- お役立ち記事
- Unleashing Excellence in Japanese Manufacturing: The Role of “Fatigue Tests” in Ensuring Durability and Performance
月間77,185名の
製造業ご担当者様が閲覧しています*
*2025年2月28日現在のGoogle Analyticsのデータより
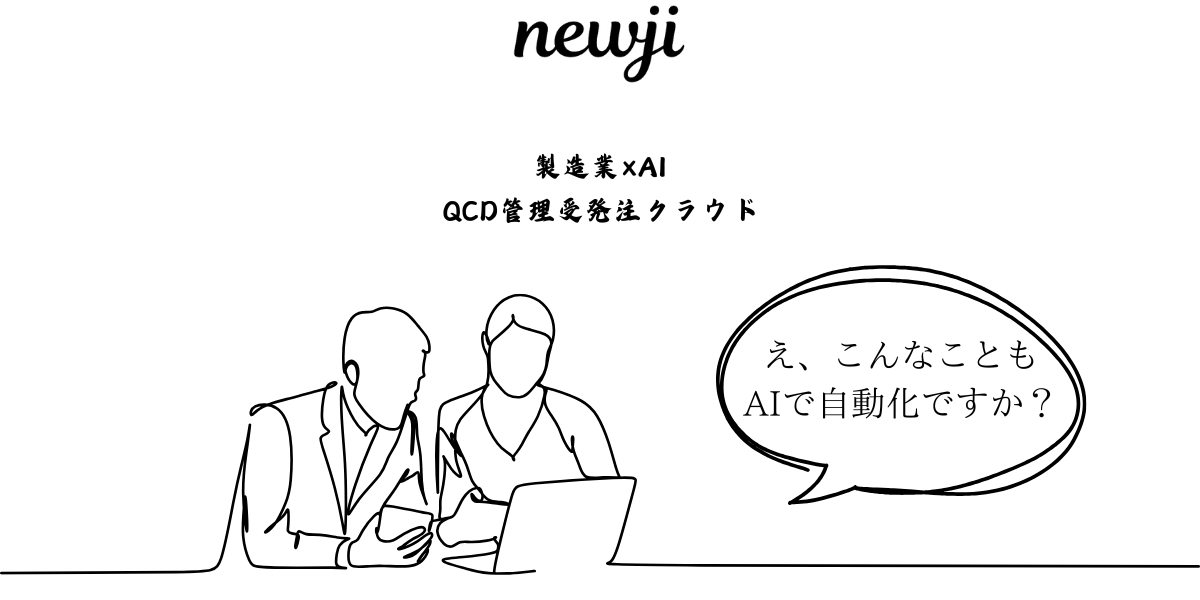
Unleashing Excellence in Japanese Manufacturing: The Role of “Fatigue Tests” in Ensuring Durability and Performance
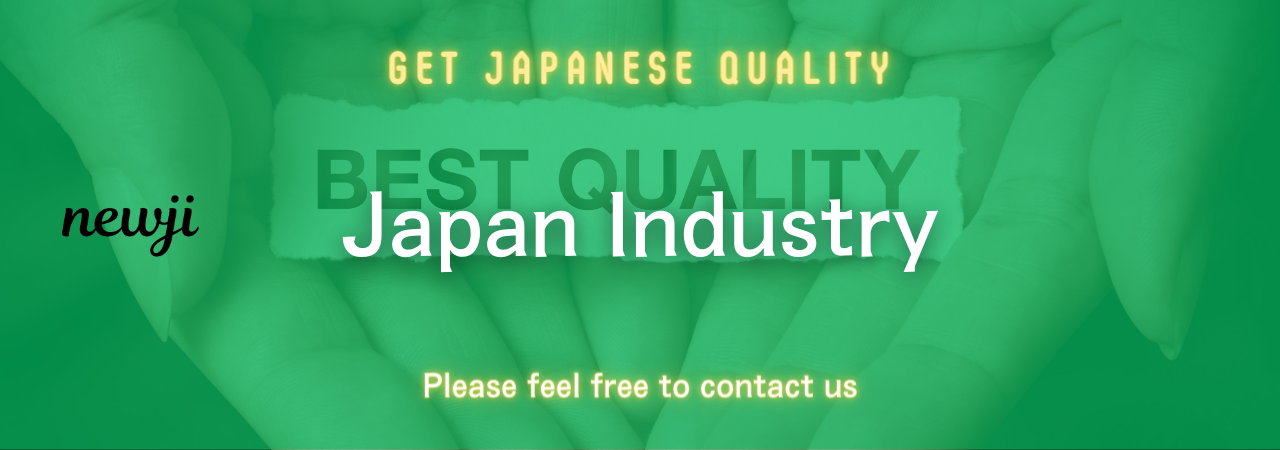
目次
Introduction
The global manufacturing landscape holds Japanese manufacturing in high regard for its meticulous approach and stringent standards.
