- お役立ち記事
- Unleashing Japan’s Manufacturing Power: An Insightful Dive into Process Capability Analysis
月間77,185名の
製造業ご担当者様が閲覧しています*
*2025年2月28日現在のGoogle Analyticsのデータより
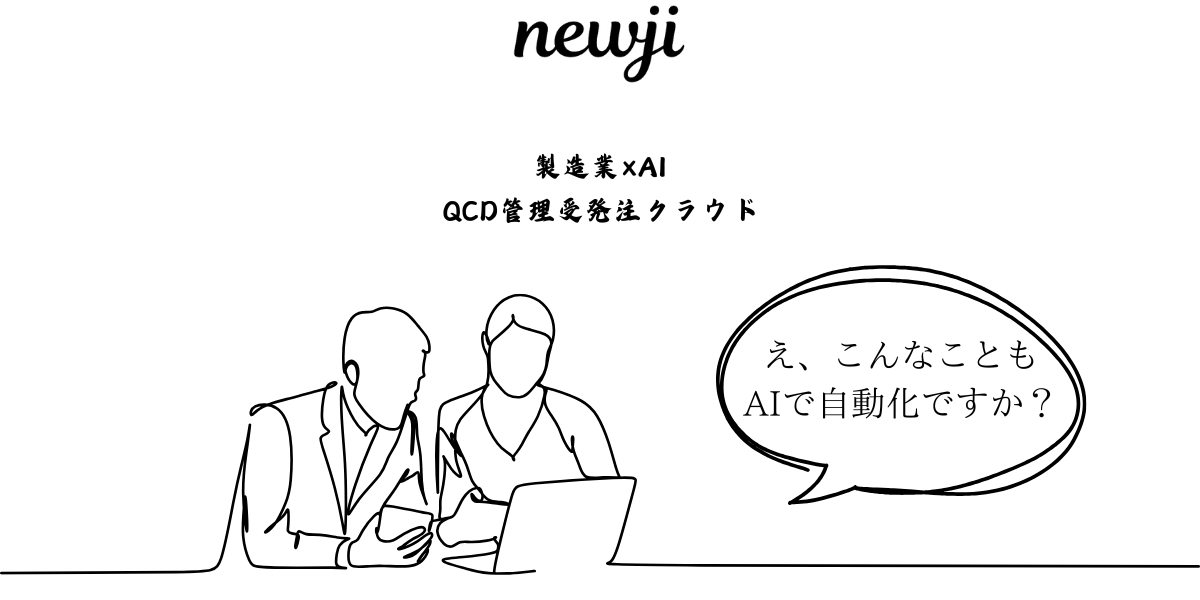
Unleashing Japan’s Manufacturing Power: An Insightful Dive into Process Capability Analysis
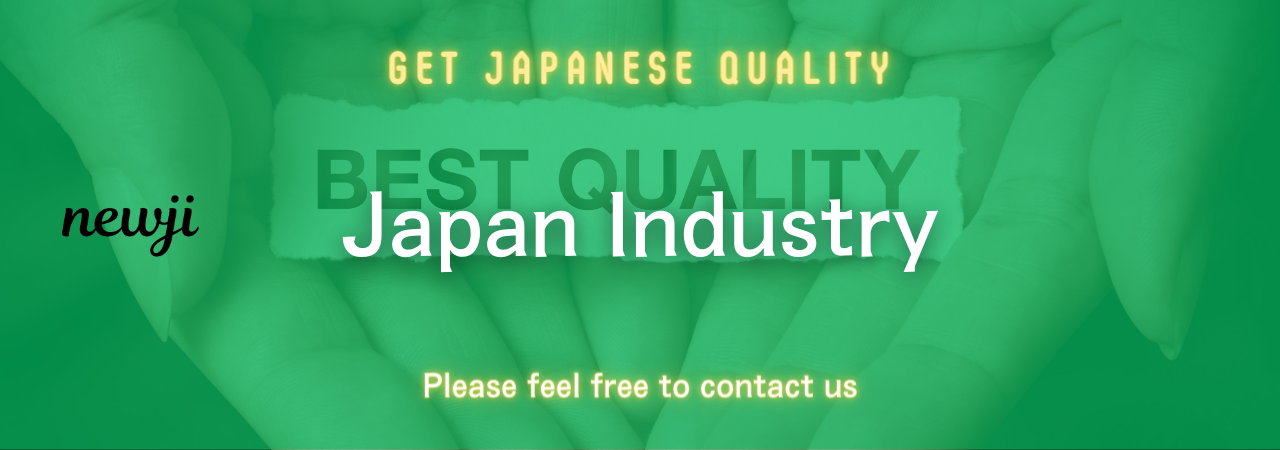
目次
Understanding Process Capability Analysis
Process Capability Analysis is a statistical technique used to assess the ability of a manufacturing process to produce products that meet specified quality standards.
