- お役立ち記事
- Troubleshooting and reliability improvement in mold design and processing technology
月間76,176名の
製造業ご担当者様が閲覧しています*
*2025年3月31日現在のGoogle Analyticsのデータより
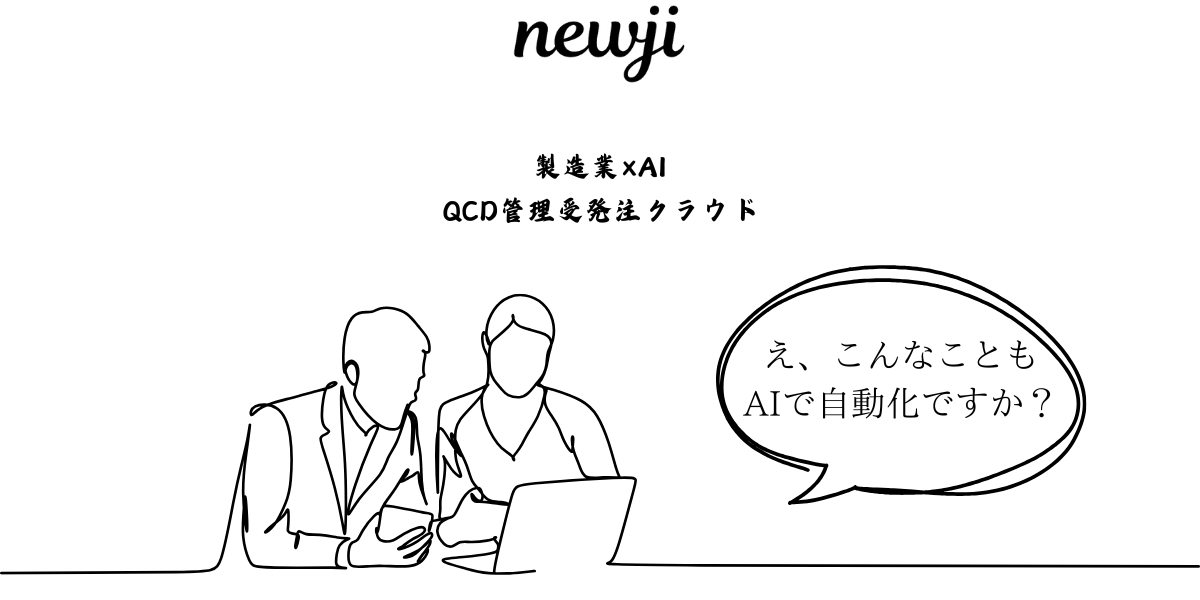
Troubleshooting and reliability improvement in mold design and processing technology
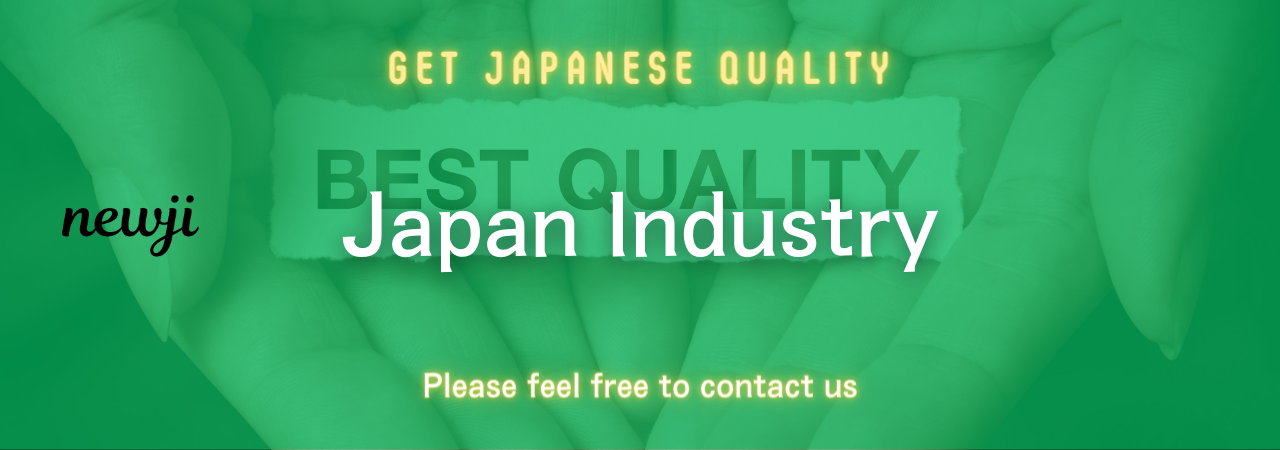
目次
Understanding Mold Design and Processing Technology
Mold design and processing technology are critical components in the manufacturing industry.
They play a significant role in the production of high-quality products, from automotive parts to household items.
Over time, advances in this field have led to more efficient and reliable manufacturing processes.
However, like any other complex system, mold design and processing technology can encounter troubleshooting issues that affect productivity and quality.
Improving the reliability of these technologies is essential for maintaining a competitive edge in the market.
The Basics of Mold Design
Mold design is a meticulous process that begins with understanding the product specifications and requirements.
