- お役立ち記事
- Troubleshooting Filling Time and Key Points for Quality Control
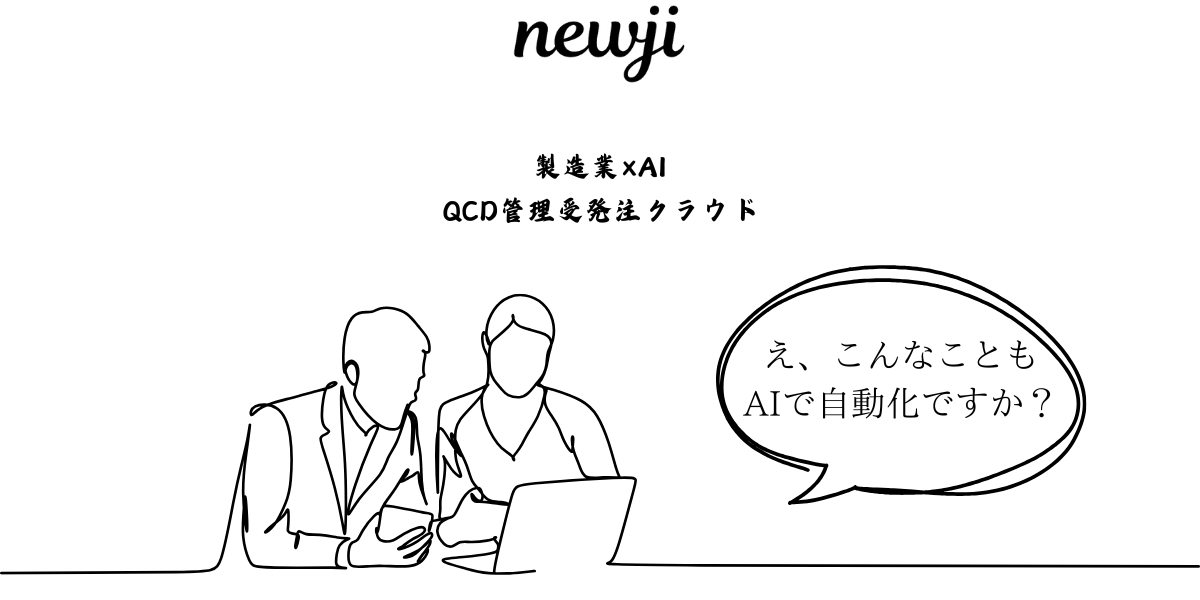
Troubleshooting Filling Time and Key Points for Quality Control
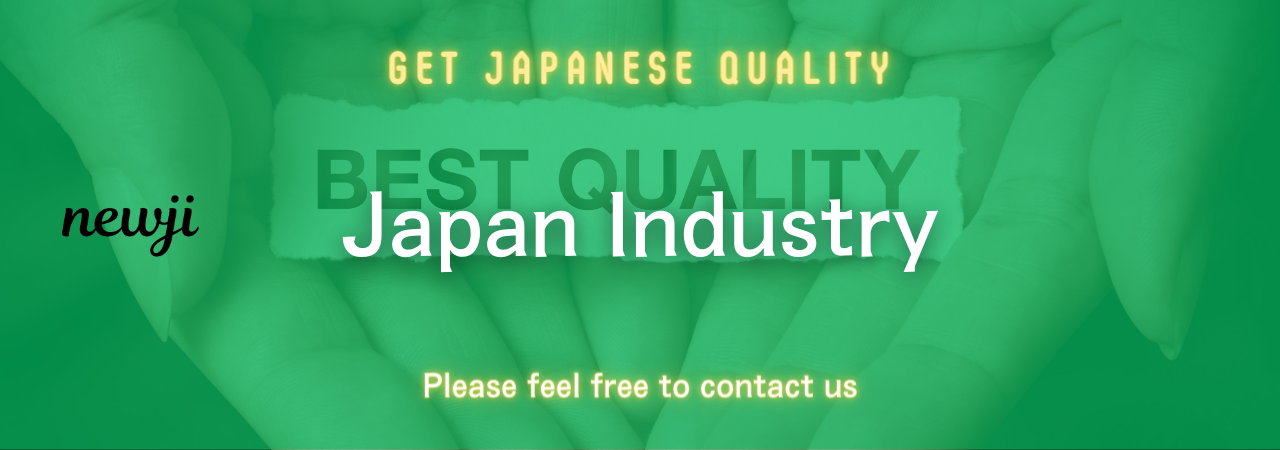
目次
Understanding Filling Time in Production
Filling time in production refers to the duration required to fill a product into its container or packaging.
This process is crucial in various industries such as food, beverages, pharmaceuticals, and cosmetics.
Efficient filling time ensures that products are packaged at optimal speed without compromising quality.
In many production lines, filling time can significantly impact overall productivity and efficiency.
Too slow, and it leads to bottlenecks in the production process.
