- お役立ち記事
- Troubleshooting Clamping Force and Practical Examples of Quality Improvement
Troubleshooting Clamping Force and Practical Examples of Quality Improvement
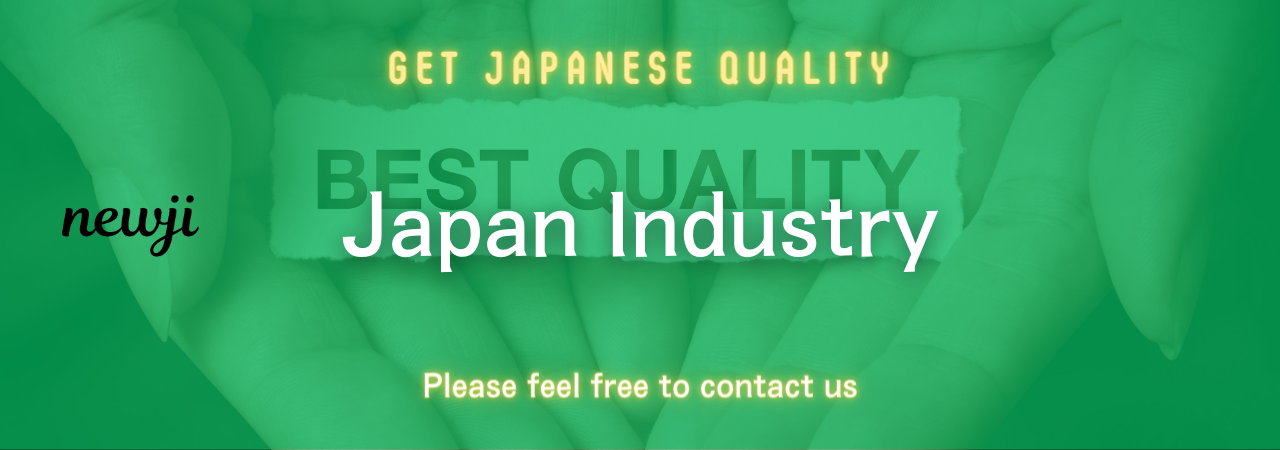
目次
Understanding Clamping Force
Clamping force is a critical concept in various manufacturing and assembly processes.
It refers to the pressure applied to hold components together firmly during processes like welding, machining, or injection molding.
The importance of achieving the correct clamping force cannot be overstated, as it impacts the quality and reliability of the final product.
The tricky part about clamping force is that it needs to be just right.
Too little force may cause parts to shift or come loose, while too much force can damage the material or the equipment.
Finding that balance requires careful calibration and ongoing monitoring.
Common Issues with Clamping Force
Misjudging clamping force is a common issue across different industries.
One frequent problem is the incorrect setting of equipment, where the applied force is either too weak or too strong.
This can stem from improper equipment maintenance or lack of calibration.
In other cases, the material properties might change due to temperature or wear and tear, affecting how clamping force is applied.
Operator error is another issue.
Even with automated systems, human oversight is critical to ensure everything is running smoothly.
Operators must be well-trained to recognize signs of inappropriate clamping force, such as unusual noise or vibration.
Unfortunately, not all operators may be adequately trained, leading to potential quality issues.
Key Strategies for Resolving Clamping Force Issues
Addressing clamping force problems starts with proper equipment calibration.
Regular maintenance and check-ups can prevent many issues related to machinery.
By ensuring that equipment settings are correct and tools are in good condition, manufacturers can avoid over or under-application of force.
Another strategy is using advanced monitoring systems.
These systems can automatically adjust the clamping force based on real-time data, adapting to any changes in material properties or environmental conditions.
Such technology minimizes the chance of human error and ensures consistent product quality.
Training is paramount for operators.
Providing comprehensive training sessions that cover the principles of clamping force and its impact on quality can enhance operator competence.
An operator who understands the mechanics behind their tasks will be better equipped to troubleshoot and fix any arising issues.
Practical Examples of Quality Improvement
The auto industry often faces clamping force challenges, especially during assembly.
One practical example is improving welding joints in car bodies.
Manufacturers have started using robotics with precise clamping force controls that adapt in real-time, ensuring every weld is of uniform quality.
Such advancements significantly reduce defect rates and improve overall vehicle safety.
In the realm of electronics, achieving the right clamping force during the assembly of circuit boards is crucial.
Too much force can damage delicate components, while too little can lead to poor connections.
By implementing automated systems that adjust force appropriately, electronics manufacturers report fewer malfunctions and higher customer satisfaction.
Injection molding is another area where controlling clamping force is vital.
For instance, manufacturers of plastic containers have to ensure consistent thickness and integrity.
By fine-tuning clamping force and using sensors to detect pressure deviations, production becomes more efficient, with less scrap and rework required.
Innovative Solutions for Future Improvements
As technology progresses, innovative solutions continue to emerge for clamping force challenges.
Smart sensors integrated into machinery can provide detailed data, allowing for predictive maintenance and reducing downtime.
These sensors can alert technicians of potential issues before they escalate, thus enhancing overall productivity.
Another potential innovation lies in the use of Artificial Intelligence (AI) to optimize clamping processes.
AI can analyze large datasets to determine the ideal clamping parameters for different materials and conditions.
By leveraging AI, manufacturers can further enhance precision and reduce human reliance on manual adjustments.
The development of eco-friendly materials also presents an opportunity for improvement.
These materials may require different clamping force considerations, prompting the need for enhanced testing and calibration protocols.
By understanding how new materials interact with existing clamping systems, manufacturers can adjust their production processes for better environmental sustainability.
Conclusion
Clamping force plays a crucial role in determining the quality and durability of products across various industries.
By addressing common issues and implementing effective strategies, manufacturers can greatly enhance their production outcomes.
Through regular maintenance, advanced monitoring systems, and comprehensive operator training, common pitfalls can be avoided.
With ongoing technological advancements, the future of clamping force management looks promising.
Integrating AI, smart sensors, and sustainable practices will drive further improvements.
Ultimately, by embracing these solutions, manufacturers will enrich product quality and consumer trust while fostering a culture of continuous improvement.
資料ダウンロード
QCD調達購買管理クラウド「newji」は、調達購買部門で必要なQCD管理全てを備えた、現場特化型兼クラウド型の今世紀最高の購買管理システムとなります。
ユーザー登録
調達購買業務の効率化だけでなく、システムを導入することで、コスト削減や製品・資材のステータス可視化のほか、属人化していた購買情報の共有化による内部不正防止や統制にも役立ちます。
NEWJI DX
製造業に特化したデジタルトランスフォーメーション(DX)の実現を目指す請負開発型のコンサルティングサービスです。AI、iPaaS、および先端の技術を駆使して、製造プロセスの効率化、業務効率化、チームワーク強化、コスト削減、品質向上を実現します。このサービスは、製造業の課題を深く理解し、それに対する最適なデジタルソリューションを提供することで、企業が持続的な成長とイノベーションを達成できるようサポートします。
オンライン講座
製造業、主に購買・調達部門にお勤めの方々に向けた情報を配信しております。
新任の方やベテランの方、管理職を対象とした幅広いコンテンツをご用意しております。
お問い合わせ
コストダウンが利益に直結する術だと理解していても、なかなか前に進めることができない状況。そんな時は、newjiのコストダウン自動化機能で大きく利益貢献しよう!
(Β版非公開)