A pivotal role in this renowned quality is attributed to the systematic incorporation of “fatigue tests.”
This article delves deeply into the essence of fatigue tests, their significance, methodologies, and the far-reaching implications they hold for durability and performance in Japanese manufacturing.
Understanding Fatigue Tests
What Are Fatigue Tests?
Fatigue tests are standardized methods employed to ascertain the durability and endurance of materials under repetitive cyclic loading.
These tests mimic real-world conditions to evaluate how materials behave under prolonged stress.
Fatigue tests are crucial in predicting the lifespan and reliability of a product.
Types of Fatigue Tests
Various types of fatigue tests exist, each tailored to specific material properties and application requirements:
– **High-Cycle Fatigue (HCF) Tests:** These tests involve a large number of cycles at relatively low stress levels.
– **Low-Cycle Fatigue (LCF) Tests:** These involve fewer cycles but occur at higher stress levels.
– **Thermal Fatigue Tests:** Focus on the material’s response to cyclic variations in temperature.
– **Corrosion Fatigue Tests:** Examine the material’s endurance in corrosive environments.
Importance of Fatigue Tests in Japanese Manufacturing
Ensuring Product Longevity
One of the paramount objectives of Japanese manufacturers is to ensure product longevity.
Fatigue tests allow manufacturers to simulate real-world usage scenarios, providing insights into how products will perform over time.
This preemptive testing helps in designing products that not only meet but often exceed customer expectations in terms of longevity and reliability.
Maintaining High Standards of Quality
Japanese manufacturing is synonymous with high quality.
Fatigue tests form the bedrock of maintaining these standards.
Through rigorous testing, manufacturers can identify potential failure points and address them before products reach the market.
This proactive approach reduces the likelihood of costly recalls and maintains the brand’s reputation for quality.
Innovation and Continuous Improvement
Fatigue tests are integral to the culture of continuous improvement, or “Kaizen,” prevalent in Japanese manufacturing.
By constantly testing and analyzing materials, manufacturers can innovate and improve their products.
This commitment to continuous improvement helps in maintaining a competitive edge in the market.
Methodologies in Fatigue Testing
Sample Preparation
Proper sample preparation is critical to obtaining accurate fatigue test results.
Samples must be representative of the actual materials used in production.
Uniformity in size, shape, and surface finish ensures consistency in test results.
Load Application
Cyclic loading is applied to the sample in a controlled manner.
The load can be in the form of stress (force per unit area) or strain (deformation per unit length).
Advanced testing machines with precise control systems are used to apply the load accurately.
Data Acquisition and Analysis
Sophisticated sensors and data acquisition systems capture real-time data during the test.
This data includes information on the number of cycles, stress levels, and material deformation.
Advanced software tools are used to analyze this data, providing insights into the material’s fatigue life.
Endurance Limit Determination
One of the key outcomes of fatigue testing is the determination of the material’s endurance limit.
This is the maximum stress level below which the material can withstand an infinite number of cycles without failing.
Understanding the endurance limit is crucial in designing durable products.
Practical Implications of Fatigue Testing
Material Selection
Fatigue test results play a significant role in material selection.
Manufacturers can choose materials that exhibit superior fatigue resistance for specific applications.
This ensures that the final product is robust and capable of withstanding real-world conditions.
Design Optimization
Fatigue test data is invaluable for design engineers.
By understanding how materials behave under cyclic loading, engineers can optimize product designs to enhance durability.
This includes making informed decisions on material thickness, geometric shapes, and stress concentration areas.
Quality Control
Incorporating fatigue tests into the quality control process helps in maintaining consistent product quality.
Regular testing of production batches ensures that materials meet the required fatigue resistance standards.
This minimizes the risk of defects and enhances overall product reliability.
Advantages of Fatigue Testing in Japanese Manufacturing
Enhanced Product Reliability
Fatigue testing provides a scientific basis for ensuring product reliability.
By understanding the material’s behavior under stress, manufacturers can predict and mitigate potential failures.
This leads to products that customers can trust for their durability and performance.
Cost Savings
Investing in fatigue testing can lead to significant cost savings in the long run.
By identifying and addressing potential issues early in the development process, manufacturers can avoid costly recalls and warranty claims.
This proactive approach also reduces the need for extensive field testing, saving both time and resources.
Customer Satisfaction
Products that undergo rigorous fatigue testing are more likely to meet or exceed customer expectations.
This translates to higher customer satisfaction and brand loyalty.
Satisfied customers are more likely to become repeat buyers and advocates for the brand.
