- お役立ち記事
- Transforming Japanese Manufacturing: The Power of Flexible Manufacturing Systems
Transforming Japanese Manufacturing: The Power of Flexible Manufacturing Systems
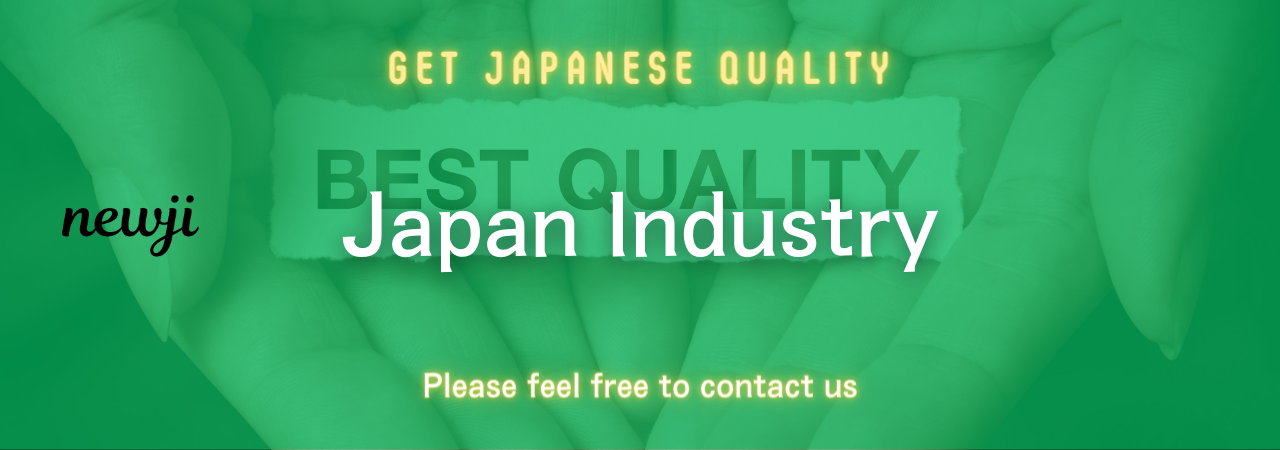
目次
Introduction to Flexible Manufacturing Systems
Flexible Manufacturing Systems (FMS) have become a cornerstone in the landscape of modern manufacturing, offering a robust solution to the complexities and unpredictabilities of contemporary production demands.
Particularly in Japanese manufacturing, FMS has garnered significant traction due to its capacity to streamline operations, reduce lead times, and accommodate market fluctuations with agility.
In an era marked by rapid technological advancement and increasingly competitive markets, the move towards FMS signifies a strategic and forward-thinking approach that aims to enhance efficiency, responsiveness, and overall competitiveness.
Understanding Flexible Manufacturing Systems
Definition and Core Components
Flexible Manufacturing Systems are integrated systems composed of automated machines connected by a central computer system.
Key components of FMS include flexible machine cells, robotics, automated guided vehicles (AGVs), computer-aided design (CAD) and computer-aided manufacturing (CAM) software, and sophisticated control and monitoring systems.
The core objective of these systems is to produce a varied product mix with minimal manual intervention and rapid adaptability to new production requirements.
Advantages of Flexible Manufacturing Systems
The primary advantages of Flexible Manufacturing Systems lie in their ability to accommodate a diverse range of products and production quantities without extensive retooling or manual intervention.
FMS enables manufacturers to respond swiftly to market changes and customer demands, fostering a more customer-centric production model.
Other considerable benefits include reduced production costs, smaller lead times, improved product quality, and enhanced operational efficiency.
Challenges and Disadvantages
Despite the significant advantages, implementing and managing FMS is not without challenges.
The initial investment cost can be substantial, including the procurement of sophisticated machinery and technology, as well as the necessary training and reorganization efforts.
Furthermore, the complexity of FMS requires robust and continuous maintenance, and any system failures can lead to significant downtime and associated costs.
