- お役立ち記事
- Transforming Japanese Manufacturing: Top Productivity Improvement Tools for Unmatched Efficiency
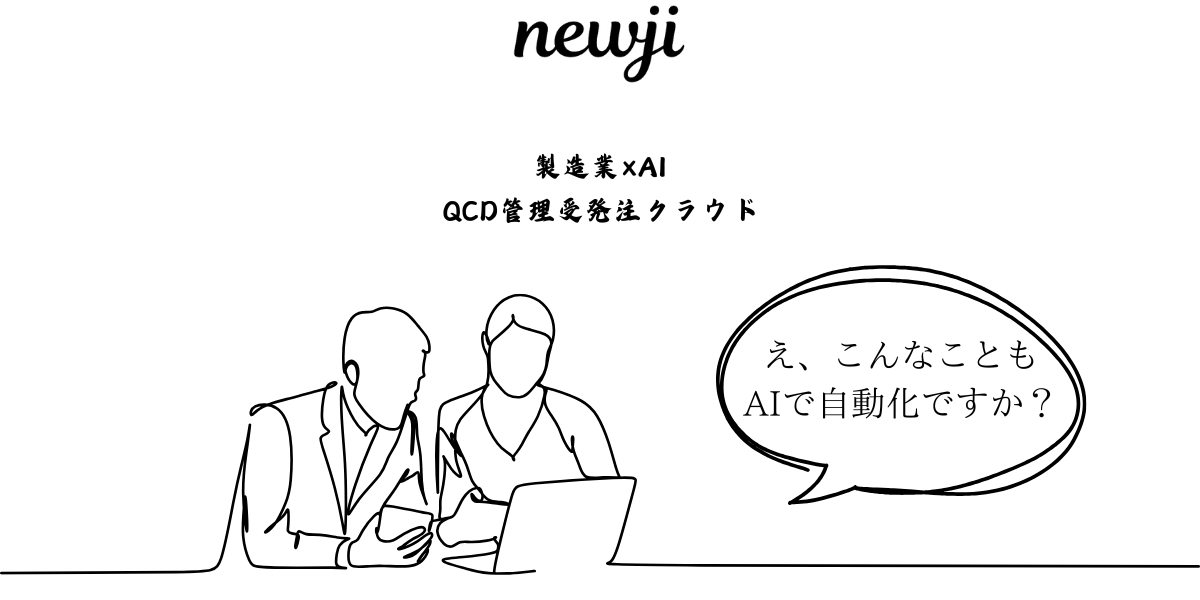
Transforming Japanese Manufacturing: Top Productivity Improvement Tools for Unmatched Efficiency
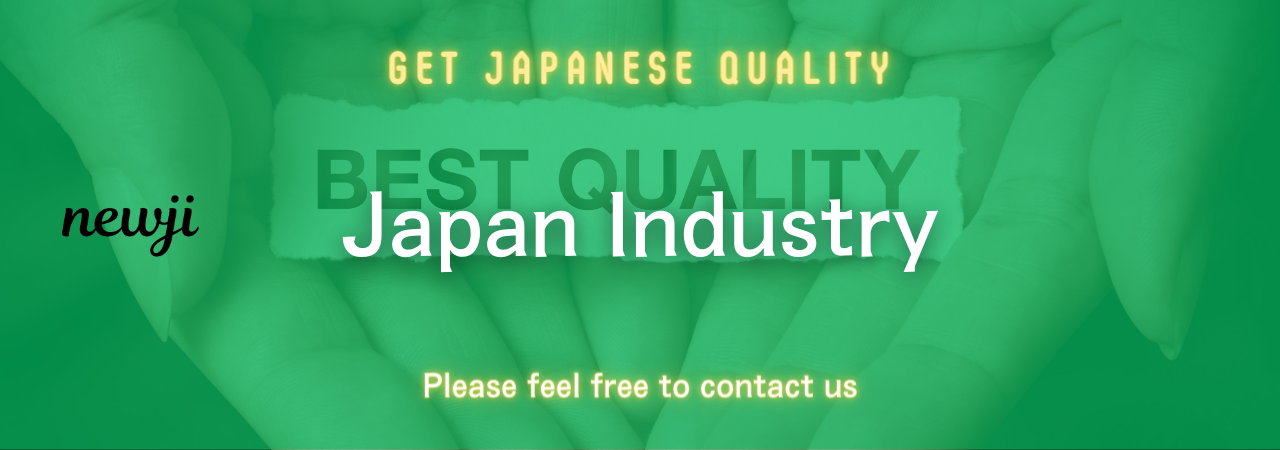
目次
Overview of Japanese Manufacturing Excellence
Japanese manufacturing is globally renowned for its commitment to quality, efficiency, and continuous improvement. This excellence stems from a deep-rooted cultural emphasis on precision, innovation, and teamwork. Japanese manufacturers have consistently set benchmarks in various industries, from automotive and electronics to machinery and consumer goods. The adoption of advanced productivity improvement tools has been pivotal in transforming their manufacturing processes, ensuring unmatched efficiency and competitiveness in the global market.
