- お役立ち記事
- Understanding Industry 4.0: Decoding the Digital Revolution in Manufacturing
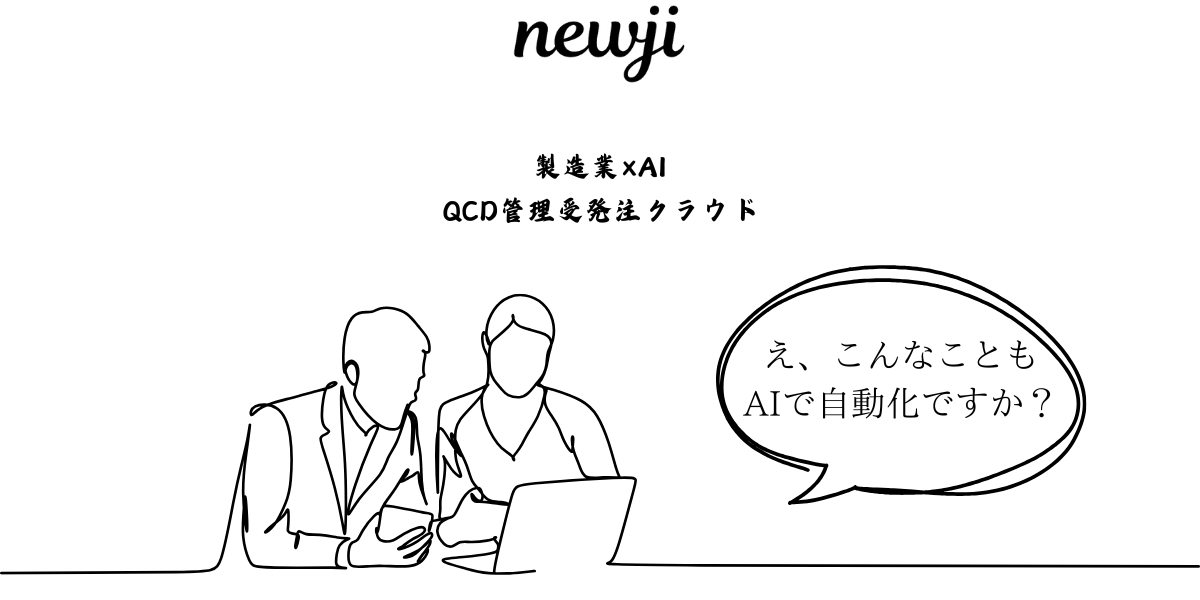
Understanding Industry 4.0: Decoding the Digital Revolution in Manufacturing
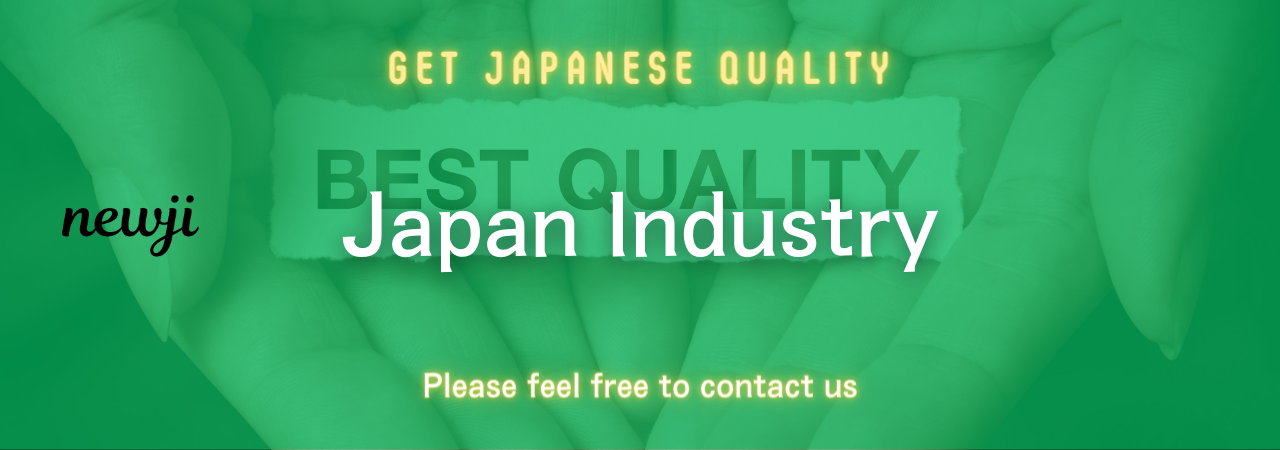
Industry 4.0 is the new buzzword in manufacturing and refers to the Fourth Industrial Revolution.
This transformation is powered by digitization and new technologies.
But what does this really mean?
How does it impact manufacturing processes and businesses?
Read on to discover the intricacies of Industry 4.0 and how it revolutionizes the manufacturing world.
目次
What is Industry 4.0?
Industry 4.0 is the latest phase in the evolution of manufacturing and industry.
The First Industrial Revolution utilized water and steam to mechanize production.
The Second used electric power to create mass production.
The Third employed electronics and information technology to automate production.
Now, Industry 4.0 leverages the potential of advanced technologies to create “smart factories.”
These smart factories considerably transform traditional manufacturing processes, making them more efficient and versatile.
Key Components of Industry 4.0
Industry 4.0 encompasses a wide variety of new technologies, each of which plays a significant role in revolutionizing manufacturing.
