- お役立ち記事
- Understanding Functional Characteristics! Correct Selection and Specific Troubleshooting of Surface Treatments for Mechanical Designers
Understanding Functional Characteristics! Correct Selection and Specific Troubleshooting of Surface Treatments for Mechanical Designers
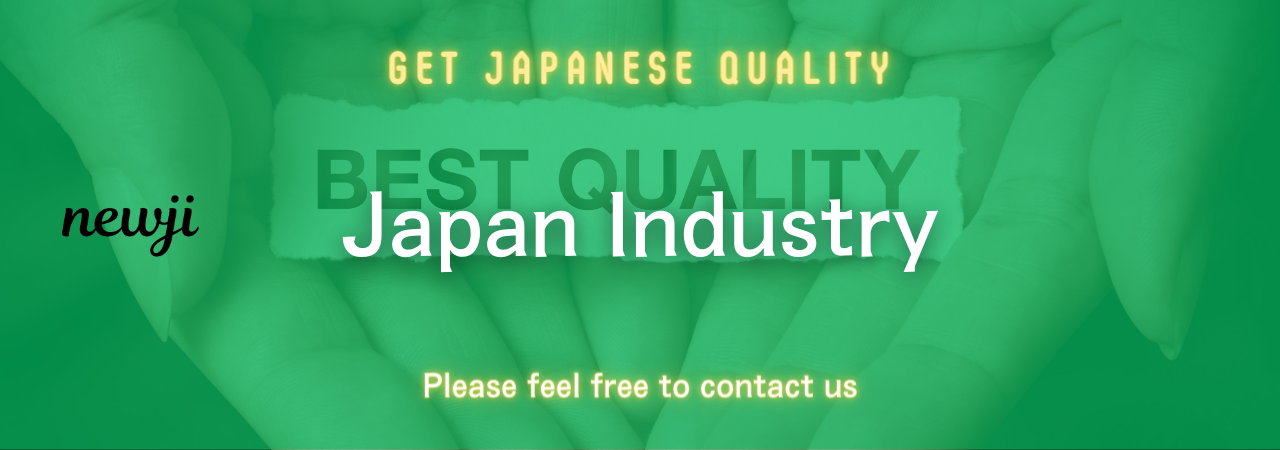
目次
Introduction to Surface Treatments
Surface treatments are critical in the field of mechanical design.
These treatments enhance the durability, aesthetic appeal, and performance of various components.
Understanding functional characteristics, correct selection, and specific troubleshooting of these treatments can significantly impact the final product’s quality.
This article delves into the essential aspects that every mechanical designer should consider while working with surface treatments.
Types of Surface Treatments
Before diving into the functional characteristics and troubleshooting, it’s essential to know the types of surface treatments available.
Coatings
Coatings are applied to the surface of a material to protect it from environmental factors such as corrosion, wear, and chemical exposure.
Common types include:
– Paints
– Powder coating
– Anodizing
– Electroplating
Each type has its unique properties and advantages.
Heat Treatments
Heat treatments change the properties of a material by heating and cooling it in a controlled environment.
The aim is to enhance hardness, strength, and resistance to wear.
Popular heat treatments include:
– Annealing
– Quenching
– Tempering
Mechanical Treatments
Mechanical treatments involve physical processes to alter the surface of the material.
These include:
– Polishing
– Grinding
– Shot peening
Such treatments improve the surface’s appearance and performance characteristics.
Functional Characteristics
Different surface treatments bring various functional benefits to a material.
Understanding these characteristics allows for an informed selection based on the specific needs of a project.
Corrosion Resistance
Corrosion resistance is essential for components exposed to moisture, chemicals, or harsh environmental conditions.
Treatments like galvanizing and anodizing provide a protective layer that inhibits corrosion.
This is crucial for parts used in marine or industrial settings.
Wear Resistance
Wear resistance is vital for components under constant friction or load.
Surface treatments like carburizing and nitriding enhance the material’s hardness, reducing wear and tear over time.
This prolongs the life of the component, ensuring better performance.
Aesthetic Appeal
Sometimes, the look and feel of the product are just as important as its performance.