Too fast, and it may cause spillage or improper sealing, which can affect product quality.
Therefore, understanding and managing filling time is essential for maintaining a smooth operation.
Common Issues Affecting Filling Time
Several issues can affect filling time in production lines.
Recognizing these problems helps in troubleshooting and improving the process’s efficiency.
Equipment Malfunction
One common issue is machinery failure or malfunction.
Old or poorly maintained equipment may operate below optimal speed, causing delays.
Regular maintenance and timely updates can help mitigate this issue and ensure machines work at their designated capacities.
Inconsistent Product Viscosity
In industries like food and cosmetics, the viscosity of the product can affect filling time.
If the product is too thick, it might fill containers more slowly, whereas a too thin product might lead to spills or overfills.
Regularly checking product consistency can help in adjusting filling speeds appropriately.
Improper Calibration
Machines and equipment need to be correctly calibrated to ensure they fill containers accurately.
Improper calibration can lead to variability in the amounts dispensed, resulting in either underfilled or overfilled containers.
Regular checks and calibrations can ensure that your equipment is set to the appropriate settings.
Operator Error
Human error is another factor that can impact filling time.
Operators may fail to set machines correctly or misinterpret the speed at which products should be filled.
Proper training and supervision can help minimize operator errors.
Strategies for Troubleshooting Filling Time
Having a set of strategies to address filling time issues is crucial for maintaining efficient production.
Regular Maintenance and Inspection
Scheduling regular maintenance and inspections for machinery and equipment can help identify potential problems before they cause delays.
This proactive approach can prevent breakdowns and ensure that machines operate at optimal speed and efficiency.
Quality Control Checks
Implementing consistent quality control checks can help spot issues with product viscosity and container sealing.
These checks ensure that products meet the required standards and help identify areas that need adjustment or improvement.
Employee Training
Providing ongoing training for employees is essential to prevent operator errors.
Training should cover machine operation, safety standards, and troubleshooting techniques.
A well-trained workforce can significantly reduce mistakes and improve filling time efficiency.
Investing in Technology
Investing in newer, more efficient technology can greatly improve filling time.
Automated systems can make adjustments in real-time, reducing the chances of human error and improving accuracy and speed.
These systems often come equipped with smart sensors and AI technology that optimize the filling process.
Key Points for Quality Control
Quality control is an integral aspect of managing filling time efficiently and ensuring product standards are met.
Consistent Product Standards
Maintaining consistent product standards is essential in production.
Ensuring that each batch of product has the same viscosity and composition can prevent disruptions in filling time.
Regular lab testing and quality checks can help maintain these standards.
Sealing and Packaging
Properly sealed and packaged products are crucial for maintaining quality.
Poor sealing can lead to contamination or spoilage.
Quality control processes should include checks for proper sealing and material integrity.
Batch Testing
Conducting batch testing helps in identifying any issues with the filling process.
Testing random samples from each production batch can help detect any anomalies and determine if adjustments are needed.
Monitoring and Recording
Keeping detailed records of production processes and outcomes aids in quality control.
These records can highlight patterns or recurring issues, enabling prompt corrective action.
Data analysis can also provide insights for improving efficiency and quality.
Improving Filling Time for Better Quality and Efficiency
Optimizing filling time not only enhances production efficiency but also assures the quality and consistency of the product.
By understanding potential issues and implementing effective troubleshooting strategies, businesses can streamline their operations.
Organizations should focus on regular maintenance, rigorous quality control checks, employee training, and technology investment.
These measures collectively contribute to a smoother production process and help address issues promptly, resulting in improved filling time and overall product quality.
資料ダウンロード
QCD調達購買管理クラウド「newji」は、調達購買部門で必要なQCD管理全てを備えた、現場特化型兼クラウド型の今世紀最高の購買管理システムとなります。
ユーザー登録
調達購買業務の効率化だけでなく、システムを導入することで、コスト削減や製品・資材のステータス可視化のほか、属人化していた購買情報の共有化による内部不正防止や統制にも役立ちます。
NEWJI DX
製造業に特化したデジタルトランスフォーメーション(DX)の実現を目指す請負開発型のコンサルティングサービスです。AI、iPaaS、および先端の技術を駆使して、製造プロセスの効率化、業務効率化、チームワーク強化、コスト削減、品質向上を実現します。このサービスは、製造業の課題を深く理解し、それに対する最適なデジタルソリューションを提供することで、企業が持続的な成長とイノベーションを達成できるようサポートします。
オンライン講座
製造業、主に購買・調達部門にお勤めの方々に向けた情報を配信しております。
新任の方やベテランの方、管理職を対象とした幅広いコンテンツをご用意しております。
お問い合わせ
コストダウンが利益に直結する術だと理解していても、なかなか前に進めることができない状況。そんな時は、newjiのコストダウン自動化機能で大きく利益貢献しよう!
(Β版非公開)