- お役立ち記事
- Trouble/defect “causal analysis method” for engineers and how to use it to solve problems
月間77,185名の
製造業ご担当者様が閲覧しています*
*2025年2月28日現在のGoogle Analyticsのデータより
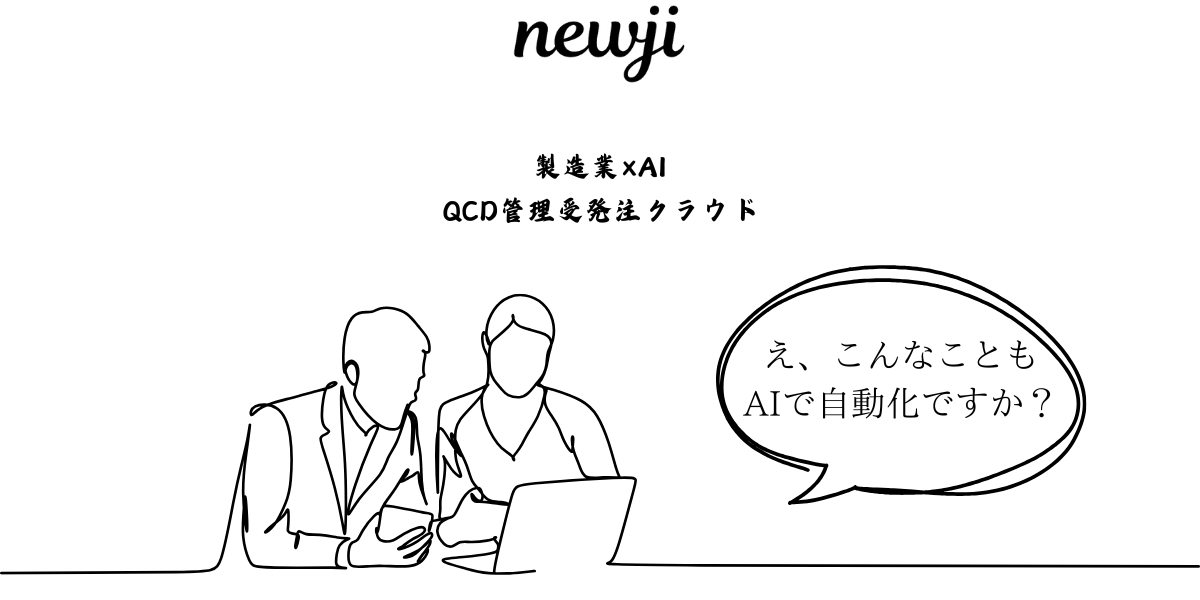
Trouble/defect “causal analysis method” for engineers and how to use it to solve problems
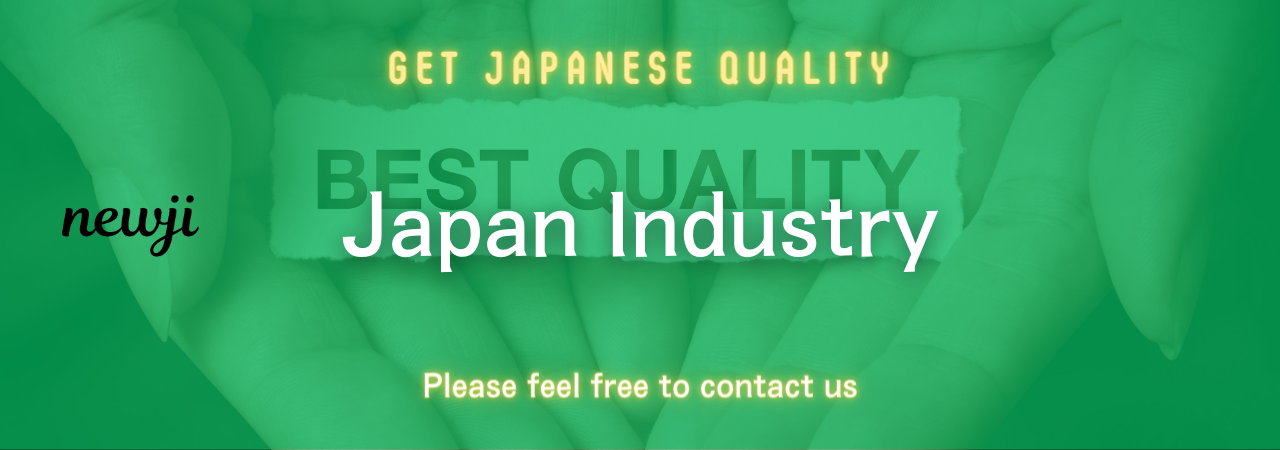
目次
Understanding Causal Analysis in Engineering
Causal analysis is a critical method used by engineers to identify the root causes of problems or defects in systems, processes, or products.
This method helps in uncovering the underlying issues that may not be immediately apparent and aids in developing effective solutions.
In engineering, understanding the cause of a problem is often more valuable than knowing its symptoms.
By digging deep through a systematic approach, engineers can implement corrective measures that prevent the recurrence of the issue.
Why is Causal Analysis Important?
In any engineering process, the ability to identify and rectify defects is crucial for efficiency, safety, and quality assurance.