It involves creating a blueprint for the mold, which includes detailed instructions on how the mold should be constructed.
Mold designers use specialized software to create 3D models and simulations, allowing them to predict the mold’s performance before it is physically built.
Key considerations in mold design include material selection, mold size, and the intricacy of the design.
Selecting the right material is crucial because it affects the mold’s durability and the quality of the final product.
The overall design needs to ensure efficient production, minimizing waste and reducing cycle times.
Common Issues in Mold Design
Despite advances in technology, mold design can still face several challenges that need troubleshooting.
Warping, cracking, and misalignment are some of the common issues that can occur in improperly designed molds.
These issues can result in defective products, leading to increased costs and waste.
Warping generally occurs due to uneven cooling of the molded product.
Proper thermal management within the mold design is crucial to prevent this issue.
Misalignment, on the other hand, can cause products to be out of tolerance, affecting how well the parts fit together.
Improving Mold Design Reliability
Enhancing the reliability of mold design involves a systematic approach to problem-solving.
First, thorough testing and simulation during the design phase can catch potential issues early on.
Using finite element analysis (FEA) software, designers can simulate how the mold will behave under various conditions, helping to optimize the design before manufacturing begins.
Material selection is another area where improvements can significantly boost reliability.
Choosing high-quality materials that can withstand operational conditions without degrading ensures longer mold life and consistent product quality.
Iterative testing and improvements can also help.
By continuously evaluating mold performance and making necessary adjustments, manufacturers can enhance reliability over time.
Challenges in Mold Processing Technology
In addition to design, mold processing technology is another critical area where issues can occur.
Processing involves the actual creation of products using the mold, and it requires precision and control to produce products of the desired quality.
Common problems in mold processing include flash, short shots, and sink marks.
Flash occurs when molten material seeps through the parting line of the mold, creating excess material on the finished product.
Short shots are caused by insufficient material filling the mold cavity, leading to incomplete products.
Sink marks are surface depressions that occur due to uneven cooling or shrinkage.
Enhancing Reliability in Mold Processing
To improve reliability in mold processing, manufacturers need to adopt stringent process controls and use advanced technology.
Monitoring and controlling parameters such as temperature, pressure, and injection speed can prevent defects and ensure consistent quality.
Automation and the use of sensors allow for real-time monitoring, enabling quick identification and correction of issues as they arise.
Regular maintenance of mold machinery is crucial.
By keeping equipment in optimal condition, manufacturers can reduce downtime and prevent unexpected failures that could disrupt production.
Training and skill development of personnel are also vital.
Well-trained technicians can identify potential issues and perform necessary adjustments, reducing dependency on trial-and-error methods.
Innovation and Future Trends
The field of mold design and processing technology continues to evolve with new innovations and trends reshaping the industry.
One emerging trend is the incorporation of digital twins in the manufacturing process.
A digital twin is a virtual model of the physical mold, allowing manufacturers to simulate, analyze, and optimize the mold in real-time.
This technology improves not only mold performance but also the efficiency and effectiveness of the manufacturing process.
Another significant trend is the use of sustainable materials and practices.
As environmental concerns increase, manufacturers are turning to biodegradable and recyclable materials to reduce the environmental impact of their products.
This approach not only meets regulatory requirements but also enhances the brand reputation of manufacturers committed to sustainability.
Furthermore, additive manufacturing, also known as 3D printing, is gaining traction in mold-making.
This technology allows for the rapid prototyping and production of complex mold designs, reducing lead times and costs.
By staying abreast of these trends and continuously improving reliability in both mold design and processing technology, manufacturers can maintain their competitive advantage and meet the evolving demands of the market.
In conclusion, troubleshooting and reliability improvement are crucial for success in mold design and processing technology.
By focusing on detailed design practices, efficient processing methods, and embracing emerging technologies, manufacturers can enhance the quality and efficiency of their operations.
資料ダウンロード
QCD管理受発注クラウド「newji」は、受発注部門で必要なQCD管理全てを備えた、現場特化型兼クラウド型の今世紀最高の受発注管理システムとなります。
ユーザー登録
受発注業務の効率化だけでなく、システムを導入することで、コスト削減や製品・資材のステータス可視化のほか、属人化していた受発注情報の共有化による内部不正防止や統制にも役立ちます。
NEWJI DX
製造業に特化したデジタルトランスフォーメーション(DX)の実現を目指す請負開発型のコンサルティングサービスです。AI、iPaaS、および先端の技術を駆使して、製造プロセスの効率化、業務効率化、チームワーク強化、コスト削減、品質向上を実現します。このサービスは、製造業の課題を深く理解し、それに対する最適なデジタルソリューションを提供することで、企業が持続的な成長とイノベーションを達成できるようサポートします。
製造業ニュース解説
製造業、主に購買・調達部門にお勤めの方々に向けた情報を配信しております。
新任の方やベテランの方、管理職を対象とした幅広いコンテンツをご用意しております。
お問い合わせ
コストダウンが利益に直結する術だと理解していても、なかなか前に進めることができない状況。そんな時は、newjiのコストダウン自動化機能で大きく利益貢献しよう!
(β版非公開)