- お役立ち記事
- Troubleshooting ABS Resin Processing Issues for SMEs
Troubleshooting ABS Resin Processing Issues for SMEs
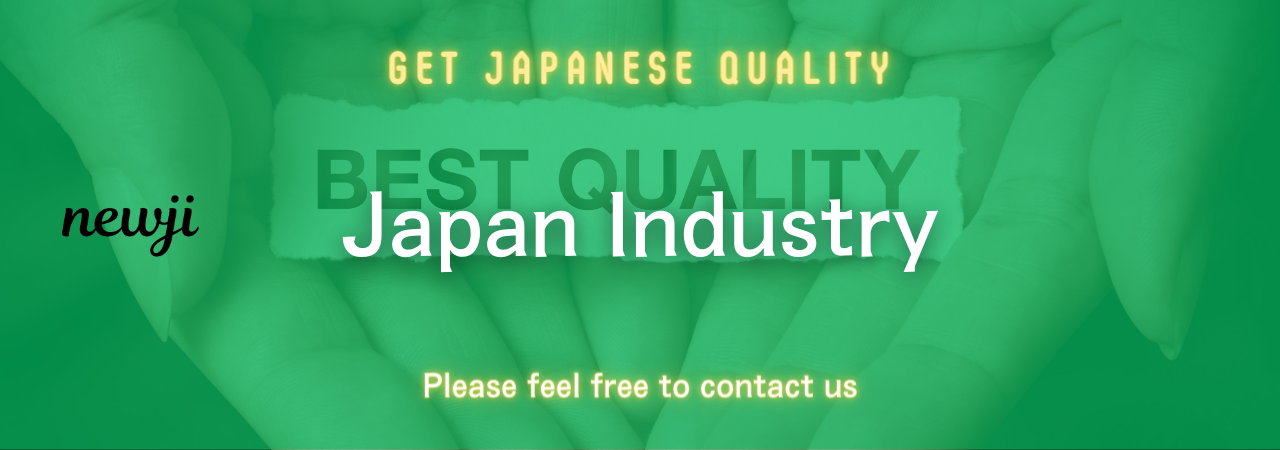
目次
Understanding ABS Resin
Acrylonitrile Butadiene Styrene, commonly known as ABS resin, is a popular thermoplastic polymer used in manufacturing various products due to its balanced properties of strength, durability, and workability.
It’s widely utilized in industries such as automotive, electronics, and consumer goods manufacturing.
However, small and medium-sized enterprises (SMEs) often encounter challenges when processing ABS resin that can impact production efficiency and product quality.
Understanding these challenges and how to troubleshoot them is crucial for maintaining competitiveness and profitability.
Common Processing Issues with ABS Resin
When working with ABS resin, SMEs may come across several processing issues that can lead to production inefficiencies or defects in finished products.
Here, we’ll explore some of these common issues and provide insights into their causes and solutions.
Melt Fracture
Melt fracture is a common issue where the surface of the ABS becomes rough and irregular during extrusion or injection molding.
This problem typically arises from excessive shear stress during processing.
To mitigate this issue, it is essential to optimize the processing temperature and screw speed.
Using a higher temperature within the recommended range for ABS can help reduce viscosity, allowing a smoother flow and minimizing shear stress.
Additionally, adjusting the screw speed to a slower setting may also help alleviate melt fracture.
Warping
Warping is a form defect where parts deform during the cooling process, affecting the structural integrity and appearance of the finished product.
This problem often occurs due to uneven cooling and internal stresses.
To troubleshoot warping, consider adjusting the cooling rate and ensuring uniform cooling across the entire part.
Using mold temperature controllers can help achieve this by regulating the temperature more accurately.
Moreover, optimizing the mold design to include uniform wall thicknesses can help in preventing internal stresses from causing warping during cooling.
Poor Surface Finish
Achieving a high-quality surface finish on ABS products is critical, especially for consumer goods and automotive parts.
Poor surface finish is often the result of improper mold temperature, inadequate venting, or contamination.
Ensuring that the mold temperature is set correctly according to the resin manufacturer’s recommendations can significantly improve the surface quality.