Additionally, the reliance on advanced technology and systems integration can pose cybersecurity risks, requiring continuous monitoring and updating of safeguards.
The Context of Japanese Manufacturing
Historical Perspective
Japanese manufacturing has long been heralded for its commitment to quality, efficiency, and continuous improvement.
Methods such as Just-In-Time (JIT) production, Total Quality Management (TQM), and Lean Manufacturing have set a global benchmark for operational excellence.
The integration of Flexible Manufacturing Systems within this well-established framework exemplifies the country’s proactive engagement with technological innovation to further augment its manufacturing prowess.
Current Market Conditions
In the current global market, manufacturing environments are increasingly characterized by volatility and complexity.
Japanese manufacturing companies face intensifying competition, evolving regulatory landscapes, and shifting consumer preferences.
These market conditions necessitate a flexible and adaptive approach to manufacturing, where FMS fits seamlessly into the broader strategy.
The ability to pivot quickly and produce high-quality, customizable products is now more crucial than ever for maintaining competitive advantage.
Implementing Flexible Manufacturing Systems
Strategic Planning and Assessment
A successful implementation of FMS begins with thorough strategic planning and assessment.
Companies must evaluate their existing production processes, identify specific pain points, and establish clear objectives for the introduction of an FMS.
This involves an in-depth analysis of market demands, product variability, production volumes, and technology infrastructure.
Conducting cost-benefit analyses and feasibility studies will provide valuable insights for informed decision-making.
Selection of Appropriate Technology and Partners
Selecting the right technology and partners is a critical step in FMS implementation.
Manufacturers need to choose equipment and systems that align with their production needs and goals.
Partnering with reputable suppliers and technology providers, especially those with a proven track record in FMS, can significantly enhance the success rates.
Close collaboration with these partners will ensure that the system is tailored to specific production requirements and provides the desired flexibility and efficiency.
Training and Skill Development
The introduction of FMS necessitates a paradigm shift in both operational practices and workforce skills.
Comprehensive training programs are essential to equip employees with the necessary knowledge and expertise to operate and maintain the new systems.
Training should encompass both technical aspects and operational procedures, fostering a culture of continuous learning and adaptation.
Additionally, developing cross-functional teams that can manage, troubleshoot, and optimize FMS will further bolster operational resilience and innovation.
Integration Process
Integration of FMS into existing production environments should be carried out meticulously to minimize disruptions.
This involves a phased approach, starting with pilot runs to iron out any potential issues, followed by gradual scaling up as confidence in the systems grows.
Continuous monitoring and iterative improvements based on feedback and performance metrics will ensure that the system not only meets but exceeds production expectations.
Continuous Improvement and Optimization
The journey of FMS implementation does not end with integration.
Continuous improvement and optimization are essential to fully leverage the benefits of flexible systems.
This includes regular performance assessments, adopting new technologies, and continually refining processes to enhance efficiency, reduce waste, and improve product quality.
Leveraging data analytics and predictive maintenance tools can further streamline operations and preemptively address potential bottlenecks.
Supplier Negotiation Techniques
Understanding Supplier Capabilities
Effective supplier negotiation is crucial in the successful adoption of FMS.
Understanding supplier capabilities, production capacities, and technological offerings forms the foundation of meaningful negotiations.
Manufacturers should engage in thorough due diligence, leveraging market research and historical performance data to evaluate potential partners.
Building a long-term relationship based on mutual trust and transparency will yield more favorable terms and foster collaborative innovation.
Setting Clear Expectations and Objectives
Setting clear expectations and objectives during negotiations is imperative.
Manufacturers should articulate their specific requirements, desired outcomes, and performance metrics.
This clarity will pave the way for more precise and mutually beneficial agreements, ensuring that suppliers are aligned with the company’s strategic vision and operational goals.
Leveraging Market Conditions
Staying informed about current market conditions provides valuable leverage during negotiations.
