- お役立ち記事
- Unleashing Innovation: How Color Pattern Sensors Revolutionize Japanese Manufacturing
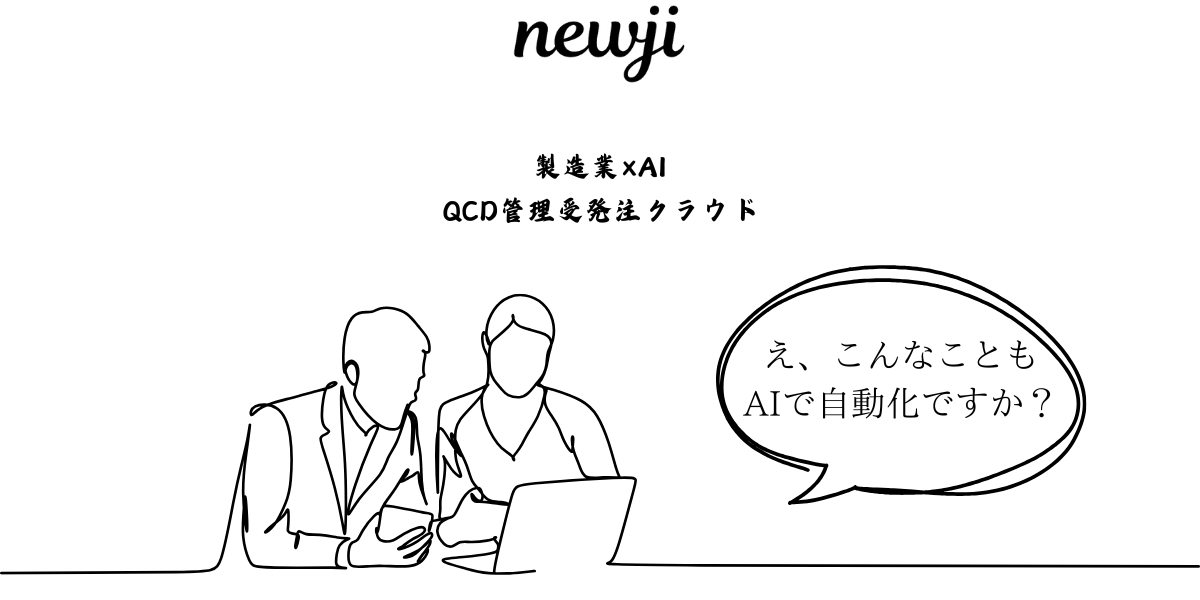
Unleashing Innovation: How Color Pattern Sensors Revolutionize Japanese Manufacturing
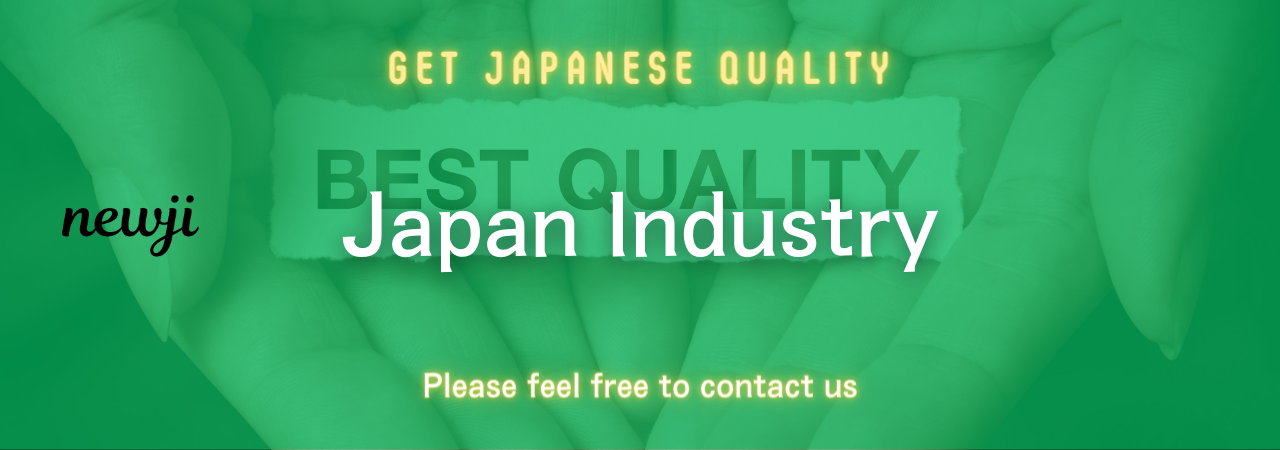
目次
Introduction
Japanese manufacturing has long been synonymous with precision, quality, and innovation. In recent years, the integration of advanced technologies such as color pattern sensors has further propelled the industry into a new era of efficiency and excellence. This article explores how color pattern sensors are revolutionizing Japanese manufacturing, offering insights into procurement and purchasing strategies, supplier negotiation techniques, market conditions, and best practices for leveraging these technologies effectively.
