- お役立ち記事
- Troubleshooting Shot Size and Tips for Improving Quality
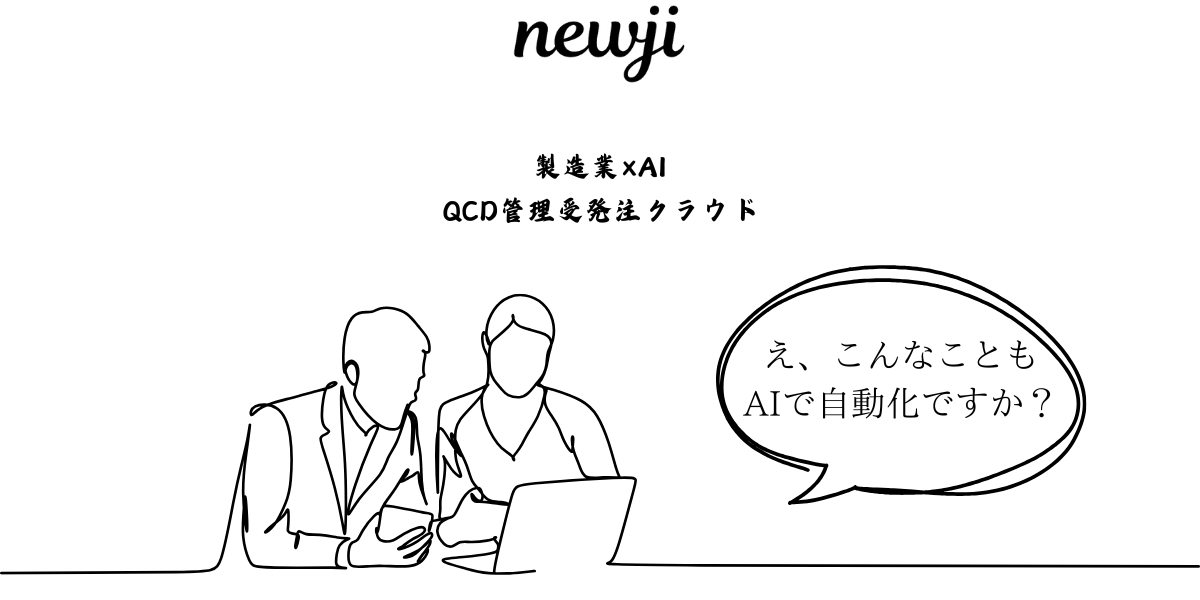
Troubleshooting Shot Size and Tips for Improving Quality
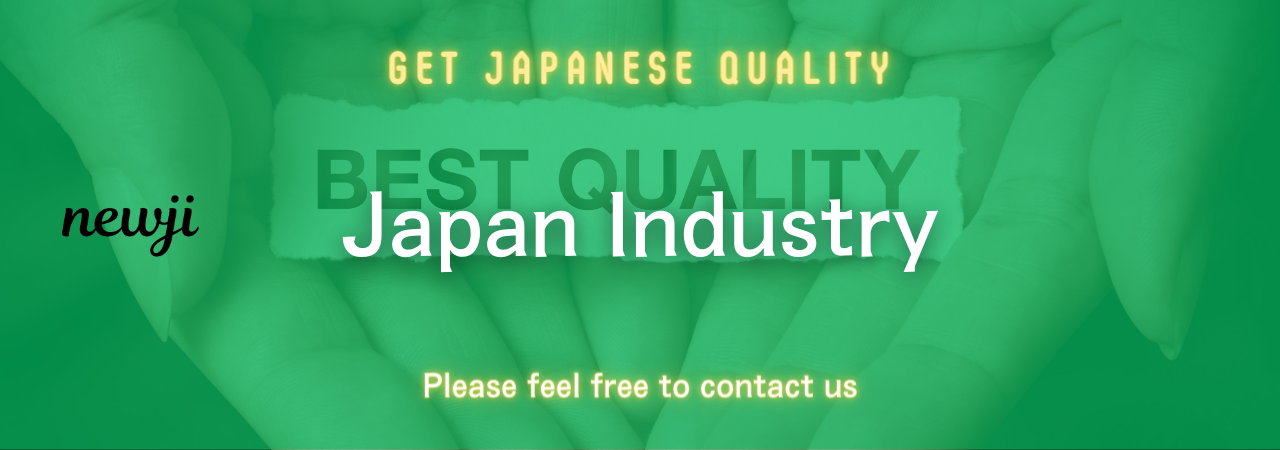
目次
Understanding Shot Size in Manufacturing
In the world of manufacturing, particularly within injection molding, the term “shot size” refers to the amount of material injected into the mold to create a part.
This process is crucial across industries, from automotive to consumer goods, because it directly impacts the quality and precision of the final product.
If the shot size isn’t properly calibrated, it can lead to a cascade of issues that affect both the aesthetics and functionality of molded parts.
Common Issues Associated with Shot Size
Problems related to shot size can range from being minor nuisances to significant defects that compromise a product’s reliability.