Top Productivity Improvement Tools in Japanese Manufacturing
Lean Manufacturing
Lean manufacturing focuses on minimizing waste without sacrificing productivity. By streamlining processes, eliminating non-value-added activities, and optimizing resource utilization, Japanese manufacturers can produce high-quality products efficiently. Techniques such as value stream mapping, just-in-time production, and continuous flow are integral components of lean manufacturing, fostering a culture of efficiency and responsiveness to market demands.
Just-In-Time (JIT) Production
JIT production ensures that materials and components arrive exactly when needed in the production process, reducing inventory costs and minimizing waste. This system requires precise coordination with suppliers and robust demand forecasting. Japanese manufacturers excel in implementing JIT, leveraging strong supplier relationships and advanced logistical systems to maintain seamless production flows and adapt swiftly to changes in demand.
Total Quality Management (TQM)
TQM is a comprehensive approach that emphasizes quality in every aspect of the manufacturing process. It involves the entire organization, from top management to frontline workers, in continuous quality improvement initiatives. Japanese companies utilize TQM to enhance product reliability, reduce defects, and increase customer satisfaction. Techniques such as statistical process control, root cause analysis, and quality circles are commonly employed to achieve these goals.
Kaizen
Kaizen, meaning “continuous improvement,” is a fundamental philosophy in Japanese manufacturing. It encourages small, incremental changes that collectively lead to significant enhancements in productivity and quality. Employees at all levels are empowered to identify areas for improvement and implement solutions. This collaborative approach fosters a proactive mindset, driving sustained operational excellence and innovation.
5S Methodology
The 5S methodology focuses on organizing and standardizing the workplace to enhance efficiency and safety. The five S’s stand for Sort, Set in order, Shine, Standardize, and Sustain. By systematically implementing 5S, Japanese manufacturers create orderly, clean, and efficient work environments that facilitate smooth operations, reduce downtime, and improve overall productivity.
Kanban System
The Kanban system is a visual scheduling tool that manages workflow and inventory levels. It uses cards or signals to indicate when new materials are needed, ensuring a balanced production pace and preventing overproduction. In Japanese manufacturing, Kanban helps maintain optimal inventory levels, reduces lead times, and enhances flexibility in responding to market variations.
Autonomous Maintenance
Autonomous maintenance empowers operators to take responsibility for the maintenance of their equipment. By performing routine inspections, cleaning, and minor repairs, operators can prevent equipment failures and extend machinery lifespan. This proactive maintenance approach enhances equipment reliability, reduces downtime, and fosters a sense of ownership and accountability among workers.
Six Sigma
Six Sigma is a data-driven methodology aimed at reducing defects and variability in manufacturing processes. By applying statistical analysis and structured problem-solving techniques, Japanese manufacturers can achieve near-perfect quality levels. Six Sigma projects typically follow the DMAIC framework—Define, Measure, Analyze, Improve, and Control—to systematically enhance process performance and ensure consistent quality outcomes.
