- お役立ち記事
- Troubles and countermeasures during injection molding
月間76,176名の
製造業ご担当者様が閲覧しています*
*2025年3月31日現在のGoogle Analyticsのデータより
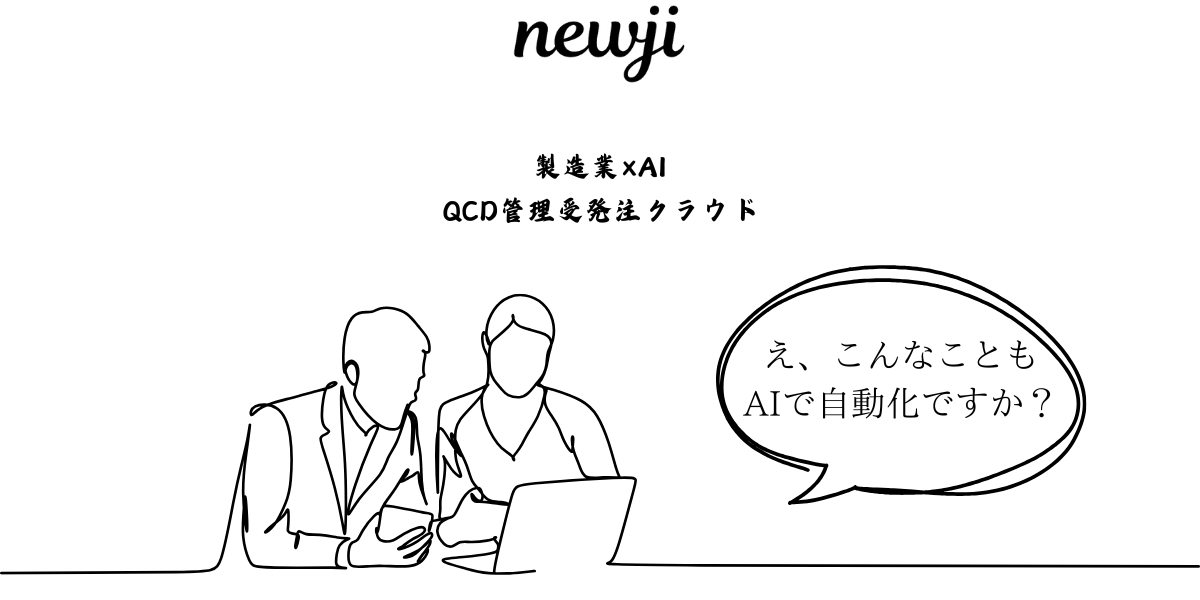
Troubles and countermeasures during injection molding
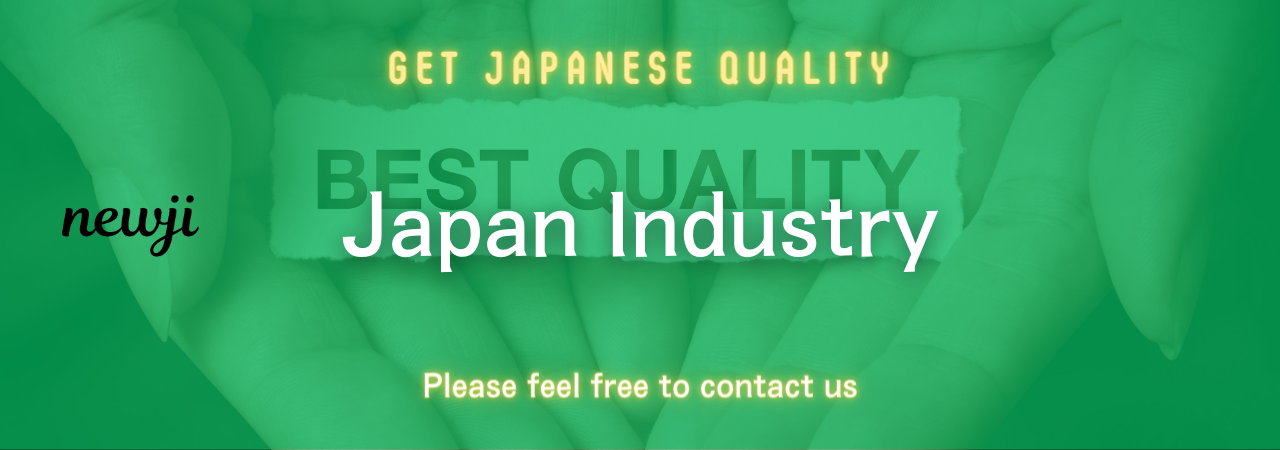
目次
Understanding Injection Molding
Injection molding is a popular manufacturing process used to produce a wide range of plastic parts, from small components to large automotive parts.
The process involves injecting molten plastic into a mold, allowing it to cool and solidify before being ejected as a finished part.
This technique is favored for its ability to produce high-quality, precise parts at scale.
Despite its numerous benefits, injection molding is not without its challenges.
