration streamlines production planning, ensuring that designs are efficiently translated into manufacturing processes. The result is optimized resource utilization and reduced lead times.
Enhanced Quality Control
With 3D CAD, Japanese manufacturers can implement more rigorous quality control measures. Detailed digital models allow for thorough inspection and testing before physical prototypes are produced. This proactive approach minimizes defects and ensures that final products meet stringent quality standards.
Cost Reduction and Resource Optimization
By reducing the need for physical prototypes and minimizing design errors, 3D CAD contributes to significant cost savings. Additionally, optimized designs result in more efficient use of materials and resources, further lowering production costs. These efficiencies are critical in maintaining Japan’s competitive edge in the global market.
Impact on Procurement and Purchasing
Supplier Selection and Evaluation
3D CAD facilitates better communication and clearer specifications between manufacturers and suppliers. Detailed digital models allow procurement teams to evaluate potential suppliers more effectively, ensuring that they meet the necessary technical requirements and quality standards. This leads to more informed decision-making and stronger supplier relationships.
Negotiation Leverage
With precise and detailed designs, procurement professionals can negotiate more effectively with suppliers. Clear specifications reduce the ambiguity in agreements, minimizing the risk of misunderstandings and disputes. Additionally, the ability to visualize and modify designs provides leverage in negotiating terms and pricing.
Inventory Management and Just-In-Time (JIT) Procurement
3D CAD supports Just-In-Time procurement strategies by providing accurate and timely information on material requirements. This precision helps in maintaining optimal inventory levels, reducing holding costs, and ensuring that materials arrive exactly when needed. Efficient inventory management is a hallmark of Japanese manufacturing efficiency.
Advantages of 3D CAD in Japanese Manufacturing
Enhanced Competitive Advantage
The adoption of 3D CAD gives Japanese manufacturers a significant competitive advantage. Superior design capabilities and efficient production processes enable companies to produce high-quality products faster than competitors. This advantage is crucial in markets where speed and quality are key differentiators.
Customization and Flexibility
3D CAD allows for greater customization of products to meet specific customer needs. Japanese manufacturers can quickly adapt designs to accommodate unique requirements, enhancing customer satisfaction and loyalty. This flexibility supports a diverse range of industries, from automotive to consumer electronics.
Sustainability and Environmental Benefits
Efficient design processes reduce material waste and energy consumption, contributing to more sustainable manufacturing practices. 3D CAD enables the development of lightweight and energy-efficient products, aligning with global sustainability goals and improving the environmental footprint of manufacturing operations.
Challenges and Disadvantages
High Initial Investment
Implementing 3D CAD systems requires significant upfront investment in software, hardware, and training. For some companies, especially smaller manufacturers, the initial costs can be prohibitive. However, the long-term benefits often outweigh these initial expenses.
Learning Curve and Skill Requirements
Effective use of 3D CAD demands specialized skills and training. Manufacturers must invest in developing their workforce’s expertise to fully leverage the technology. The learning curve can initially slow down productivity, but with proper training programs, employees can quickly become proficient.
Integration with Existing Systems
Integrating 3D CAD with legacy systems and existing workflows can be complex. Compatibility issues and the need for system upgrades may arise, posing challenges for smooth implementation. Careful planning and phased integration strategies can mitigate these challenges.
Supplier Negotiation Techniques with 3D CAD
Transparent Communication
Using 3D CAD data ensures that all parties have a clear and accurate understanding of product specifications. This transparency fosters trust and facilitates smoother negotiations, as suppliers can provide more accurate quotes and timelines based on detailed designs.
Value Engineering Collaboration
Japanese manufacturers can engage suppliers in value engineering discussions, leveraging 3D CAD to explore cost-saving opportunities without compromising quality. Collaborative efforts to refine designs can result in mutually beneficial agreements that enhance overall value.
Performance-Based Contracts
With precise design data from 3D CAD, manufacturers can negotiate performance-based contracts that align supplier incentives with desired outcomes. This approach encourages suppliers to meet or exceed quality and efficiency standards, driving continuous improvement.
Market Conditions Influencing 3D CAD Adoption
Global Competition
The intense global competition in manufacturing necessitates the adoption of advanced technologies like 3D CAD to maintain competitiveness. Japanese manufacturers face pressure to innovate and deliver high-quality products swiftly, making 3D CAD essential for staying ahead.
