- お役立ち記事
- Troubleshooting techniques for high-precision measuring instruments and their applications in the manufacturing market
月間77,185名の
製造業ご担当者様が閲覧しています*
*2025年2月28日現在のGoogle Analyticsのデータより
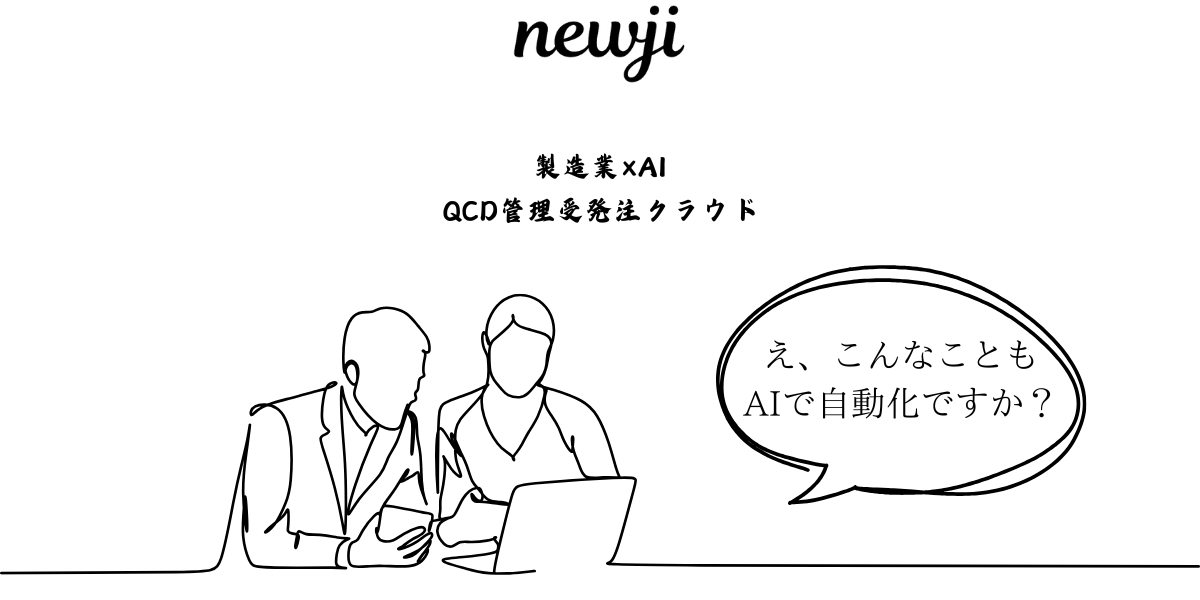
Troubleshooting techniques for high-precision measuring instruments and their applications in the manufacturing market
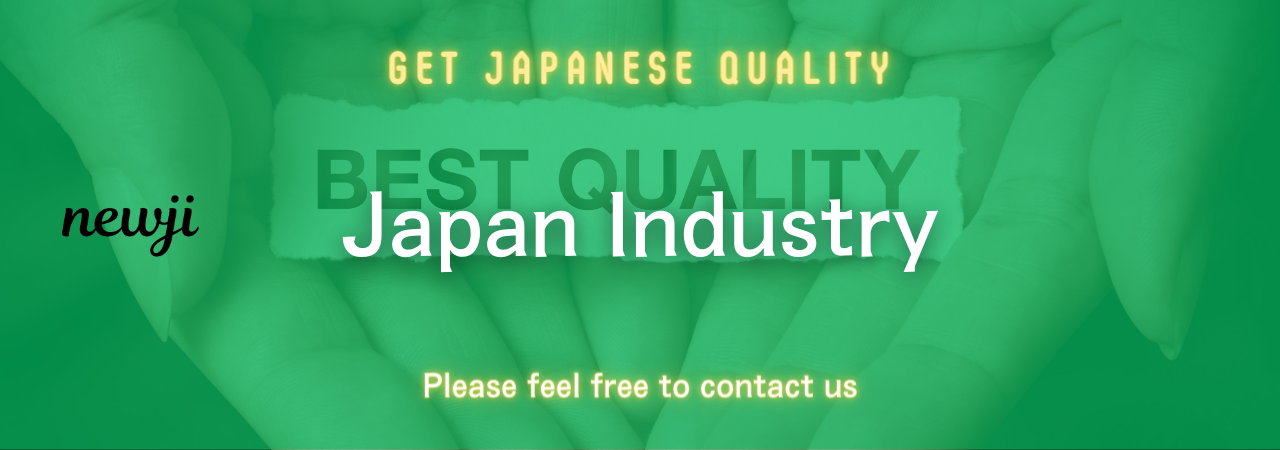
目次
Understanding High-Precision Measuring Instruments
High-precision measuring instruments are essential tools in the manufacturing industry.
These devices ensure that products are made to exact specifications and that quality control standards are maintained.
Such instruments include micrometers, calipers, optical comparators, and coordinate measuring machines, among others.
They are used to measure dimensions, weights, lengths, and other critical parameters with high accuracy.
The Importance of Accuracy in Manufacturing
In the manufacturing market, the importance of accuracy cannot be overstated.
Products that do not meet quality specifications can result in wasted materials, additional costs, and dissatisfied customers.
