- お役立ち記事
- Troubleshooting and Reliability Improvement in Mold Design and Manufacturing
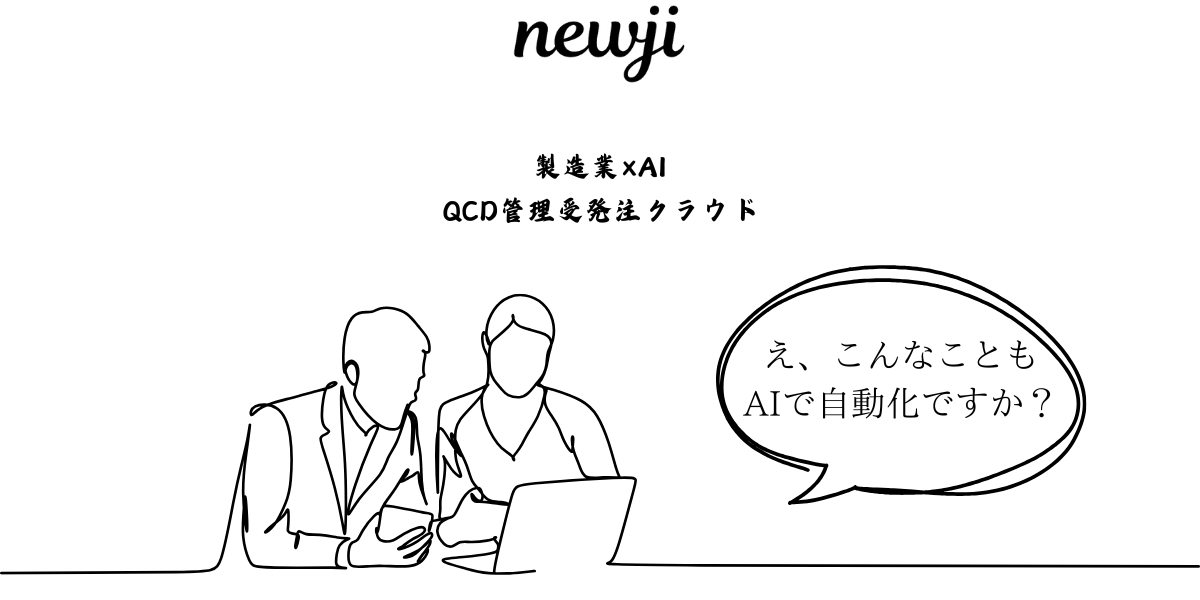
Troubleshooting and Reliability Improvement in Mold Design and Manufacturing
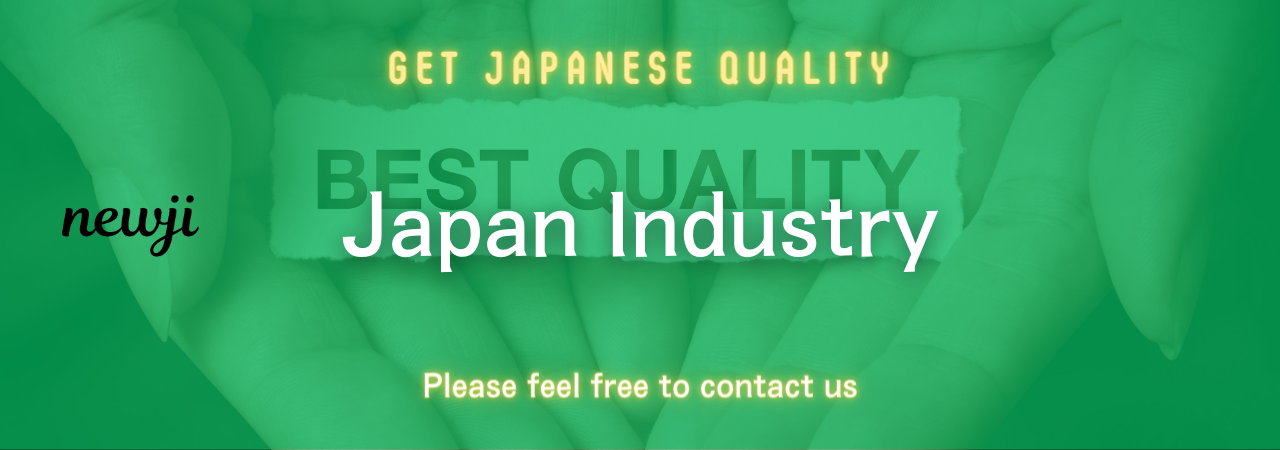
目次
Understanding the Basics of Mold Design and Manufacturing
When diving into the world of mold design and manufacturing, it’s important to first understand the basic principles involved.
Mold design is a key part of manufacturing processes where materials like plastic, metal, or rubber are shaped into specific forms.
The mold consists of several components designed to form the desired shape of the final product.
The process begins with a concept or design, which is then translated into a mold that will be both functional and efficient.
The mold must be carefully designed to ensure that it not only creates a high-quality product but also supports the ease and cost-effectiveness of manufacturing.
