- お役立ち記事
- Understanding and Managing the Firing Process: Heat Treatment for Ceramic Manufacturing and Improving Material Properties
Understanding and Managing the Firing Process: Heat Treatment for Ceramic Manufacturing and Improving Material Properties
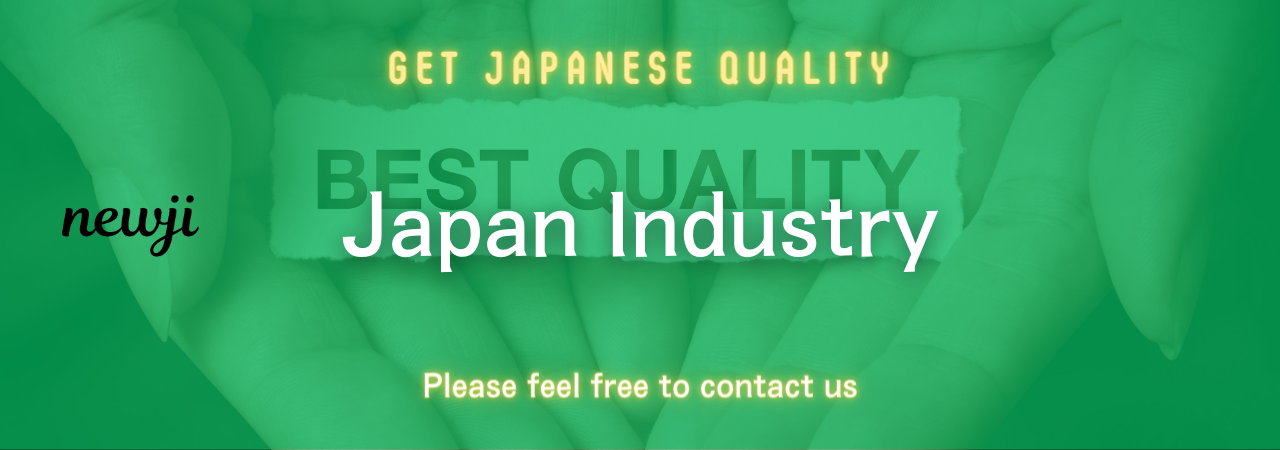
In ceramics manufacturing, one key process that significantly impacts the final product’s quality is heat treatment.
This process involves heating the ceramic materials at high temperatures to achieve desired mechanical and physical properties.
Understanding the firing process is crucial for improving material properties and ensuring the production of high-quality ceramics.
目次
What is Heat Treatment in Ceramic Manufacturing?
Heat treatment, also known as firing, is the process of heating ceramic materials to high temperatures.
This operation is essential for transforming raw ceramic mixtures into hard, durable, and functional products.
The heat treatment process usually involves several stages, each contributing to the material’s final properties.
Stages of the Heat Treatment Process
1. Drying: Before the actual firing begins, ceramic materials need to be thoroughly dried to remove any residual moisture.
This step prevents the formation of steam, which can cause cracks or other defects during firing.
Drying is typically done at relatively low temperatures, often between 100°C and 300°C.
2. Bisque Firing: This is the first high-temperature firing step.
The temperature during bisque firing usually ranges between 800°C and 1000°C.
At this stage, organic materials in the ceramic mixture burn off, and the clay particles begin to fuse.
However, the ceramics are still porous and not fully vitrified (turned into glass-like state).
3. Glaze Application: After bisque firing, a glaze can be applied to the ceramics.
Glaze is a glass-like coating that adds aesthetic appeal and provides a protective layer.
4. Glaze Firing: This is the second high-temperature firing.
It typically occurs at temperatures ranging from 1000°C to 1300°C, depending on the type of ceramic and glaze used.
During this process, the glaze melts and fuses to the ceramic surface, creating a smooth and impermeable layer.
5. Cooling: Proper cooling is essential to avoid thermal shock and stress, which can cause the ceramics to crack or warp.
Controlled cooling allows the material to stabilize and attain its final properties.
Why is Heat Treatment Important?
Heat treatment is critical in enhancing the mechanical and physical properties of ceramics.
Controlled firing helps achieve the correct structural changes in the material, leading to improved hardness, strength, durability, and thermal stability.
The firing process also allows for the removal of impurities and volatile substances, which can weaken the final product.
Impact on Mechanical Properties
The heat treatment process optimizes the mechanical properties of ceramics in various ways.
1. Hardness: Proper firing increases the hardness of ceramics, making them resistant to scratching and wear.
2. Strength: Heat-treated ceramics exhibit higher tensile and compressive strength, enabling them to withstand greater mechanical loads.
3. Fracture Toughness: Controlled heat treatment can enhance the fracture toughness of ceramics, making them less prone to cracking under stress.
