- お役立ち記事
- Type and selection of optimal mechanical seals according to operating conditions
月間76,176名の
製造業ご担当者様が閲覧しています*
*2025年3月31日現在のGoogle Analyticsのデータより
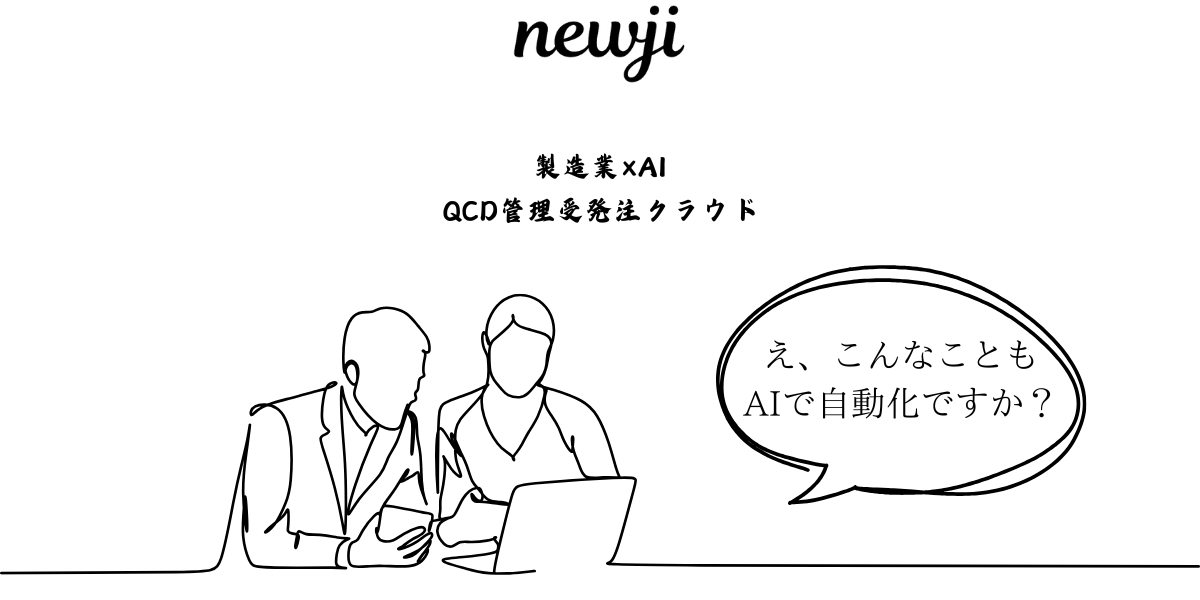
Type and selection of optimal mechanical seals according to operating conditions
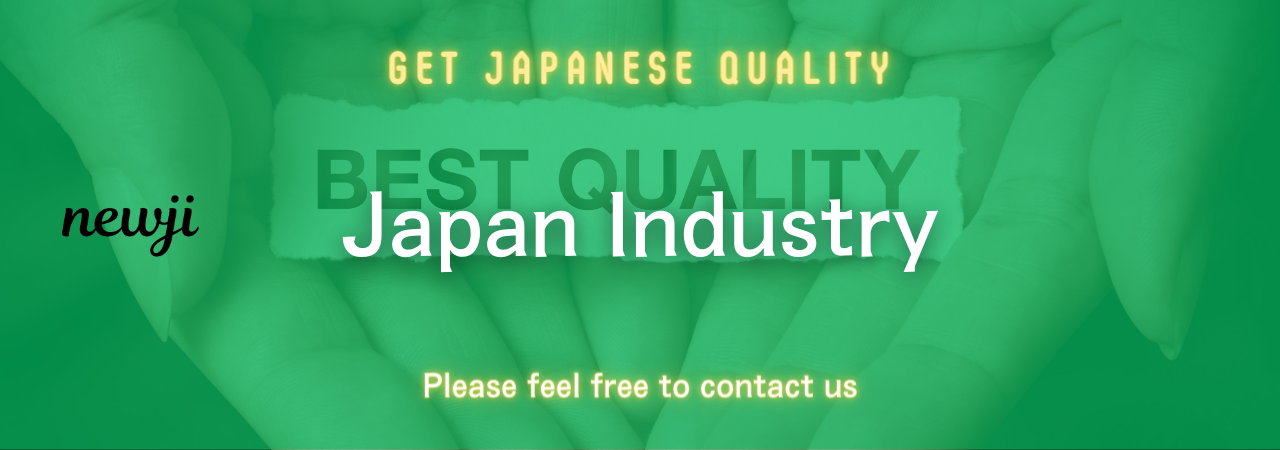
目次
Understanding Mechanical Seals
Mechanical seals play a critical role in various industrial applications by preventing leaks between rotating and stationary parts of machines.
These seals are incredibly important in industries such as oil and gas, chemical processing, water treatment, and many others where maintaining the integrity of a system is crucial.
Mechanical seals are designed to prevent leakage through carefully engineered surfaces that provide a tight seal.
