- お役立ち記事
- Troubleshooting Fluororesin Processing for SMEs
Troubleshooting Fluororesin Processing for SMEs
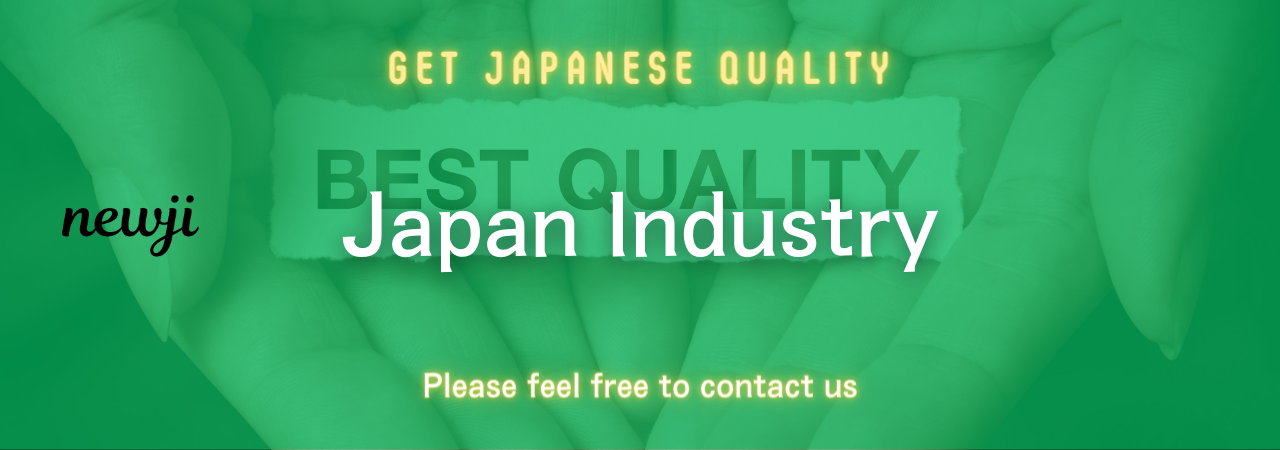
目次
Understanding Fluororesin
Fluororesin, commonly known as PTFE (Polytetrafluoroethylene), is a versatile material widely used in various industries due to its unique properties.
It is known for its high resistance to heat, chemical reactions, and electrical insulation, making it ideal for small and medium enterprises (SMEs) involved in manufacturing and industrial processes.
However, processing fluororesin can pose certain challenges, particularly for SMEs that may not have access to the same resources as larger corporations.
In this article, we’ll explore some essential troubleshooting tips to help SMEs optimize their fluororesin processing.
Identifying Common Processing Issues
Before diving into troubleshooting, it is essential to identify the common challenges faced during fluororesin processing.
One of the primary issues is poor adhesion, which can result in delamination or separation of layers in products.
Additionally, SMEs may encounter difficulties with uneven thickness distribution or achieving the desired surface finish.
Understanding these issues is the first step in finding effective solutions.
Choosing the Right Processing Method
Fluororesin can be processed through various methods, including extrusion, injection molding, and compression molding.
Each method has its benefits and challenges, so SMEs should carefully evaluate which one suits their specific needs.
Extrusion is great for producing continuous lengths of products and is often used for tubing or rod shapes.
Injection molding is ideal for creating intricate shapes but may require more expensive tooling.
Compression molding is suitable for producing large, solid parts but might present challenges in temperature control.
Evaluate your production requirements, product specifications, and budget to choose the appropriate processing method.
Optimizing Temperature Settings
One of the critical factors in fluororesin processing is maintaining the correct temperature settings.
Fluororesin has a high melting point, but overheating can lead to thermal degradation, affecting product quality.
On the other hand, underheating can cause insufficient melting, leading to incomplete products.
Ensure that your equipment is properly calibrated and that operators are trained to maintain accurate temperature settings.
Regular maintenance of heating elements and temperature monitoring can prevent these issues.
Ensuring Mold Quality and Design
The quality and design of the mold play a crucial role in the success of fluororesin processing.
Improper mold design can lead to issues such as incomplete filling, air traps, or flash formation.
To avoid these problems, SMEs should work with skilled mold designers and fabricators who are experienced in fluororesin processing.
Precision in mold design ensures that the material fills the mold evenly, resulting in high-quality final products.
Regular inspection and maintenance of molds are also essential to prevent wear and tear, which can affect product quality.
Troubleshooting Adhesion Problems
Adhesion problems in fluororesin products can be challenging due to the material’s non-stick properties.
One effective way to enhance adhesion is by employing surface treatment techniques.
Surface roughening, plasma treatment, or chemical etching can create a bonding surface for adhesives or coatings.
SMEs can also use primers specifically designed for fluororesin to improve adhesion properties.
It is important to test these treatments in small batches to determine the best approach for your particular application.
Addressing Uneven Thickness Issues
Uneven thickness distribution is a common problem in fluororesin processing, and it is often caused by improper material flow or temperature gradients.
Ensuring uniform material flow can be achieved by optimizing mold design and flow paths.
Additionally, using flow simulation software can help identify potential areas of concern before actual production begins.
Temperature gradients can be minimized by ensuring proper heater placement and using appropriately insulated equipment.
Monitoring temperature distribution throughout the process is vital to achieve consistent thickness in products.
Improving Surface Finish
Achieving the desired surface finish in fluororesin products can be challenging due to its slippery and non-stick nature.
To improve surface finish, SMEs can employ polishing techniques or use additives in the material formulation.
Selecting the right type of filler or additive can enhance surface properties.
Additionally, controlling the cooling rate during processing can help achieve a smooth and even surface finish.
Testing different cooling rates and surface treatments can provide insights into achieving the desired aesthetic qualities.
Conclusion
Processing fluororesin can be challenging for SMEs, but with the right approach and understanding of the material, it can be effectively managed.
By identifying common problems, optimizing processing methods, and implementing effective troubleshooting techniques, SMEs can enhance their production capabilities.
Remember to prioritize quality control, invest in skilled personnel, and stay updated with the latest technology and methodologies in fluororesin processing.
These steps will help SMEs successfully navigate the complexities of fluororesin, leading to high-quality products and customer satisfaction.
資料ダウンロード
QCD調達購買管理クラウド「newji」は、調達購買部門で必要なQCD管理全てを備えた、現場特化型兼クラウド型の今世紀最高の購買管理システムとなります。
ユーザー登録
調達購買業務の効率化だけでなく、システムを導入することで、コスト削減や製品・資材のステータス可視化のほか、属人化していた購買情報の共有化による内部不正防止や統制にも役立ちます。
NEWJI DX
製造業に特化したデジタルトランスフォーメーション(DX)の実現を目指す請負開発型のコンサルティングサービスです。AI、iPaaS、および先端の技術を駆使して、製造プロセスの効率化、業務効率化、チームワーク強化、コスト削減、品質向上を実現します。このサービスは、製造業の課題を深く理解し、それに対する最適なデジタルソリューションを提供することで、企業が持続的な成長とイノベーションを達成できるようサポートします。
オンライン講座
製造業、主に購買・調達部門にお勤めの方々に向けた情報を配信しております。
新任の方やベテランの方、管理職を対象とした幅広いコンテンツをご用意しております。
お問い合わせ
コストダウンが利益に直結する術だと理解していても、なかなか前に進めることができない状況。そんな時は、newjiのコストダウン自動化機能で大きく利益貢献しよう!
(Β版非公開)