- お役立ち記事
- Troubleshooting in Extrusion Molding: Common Problems and Solutions
月間76,176名の
製造業ご担当者様が閲覧しています*
*2025年3月31日現在のGoogle Analyticsのデータより
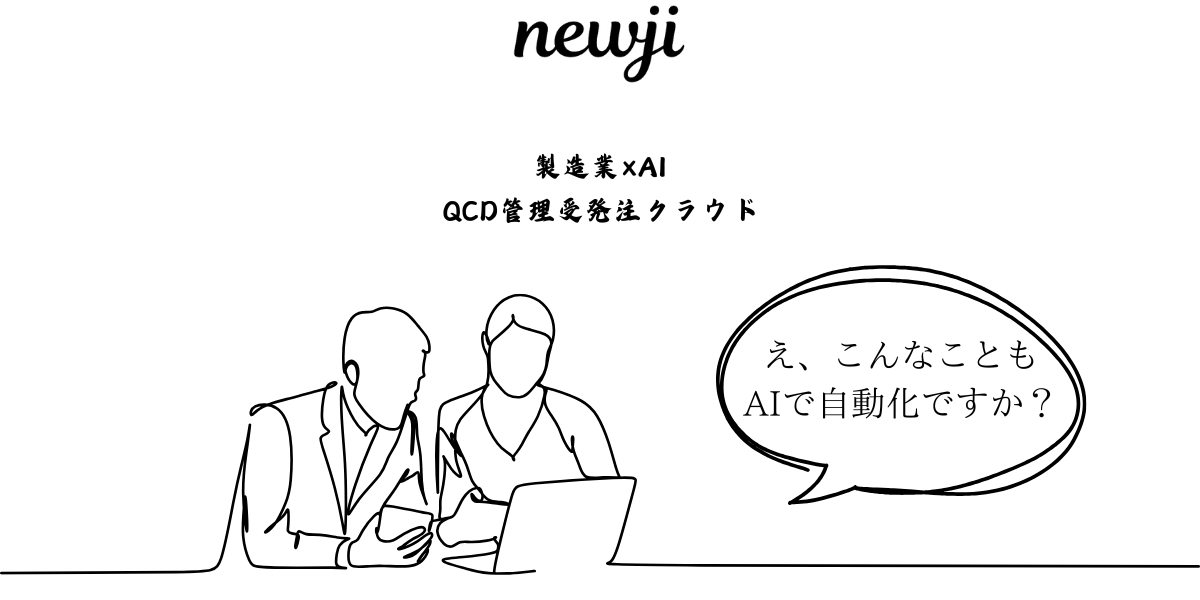
Troubleshooting in Extrusion Molding: Common Problems and Solutions
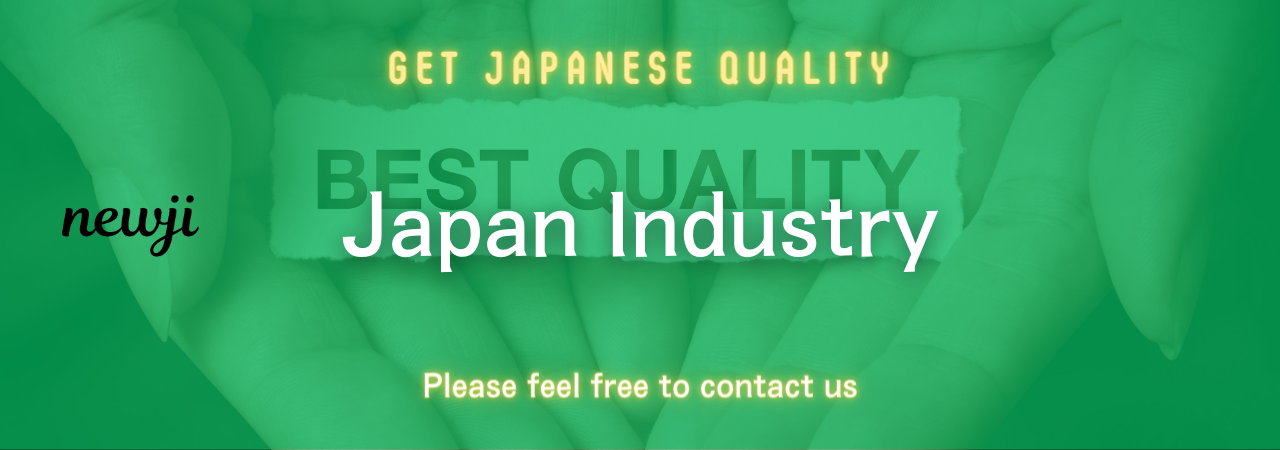
Extrusion molding is a widely utilized manufacturing process used to create a vast array of plastic products. It is a versatile technique that involves forcing molten plastic through a shaped die, ensuring continuous production of items like pipes, sheets, and profiles.
Despite its efficiency, extrusion molding is not without its challenges. Various issues can arise during the process, leading to defects in the final product. Understanding these common problems and their solutions is crucial for maintaining product quality and minimizing downtime.
目次
Introduction to Extrusion Molding
Extrusion molding is a process where raw plastic material is melted and formed into a continuous shape. The process starts with plastic pellets or powders being fed into an extruder. These materials are then heated to a molten state and pushed through a die to form the desired shape. The continuous plastic extrusion is then cooled and cut to length.