Proper venting of molds is also vital to prevent trapped air from leaving blemishes on the surface.
Additionally, maintaining a clean production environment and using high-purity ABS resin can help eliminate contamination issues.
Brittleness
Brittleness in ABS products can lead to premature product failure, which is particularly undesirable in applications requiring durability.
This issue is generally caused by excessive cooling rates or improper material blends.
Adjusting the cooling rate to ensure gradual cooling and allowing for proper crystalline formation can enhance the material’s impact strength.
Furthermore, working with reputable suppliers to obtain ABS materials with the correct blend ratio of acrylonitrile-butadiene-styrene components will help in maintaining the desired properties.
Flow Marks
Flow marks, also known as flow lines, are visible patterns that appear on the surface of molded parts, often detracting from the aesthetic appeal of the product.
These marks are typically a result of variations in the flow speed or temperature of the resin as it fills the mold.
To reduce flow marks, it is important to manage the injection speed and temperature effectively.
Gradual ramping of the injection speed and maintaining a consistent mold temperature can help achieve a uniform material flow, thereby minimizing visible flow patterns.
Optimizing ABS Resin Processing
Successfully processing ABS resin involves a combination of understanding the material’s properties and fine-tuning the production parameters.
Training and Expertise
Training the workforce in proper handling and processing techniques is essential.
Ensuring that operators are well-versed with the mechanical and thermal properties of ABS resin can lead to a significant reduction in production issues.
Invest in regular training sessions to keep your team updated with the latest best practices and advancements in resin processing technology.
Regular Maintenance of Equipment
Routine maintenance of processing equipment can prevent defects associated with wear and tear.
Ensure that machines are calibrated correctly and that any worn-out parts are replaced promptly to maintain precision in molding and extrusion processes.
Quality Control and Testing
Implementing stringent quality control processes ensures that each batch of ABS resin meets the specific requirements before entering production.
Conduct tests such as melt flow index and impact strength assessments to ascertain the material’s suitability for the intended application.
Supplier Collaboration and Feedback
Collaboration with ABS resin suppliers is vital to troubleshooting processing issues efficiently.
Providing feedback on material performance and seeking advice on optimal processing conditions can help enhance product outcomes.
Suppliers may offer insights or alternative resins better suited to your specific needs.
Conclusion
Processing ABS resin effectively necessitates a deep understanding of the material characteristics and meticulous adjustment of production processes.
For SMEs, overcoming the challenges associated with ABS resin processing is pivotal to maintaining product quality and competitive advantage in the market.
By addressing common issues such as melt fracture, warping, and brittleness through careful adjustments and process optimizations, SMEs can improve their production outcomes and ensure consistent product quality.
Staying informed about the latest processing technologies and maintaining strong communication with suppliers will further bolster the ability to troubleshoot and resolve ABS resin processing issues effectively.
資料ダウンロード
QCD調達購買管理クラウド「newji」は、調達購買部門で必要なQCD管理全てを備えた、現場特化型兼クラウド型の今世紀最高の購買管理システムとなります。
ユーザー登録
調達購買業務の効率化だけでなく、システムを導入することで、コスト削減や製品・資材のステータス可視化のほか、属人化していた購買情報の共有化による内部不正防止や統制にも役立ちます。
NEWJI DX
製造業に特化したデジタルトランスフォーメーション(DX)の実現を目指す請負開発型のコンサルティングサービスです。AI、iPaaS、および先端の技術を駆使して、製造プロセスの効率化、業務効率化、チームワーク強化、コスト削減、品質向上を実現します。このサービスは、製造業の課題を深く理解し、それに対する最適なデジタルソリューションを提供することで、企業が持続的な成長とイノベーションを達成できるようサポートします。
オンライン講座
製造業、主に購買・調達部門にお勤めの方々に向けた情報を配信しております。
新任の方やベテランの方、管理職を対象とした幅広いコンテンツをご用意しております。
お問い合わせ
コストダウンが利益に直結する術だと理解していても、なかなか前に進めることができない状況。そんな時は、newjiのコストダウン自動化機能で大きく利益貢献しよう!
(Β版非公開)