The Role of Color Pattern Sensors in Modern Manufacturing
Color pattern sensors are sophisticated devices that detect and interpret color patterns on products or components during the manufacturing process. These sensors play a crucial role in ensuring product quality, automating processes, and enhancing overall production efficiency.
Enhancing Quality Control
Quality control is a cornerstone of Japanese manufacturing. Color pattern sensors contribute significantly by providing real-time inspection capabilities. They detect color deviations, inconsistencies, and defects that might not be visible to the human eye. This immediate feedback allows for prompt corrective actions, reducing the likelihood of defective products reaching the market.
Improving Production Efficiency
By automating the inspection process, color pattern sensors eliminate the need for manual quality checks, which can be time-consuming and prone to human error. This automation leads to faster production cycles and allows manufacturers to maintain high throughput without compromising on quality.
Facilitating Automation and Smart Manufacturing
Color pattern sensors are integral to the development of smart factories. They enable seamless integration with other automated systems, such as robotics and AI-driven analytics. This interconnectedness facilitates advanced manufacturing techniques, predictive maintenance, and data-driven decision-making, further enhancing factory efficiency and innovation.
Advantages of Integrating Color Pattern Sensors
The adoption of color pattern sensors offers numerous advantages to Japanese manufacturers, particularly in the realms of procurement, quality control, and operational efficiency.
Enhanced Product Quality
Color pattern sensors ensure that each product meets strict quality standards by consistently monitoring color accuracy and pattern integrity. This level of precision is essential for industries where color consistency is critical, such as automotive, electronics, and consumer goods.
Cost Savings
Automated inspection reduces labor costs associated with manual quality checks. Additionally, early detection of defects minimizes waste and rework, leading to significant cost savings over time.
Increased Production Speed
With color pattern sensors handling quality inspections at high speeds, manufacturers can maintain faster production rates without sacrificing quality. This efficiency is particularly beneficial in high-volume manufacturing environments.
Data Collection and Analysis
Color pattern sensors generate valuable data that can be analyzed to identify trends, optimize processes, and predict potential issues. This data-driven approach supports continuous improvement initiatives and strategic decision-making.
Challenges and Disadvantages
While the benefits of color pattern sensors are substantial, manufacturers must also navigate certain challenges to maximize their potential.
Initial Investment Costs
Implementing color pattern sensor technology requires a significant upfront investment. The costs include purchasing the sensors, integrating them into existing systems, and training staff to operate and maintain the equipment.
Integration with Existing Systems
Seamlessly integrating color pattern sensors with current manufacturing systems can be complex. It requires careful planning, expertise, and sometimes, customization to ensure compatibility and optimal performance.
Technical Skill Requirements
Operating and maintaining advanced sensors necessitates specialized technical skills. Manufacturers must invest in training their workforce or hiring skilled personnel to manage these technologies effectively.
Supplier Negotiation Techniques
Successfully procuring color pattern sensors from Japanese suppliers involves strategic negotiation techniques that account for both cultural and business practices.
Building Strong Relationships with Japanese Suppliers
In Japanese business culture, building trust and long-term relationships is paramount. Establishing strong connections with suppliers fosters cooperation, reliability, and mutual respect, which are essential for successful negotiations.
Understanding Cultural Nuances
Japanese business practices emphasize harmony, respect, and indirect communication. Being mindful of these cultural nuances can enhance negotiation outcomes and facilitate smoother interactions with suppliers.
Leveraging Long-Term Partnerships
Emphasizing the potential for long-term collaboration can be advantageous in negotiations. Suppliers are more likely to offer favorable terms and prioritize your business if they see a commitment to a sustained partnership.
Market Conditions for Color Pattern Sensors
Understanding the current market landscape is crucial for making informed procurement decisions regarding color pattern sensors.
Current Trends in Japanese Manufacturing
Japanese manufacturers are increasingly adopting Industry 4.0 technologies, including advanced sensors, robotics, and AI. This trend reflects a broader commitment to innovation, efficiency, and competitiveness in the global market.
Demand for Color Pattern Sensors
The demand for color pattern sensors is growing as manufacturers seek to enhance quality control and automate their production lines. Industries such as automotive, electronics, and consumer goods are leading the adoption of these technologies.