Polishing and painting significantly improve the visual appeal, which is crucial for consumer-facing products.
An attractive finish can set a product apart in a competitive market.
Electrical Conductivity
In some applications, maintaining electrical conductivity is crucial.
Electroplating with metals like gold and silver can retain the electrical properties of the base material while offering additional benefits like corrosion resistance.
Correct Selection of Surface Treatments
Choosing the right surface treatment is essential for maximizing both performance and cost-effectiveness.
Here are a few factors to consider:
Material Compatibility
Not all surface treatments are suitable for every material.
For instance, anodizing is primarily used for aluminum.
Understanding the base material’s properties ensures that the chosen treatment complements it effectively.
Environmental Conditions
Consider the conditions where the component will be used.
Harsh environments may require robust surface treatments resistant to extreme temperatures, chemicals, or moisture.
Cost and Budget Constraints
High-performance surface treatments can be expensive.
However, investing in a suitable treatment can save costs in the long run by reducing wear and tear and prolonging the component’s lifespan.
It’s essential to strike a balance between performance needs and budget constraints.
Application Methods
Different treatments involve varied application methods, some of which may be more suited for large-scale production while others are ideal for precision components.
Understanding the manufacturing process helps in selecting a treatment that aligns with production capabilities.
Troubleshooting Surface Treatments
Despite best efforts, issues can arise during or after the application of surface treatments.
Being aware of common problems and their solutions can save time and costs.
Poor Adhesion
One common issue is the poor adhesion of coatings or treatments.
This can result from improper surface preparation, contamination, or incorrect application techniques.
Ensure the surface is clean, dry, and appropriately prepped before applying any treatment.
Using primers or bonding agents can also enhance adhesion.
Inconsistent Coverage
Inconsistent coverage can lead to areas of a component being exposed to environmental damage.
This often results from uneven application or inadequate curing times.
Thorough inspections during and after the treatment process can help detect and address these issues early.
Surface Cracking
Surface cracking can occur due to excessive stress, improper heat treatment, or the use of incompatible materials.
Careful monitoring of the treatment process parameters, such as temperature and pressure, can help prevent these issues.
Selecting a treatment compatible with the base material is also crucial.
Discoloration
Discoloration can be a significant issue for components where aesthetics matter.
This may result from overheating, chemical reactions, or contamination during the treatment process.
Implementing quality control checks throughout the process ensures consistent color and appearance.
Conclusion
Understanding the functional characteristics, selecting the appropriate surface treatments, and troubleshooting potential issues are vital aspects of mechanical design.
Investing time in understanding these elements can lead to better-performing, longer-lasting, and visually appealing components.
By considering factors like material compatibility, environmental conditions, and application methods, mechanical designers can make informed decisions, enhancing the overall quality and reliability of their projects.
資料ダウンロード
QCD調達購買管理クラウド「newji」は、調達購買部門で必要なQCD管理全てを備えた、現場特化型兼クラウド型の今世紀最高の購買管理システムとなります。
ユーザー登録
調達購買業務の効率化だけでなく、システムを導入することで、コスト削減や製品・資材のステータス可視化のほか、属人化していた購買情報の共有化による内部不正防止や統制にも役立ちます。
NEWJI DX
製造業に特化したデジタルトランスフォーメーション(DX)の実現を目指す請負開発型のコンサルティングサービスです。AI、iPaaS、および先端の技術を駆使して、製造プロセスの効率化、業務効率化、チームワーク強化、コスト削減、品質向上を実現します。このサービスは、製造業の課題を深く理解し、それに対する最適なデジタルソリューションを提供することで、企業が持続的な成長とイノベーションを達成できるようサポートします。
オンライン講座
製造業、主に購買・調達部門にお勤めの方々に向けた情報を配信しております。
新任の方やベテランの方、管理職を対象とした幅広いコンテンツをご用意しております。
お問い合わせ
コストダウンが利益に直結する術だと理解していても、なかなか前に進めることができない状況。そんな時は、newjiのコストダウン自動化機能で大きく利益貢献しよう!
(Β版非公開)