Common symptoms of improper shot size include flash, incomplete filling, sink marks, and warping.
These defects not only degrade the physical appearance of a product but also can affect its structural integrity and performance.
Flash occurs when excessive material overflows from the mold cavity, creating thin, unwanted pieces.
This happens if the shot size is too large.
Conversely, incomplete filling occurs if there isn’t enough material, leading to voids or parts with missing elements.
Sink marks and warping affect the surface and dimensional stability, often resulting from an imbalance in the shot size and cooling times.
Identifying the Root Causes
Before fine-tuning a shot size, it’s vital to identify the root causes of issues.
Several factors can influence the correct shot size, and understanding them can help manufacturers rectify and prevent defects.
One major factor is the precision of the machinery.
Older or poorly maintained machines may not inject materials consistently, leading to variations in shot size.
Material properties, such as viscosity or temperature sensitivity, can also play a pivotal role.
Materials like thermoplastics behave differently under varying conditions, affecting the flow and final volume in the mold.
Additionally, the design of the mold itself is crucial.
A complex or poorly designed mold may necessitate adjustments in shot size to achieve the desired results.
Close collaboration between product designers and manufacturing engineers often helps in creating molds that can be accommodated by the production equipment’s capabilities.
Optimizing Shot Size for Better Quality
Effective troubleshooting and optimization of shot size require systematic approaches and the application of both experience and technology.
Here are some tips for improving the shot size process:
1. **Regular Machine Maintenance**: Ensure all equipment is routinely inspected and maintained.
Check for signs of wear and tear, and replace components when necessary to maintain precision.
2. **Material Testing and Selection**: Conduct thorough tests of materials before batch production.
Understand how different materials behave under varying temperatures and pressures to fine-tune shot sizes accordingly.
3. **Utilize Simulation Software**: Advanced simulation programs can model the injection molding process, predicting potential issues related to shot size.
These simulations enable engineers to adjust parameters and optimize the shot size even before starting production.
4. **Documenting and Analyzing Data**: Keep detailed records of production runs, including shot sizes, defects encountered, and any adjustments made.
Analyzing this data can reveal patterns and provide insights for future projects.
5. **Training and Skill Development**: Ensure that operators and engineers are trained and updated on the best practices and latest technologies.
Skilled personnel can adeptly handle unexpected issues and make necessary adjustments on the fly.
Implementing Continuous Improvement Strategies
Improving shot size management isn’t a one-time activity.
It requires a commitment to continuous improvement, leveraging the strategies outlined above while being open to new methods and technologies.
Implementing a robust quality assurance system aligns team efforts towards detecting issues early in the production process.
Empowering teams to contribute suggestions and making incremental changes can lead to significant long-term improvements.
With technological advancements, techniques such as machine learning and IoT (Internet of Things) can be integrated into the process.
These technologies provide real-time data and predictive analyses, allowing manufacturers to foresee potential issues and adjust shot sizes dynamically.
The Impact on Quality and Efficiency
By mastering shot size optimization, manufacturers can enhance both quality and efficiency.
Properly calibrated shot sizes result in parts with better precision, reduced wastage of materials, and lower rates of defects.
This leads to improved customer satisfaction as the final products meet or exceed quality expectations.
Additionally, the efficient use of materials and reduction of defects translate into cost savings.
This makes the production process not only more sustainable but also economically viable.
Conclusion
The journey to perfecting shot size is a blend of art and science, requiring attention to detail, technical knowledge, and experience.
By focusing on the root causes, implementing effective strategies, and continually improving processes, manufacturers can achieve high-quality products with consistent results.
Tackling shot size challenges proactively not only enhances product quality but also strengthens the overall manufacturing process.
In the competitive landscape of modern manufacturing, such quality-centric approaches can be the key differentiator.
資料ダウンロード
QCD調達購買管理クラウド「newji」は、調達購買部門で必要なQCD管理全てを備えた、現場特化型兼クラウド型の今世紀最高の購買管理システムとなります。
ユーザー登録
調達購買業務の効率化だけでなく、システムを導入することで、コスト削減や製品・資材のステータス可視化のほか、属人化していた購買情報の共有化による内部不正防止や統制にも役立ちます。
NEWJI DX
製造業に特化したデジタルトランスフォーメーション(DX)の実現を目指す請負開発型のコンサルティングサービスです。AI、iPaaS、および先端の技術を駆使して、製造プロセスの効率化、業務効率化、チームワーク強化、コスト削減、品質向上を実現します。このサービスは、製造業の課題を深く理解し、それに対する最適なデジタルソリューションを提供することで、企業が持続的な成長とイノベーションを達成できるようサポートします。
オンライン講座
製造業、主に購買・調達部門にお勤めの方々に向けた情報を配信しております。
新任の方やベテランの方、管理職を対象とした幅広いコンテンツをご用意しております。
お問い合わせ
コストダウンが利益に直結する術だと理解していても、なかなか前に進めることができない状況。そんな時は、newjiのコストダウン自動化機能で大きく利益貢献しよう!
(Β版非公開)