This method is known for its ability to produce large volumes of uniform products efficiently. However, like any manufacturing process, it comes with its own set of potential issues that must be addressed to ensure smooth operation and high-quality outputs.
Common Problems in Extrusion Molding
Several problems can occur during the extrusion molding process. Identifying these issues early and understanding their root causes are essential for swift resolution.
1. Melt Fracture
Melt fracture is a surface defect characterized by irregularities or distortions in the extruded material. It gives the product a rough or cracked appearance.
Causes:
– Excessive shear stress
– High extrusion speeds
– Inconsistent material flow
Solutions:
– Reduce the extruder speed to minimize shear
– Use a die with a smoother transition zone
– Ensure consistent material temperature and flow
2. Die Lines
Die lines are longitudinal lines or ridges on the extruded product’s surface. These can affect the appearance and performance of the product.
Causes:
– Contaminants in the raw material
– Damaged or worn-out die
– Uneven die temperature
Solutions:
– Clean the die and remove any contaminants
– Replace or repair the damaged die
– Ensure even heating across the die
3. Bubbles and Voids
Bubbles or voids within the extruded material can compromise its structural integrity. These defects often result from trapped air or gases.
Causes:
– Poor material feeding techniques
– Excessive moisture content in the raw material
– High extrusion temperatures
Solutions:
– Improve material feeding to reduce air entrapment
– Dry the raw material thoroughly before extrusion
– Lower the extrusion temperature
4. Sharkskin
Sharkskin is another surface defect where the extruded product has a rough, wavy appearance. This can affect both the aesthetic quality and performance.
Causes:
– High shear rates at the die exit
– Inadequate lubrication of the die
– Non-uniform material temperature
Solutions:
– Decrease the extruder speed to reduce shear rates
– Apply adequate lubrication at the die exit
– Ensure consistent material temperature throughout the process
5. Dimensional Inconsistencies
Dimensional inconsistencies refer to variations in the size and shape of the extruded products. These defects can lead to products that do not meet specified tolerances.
Causes:
– Fluctuating extrusion temperatures
– Inconsistent material feed rates
– Irregular die gap settings
Solutions:
– Maintain a consistent extrusion temperature
– Ensure a steady material feed rate
– Regularly inspect and adjust die gap settings
Preventative Measures and Best Practices
Maintaining high-quality extrusion output requires more than just troubleshooting problems as they arise. Implementing preventative measures and adhering to best practices can significantly reduce the occurrence of defects.
1. Regular Maintenance
Routine maintenance of extrusion equipment is crucial. Regularly inspect the extruder, die, and associated equipment for wear and tear, and address any issues promptly. This helps in maintaining consistent performance and reducing the risk of unexpected downtime.
2. Quality Raw Materials
The quality of raw materials directly impacts the final product. Ensure that only high-quality, contamination-free materials are used in the extrusion process. Additionally, properly drying the materials before use can prevent moisture-related defects.
3. Process Control and Monitoring
Implement robust process control and monitoring systems. Continuously track key variables such as temperature, pressure, and feed rates. Real-time monitoring allows for quick adjustments and helps maintain a stable extrusion process.
4. Operator Training
Well-trained operators are essential for efficient extrusion molding. Ensure that all operators are adequately trained in both machine operation and troubleshooting techniques. Regular training sessions can keep the team updated on best practices and new technologies.
5. Proper Die Design and Maintenance
The die plays a critical role in the extrusion process. Ensure that the die is designed for the specific material and application. Regularly clean and maintain the die to prevent contamination and wear, which can lead to surface defects and dimensional inconsistencies.
Conclusion
Extrusion molding is a sophisticated process with the potential for various issues. However, understanding common problems and their solutions can significantly enhance the efficiency and quality of production.
By addressing issues such as melt fracture, die lines, bubbles and voids, sharkskin, and dimensional inconsistencies with targeted strategies, manufacturers can ensure smoother operations. Additionally, incorporating preventative measures like regular maintenance, using high-quality raw materials, implementing process control, and providing operator training can help preemptively mitigate potential problems.
Implementing these best practices and solutions can help manufacturers produce high-quality extruded products consistently, enhancing both efficiency and customer satisfaction.
資料ダウンロード
QCD管理受発注クラウド「newji」は、受発注部門で必要なQCD管理全てを備えた、現場特化型兼クラウド型の今世紀最高の受発注管理システムとなります。
ユーザー登録
受発注業務の効率化だけでなく、システムを導入することで、コスト削減や製品・資材のステータス可視化のほか、属人化していた受発注情報の共有化による内部不正防止や統制にも役立ちます。
NEWJI DX
製造業に特化したデジタルトランスフォーメーション(DX)の実現を目指す請負開発型のコンサルティングサービスです。AI、iPaaS、および先端の技術を駆使して、製造プロセスの効率化、業務効率化、チームワーク強化、コスト削減、品質向上を実現します。このサービスは、製造業の課題を深く理解し、それに対する最適なデジタルソリューションを提供することで、企業が持続的な成長とイノベーションを達成できるようサポートします。
製造業ニュース解説
製造業、主に購買・調達部門にお勤めの方々に向けた情報を配信しております。
新任の方やベテランの方、管理職を対象とした幅広いコンテンツをご用意しております。
お問い合わせ
コストダウンが利益に直結する術だと理解していても、なかなか前に進めることができない状況。そんな時は、newjiのコストダウン自動化機能で大きく利益貢献しよう!
(β版非公開)