Impact on Physical Properties
Heat treatment also enhances the physical properties of ceramics, which are crucial for their various applications.
1. Thermal Stability: Proper firing improves the ceramic’s thermal stability, allowing it to withstand high temperatures without degradation.
2. Chemical Resistance: Heat-treated ceramics are more resistant to chemicals, making them suitable for use in corrosive environments.
3. Electrical Insulation: Many ceramics are used as electrical insulators, and the heat treatment process ensures they retain their insulating properties under operational conditions.
Types of Kilns Used in Heat Treatment
The kiln is the furnace where the ceramic pieces are fired.
Different types of kilns are used depending on the desired firing conditions and the type of ceramics being produced.
Electric Kilns
Electric kilns are widely used in both commercial and hobby ceramic production.
They offer precise temperature control, which is essential for consistent firing results.
Electric kilns are clean and efficient, making them ideal for use in indoor settings.
Gas Kilns
Gas kilns are often used for larger-scale ceramic production.
They allow for a more dynamic firing environment, with the possibility of introducing various atmospheres (oxidizing or reducing) to achieve specific material properties.
Gas kilns require proper ventilation due to the combustion gases produced during firing.
Wood-Fired Kilns
Wood-fired kilns are the traditional type of kiln and are still used by some ceramic artists.
The firing process in wood-fired kilns is more challenging to control but can produce unique aesthetic effects on the ceramics.
They require a significant amount of labor and time to operate.
Salt/Soda Kilns
Salt or soda kilns introduce salt or sodium carbonate during firing.
This practice creates a glaze-like finish on the ceramics without having to apply glaze beforehand.
These kilns also require careful handling to manage the corrosive nature of the salts.
Optimizing the Firing Process
Achieving optimal results in ceramic heat treatment involves careful control of several factors.
Temperature Control
Precise temperature control is critical to ensure the ceramic material reaches the necessary firing temperature for the appropriate duration.
Overfiring can cause the material to melt or deform, while underfiring may result in insufficiently fused ceramics with poor mechanical properties.
Firing Atmosphere
The atmosphere within the kiln (oxidizing, reducing, or neutral) can significantly affect the final properties of the ceramics.
Different atmospheres can change the color, texture, and chemical composition of the material.
Careful control of the kiln atmosphere is necessary to achieve the desired outcomes.
Firing Schedule
A well-planned firing schedule, including ramp rates (how quickly the temperature increases), soak times (how long the temperature is held at specific points), and cooling rates, is essential for optimal results.
A poorly designed firing schedule can cause defects such as cracking, warping, or incomplete vitrification.
Common Defects and How to Avoid Them
Several common defects can occur during the heat treatment process, but they can often be avoided with proper care and attention.
Cracking
Cracking can be caused by thermal shock, rapid temperature changes, or internal stresses within the ceramic material.
To prevent cracking, ensure a slow and controlled heating and cooling process.
Warping
Warping occurs when different parts of the ceramic piece shrink unevenly during firing.
This can be minimized by ensuring uniform thickness and careful placement of the pieces within the kiln.
Blistering
Blistering is caused by trapped gases within the ceramic material that escape during firing.
Proper drying and bisque firing can help to remove these gases and prevent blistering.
In conclusion, understanding and managing the firing process is critical for producing high-quality ceramics with superior material properties.
By carefully controlling the temperature, atmosphere, and firing schedule, it is possible to achieve optimal results and minimize common defects.
Whether you are a professional in the ceramics industry or an enthusiast, mastering the heat treatment process is essential for success in ceramic manufacturing.
資料ダウンロード
QCD調達購買管理クラウド「newji」は、調達購買部門で必要なQCD管理全てを備えた、現場特化型兼クラウド型の今世紀最高の購買管理システムとなります。
ユーザー登録
調達購買業務の効率化だけでなく、システムを導入することで、コスト削減や製品・資材のステータス可視化のほか、属人化していた購買情報の共有化による内部不正防止や統制にも役立ちます。
NEWJI DX
製造業に特化したデジタルトランスフォーメーション(DX)の実現を目指す請負開発型のコンサルティングサービスです。AI、iPaaS、および先端の技術を駆使して、製造プロセスの効率化、業務効率化、チームワーク強化、コスト削減、品質向上を実現します。このサービスは、製造業の課題を深く理解し、それに対する最適なデジタルソリューションを提供することで、企業が持続的な成長とイノベーションを達成できるようサポートします。
オンライン講座
製造業、主に購買・調達部門にお勤めの方々に向けた情報を配信しております。
新任の方やベテランの方、管理職を対象とした幅広いコンテンツをご用意しております。
お問い合わせ
コストダウンが利益に直結する術だと理解していても、なかなか前に進めることができない状況。そんな時は、newjiのコストダウン自動化機能で大きく利益貢献しよう!
(Β版非公開)