Advantages and Disadvantages of Japanese Productivity Tools
Advantages
Japanese productivity improvement tools offer numerous benefits that contribute to manufacturing excellence. These tools enhance operational efficiency by reducing waste, optimizing resource utilization, and streamlining workflows. They also promote high-quality standards, ensuring products meet or exceed customer expectations. Additionally, these methodologies foster a culture of continuous improvement and employee engagement, driving innovation and adaptability in a dynamic market environment. The strong emphasis on collaboration and communication strengthens supplier relationships, facilitating seamless integration across the supply chain.
Disadvantages
While Japanese productivity tools offer significant advantages, they also present certain challenges. Implementing these methodologies requires substantial cultural and organizational changes, which can be difficult for companies with ingrained practices. The initial investment in training and process redesign can be resource-intensive. Additionally, the rigorous adherence to these systems may limit flexibility, making it challenging to swiftly adapt to unforeseen disruptions or market shifts. In some cases, the emphasis on incremental improvements may slow down the adoption of radical innovations necessary for long-term growth.
Supplier Negotiation Techniques in Japanese Manufacturing
Effective supplier negotiation is crucial for maintaining the high standards of Japanese manufacturing. Japanese companies employ a collaborative negotiation approach, emphasizing long-term relationships over short-term gains. Key techniques include:
Building Trust and Mutual Respect
Japanese manufacturers prioritize building trust and mutual respect with their suppliers. This foundation fosters open communication, transparency, and a willingness to collaborate on problem-solving and innovation. Trust-based relationships lead to more favorable negotiation outcomes and stronger partnerships.
Win-Win Negotiation
Rather than adopting a competitive stance, Japanese negotiators strive for win-win solutions that benefit both parties. By understanding the supplier’s needs and constraints, they work towards agreements that enhance value for both sides, ensuring sustainable and productive partnerships.
Emphasis on Long-Term Relationships
Japanese companies focus on establishing long-term relationships with suppliers, which encourages suppliers to invest in quality and reliability. This long-term perspective leads to better terms, consistent quality, and enhanced collaboration in developing new products and improving processes.
Detail-Oriented Communication
During negotiations, Japanese manufacturers are meticulous and detail-oriented. They clearly outline their requirements, expectations, and specifications to avoid misunderstandings. This precision ensures that both parties have a comprehensive understanding of the agreement, reducing the likelihood of future disputes.
Patience and Persistence
Japanese negotiators exhibit patience and persistence, understanding that building strong partnerships takes time. They are willing to engage in prolonged discussions to reach mutually beneficial agreements, recognizing the value of establishing solid foundations for future collaborations.
Market Conditions Affecting Procurement from Japan
The procurement landscape from Japan is influenced by various market conditions that manufacturers must navigate to optimize their purchasing strategies.
Economic Stability
Japan’s economic stability plays a significant role in procurement decisions. A stable economy ensures reliable supply chains, consistent pricing, and predictable delivery schedules. Manufacturers can plan and forecast with greater accuracy, reducing risks associated with economic volatility.
Technological Advancements
Japan’s leadership in technology and innovation provides manufacturers with access to cutting-edge products and advanced manufacturing techniques. Staying abreast of technological advancements is essential for maintaining competitive advantage and meeting evolving market demands.
Global Trade Policies
International trade policies, tariffs, and trade agreements impact the cost and feasibility of procuring from Japan. Manufacturers must stay informed about changes in trade regulations to mitigate potential risks and capitalize on opportunities for favorable trade terms.
Supply Chain Resilience
Recent global disruptions have highlighted the importance of supply chain resilience. Japanese manufacturers are known for their robust and flexible supply chains, which can adapt to disruptions and maintain continuity in production. Evaluating the resilience of Japanese suppliers is crucial for ensuring uninterrupted procurement.
Currency Fluctuations
Currency exchange rates between the Japanese yen and other currencies affect the cost of procurement. Manufacturers must monitor currency fluctuations and implement strategies such as hedging to manage financial risks and maintain cost stability.
