- お役立ち記事
- Troubleshooting Extrusion Molding: Common Issues and Their Solutions
Troubleshooting Extrusion Molding: Common Issues and Their Solutions
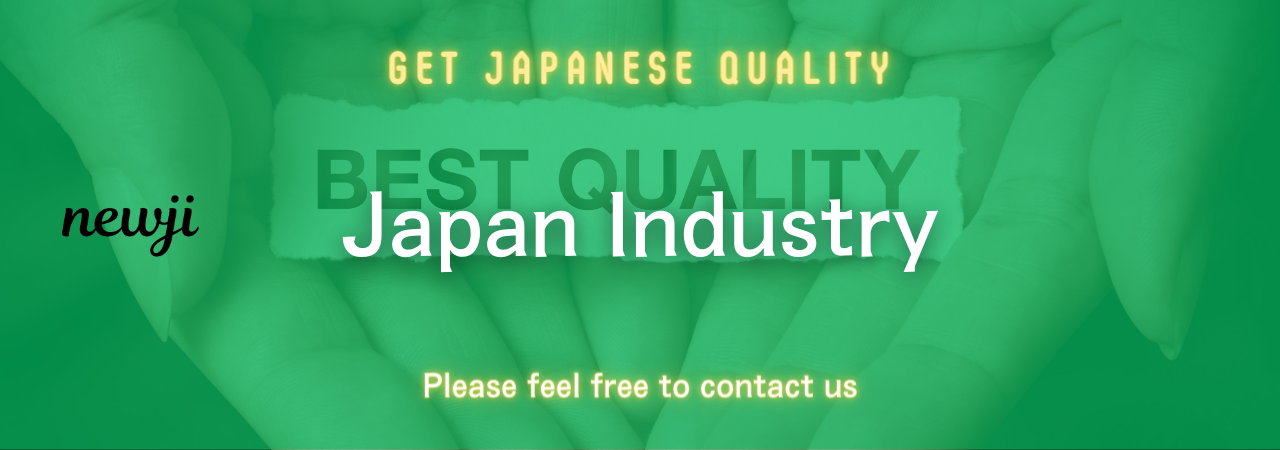
目次
Introduction to Extrusion Molding
Extrusion molding is a cornerstone process in manufacturing, widely used to create objects with a fixed cross-sectional profile such as pipes, sheets, and films.
Over the years, this process has proven to be efficient and versatile, accommodating a range of materials from plastics to metals.
Despite its benefits, extrusion molding can present challenges.
Understanding these common issues, along with their solutions, can significantly improve the quality and efficiency of the production process.
Understanding the Extrusion Process
Before diving into troubleshooting, it’s crucial to grasp the basics of extrusion molding.
In this process, raw material is melted and forced through a die to form a continuous shape.
The extruded product is then cooled and cut to the desired length.
Attention to every stage of this process is vital, as small variations can lead to defects or inefficiencies.
Common Extrusion Molding Issues
Though effective, extrusion molding is not free from issues.
Below are some of the most frequent problems encountered during the process:
1. Surface Defects
Surface defects, such as rough surfaces, die lines, or sharkskin, are common in extrusion.
These defects not only affect the appearance but can also compromise the performance of the final product.
2. Dimensional Inaccuracy
Achieving precise dimensions is essential in extrusion molding.
Deviations can lead to products that don’t fit their intended application, leading to material wastage and rework.
3. Inconsistent Wall Thickness
Variation in wall thickness can trigger several problems including structural weakness and increased material costs.
4. Melt Fracture
Melt fracture occurs when the polymer melt behaves in a non-linear manner as it exits the die, causing irregularities in the surface finish.
5. Uneven Cooling
Inadequate or uneven cooling of the extruded material can result in warping or deformation, affecting the final product’s structural integrity.
Solutions to Common Extrusion Issues
Addressing these issues isn’t just about spotting defects but adopting practical solutions to mitigate them.
Here are some solutions to the common problems:
1. Resolving Surface Defects
To tackle rough surfaces or defects such as sharkskin, opt for smoother dies and check the extrusion speed.
Reducing extrusion speed and optimizing die temperature can also help achieve a smoother finish.
2. Ensuring Dimensional Accuracy
Regular calibration and maintenance of the die and other extrusion equipment is crucial for dimensional accuracy.
Implementing accurate temperature control mechanisms and uniform material feeding can also enhance precision.
3. Attaining Consistent Wall Thickness
Consistency in wall thickness can be improved through optimal die design and alignment.
Real-time monitoring and adjustments of the material flow and extrusion speed are critical for uniformity in wall thickness.
4. Preventing Melt Fracture
Melt fracture can be minimized by ensuring a smooth transition of the melt through the die.
Adjusting melt temperatures and reducing the shear rate can also help alleviate the occurrence of this issue.
5. Promoting Even Cooling
To prevent warping or deformation caused by uneven cooling, ensure that the cooling process is uniform.
This can be achieved through proper placement and calibration of cooling equipment, along with optimizing coolant flow rates.
Additional Tips for Optimal Extrusion Molding
There are several proactive measures manufacturers can take to circumvent common extrusion problems.
Routine inspections and regular maintenance of equipment play a key role in preventing unexpected downtimes and maintaining high product quality.
Investing in training for technical personnel ensures that potential issues are identified and addressed early in the process.
Continuous improvements and finding new ways to optimize the process can lead to better product quality and operational efficiency.
Conclusion
Troubleshooting extrusion molding requires a systematic approach to identify the root cause of common issues and implement effective solutions.
By addressing surface defects, maintaining dimensional accuracy, ensuring consistent wall thickness, preventing melt fracture, and promoting even cooling, manufacturers can significantly enhance their production process.
Staying vigilant and proactive can lead not only to superior product quality but also to lower operational costs and greater customer satisfaction.
Understanding and applying these solutions can be the key to excelling in the extrusion molding industry.
資料ダウンロード
QCD調達購買管理クラウド「newji」は、調達購買部門で必要なQCD管理全てを備えた、現場特化型兼クラウド型の今世紀最高の購買管理システムとなります。
ユーザー登録
調達購買業務の効率化だけでなく、システムを導入することで、コスト削減や製品・資材のステータス可視化のほか、属人化していた購買情報の共有化による内部不正防止や統制にも役立ちます。
NEWJI DX
製造業に特化したデジタルトランスフォーメーション(DX)の実現を目指す請負開発型のコンサルティングサービスです。AI、iPaaS、および先端の技術を駆使して、製造プロセスの効率化、業務効率化、チームワーク強化、コスト削減、品質向上を実現します。このサービスは、製造業の課題を深く理解し、それに対する最適なデジタルソリューションを提供することで、企業が持続的な成長とイノベーションを達成できるようサポートします。
オンライン講座
製造業、主に購買・調達部門にお勤めの方々に向けた情報を配信しております。
新任の方やベテランの方、管理職を対象とした幅広いコンテンツをご用意しております。
お問い合わせ
コストダウンが利益に直結する術だと理解していても、なかなか前に進めることができない状況。そんな時は、newjiのコストダウン自動化機能で大きく利益貢献しよう!
(Β版非公開)