This is where high-precision measuring instruments come into play.
They provide the data needed to verify that each component is made correctly, ensuring that the final product meets all standards.
Common Issues with Measuring Instruments
Even the most precise measurement tools can encounter issues that affect their accuracy.
Understanding these common issues is the first step in troubleshooting.
Calibration Problems
Calibration is a critical factor in ensuring the accuracy of measuring instruments.
Over time, instruments can drift from their calibrated settings, resulting in inaccurate measurements.
Regular recalibration is necessary to maintain precision.
Manufacturers should establish a routine calibration schedule based on the instrument’s usage and the manufacturer’s recommendations.
Environmental Factors
Environmental conditions can significantly impact the accuracy of measuring instruments.
Factors such as temperature, humidity, and vibrations can cause measurement errors.
To minimize these effects, it is important to operate instruments in a controlled environment.
This might involve stabilizing temperature and humidity levels or isolating equipment from sources of vibration.
Wear and Tear
Regular usage of measuring instruments can lead to mechanical wear and tear.
Parts such as scales, gears, and bearings can degrade over time, leading to diminished accuracy.
Routine maintenance and timely replacement of worn components are crucial to preserving the instrument’s precision.
Troubleshooting Techniques
Effective troubleshooting of high-precision measuring instruments involves a systematic approach to identify and resolve issues.
Visual Inspection
Start with a thorough visual inspection of the instrument.
Look for signs of physical damage, wear, and dirt build-up, especially on sensors and critical measuring components.
Clean the instrument gently using manufacturer-recommended materials.
Check Calibration
Verify the instrument’s calibration status.
Use a known reference standard to test the instrument’s accuracy.
If deviations are found, recalibrate the device according to the manufacturer’s guidelines.
Assess the Environment
Evaluate the environment in which the instrument is used.
Ensure that the temperature and humidity levels are within the acceptable range specified by the manufacturer.
Relocate or protect the instrument from sources of vibration if necessary.
Consult the Manual
Refer to the instrument’s manual for troubleshooting advice.
Manufacturers often provide instructions for diagnosing common problems and performing basic repairs.
Following these guidelines can prevent more significant issues from developing.
Applications in the Manufacturing Market
High-precision measuring instruments are used across various manufacturing sectors, playing a crucial role in quality control and product development.
Automotive Industry
In the automotive industry, these instruments are essential for ensuring that parts fit together correctly and meet safety standards.
They are used in the production of engines, transmission systems, and other critical components to ensure precision and performance.
Aerospace Manufacturing
Aerospace manufacturers rely on high-precision measuring tools to meet stringent safety and performance standards.
Every component, from turbine blades to fuselage parts, is measured to exact specifications to ensure proper function.
Electronics Manufacturing
The electronics sector demands high precision due to the small size and complexity of components.
Measuring instruments ensure that circuit boards, connectors, and microchips meet industry regulations and performance criteria.
Advancements in Measurement Technology
Innovations in measurement technology continue to enhance the capability and accuracy of these instruments, supporting the manufacturing industry’s ongoing growth and development.
Digital Innovations
Modern measuring tools increasingly incorporate digital technology, improving ease of use and data integration.
Digital micrometers and calipers provide instant readings, reducing human error and enhancing efficiency.
Automation and Integration
The integration of measuring instruments with automated manufacturing systems allows for real-time quality control.
Such integration increases production efficiency and facilitates the collection of data for analysis and improvement.
Nanotechnology
Advancements in nanotechnology have led to the development of instruments capable of measuring at microscopic levels.
These innovations support industries that require extremely high precision, such as semiconductor manufacturing.
Conclusion
High-precision measuring instruments are indispensable in the manufacturing industry, ensuring that products meet the highest quality standards.
Understanding common issues, employing effective troubleshooting techniques, and embracing technological advancements enhance their reliability and utility.
As the demand for precision grows, these instruments will continue to be vital tools for manufacturers aiming for excellence in their products.
資料ダウンロード
QCD管理受発注クラウド「newji」は、受発注部門で必要なQCD管理全てを備えた、現場特化型兼クラウド型の今世紀最高の受発注管理システムとなります。
ユーザー登録
受発注業務の効率化だけでなく、システムを導入することで、コスト削減や製品・資材のステータス可視化のほか、属人化していた受発注情報の共有化による内部不正防止や統制にも役立ちます。
NEWJI DX
製造業に特化したデジタルトランスフォーメーション(DX)の実現を目指す請負開発型のコンサルティングサービスです。AI、iPaaS、および先端の技術を駆使して、製造プロセスの効率化、業務効率化、チームワーク強化、コスト削減、品質向上を実現します。このサービスは、製造業の課題を深く理解し、それに対する最適なデジタルソリューションを提供することで、企業が持続的な成長とイノベーションを達成できるようサポートします。
製造業ニュース解説
製造業、主に購買・調達部門にお勤めの方々に向けた情報を配信しております。
新任の方やベテランの方、管理職を対象とした幅広いコンテンツをご用意しております。
お問い合わせ
コストダウンが利益に直結する術だと理解していても、なかなか前に進めることができない状況。そんな時は、newjiのコストダウン自動化機能で大きく利益貢献しよう!
(β版非公開)