- お役立ち記事
- Understanding the Relationship Between Gate Design and Molding Cycles for Efficiency
Understanding the Relationship Between Gate Design and Molding Cycles for Efficiency
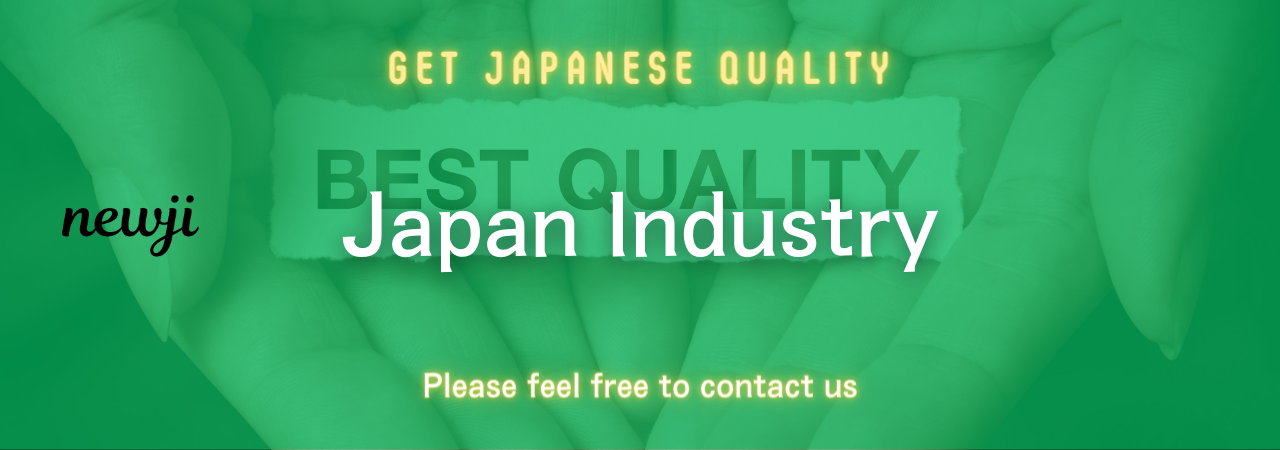
When it comes to the world of manufacturing, particularly in molding and casting, the efficiency of the process is of utmost importance.
One of the key factors that can dramatically impact this efficiency is the design of the gate used in molding.
Gate design plays a pivotal role in determining the molding cycle time, which in turn influences production speed, costs, and overall product quality.
In this article, we will delve into the relationship between gate design and molding cycles, and how understanding this relationship can lead to more efficient manufacturing processes.
目次
Understanding Gate Design in Molding
Before discussing the relationship between gate design and molding cycles, let’s first understand what a gate is in the context of molding.
A gate is the entry point through which the molten material enters the mold cavity.
Its purpose is to ensure the smooth and even filling of the mold, minimizing defects and ensuring optimal product quality.
The design of the gate affects how quickly and efficiently the material can flow into the mold, which in turn affects the overall molding cycle time.
Types of Gates
There are various types of gates used in molding, each with its unique design and specific applications.
1. **Edge Gates**: These gates are located at the edge of the mold cavity and are often used for parts where aesthetics are important, as they minimize the visibility of the gate mark.
2. **Fan Gates**: These gates allow for even distribution of material across a larger area, which is beneficial for larger parts.
3. **Pin Gates**: Used primarily in hot runner systems, pin gates leave a minimal mark on the finished product and are ideal for high-volume production.
4. **Diaphragm Gates**: Commonly used in cylindrical parts, these gates allow for uniform filling around a central point.
Each type of gate design provides specific advantages and challenges in terms of the molding cycle, which manufacturers must carefully consider.
Impact of Gate Design on Molding Cycles
The design of the gate directly influences several factors of the molding cycle, including the time it takes to fill the mold, cooling time, and ease of ejection.
These elements combined determine the overall cycle time, which is a crucial metric for efficient production.
Mold Fill Time
The size and shape of the gate affect how quickly the mold can be filled.
A smaller gate restricts the flow of material, potentially increasing the fill time.
Conversely, a larger gate allows for faster filling but may compromise the aesthetics or structural integrity of the final product.
Balancing these factors is essential to optimizing the molding cycle.
Cooling Time
Gate design also impacts the cooling phase of the molding process.
The location of the gate can create varying thicknesses in the material, which can lead to uneven cooling.
Uneven cooling often results in warping or other defects, necessitating adjustments that can lengthen cycle time.
Designing a gate that ensures uniform distribution of material can help reduce cooling time and enhance product quality.
Ejection Efficiency
Finally, the ease with which a product can be ejected from the mold is influenced by gate design.
If the gate leaves a large or awkward mark, additional finishing processes might be needed to remove or hide it, thus extending the cycle.
A well-designed gate minimizes these marks and allows for smoother ejection, thereby saving time and reducing wear on the mold.
Design Considerations for Improving Efficiency
To achieve optimal efficiency in molding processes, manufacturers must carefully consider several factors when designing a gate.
These factors influence not only the cycle time but also the quality and consistency of the final product.
Material Selection
The type of material being molded can greatly influence gate design.
Different materials have varying viscosities and thermal properties, which should be accounted for in the design process.
For example, a material that cools quickly may benefit from a gate design that promotes rapid filling and uniform thickness.
Mold Design
The overall design of the mold is another critical consideration.
Complex or intricate molds may require specific gate designs to ensure all parts of the mold are filled properly.
An optimized gate design takes into account the contours and dimensions of the mold to ensure efficient material flow.
Gate Location
Where the gate is placed on the mold can significantly affect the cycle time and the quality of the molded part.
Placing the gate in an area that allows for balanced fill and minimal waste is crucial.
Strategically positioning the gate can also help in reducing the formation of air bubbles and other defects.
Conclusion
Understanding the relationship between gate design and molding cycles is essential for improving manufacturing efficiency.
By carefully selecting the type, size, location, and material of the gate, manufacturers can significantly enhance production speeds while maintaining high product quality.
Optimizing these elements leads to shorter cycle times, reducing costs and increasing the output of a manufacturing operation.
Staying informed about advancements in gate design technology and regularly reviewing molding processes can ensure continuous improvements in manufacturing efficiency.
資料ダウンロード
QCD調達購買管理クラウド「newji」は、調達購買部門で必要なQCD管理全てを備えた、現場特化型兼クラウド型の今世紀最高の購買管理システムとなります。
ユーザー登録
調達購買業務の効率化だけでなく、システムを導入することで、コスト削減や製品・資材のステータス可視化のほか、属人化していた購買情報の共有化による内部不正防止や統制にも役立ちます。
NEWJI DX
製造業に特化したデジタルトランスフォーメーション(DX)の実現を目指す請負開発型のコンサルティングサービスです。AI、iPaaS、および先端の技術を駆使して、製造プロセスの効率化、業務効率化、チームワーク強化、コスト削減、品質向上を実現します。このサービスは、製造業の課題を深く理解し、それに対する最適なデジタルソリューションを提供することで、企業が持続的な成長とイノベーションを達成できるようサポートします。
オンライン講座
製造業、主に購買・調達部門にお勤めの方々に向けた情報を配信しております。
新任の方やベテランの方、管理職を対象とした幅広いコンテンツをご用意しております。
お問い合わせ
コストダウンが利益に直結する術だと理解していても、なかなか前に進めることができない状況。そんな時は、newjiのコストダウン自動化機能で大きく利益貢献しよう!
(Β版非公開)