- お役立ち記事
- Troubleshooting Weld Lines and Strategies to Prevent Molding Defects
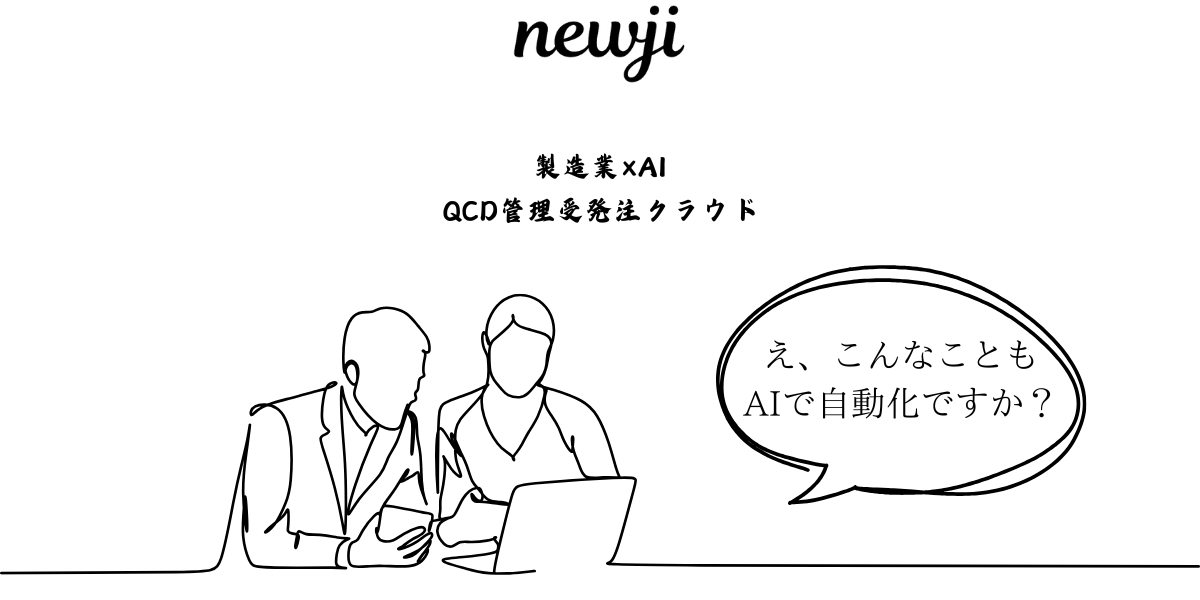
Troubleshooting Weld Lines and Strategies to Prevent Molding Defects
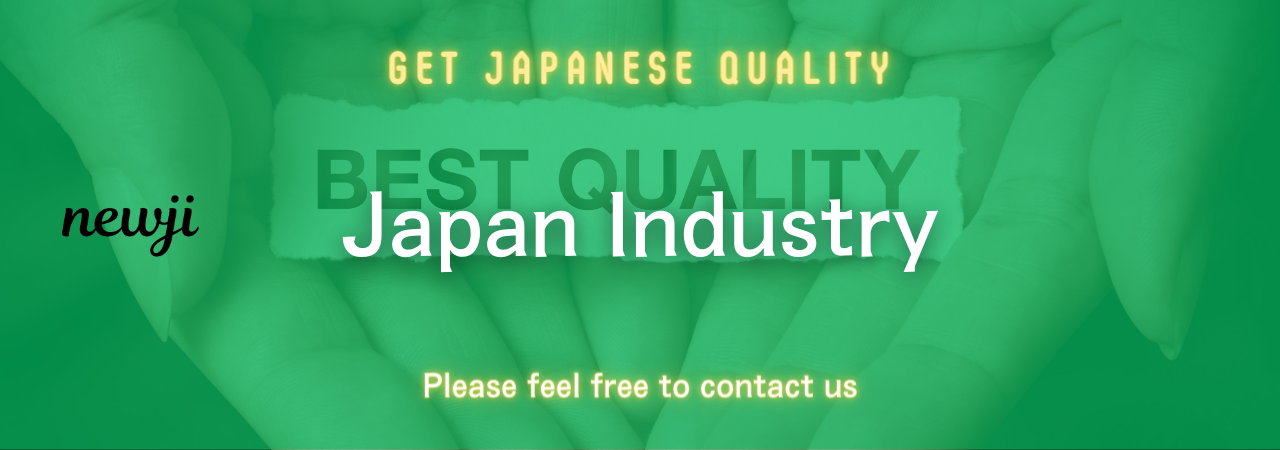
目次
Understanding Weld Lines
Weld lines, sometimes referred to as knit lines, are a common defect in the injection molding process.
They appear wherever two or more flow fronts of molten plastic meet, resulting in a lighter line or area that can compromise the strength and appearance of a part.
These lines can appear in any molded part, but they are most visible in parts with high gloss finishes or translucent materials.
Weld lines occur because molten plastic cools down as it moves through the mold.
When separate fronts of this cooling plastic come together, they may not bond perfectly, leaving a visible line.
