- お役立ち記事
- Understanding the basics of injection molding, the causes and mechanisms of molding defects, and their application to preventive measures and their key points.
月間76,176名の
製造業ご担当者様が閲覧しています*
*2025年3月31日現在のGoogle Analyticsのデータより
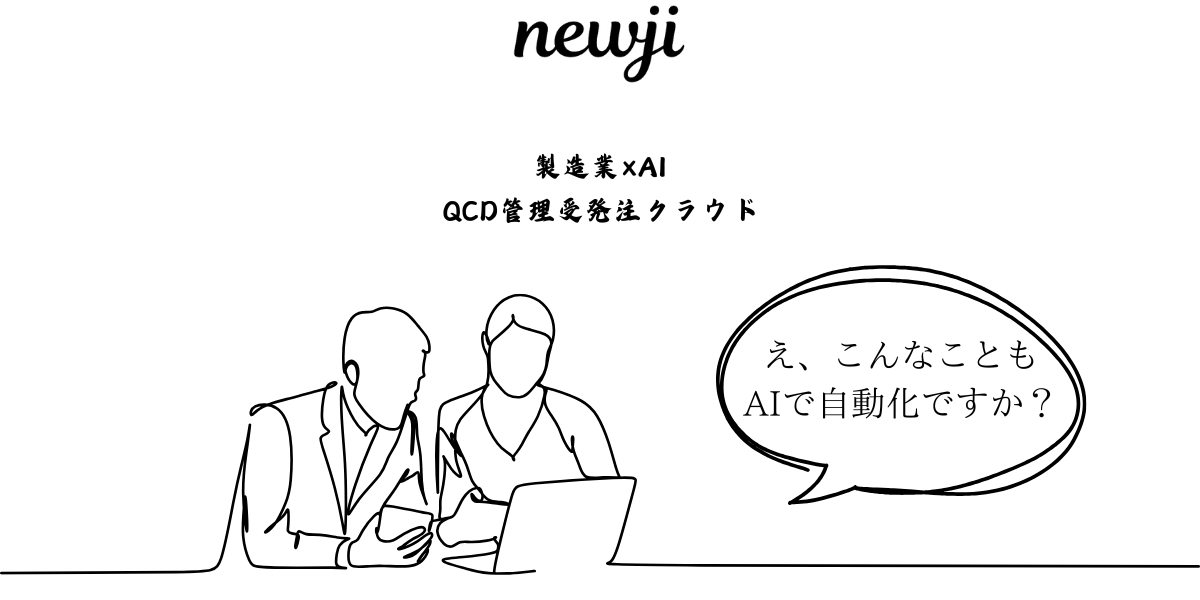
Understanding the basics of injection molding, the causes and mechanisms of molding defects, and their application to preventive measures and their key points.
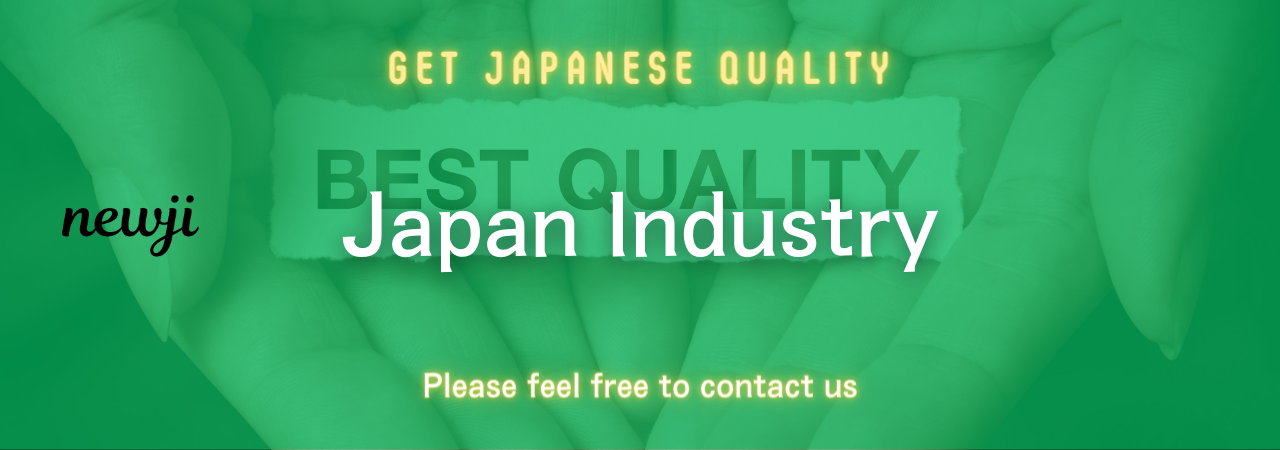
目次
Understanding the Basics of Injection Molding
Injection molding is a manufacturing process used to produce a wide range of products, from small components to large parts.
Its versatility and efficiency make it one of the most popular methods for producing plastic parts.
The process involves melting plastic pellets and injecting the molten material into a mold.
Once cooled, the mold is opened to reveal the finished part.
The cycle then repeats for mass production.
Understanding the basics of injection molding is essential for industries requiring precision and mass production.