Challenges and Disadvantages of Fatigue Testing
Initial Investment
One of the primary disadvantages of fatigue testing is the initial investment required.
Setting up a fatigue testing lab with advanced equipment can be costly.
However, this investment is often justified by the long-term benefits in terms of product quality and reliability.
Time-Consuming Process
Fatigue testing can be time-consuming, especially for high-cycle fatigue tests.
The extended duration of these tests may delay the product development process.
However, manufacturers mitigate this by integrating fatigue testing early in the design phase.
Complex Data Interpretation
Interpreting fatigue test data requires specialized knowledge and expertise.
The complexity of the data can be a challenge for manufacturers who lack in-house expertise.
However, partnering with specialized testing labs or investing in training programs can overcome this hurdle.
Supplier Negotiation Techniques for Fatigue Testing Equipment
Understanding Market Conditions
Before entering negotiations for fatigue testing equipment, it’s crucial to understand the current market conditions.
This includes knowing the leading suppliers, the latest technological advancements, and the pricing trends.
Being well-informed gives you a stronger negotiating position.
Assessing Supplier Capabilities
Evaluate potential suppliers based on their capabilities and track record.
Consider factors such as their product range, after-sales support, and reputation in the industry.
A supplier with a strong presence and positive feedback is more likely to provide reliable and high-quality equipment.
Negotiating Terms and Conditions
Negotiate terms and conditions beyond the price.
This includes warranties, maintenance agreements, and training programs.
A comprehensive service package can add significant value to your purchase and ensure optimal equipment performance.
Leveraging Long-Term Relationships
If you have an existing relationship with a supplier, leverage it during negotiations.
Long-term relationships often come with mutual trust and better pricing options.
Suppliers may offer discounts or favorable terms to retain a valuable customer.
Best Practices in Implementing Fatigue Testing
Creating a Dedicated Testing Facility
Setting up a dedicated fatigue testing facility ensures that all tests are conducted in a controlled environment.
This enhances the accuracy and reliability of test results.
Ensure the facility is equipped with advanced testing machines, data acquisition systems, and trained personnel.
Standardizing Testing Procedures
Standardize testing procedures to ensure consistency in results.
Develop detailed protocols for sample preparation, load application, data collection, and analysis.
Standardization minimizes variability and enhances the comparability of test results.
Integrating Testing with Design and Production
Integrate fatigue testing with the design and production processes.
Collaborate with design engineers to incorporate test results into product designs.
Ensure that production batches undergo regular testing to maintain quality standards.
Continuous Training and Development
Invest in continuous training and development programs for your testing personnel.
Stay updated with the latest advancements in fatigue testing methodologies and equipment.
This ensures that your team is well-equipped to conduct accurate and reliable tests.
Conclusion
The role of fatigue tests in Japanese manufacturing cannot be overstated.
They are integral to ensuring product durability, maintaining high standards of quality, and fostering innovation.
While there are challenges associated with fatigue testing, the long-term benefits far outweigh the initial investment and effort.
By understanding the significance of fatigue tests, employing best practices, and leveraging insightful supplier negotiation techniques, you can unlock the potential for excellence in manufacturing.
Japanese manufacturers have set a benchmark in this regard, and emulating their approach can lead to substantial improvements in product reliability and customer satisfaction.
In a world where quality and durability are paramount, fatigue tests stand as a testament to the unwavering commitment to excellence.
資料ダウンロード
QCD管理受発注クラウド「newji」は、受発注部門で必要なQCD管理全てを備えた、現場特化型兼クラウド型の今世紀最高の受発注管理システムとなります。
ユーザー登録
受発注業務の効率化だけでなく、システムを導入することで、コスト削減や製品・資材のステータス可視化のほか、属人化していた受発注情報の共有化による内部不正防止や統制にも役立ちます。
NEWJI DX
製造業に特化したデジタルトランスフォーメーション(DX)の実現を目指す請負開発型のコンサルティングサービスです。AI、iPaaS、および先端の技術を駆使して、製造プロセスの効率化、業務効率化、チームワーク強化、コスト削減、品質向上を実現します。このサービスは、製造業の課題を深く理解し、それに対する最適なデジタルソリューションを提供することで、企業が持続的な成長とイノベーションを達成できるようサポートします。
製造業ニュース解説
製造業、主に購買・調達部門にお勤めの方々に向けた情報を配信しております。
新任の方やベテランの方、管理職を対象とした幅広いコンテンツをご用意しております。
お問い合わせ
コストダウンが利益に直結する術だと理解していても、なかなか前に進めることができない状況。そんな時は、newjiのコストダウン自動化機能で大きく利益貢献しよう!
(β版非公開)