- お役立ち記事
- Trunk Hinge Manufacturing Process and Durability Strengthening
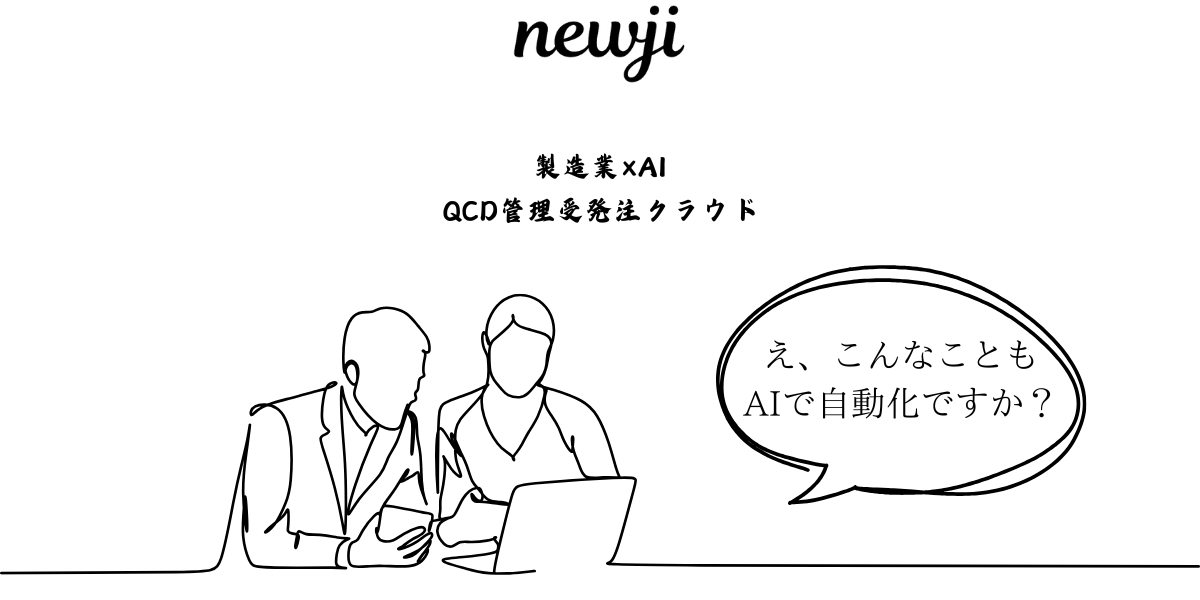
Trunk Hinge Manufacturing Process and Durability Strengthening
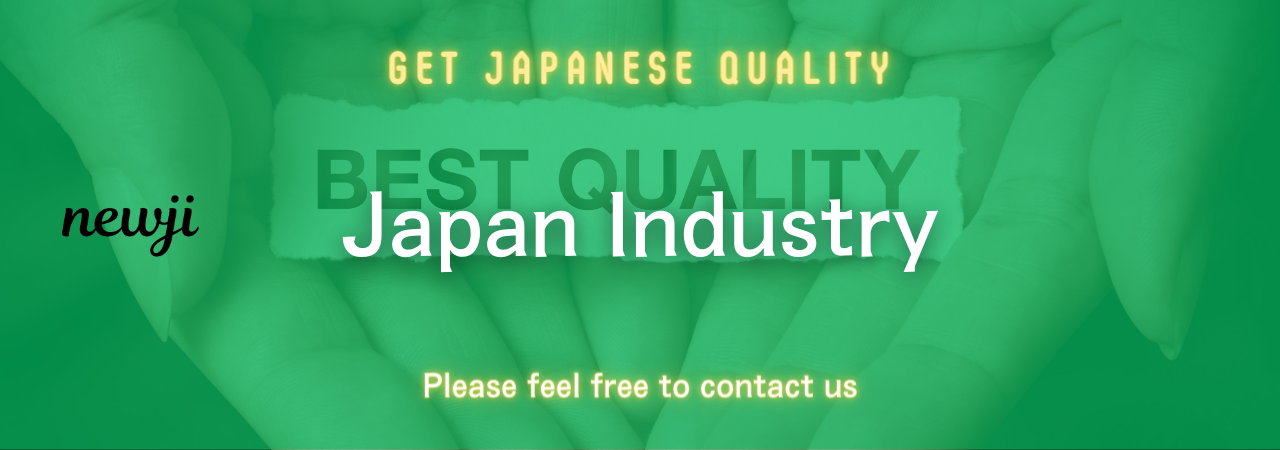
目次
Introduction to Trunk Hinges
Trunk hinges are crucial components in vehicles.
They allow the trunk to open and close smoothly.
Understanding their manufacturing process and methods to enhance their durability is important for maintaining vehicle quality.
In this article, we explore how trunk hinges are made and how manufacturers ensure they are strong and long-lasting.
Materials Used in Trunk Hinges
To begin with, let’s discuss the materials.
Trunk hinges are typically made from metals like steel and aluminum.
Steel is strong and durable, making it a popular choice.
Aluminum, on the other hand, is lightweight and resistant to corrosion.
Both materials offer benefits, and the choice often depends on the specific requirements of the vehicle.
Steel Hinges
Steel hinges are known for their strength.
They can withstand significant amounts of stress and strain.
This makes them ideal for heavy-duty vehicles and larger trunks.