The process begins with material selection.
Thermoplastics are the most common materials used in injection molding due to their ability to be melted and re-solidified.
Each type of plastic has unique properties, such as melting temperature and strength, which influence the final product.
Once the material is chosen, the next step involves the preparation of the mold and injection molding machine.
Molds are typically made from steel or aluminum and consist of two halves that form a cavity into which the material is injected.
The design of the mold is crucial, as it determines the shape and quality of the finished product.
The molding machine must be calibrated to the correct temperature and pressure to ensure consistency and quality in production.
Key parameters such as cycle time, pressure, and temperature must be closely monitored and adjusted to suit the characteristics of the material and the complexity of the design.
Injection molding offers several advantages, including high production rates, reduced waste material, and the ability to produce complex shapes.
However, it also has limitations, such as high initial costs for mold creation and maintenance.
As we delve deeper, understanding defects and preventive measures become imperative for maintaining the quality and efficiency of the injection molding process.
Causes and Mechanisms of Molding Defects
Despite the precision of injection molding, defects can occur.
These defects line start part defects, affect the quality and functionality of the finished product, and can increase production costs if not addressed.
Several causes lead to molding defects.
One major cause is inappropriate material selection.
Choosing the wrong plastic type for the desired product specifications often results in inefficiencies and defects.
Another common cause is poor mold design.
A mold that is not properly aligned or designed can lead to defects such as warping, flashing, or sink marks.
These issues usually arise when the flow of plastic is uneven or gets trapped.
Insufficient machine parameters often contribute to defects.
For example, incorrect injection speed, pressure, or temperature can lead to incomplete filling, causing short shots, where the material does not fill the mold cavity completely.
Similarly, too high an injection rate might cause flashing, where excess material escapes from the cavity.
Understanding the mechanisms behind these defects is vital for diagnosis and prevention.
For instance, warping occurs due to uneven cooling of the material, which results in deformations.
Sink marks happen when the outer surface solidifies faster than the inner layers, creating depressions.
Cracking or crazing can occur from residual stresses within the molded parts or external forces, which cause micro-cracks on the surface.
The presence of moisture in the material can also cause defects, leading to splay or bubbles.
Knowing these causes and mechanisms allows manufacturers to implement preventive measures effectively.
Applying Preventive Measures and Key Points
Preventive measures in injection molding aim to minimize defects and improve product quality.
These measures require a comprehensive understanding of both the molding process and potential defects.
One important preventive measure is proper material handling and selection.
Ensuring the material is free from impurities and moisture is crucial.
Pre-drying plastics can prevent defects like splay and bubbles, ensuring the final product is defect-free.
Maintaining optimal machine settings is another critical preventive measure.
Regular calibration of the injection molding machine can prevent defects related to pressure, temperature, and cycle time.
Automating these parameters can help maintain consistency in production, reducing the likelihood of defects.
The design and maintenance of the mold itself play a significant role in defect prevention.
Regular inspection and maintenance of molds ensure their alignment and cleanliness, preventing issues like flashing and warping.
Design modifications, such as improving flow paths, can greatly reduce defects.
Implementing a robust quality control system is vital to catch defects early.
Regular inspections and testing allow defects to be identified and rectified quickly, reducing the risk of defective products reaching the end user.
Employee training is also a key point for preventive measures.
Ensuring that the workforce understands the complexities of injection molding, including how to manage and maintain machinery and detect issues, is crucial for reducing defects.
Finally, investing in advanced technologies such as computer-aided engineering (CAE) tools can predict potential problems in the design phase before production begins, allowing for changes that help prevent defects.
In conclusion, while injection molding is an efficient and versatile manufacturing process, understanding and applying basic principles, recognizing defect mechanisms, and employing preventive strategies are key to successful production.
Prioritizing these elements not only enhances product quality but also streamlines production, ultimately leading to cost savings and improved satisfaction for both manufacturers and their customers.
資料ダウンロード
QCD管理受発注クラウド「newji」は、受発注部門で必要なQCD管理全てを備えた、現場特化型兼クラウド型の今世紀最高の受発注管理システムとなります。
ユーザー登録
受発注業務の効率化だけでなく、システムを導入することで、コスト削減や製品・資材のステータス可視化のほか、属人化していた受発注情報の共有化による内部不正防止や統制にも役立ちます。
NEWJI DX
製造業に特化したデジタルトランスフォーメーション(DX)の実現を目指す請負開発型のコンサルティングサービスです。AI、iPaaS、および先端の技術を駆使して、製造プロセスの効率化、業務効率化、チームワーク強化、コスト削減、品質向上を実現します。このサービスは、製造業の課題を深く理解し、それに対する最適なデジタルソリューションを提供することで、企業が持続的な成長とイノベーションを達成できるようサポートします。
製造業ニュース解説
製造業、主に購買・調達部門にお勤めの方々に向けた情報を配信しております。
新任の方やベテランの方、管理職を対象とした幅広いコンテンツをご用意しております。
お問い合わせ
コストダウンが利益に直結する術だと理解していても、なかなか前に進めることができない状況。そんな時は、newjiのコストダウン自動化機能で大きく利益貢献しよう!
(β版非公開)