Problems left unresolved can lead to significant setbacks, financial loss, or even catastrophic failures.
Causal analysis provides a structured framework to dissect complex problems and pinpoint where things went wrong.
This not only saves time and resources but also leads to more reliable outcomes and improved performance of systems and products.
Steps in the Causal Analysis Process
Step 1: Define the Problem
The first step in causal analysis is to clearly define the problem you are facing.
This involves collecting data related to the issue, including when it occurs, under what circumstances, and how frequently.
A well-defined problem sets the foundation for effective analysis and eventual solutions.
Step 2: Identify Possible Causes
Once you have clearly defined the problem, the next step is to brainstorm and list possible causes.
Consider every aspect of the system or process that might contribute to the defect.
At this stage, it’s important to be exhaustive and not dismiss any potential cause prematurely.
Tools like brainstorming sessions, fishbone diagrams, and process mapping can facilitate this exploration.
Step 3: Analyze Cause and Effect
After identifying possible causes, the next step is to analyze cause and effect relationships.
This involves evaluating how each potential cause could contribute to the problem and determining the interactions between different factors.
Dependency diagrams and logic trees can be used effectively to visualize complex interactions and help prioritize the most likely causes.
Step 4: Verify Root Cause
Verification is crucial in ensuring that the identified root cause truly leads to the defect.
Testing hypotheses through experiments or simulations can help validate theories about the problem’s origin.
This may involve replicating the defect under controlled conditions or tracing the issue in historical data to confirm its presence.
Step 5: Develop and Implement Solutions
Once the root cause is verified, engineers can move towards developing a solution that addresses the underlying issue.
Solutions should aim to not only fix the problem but also prevent its recurrence in the future.
Implementation might involve redesigning a process, upgrading components, or instituting new practices or policies.
Tools For Effective Causal Analysis
There are several tools that engineers can utilize to streamline the causal analysis process.
5 Whys Technique
The 5 Whys is a simple yet powerful tool used to drill down into the root cause of a problem by repeatedly asking “why?”.
Typically, asking “why” five times can lead you to the underlying issue, although the number may vary depending on the complexity of the problem.
Fishbone Diagram
Also known as an Ishikawa or cause-and-effect diagram, the fishbone diagram is useful for visualizing the many potential causes of a problem.
It resembles a fish skeleton with the problem at the head and possible causes branching out like fish bones.
Failure Mode and Effects Analysis (FMEA)
FMEA is a systematic method for evaluating processes to identify where and how they might fail.
This tool helps prioritize potential failures based on their impact, frequency, and detectability, allowing for targeted problem-solving.
Root Cause Analysis Software
In today’s digital age, specialized RCA software can automate much of the data collection and analysis required in causal analysis.
These tools facilitate sorting through vast amounts of information and extracting pertinent insights efficiently.
Challenges in Causal Analysis
While causal analysis is immensely valuable, it is not without challenges.
Complex Systems
In complex systems, isolating a single cause can be difficult as multiple factors often intertwine to create problems.
This complexity requires a thorough understanding of the system and a multi-faceted analytical approach.
Time Constraints
Engineers working under tight deadlines may find it challenging to allocate sufficient time for comprehensive causal analysis.
However, rushing through the process without fully understanding the problem can lead to incomplete solutions.
Data Limitations
Insufficient or poor quality data can impact the effectiveness of causal analysis.
Accurate and detailed data collection is crucial for precise diagnosis of issues.
Conclusion
Causal analysis is an indispensable tool in an engineer’s arsenal for identifying and resolving defects.
By meticulously following a structured approach, engineers can ensure efficient, effective, and lasting solutions to problems.
While challenges exist, using the right tools and techniques can significantly enhance the accuracy and efficiency of the analysis.
Ultimately, mastering causal analysis not only boosts the reliability of engineering outcomes but also contributes to continuous improvement and innovation in engineering practices.
資料ダウンロード
QCD管理受発注クラウド「newji」は、受発注部門で必要なQCD管理全てを備えた、現場特化型兼クラウド型の今世紀最高の受発注管理システムとなります。
ユーザー登録
受発注業務の効率化だけでなく、システムを導入することで、コスト削減や製品・資材のステータス可視化のほか、属人化していた受発注情報の共有化による内部不正防止や統制にも役立ちます。
NEWJI DX
製造業に特化したデジタルトランスフォーメーション(DX)の実現を目指す請負開発型のコンサルティングサービスです。AI、iPaaS、および先端の技術を駆使して、製造プロセスの効率化、業務効率化、チームワーク強化、コスト削減、品質向上を実現します。このサービスは、製造業の課題を深く理解し、それに対する最適なデジタルソリューションを提供することで、企業が持続的な成長とイノベーションを達成できるようサポートします。
製造業ニュース解説
製造業、主に購買・調達部門にお勤めの方々に向けた情報を配信しております。
新任の方やベテランの方、管理職を対象とした幅広いコンテンツをご用意しております。
お問い合わせ
コストダウンが利益に直結する術だと理解していても、なかなか前に進めることができない状況。そんな時は、newjiのコストダウン自動化機能で大きく利益貢献しよう!
(β版非公開)