By selecting the correct mechanical seal, you can help ensure that machinery operates efficiently and safely.
Types of Mechanical Seals
There are several types of mechanical seals, each designed for specific applications and operating conditions.
Understanding these different types is essential for choosing the right seal for your needs.
Pusher Seals
Pusher seals use a secondary seal ring that moves axially along the shaft to accommodate seal face wear and axial movement of the equipment.
These seals are commonly used in applications with moderate to high pressure and speed because they are versatile and effective.
Non-Pusher Seals
Non-pusher seals, also known as bellows seals, are designed without secondary rings.
Instead, they have a flexible bellows component that can absorb axial movement.
These seals are suitable for high-temperature applications since they eliminate the concerns associated with using elastomer seals that might degrade over time.
Cartridge Seals
Cartridge seals come ready to install as a unit.
This setup reduces the time needed for installation and the chance of installation errors.
Cartridge seals are highly popular because they require less maintenance and ensure reliable performance in demanding conditions.
Dry-Running Seals
Dry-running seals are engineered to operate without the need for a liquid barrier or lubrication.
These seals are often used in applications handling dry or gaseous media where lubrication is not possible.
They are also beneficial where contamination from fluids should be avoided.
Balanced and Unbalanced Seals
Balanced seals are designed to reduce the pressure exerted on the seal faces, which decreases wear and extends the life of the seal.
These are ideal for high-pressure applications.
Unbalanced seals are used in low to moderate pressure settings; they are simpler and more economical compared to balanced seals.
Selecting the Optimal Mechanical Seal
Selecting the right mechanical seal requires understanding and considering several key factors of your operating conditions.
Each factor will influence the type of mechanical seal needed for reliable and efficient operation.
Operating Pressure
The operating pressure of your system is one of the first things to consider when selecting a mechanical seal.
Higher-pressure systems will typically require balanced seals due to their ability to handle pressure effectively without excessive wear.
Operating Temperature
Temperature is another critical factor as it affects the materials that can be used for the mechanical seal.
Non-pusher seals, such as bellows seals, are often selected for high-temperature applications where traditional materials could break down over time.
Shaft Speed
The speed of the rotating shaft is important in determining the type of seal needed.
Higher speeds may call for seals that can withstand significant dynamic forces, such as cartridge seals, which offer robustness and reduced maintenance.
Fluid Nature and Compatibility
Understanding the nature of the fluid that the seal will come into contact with is vital.
If the fluid is corrosive or abrasive, selecting a material that resists wear and corrosion is crucial for longevity and performance.
Seals should be made from materials compatible with the fluid to avoid degradation over time.
Environmental and Safety Concerns
Environmental and safety considerations also play a significant role.
For example, if there is a need to prevent product contamination or leakage into the environment, opting for dry-running seals or more advanced sealing solutions might be necessary.
These considerations ensure compliance with environmental regulations and ensure worker safety.
Maintaining Mechanical Seals
Once the proper mechanical seal is selected, regular maintenance is key to ensuring its longevity and efficient operation.
Routine inspections to check for wear, tear, and proper alignment can prevent failure.
Additionally, following the manufacturer’s guidelines for operation and maintenance is critical, as this can vary significantly between different types and brands of mechanical seals.
Conclusion
Mechanical seals are essential components that prevent leakage between rotating parts in machinery, protecting both the environment and the equipment itself.
By understanding the different types of mechanical seals and considering factors such as pressure, temperature, speed, and fluid compatibility, you can select the optimal seal for your application’s specific operating conditions.
Regular maintenance and proper handling will further ensure the seal’s effective operation and longevity.
Ultimately, selecting the right mechanical seal not only improves equipment efficiency but also contributes to overall system safety and reliability.
資料ダウンロード
QCD管理受発注クラウド「newji」は、受発注部門で必要なQCD管理全てを備えた、現場特化型兼クラウド型の今世紀最高の受発注管理システムとなります。
ユーザー登録
受発注業務の効率化だけでなく、システムを導入することで、コスト削減や製品・資材のステータス可視化のほか、属人化していた受発注情報の共有化による内部不正防止や統制にも役立ちます。
NEWJI DX
製造業に特化したデジタルトランスフォーメーション(DX)の実現を目指す請負開発型のコンサルティングサービスです。AI、iPaaS、および先端の技術を駆使して、製造プロセスの効率化、業務効率化、チームワーク強化、コスト削減、品質向上を実現します。このサービスは、製造業の課題を深く理解し、それに対する最適なデジタルソリューションを提供することで、企業が持続的な成長とイノベーションを達成できるようサポートします。
製造業ニュース解説
製造業、主に購買・調達部門にお勤めの方々に向けた情報を配信しております。
新任の方やベテランの方、管理職を対象とした幅広いコンテンツをご用意しております。
お問い合わせ
コストダウンが利益に直結する術だと理解していても、なかなか前に進めることができない状況。そんな時は、newjiのコストダウン自動化機能で大きく利益貢献しよう!
(β版非公開)