However, steel is prone to rust, so it requires special treatments to enhance its durability.
Aluminum Hinges
Aluminum hinges are lighter, which can improve fuel efficiency in vehicles.
They are also highly resistant to rust.
However, aluminum is not as strong as steel, so it might not be suitable for all vehicle types.
Manufacturers often use specific alloys to enhance aluminum’s strength.
The Manufacturing Process
The manufacturing process of trunk hinges involves several steps.
Each step is crucial to ensure the final product meets quality standards.
Let’s break down the process:
Step 1: Design and Prototyping
The first step is to design the hinge.
Engineers use computer-aided design (CAD) software to create detailed designs.
These designs help in visualizing the final product and identifying any potential issues.
Once the design is approved, a prototype is created.
This prototype undergoes various tests to ensure it meets all specifications.
Step 2: Material Selection and Cutting
After the design is finalized, the appropriate material is selected.
The material is then cut into precise shapes and sizes using advanced cutting machines.
This step requires high precision to ensure each part fits perfectly.
Step 3: Forming and Shaping
Next, the cut material is formed into the desired shape.
This process may involve bending, stamping, and machining.
Specialized tools and machines are used to achieve the perfect shape and size.
This step ensures the hinge will function smoothly.
Step 4: Assembly
Once the parts are shaped, they are assembled.
This involves attaching various components like pins, bushings, and springs.
The assembly process must be precise to ensure the hinge functions correctly.
Automated machines and skilled workers work together to achieve this precision.
Step 5: Surface Treatment
To enhance durability, the surface of the hinge is treated.
This may involve processes like galvanization, painting, or coating.
These treatments protect the hinge from rust and wear, ensuring it lasts longer.
Step 6: Quality Testing
The final step is quality testing.
Each hinge undergoes rigorous tests to ensure it meets industry standards.
This includes stress tests, corrosion tests, and functional tests.
Only hinges that pass these tests are approved for use in vehicles.
Improving Trunk Hinge Durability
Manufacturers implement several strategies to enhance the durability of trunk hinges.
Let’s explore these strategies:
Use of High-Quality Materials
One of the primary ways to enhance durability is by using high-quality materials.
Advanced steel and aluminum alloys offer better strength and resistance to wear.
These materials are more expensive but greatly enhance the lifespan of the hinge.
Advanced Surface Treatments
Applying advanced surface treatments can significantly improve durability.
For example, galvanized coatings protect steel from rust.
Similarly, anodizing aluminum increases its resistance to corrosion.
Regular Maintenance
Regular maintenance also plays a crucial role.
Lubricating the hinges periodically ensures smooth operation and reduces wear.
Inspecting the hinges for signs of damage can help in timely repairs, preventing major failures.
Finite Element Analysis
Finite Element Analysis (FEA) is a modern technique used in the design phase.
It helps in simulating how the hinge will perform under various conditions.
This allows engineers to identify and address potential weak points, enhancing durability.
Innovations in Trunk Hinge Manufacturing
The automotive industry is constantly evolving, and so is trunk hinge manufacturing.
Let’s look at some innovations:
3D Printing
3D printing technology is revolutionizing manufacturing.
It allows for rapid prototyping and the creation of complex designs.
3D-printed hinges can be lightweight yet strong, offering new possibilities in hinge design.
Smart Materials
Smart materials can change their properties in response to environmental conditions.
For instance, shape-memory alloys can return to their original shape after bending.
These materials can be used to create self-healing hinges that are more durable.
Robotic Assembly
Robotic assembly improves precision and efficiency.
Robots can assemble hinges with high accuracy, reducing the chances of defects.
This leads to higher-quality hinges that perform better and last longer.
Conclusion
Trunk hinges are essential components in vehicles, and their manufacturing process is complex.
From material selection to quality testing, each step is crucial to ensure the final product is durable and reliable.
By using high-quality materials, advanced surface treatments, and innovative technologies, manufacturers can produce hinges that stand the test of time.
As the automotive industry continues to evolve, we can expect even more advancements in trunk hinge manufacturing, leading to better-performing vehicles.
資料ダウンロード
QCD調達購買管理クラウド「newji」は、調達購買部門で必要なQCD管理全てを備えた、現場特化型兼クラウド型の今世紀最高の購買管理システムとなります。
ユーザー登録
調達購買業務の効率化だけでなく、システムを導入することで、コスト削減や製品・資材のステータス可視化のほか、属人化していた購買情報の共有化による内部不正防止や統制にも役立ちます。
NEWJI DX
製造業に特化したデジタルトランスフォーメーション(DX)の実現を目指す請負開発型のコンサルティングサービスです。AI、iPaaS、および先端の技術を駆使して、製造プロセスの効率化、業務効率化、チームワーク強化、コスト削減、品質向上を実現します。このサービスは、製造業の課題を深く理解し、それに対する最適なデジタルソリューションを提供することで、企業が持続的な成長とイノベーションを達成できるようサポートします。
オンライン講座
製造業、主に購買・調達部門にお勤めの方々に向けた情報を配信しております。
新任の方やベテランの方、管理職を対象とした幅広いコンテンツをご用意しております。
お問い合わせ
コストダウンが利益に直結する術だと理解していても、なかなか前に進めることができない状況。そんな時は、newjiのコストダウン自動化機能で大きく利益貢献しよう!
(Β版非公開)