Understanding these common issues and their solutions is crucial for ensuring a smooth manufacturing process.
Common Issues in Injection Molding
Several problems can arise during the injection molding process, affecting the quality and consistency of the final product.
Below, we discuss some of the most common issues encountered and their respective countermeasures.
Warping
Warping occurs when the molded part bends or twists, leading to dimensional inaccuracies.
This can be caused by uneven cooling, residual stresses, or improper mold design.
**Countermeasures:**
To address warping, ensure uniform cooling across the part by improving the mold design or adjusting the cooling time.
Consider using a plastic material with lower shrinkage properties to minimize dimensional changes.
Optimizing packing pressure and time can also help alleviate this issue.
Sink Marks
Sink marks are depressions or cavities that appear on the surface of the molded part.
They typically occur due to insufficient cooling or packing pressure, leading to imperfect filling.
**Countermeasures:**
To prevent sink marks, increase the packing pressure and extend the packing time.
Using a higher mold temperature can also help by allowing better material flow.
Ensuring a consistent wall thickness across the design can reduce the likelihood of sink marks.
Flow Lines
Flow lines are visible streaks or patterns on the surface of the molded part.
These occur when the molten plastic cools down too quickly, leading to a visible alteration in material flow.
**Countermeasures:**
To minimize flow lines, increase the injection speed to ensure the plastic fills the mold quickly and uniformly.
Raising the mold temperature can also improve material flow and reduce the appearance of flow lines.
If necessary, redesign the runner system to allow for smoother plastic flow into the mold.
Short Shots
Short shots occur when the plastic does not completely fill the mold cavity, resulting in incomplete parts.
This can be due to inadequate material flow, incorrect injection speed, or insufficient pressure.
**Countermeasures:**
To solve short shots, increase the injection pressure and speed to ensure the cavity is completely filled.
Check for blockages in the mold or runner system and clear any obstructions.
Additionally, ensure the material is at the correct temperature to maintain optimal flow.
Burn Marks
Burn marks are dark or discolored areas on the surface of the molded part.
They result from air trapped within the mold cavity, which heats up and causes discoloration during injection.
**Countermeasures:**
To prevent burn marks, improve the mold venting system to allow trapped air to escape.
Decrease the injection speed to reduce the chance of air entrapment.
Optimizing the gate location can also help maintain a steady flow of material, reducing the likelihood of burn marks.
Improving Mold Design
An effective mold design is key to avoiding many common injection molding issues.
Here are some tips for optimizing mold design:
– Ensure uniform wall thickness to reduce warping and sink marks.
– Design gates, vents, and runners to allow smooth and consistent flow.
– Employ appropriate draft angles to facilitate part ejection and reduce stress on the molded part.
Choosing the Right Material
The choice of plastic material has a significant impact on the injection molding process.
Each polymer has different properties, influencing factors such as shrinkage, cooling time, and flow capability.
Selecting the right material requires understanding the intended use of the part and its required characteristics.
Consult material data sheets and conduct tests to determine the best match for your project.
Optimizing Processing Parameters
Fine-tuning processing parameters such as temperature, pressure, and cycle time can significantly reduce issues in injection molding.
Conduct trials to identify optimal settings and monitor machine conditions regularly.
Implementing consistent monitoring and maintenance can ensure that your injection molding process remains efficient and produces high-quality parts.
Conclusion
Injection molding, while highly advantageous, presents several challenges that require careful consideration and adjustment.
Identifying potential issues and understanding their countermeasures is vital to maintaining production efficiency and quality.
By optimizing mold design, choosing appropriate materials, and fine-tuning processing parameters, manufacturers can overcome these problems and achieve successful injection-molded parts time after time.
資料ダウンロード
QCD管理受発注クラウド「newji」は、受発注部門で必要なQCD管理全てを備えた、現場特化型兼クラウド型の今世紀最高の受発注管理システムとなります。
ユーザー登録
受発注業務の効率化だけでなく、システムを導入することで、コスト削減や製品・資材のステータス可視化のほか、属人化していた受発注情報の共有化による内部不正防止や統制にも役立ちます。
NEWJI DX
製造業に特化したデジタルトランスフォーメーション(DX)の実現を目指す請負開発型のコンサルティングサービスです。AI、iPaaS、および先端の技術を駆使して、製造プロセスの効率化、業務効率化、チームワーク強化、コスト削減、品質向上を実現します。このサービスは、製造業の課題を深く理解し、それに対する最適なデジタルソリューションを提供することで、企業が持続的な成長とイノベーションを達成できるようサポートします。
製造業ニュース解説
製造業、主に購買・調達部門にお勤めの方々に向けた情報を配信しております。
新任の方やベテランの方、管理職を対象とした幅広いコンテンツをご用意しております。
お問い合わせ
コストダウンが利益に直結する術だと理解していても、なかなか前に進めることができない状況。そんな時は、newjiのコストダウン自動化機能で大きく利益貢献しよう!
(β版非公開)