Competitive Landscape
The market for color pattern sensors is competitive, with several established and emerging players offering a range of products. Manufacturers must evaluate suppliers based on factors such as technology, reliability, support services, and cost-effectiveness.
Best Practices in Procurement and Purchasing
Adopting best practices in procurement and purchasing can optimize the acquisition of color pattern sensors and ensure they deliver maximum value to the manufacturing process.
Evaluating Supplier Capabilities
Assessing a supplier’s technical expertise, production capacity, and quality assurance processes is essential. This evaluation ensures that the supplier can meet your specific requirements and maintain consistent product quality.
Ensuring Quality Standards
Establishing clear quality standards and expectations with suppliers helps maintain the integrity of the sensors. Implementing stringent quality control measures and regular audits can mitigate risks related to product defects and inconsistencies.
Effective Communication Strategies
Maintaining open and transparent communication with suppliers fosters collaboration and problem-solving. Regular updates, feedback sessions, and clear documentation are vital for addressing issues promptly and enhancing the overall procurement process.
Practical Insights from the Field
Drawing from real-world experiences in procurement and purchasing can provide valuable lessons for integrating color pattern sensors into Japanese manufacturing.
Case Study: Automotive Industry
An automotive manufacturer implemented color pattern sensors to inspect paint finishes on vehicle bodies. The sensors detected color mismatches and surface defects with high precision, reducing the rate of rejections and enhancing overall product quality. By automating the inspection process, the manufacturer also increased production throughput and lowered labor costs.
Case Study: Electronics Manufacturing
In the electronics sector, a company utilized color pattern sensors to verify the placement and alignment of components on circuit boards. The sensors identified misalignments and incorrect color codes, ensuring that only accurately assembled boards proceeded to the next production stage. This implementation minimized defects and improved the reliability of the final products.
Future Outlook
The future of color pattern sensors in Japanese manufacturing looks promising, with ongoing advancements poised to further transform the industry.
Advancements in Sensor Technology
Continuous improvements in sensor technology, including enhanced image processing algorithms and increased sensitivity, will expand the capabilities of color pattern sensors. These advancements will enable even more precise quality control and support increasingly complex manufacturing processes.
Integration with Emerging Technologies
Color pattern sensors will increasingly integrate with other emerging technologies such as artificial intelligence, machine learning, and the Internet of Things (IoT). This integration will facilitate smarter manufacturing systems, predictive maintenance, and more efficient operations.
Sustainability and Environmental Impact
As sustainability becomes a critical focus, color pattern sensors can contribute by optimizing resource usage, reducing waste, and ensuring compliance with environmental standards. Manufacturers can leverage these sensors to enhance their sustainability initiatives and meet regulatory requirements.
Conclusion
Color pattern sensors are revolutionizing Japanese manufacturing by enhancing quality control, improving production efficiency, and enabling advanced automation. While there are challenges associated with their implementation, the benefits far outweigh the drawbacks. By adopting strategic procurement and purchasing practices, building strong supplier relationships, and staying abreast of market trends, manufacturers can effectively leverage color pattern sensors to drive innovation and maintain a competitive edge in the global market. As technology continues to evolve, color pattern sensors will remain a pivotal component in the pursuit of manufacturing excellence.
資料ダウンロード
QCD調達購買管理クラウド「newji」は、調達購買部門で必要なQCD管理全てを備えた、現場特化型兼クラウド型の今世紀最高の購買管理システムとなります。
ユーザー登録
調達購買業務の効率化だけでなく、システムを導入することで、コスト削減や製品・資材のステータス可視化のほか、属人化していた購買情報の共有化による内部不正防止や統制にも役立ちます。
NEWJI DX
製造業に特化したデジタルトランスフォーメーション(DX)の実現を目指す請負開発型のコンサルティングサービスです。AI、iPaaS、および先端の技術を駆使して、製造プロセスの効率化、業務効率化、チームワーク強化、コスト削減、品質向上を実現します。このサービスは、製造業の課題を深く理解し、それに対する最適なデジタルソリューションを提供することで、企業が持続的な成長とイノベーションを達成できるようサポートします。
オンライン講座
製造業、主に購買・調達部門にお勤めの方々に向けた情報を配信しております。
新任の方やベテランの方、管理職を対象とした幅広いコンテンツをご用意しております。
お問い合わせ
コストダウンが利益に直結する術だと理解していても、なかなか前に進めることができない状況。そんな時は、newjiのコストダウン自動化機能で大きく利益貢献しよう!
(Β版非公開)