Manufacturers can harness insights on supply and demand dynamics, price trends, and technological advancements to negotiate more favorable terms.
Understanding the competitive landscape and potential alternative suppliers also strengthens the negotiating position, creating opportunities for better pricing, terms, and service levels.
Building Strategic Partnerships
Lastly, building strategic partnerships with suppliers is a key aspect of successful FMS implementation.
Engaging in long-term collaborations rather than transactional relationships fosters innovation, continuous improvement, and mutual benefits.
Joint development initiatives, co-investment in new technologies, and collaborative problem-solving can lead to enhanced performance and sustained competitive advantage.
Best Practices for FMS Implementation
Lean Manufacturing Integration
Integrating flexible manufacturing systems within a Lean Manufacturing framework can amplify their benefits.
FMS complements Lean principles by promoting waste reduction, improving flow, and enhancing responsiveness.
Manufacturers can leverage FMS to implement just-in-time production, streamline operations, and maintain high quality standards while reducing lead times and inventory levels.
Focus on Agility and Responsiveness
The core strength of FMS lies in its agility and responsiveness.
Manufacturers should prioritize flexibility and rapid adaptation to changing market demands.
Implementing dynamic scheduling, real-time monitoring, and adaptive control systems will ensure that production remains aligned with fluctuating customer requirements and market conditions.
Customization and Personalization
In an age where customization and personalization are highly valued, FMS empowers manufacturers to produce tailored and unique products efficiently.
Leveraging FMS capabilities allows for batch-of-one production, where each unit can be customized without sacrificing efficiency.
This customer-centric approach can significantly enhance satisfaction, loyalty, and brand differentiation.
Investing in Advanced Technologies
Continual investment in advanced technologies is essential to fully harness the potential of FMS.
Emerging technologies such as the Internet of Things (IoT), artificial intelligence (AI), and robotics further enhance the capabilities of flexible manufacturing systems.
These technologies enable predictive maintenance, data-driven decision-making, and autonomous operations, driving operational excellence and maximizing return on investment.
Conclusion
The adoption and integration of Flexible Manufacturing Systems represent a transformative leap for Japanese manufacturing.
By embracing the power of FMS, manufacturers can achieve unparalleled flexibility, efficiency, and responsiveness, positioning themselves at the forefront of the global market.
While challenges and complexities exist, a strategic and well-executed approach encompassing thorough planning, robust partnerships, continuous improvement, and best practices can unlock the full potential of flexible manufacturing systems.
As market dynamics continue to evolve, the proactive adoption of these advanced systems will be crucial in sustaining competitiveness and thriving in the fast-paced, ever-changing world of manufacturing.
資料ダウンロード
QCD調達購買管理クラウド「newji」は、調達購買部門で必要なQCD管理全てを備えた、現場特化型兼クラウド型の今世紀最高の購買管理システムとなります。
ユーザー登録
調達購買業務の効率化だけでなく、システムを導入することで、コスト削減や製品・資材のステータス可視化のほか、属人化していた購買情報の共有化による内部不正防止や統制にも役立ちます。
NEWJI DX
製造業に特化したデジタルトランスフォーメーション(DX)の実現を目指す請負開発型のコンサルティングサービスです。AI、iPaaS、および先端の技術を駆使して、製造プロセスの効率化、業務効率化、チームワーク強化、コスト削減、品質向上を実現します。このサービスは、製造業の課題を深く理解し、それに対する最適なデジタルソリューションを提供することで、企業が持続的な成長とイノベーションを達成できるようサポートします。
オンライン講座
製造業、主に購買・調達部門にお勤めの方々に向けた情報を配信しております。
新任の方やベテランの方、管理職を対象とした幅広いコンテンツをご用意しております。
お問い合わせ
コストダウンが利益に直結する術だと理解していても、なかなか前に進めることができない状況。そんな時は、newjiのコストダウン自動化機能で大きく利益貢献しよう!
(Β版非公開)