Let’s delve into some of these key components:
Internet of Things (IoT)
IoT involves embedding sensors and devices that can communicate with each other over the internet.
In manufacturing, this means machines can collect and share data in real-time, optimizing performance and reducing downtime.
Big Data and Analytics
The massive amount of data generated by connected devices can be processed and analyzed.
This provides insights into manufacturing processes, helping to identify inefficiencies, predict maintenance needs, and improve product quality.
Artificial Intelligence (AI) and Machine Learning
AI and machine learning enable systems to make decisions based on data, learning and improving over time.
In a manufacturing context, this can mean better quality control, more efficient workflows, and automated problem-solving.
Advanced Robotics
Robots in Industry 4.0 are not just tools but intelligent systems that can collaborate with humans.
They can perform a wide range of tasks, from assembly to inspection, often with greater precision and consistency than human workers.
Cloud Computing
Cloud computing allows companies to store and process enormous amounts of data without needing physical infrastructure.
This makes it easier for manufacturers to scale operations, collaborate across geographies, and access powerful computational resources.
Cyber-Physical Systems
These are integrations of physical processes with computational models and data.
They allow for the tight coordination and control of physical activities through software, enabling innovations like digital twins and predictive maintenance.
Benefits of Industry 4.0
The integration of these advanced technologies provides several critical benefits, making the adoption of Industry 4.0 a compelling proposition:
Increased Efficiency
By automating processes and optimizing resource use, manufacturing units can achieve significantly higher efficiencies.
Real-time data and analytics enable quick decision-making, ensuring smoother operations.
Enhanced Product Quality
Continuous monitoring and data analysis lead to improved quality control.
Manufacturers can detect defects earlier and adjust processes to ensure the highest product standards.
Reduced Operational Costs
Predictive maintenance and efficient resource use help lower operational costs.
IoT-enabled devices can predict and address issues before they lead to costly downtimes.
Greater Flexibility and Customization
Advanced manufacturing systems allow for far more flexibility in product designs and customizations.
This makes it easier to meet individual customer demands and develop bespoke solutions.
Improved Safety and Working Conditions
Automation and real-time monitoring contribute to safer working environments.
Machines can take over dangerous tasks, and sensors can detect hazardous conditions before accidents occur.
Challenges of Implementing Industry 4.0
Despite its promise, implementing Industry 4.0 is not without challenges.
Understanding these obstacles can help companies better prepare for this digital transformation:
High Initial Costs
The initial investment in hardware, software, and training can be substantial.
Small and medium-sized enterprises may find it particularly challenging to bear these costs upfront.
Skills Gap
Adopting new technologies requires a skilled workforce.
There is a growing need for operators and technicians proficient in digital tools and data analytics, leading to potential skill gaps.
Data Security Concerns
With increased connectivity comes the risk of cyber-attacks.
Manufacturers must invest in robust cybersecurity measures to protect sensitive data and ensure operational continuity.
Integration with Existing Systems
Integrating new technologies with legacy systems can be complex and daunting.
Ensuring seamless interoperability between old and new systems requires careful planning and execution.
The Future of Manufacturing with Industry 4.0
The future of manufacturing looks incredibly promising with the continued adoption of Industry 4.0.
The next steps involve further integrating and refining these technologies to realize even greater efficiencies and innovations:
Smart Supply Chains
Artificial intelligence and IoT will transform supply chains into intelligent ecosystems.
Manufacturers can expect better coordination, real-time inventory management, and more responsive logistics.
Distributed Manufacturing
Industry 4.0 facilitates more distributed manufacturing, where production can occur closer to end-users.
This can significantly reduce transportation costs and turnaround times.
Mass Customization
With advanced manufacturing systems, mass customization becomes more viable.
Manufacturers can produce highly customized products at near mass production efficiency levels.
Increased Collaboration
Cloud computing and collaborative robots will enable unprecedented levels of collaboration between human workers and machines.
Teams can work across distances and time zones, sharing information and tasks seamlessly.
As we forge ahead into this new era, Industry 4.0 will continue to shape the landscape of manufacturing, pushing the boundaries of what’s possible and driving us toward a smarter, more efficient future.
資料ダウンロード
QCD調達購買管理クラウド「newji」は、調達購買部門で必要なQCD管理全てを備えた、現場特化型兼クラウド型の今世紀最高の購買管理システムとなります。
ユーザー登録
調達購買業務の効率化だけでなく、システムを導入することで、コスト削減や製品・資材のステータス可視化のほか、属人化していた購買情報の共有化による内部不正防止や統制にも役立ちます。
NEWJI DX
製造業に特化したデジタルトランスフォーメーション(DX)の実現を目指す請負開発型のコンサルティングサービスです。AI、iPaaS、および先端の技術を駆使して、製造プロセスの効率化、業務効率化、チームワーク強化、コスト削減、品質向上を実現します。このサービスは、製造業の課題を深く理解し、それに対する最適なデジタルソリューションを提供することで、企業が持続的な成長とイノベーションを達成できるようサポートします。
オンライン講座
製造業、主に購買・調達部門にお勤めの方々に向けた情報を配信しております。
新任の方やベテランの方、管理職を対象とした幅広いコンテンツをご用意しております。
お問い合わせ
コストダウンが利益に直結する術だと理解していても、なかなか前に進めることができない状況。そんな時は、newjiのコストダウン自動化機能で大きく利益貢献しよう!
(Β版非公開)