This defect can frequently be seen in parts with holes or multiple gates, as these features can split the flow of plastic, resulting in more than one flow front.
A perfect understanding of weld lines is crucial for both designers and engineers, as the defect can lead to weakened product integrity, unsatisfactory aesthetics, and increased production costs.
By comprehending how weld lines are formed and knowing the strategies to manage them, manufacturers can enhance product quality and customer satisfaction.
Causes of Weld Lines
There are various factors that contribute to the formation of weld lines.
One primary cause is improper flow of the molten material due to inadequate mold design or poor gating.
If the mold design does not facilitate uniform flow, the plastic will cool unevenly, causing weld lines to form where the different flow fronts meet.
Material temperature also plays a pivotal role in the formation of weld lines.
If the molten material is not at the right temperature, it solidifies too soon at the point of convergence, leading to lines.
Conversely, if the material is too hot, it can degrade, resulting in poor bonding.
Additionally, the speed at which the material is injected can cause this defect.
Slow injection speeds mean that the fluid plastic spends more time in the mold, leading to premature cooling.
Extreme temperatures during the injection process, whether too hot or too cold, can also impact the flow and bonding quality, leading to the infamous weld lines.
Identifying Weld Lines
Identifying weld lines requires a keen eye and a thorough inspection process.
Visual inspection is often enough to spot noticeable lines, especially in high-gloss or transparent parts.
These lines are typically weaker and can be a starting point for part fractures under stress or pressure.
Non-destructive testing techniques, such as ultrasonics or X-ray imaging, are also useful for identifying weld lines, particularly in critical applications.
For a more qualitative analysis, tensile strength tests can also be carried out.
Should the part fail along a weld line, it indicates poor bonding at that specific junction.
Strategies to Prevent Weld Lines
The key to preventing weld lines is optimizing the component design, mold structure, and processing conditions.
Optimize Mold Design
A well-thought-out mold design can greatly reduce weld line formation.
Ensuring that the gates are located appropriately can improve the flow of the material and reduce the number of flow fronts that can cause weld lines.
Additionally, placing gates in areas of the part that are less significant in terms of structural and aesthetic value can help minimize the impact of weld lines.
Proper cooling channels in molds are also essential.
These channels should facilitate even temperature distribution throughout the part, thereby avoiding premature solidification that can contribute to weld line formation.
Adjust Material and Injection Parameters
Choosing the right material with suitable flow properties can minimize weld line issues.
Materials that flow more smoothly and uniformly are less likely to form weld lines.
Additionally, pre-drying of materials that are sensitive to moisture can prevent degradation during the injection process, reducing defects.
Optimal injection speed and pressure are critical.
Adjusting these parameters can ensure that the material fills the mold before it cools, reducing the likelihood of weld line formation.
This means finding a balance between too fast (which can create turbulence and air entrapment) and too slow (leading to premature solidification).
Use of Processing Aids
Processing aids, such as flow enhancers, can also help prevent or reduce weld lines.
These additives improve the flow characteristics of the plastic material, facilitating better filling and fusion at the convergence points.
Furthermore, in some cases, post-molding processes like annealing can help in improving the bond strength at weld lines, thus enhancing the part’s aesthetic and structural integrity.
Conclusion
Weld lines, while a common issue in injection molding, can be effectively managed with a combination of informed design choices, accurate processing settings, and strategic material selection.
By understanding the nuances of how these lines form and implementing prevention strategies, manufacturers can ensure the production of high-quality, visually appealing, and structurally sound products.
Investing time and energy into preventing weld lines not only enhances end-product appearance and durability but also optimizes overall manufacturing efficiency, ultimately leading to cost savings and improved customer satisfaction. Knowledge and proactive measures are the best tools to combat this prevalent defect in the world of injection molding.
資料ダウンロード
QCD調達購買管理クラウド「newji」は、調達購買部門で必要なQCD管理全てを備えた、現場特化型兼クラウド型の今世紀最高の購買管理システムとなります。
ユーザー登録
調達購買業務の効率化だけでなく、システムを導入することで、コスト削減や製品・資材のステータス可視化のほか、属人化していた購買情報の共有化による内部不正防止や統制にも役立ちます。
NEWJI DX
製造業に特化したデジタルトランスフォーメーション(DX)の実現を目指す請負開発型のコンサルティングサービスです。AI、iPaaS、および先端の技術を駆使して、製造プロセスの効率化、業務効率化、チームワーク強化、コスト削減、品質向上を実現します。このサービスは、製造業の課題を深く理解し、それに対する最適なデジタルソリューションを提供することで、企業が持続的な成長とイノベーションを達成できるようサポートします。
オンライン講座
製造業、主に購買・調達部門にお勤めの方々に向けた情報を配信しております。
新任の方やベテランの方、管理職を対象とした幅広いコンテンツをご用意しております。
お問い合わせ
コストダウンが利益に直結する術だと理解していても、なかなか前に進めることができない状況。そんな時は、newjiのコストダウン自動化機能で大きく利益貢献しよう!
(Β版非公開)