A well-designed mold can result in quicker production times and less waste, ultimately improving profitability.
Common Troubleshooting Issues in Mold Design
No manufacturing process is without its challenges, and mold design is no exception.
Understanding common troubleshooting issues can vastly improve efficiency and reliability in mold manufacturing.
One frequent issue involves improper cooling, which can lead to warping or deformities in the final product.
This is often due to an uneven distribution of cooling channels or an improperly balanced cooling system.
Ensuring consistent temperature control is critical to producing an accurate and defect-free product.
Another common problem occurs when there are design flaws such as sharp corners or thin walls that make the mold difficult to fill.
These design errors can lead to incomplete parts with defects or weak spots that could cause the product to fail.
Addressing these issues requires a deep dive into the design phase to make necessary adjustments for smoother production.
Material Considerations in Mold Manufacturing
The choice of material plays an important role in the mold design and manufacturing process.
Different materials will react differently under heat and pressure, making it crucial to select one that aligns with the intended use of the final product.
For instance, plastic molds are increasingly popular due to their versatility and cost-effectiveness.
However, incorrect material selection can lead to problems such as shrinkage or chemical incompatibility, affecting the product’s quality and performance.
Understanding the mechanical properties of the materials in use can prevent such issues and ensure reliable results.
Furthermore, the properties of the mold material can influence the wear and tear of the mold itself, impacting its longevity and requiring more frequent maintenance or replacements.
Selecting a durable material not only extends the life of the mold but also reduces production downtime.
Techniques for Reliability Improvement
Improving the reliability of mold design and manufacturing involves both technical strategies and innovative approaches.
One effective method is the integration of computer-aided design (CAD) and simulation tools, which allow designers to visualize and test their designs in a virtual environment.
This helps identify potential problems before the mold is actually produced, saving both time and resources.
Another approach is employing robust quality control measures throughout the manufacturing process.
Regular inspections and in-process checks can catch defects early, allowing for quick corrections and minimizing the risk of producing faulty products.
Investing in advanced quality assurance procedures ensures that each product meets specific standards and expectations.
Regular maintenance and upkeep of molds are also essential to sustaining long-term reliability.
Scheduling preventive maintenance checks can help identify wear and tear issues before they become significant problems, ensuring continuous and efficient production.
Future Trends in Mold Design
The future of mold design and manufacturing holds exciting potential with advancements in technology and innovation.
3D printing, for instance, is making strides in the industry, offering new possibilities for creating complex mold designs with ease and precision.
This technology allows for quicker prototyping and the potential for more intricate designs that were once difficult or impossible to achieve with traditional methods.
Automation and the use of smart technologies are also paving the way for improvements in mold manufacturing.
Automated systems can enhance productivity by reducing manual intervention and human errors, while smart sensors and IoT devices provide real-time data insights for better decision-making and process efficiency.
Sustainability is becoming increasingly important, and manufacturers are looking for ways to minimize their environmental impact.
This includes adopting sustainable practices and materials that reduce waste and energy consumption during the manufacturing process.
Steps to Ensure Successful Mold Manufacturing
To ensure successful outcomes in mold design and manufacturing, several steps can be taken.
Firstly, investing in comprehensive training programs for designers and engineers will ensure that they are well-equipped with the latest knowledge and skills in the field.
Staying up-to-date with industry trends and best practices plays an important role in maintaining a competitive edge.
Secondly, establishing clear communication between design teams, engineers, and manufacturers can prevent misunderstandings and misalignments that often lead to errors in production.
Collaborative efforts result in more coherent strategies and solutions.
Finally, setting up a feedback loop with customers can provide valuable insights into performance and user satisfaction, spotlighting opportunities for improvement in product design and performance.
By following these guidelines and embracing both conventional and innovative strategies, success in mold design and manufacturing is achievable, ensuring robust, reliable, and efficient production processes.
資料ダウンロード
QCD調達購買管理クラウド「newji」は、調達購買部門で必要なQCD管理全てを備えた、現場特化型兼クラウド型の今世紀最高の購買管理システムとなります。
ユーザー登録
調達購買業務の効率化だけでなく、システムを導入することで、コスト削減や製品・資材のステータス可視化のほか、属人化していた購買情報の共有化による内部不正防止や統制にも役立ちます。
NEWJI DX
製造業に特化したデジタルトランスフォーメーション(DX)の実現を目指す請負開発型のコンサルティングサービスです。AI、iPaaS、および先端の技術を駆使して、製造プロセスの効率化、業務効率化、チームワーク強化、コスト削減、品質向上を実現します。このサービスは、製造業の課題を深く理解し、それに対する最適なデジタルソリューションを提供することで、企業が持続的な成長とイノベーションを達成できるようサポートします。
オンライン講座
製造業、主に購買・調達部門にお勤めの方々に向けた情報を配信しております。
新任の方やベテランの方、管理職を対象とした幅広いコンテンツをご用意しております。
お問い合わせ
コストダウンが利益に直結する術だと理解していても、なかなか前に進めることができない状況。そんな時は、newjiのコストダウン自動化機能で大きく利益貢献しよう!
(Β版非公開)