Best Practices for Procurement and Purchasing in Japanese Manufacturing
Develop Strong Supplier Relationships
Building and maintaining strong relationships with Japanese suppliers is fundamental. This involves regular communication, mutual respect, and collaboration on quality and innovation. Long-term partnerships foster trust and reliability, ensuring consistent supply and favorable terms.
Implement Rigorous Quality Standards
Adhering to strict quality standards is essential in Japanese manufacturing. Manufacturers should establish clear quality expectations, conduct regular audits, and collaborate with suppliers to ensure that products meet the required specifications. Investing in quality control processes reduces defects and enhances product reliability.
Leverage Technology and Automation
Utilizing advanced technologies and automation in procurement processes enhances efficiency and accuracy. Digital tools for inventory management, demand forecasting, and supplier relationship management streamline operations and provide valuable insights for informed decision-making.
Adopt a Continuous Improvement Mindset
Embracing the principles of continuous improvement ensures that procurement processes remain efficient and responsive to changing market conditions. Regularly reviewing and optimizing procurement strategies, seeking feedback from suppliers, and encouraging innovative solutions drive sustained excellence.
Ensure Transparent Communication
Clear and transparent communication with suppliers is crucial for successful procurement. Establishing open channels for dialogue, sharing forecasts and demand plans, and promptly addressing issues prevent misunderstandings and strengthen partnerships.
Diversify Supply Sources
While maintaining strong ties with Japanese suppliers, diversifying the supply base mitigates risks associated with dependency on a single source. Exploring alternative suppliers in different regions enhances supply chain resilience and ensures continuity in procurement.
Focus on Sustainability
Incorporating sustainability into procurement strategies aligns with global trends and corporate responsibility goals. Working with suppliers who prioritize environmentally friendly practices and sustainable sourcing contributes to long-term viability and positive brand reputation.
Conclusion
Japanese manufacturing stands as a paragon of efficiency, quality, and continuous improvement. The adoption of top productivity improvement tools such as lean manufacturing, JIT production, TQM, and Kaizen has been instrumental in achieving unmatched operational excellence. While these tools offer significant advantages in enhancing productivity and quality, they also require substantial commitment and cultural alignment to overcome potential challenges.
Effective supplier negotiation techniques, characterized by trust-building, collaborative problem-solving, and a focus on long-term relationships, further strengthen Japanese manufacturing’s competitive edge. Understanding the market conditions, including economic stability, technological advancements, and global trade policies, is essential for optimizing procurement and purchasing strategies from Japan.
Adhering to best practices in procurement—such as developing strong supplier relationships, implementing rigorous quality standards, leveraging technology, and embracing continuous improvement—ensures sustained excellence and adaptability in a dynamic global market. By integrating these strategies, manufacturers can harness the full potential of Japanese manufacturing expertise, achieving superior efficiency and maintaining a competitive advantage in their respective industries.
資料ダウンロード
QCD調達購買管理クラウド「newji」は、調達購買部門で必要なQCD管理全てを備えた、現場特化型兼クラウド型の今世紀最高の購買管理システムとなります。
ユーザー登録
調達購買業務の効率化だけでなく、システムを導入することで、コスト削減や製品・資材のステータス可視化のほか、属人化していた購買情報の共有化による内部不正防止や統制にも役立ちます。
NEWJI DX
製造業に特化したデジタルトランスフォーメーション(DX)の実現を目指す請負開発型のコンサルティングサービスです。AI、iPaaS、および先端の技術を駆使して、製造プロセスの効率化、業務効率化、チームワーク強化、コスト削減、品質向上を実現します。このサービスは、製造業の課題を深く理解し、それに対する最適なデジタルソリューションを提供することで、企業が持続的な成長とイノベーションを達成できるようサポートします。
オンライン講座
製造業、主に購買・調達部門にお勤めの方々に向けた情報を配信しております。
新任の方やベテランの方、管理職を対象とした幅広いコンテンツをご用意しております。
お問い合わせ
コストダウンが利益に直結する術だと理解していても、なかなか前に進めることができない状況。そんな時は、newjiのコストダウン自動化機能で大きく利益貢献しよう!
(Β版非公開)