Technological Advancements
Rapid advancements in CAD software and hardware enhance the capabilities and affordability of 3D CAD systems. Continuous innovation in technology makes it easier for manufacturers to adopt and integrate 3D CAD into their operations, fostering widespread acceptance.
Customer Demands for Customization
Modern customers increasingly demand customized products tailored to their specific needs. 3D CAD empowers manufacturers to meet these demands efficiently, providing the flexibility needed to design and produce personalized solutions without compromising on quality or speed.
Best Practices for Implementing 3D CAD in Japanese Manufacturing
Comprehensive Training Programs
Investing in comprehensive training programs ensures that employees are proficient in using 3D CAD tools. This investment not only enhances individual skills but also promotes a culture of continuous learning and technological proficiency within the organization.
Phased Implementation Strategy
Adopting a phased implementation strategy allows manufacturers to integrate 3D CAD systems gradually, minimizing disruption to existing workflows. Starting with pilot projects can help identify potential challenges and refine processes before full-scale adoption.
Collaboration with Technology Partners
Partnering with technology providers and consultants can facilitate the successful implementation of 3D CAD systems. These partners offer expertise and support, ensuring that manufacturers can effectively leverage the technology to achieve their strategic goals.
Continuous Process Improvement
Embracing a mindset of continuous process improvement ensures that the benefits of 3D CAD are maximized over time. Regularly reviewing and optimizing design and production processes helps maintain efficiency and drives ongoing innovation.
Future Trends in 3D CAD and Japanese Manufacturing
Integration with Artificial Intelligence and Machine Learning
The future of 3D CAD lies in its integration with artificial intelligence (AI) and machine learning (ML). These technologies can automate complex design tasks, predict potential issues, and optimize designs for performance and cost, further enhancing innovation and efficiency.
Augmented Reality and Virtual Reality Applications
Augmented reality (AR) and virtual reality (VR) applications are set to complement 3D CAD by providing immersive design experiences. These technologies enable more intuitive visualization and interaction with designs, improving collaboration and decision-making processes.
Sustainable Design Practices
As sustainability becomes increasingly important, 3D CAD will play a crucial role in developing environmentally friendly designs. Advanced simulation and analysis tools will help manufacturers create products that minimize environmental impact while maintaining high performance and quality.
Conclusion
The adoption of 3D CAD technology has profoundly transformed Japanese manufacturing, driving innovation and enhancing efficiency across various facets of the production process. From accelerated product development and improved design accuracy to streamlined procurement and strengthened supplier relationships, the benefits of 3D CAD are multifaceted.
While challenges such as initial investment and the need for specialized skills exist, the long-term advantages of adopting 3D CAD far outweigh these obstacles. By implementing best practices and staying attuned to future technological trends, Japanese manufacturers can continue to leverage 3D CAD to maintain their competitive edge in the global market.
As the manufacturing landscape evolves, the integration of 3D CAD with emerging technologies like AI, ML, AR, and VR will further unlock new opportunities for innovation and efficiency. Embracing these advancements will ensure that Japanese manufacturing remains at the forefront of technological excellence and industry leadership.
資料ダウンロード
QCD調達購買管理クラウド「newji」は、調達購買部門で必要なQCD管理全てを備えた、現場特化型兼クラウド型の今世紀最高の購買管理システムとなります。
ユーザー登録
調達購買業務の効率化だけでなく、システムを導入することで、コスト削減や製品・資材のステータス可視化のほか、属人化していた購買情報の共有化による内部不正防止や統制にも役立ちます。
NEWJI DX
製造業に特化したデジタルトランスフォーメーション(DX)の実現を目指す請負開発型のコンサルティングサービスです。AI、iPaaS、および先端の技術を駆使して、製造プロセスの効率化、業務効率化、チームワーク強化、コスト削減、品質向上を実現します。このサービスは、製造業の課題を深く理解し、それに対する最適なデジタルソリューションを提供することで、企業が持続的な成長とイノベーションを達成できるようサポートします。
オンライン講座
製造業、主に購買・調達部門にお勤めの方々に向けた情報を配信しております。
新任の方やベテランの方、管理職を対象とした幅広いコンテンツをご用意しております。
お問い合わせ
コストダウンが利益に直結する術だと理解していても、なかなか前に進めることができない状況。そんな時は、newjiのコストダウン自動化機能で大きく利益貢献しよう!
(Β版非公開)