It involves measuring the variability in a process and determining how well it can consistently produce items within the desired specifications.
This analysis is crucial for maintaining high-quality standards and ensuring customer satisfaction in manufacturing operations.
Definition and Importance
Process Capability Analysis quantifies the performance of a manufacturing process in relation to its specifications.
It provides a numerical value that indicates how well a process can produce outputs within the defined limits.
This measurement is vital for identifying areas of improvement and ensuring that products meet quality expectations.
In the competitive manufacturing landscape, especially in Japan, maintaining high process capability is essential for sustaining market leadership and customer trust.
Key Metrics in Process Capability
Several key metrics are used in Process Capability Analysis to evaluate process performance:
– **Cp (Process Capability Index):** Measures the potential capability of a process by comparing the width of the process spread to the width of the specification limits.
– **Cpk (Process Capability Index adjusted for centering):** Considers whether the process mean is centered between the specification limits, providing a more accurate assessment.
– **Pp and Ppk:** Similar to Cp and Cpk but focus on overall process performance rather than short-term capability.
These metrics help manufacturers understand the capability of their processes and identify necessary adjustments to improve quality.
The Role of Process Capability Analysis in Japanese Manufacturing
Japanese manufacturing is renowned for its emphasis on quality and efficiency, and Process Capability Analysis plays a pivotal role in this success.
By systematically evaluating and enhancing process capabilities, Japanese manufacturers maintain their reputation for producing high-quality products consistently.
Cultural Emphasis on Quality
Quality is deeply ingrained in Japanese manufacturing culture.
The concept of “Kaizen,” meaning continuous improvement, drives ongoing efforts to refine processes and eliminate defects.
Process Capability Analysis aligns with this cultural focus by providing measurable insights that inform improvement initiatives.
This systematic approach ensures that quality remains a priority at every stage of production.
Continuous Improvement (Kaizen)
Kaizen is a foundational principle in Japanese manufacturing that advocates for continuous, incremental improvements.
Process Capability Analysis supports Kaizen by identifying process variations and pinpointing areas where enhancements can be made.
By regularly conducting capability analyses, manufacturers can implement small, consistent changes that collectively lead to significant performance gains over time.
Advantages of Robust Process Capability Analysis
Implementing a strong Process Capability Analysis framework offers numerous benefits to manufacturing operations.
These advantages contribute to improved product quality, cost efficiency, and competitive positioning.
Enhancing Product Quality
A thorough capability analysis ensures that manufacturing processes are capable of producing products that meet or exceed quality standards.
By identifying and reducing process variability, manufacturers can achieve higher consistency in their products, leading to increased customer satisfaction and reduced defect rates.
Reducing Costs through Efficiency
Improving process capability often leads to greater operational efficiency.
Fewer defects and less rework translate to lower production costs.
Moreover, efficient processes reduce waste and optimize resource utilization, contributing to overall cost savings.
Gaining Competitive Advantage
High process capability differentiates manufacturers in the competitive market.
Consistently delivering high-quality products enhances brand reputation and customer loyalty.
This competitive edge is particularly significant in industries where quality is a key purchasing criterion.
Challenges and Disadvantages
While Process Capability Analysis offers significant benefits, there are also challenges and potential drawbacks to consider.
Understanding these issues is essential for effective implementation and achieving desired outcomes.
Initial Implementation Costs
Establishing a robust capability analysis framework can require substantial initial investment.
Costs may include purchasing statistical software, training personnel, and setting up data collection systems.
These upfront expenses can be a barrier for some organizations, particularly smaller manufacturers.
Resistance to Change
Implementing new analytical processes often encounters resistance from employees accustomed to existing workflows.
Overcoming this resistance requires effective change management strategies, including training, communication, and demonstrating the benefits of the new system.
Complexity in Data Analysis
Process Capability Analysis involves complex statistical methods that can be challenging to interpret.
Accurate analysis requires a solid understanding of statistical principles and the ability to apply them correctly.
Without proper expertise, there is a risk of misinterpretation, leading to incorrect conclusions and ineffective process improvements.
Supplier Negotiation Techniques Focused on Process Capability
In the context of procurement and purchasing, understanding and leveraging Process Capability Analysis is crucial when negotiating with suppliers.
Effective negotiation strategies ensure that suppliers meet quality standards and contribute to the overall efficiency of the manufacturing process.
Establishing Clear Expectations
Begin negotiations by clearly communicating your quality standards and process capability requirements.
Specify the acceptable range of process variability and the metrics used to measure capability.
Setting clear expectations helps align the supplier’s processes with your quality objectives from the outset.
Leveraging Performance Data
Use data from Process Capability Analysis to inform negotiations.
Present evidence of required process capabilities and discuss how the supplier’s current performance compares.
Data-driven discussions facilitate objective decision-making and help identify areas for mutual improvement.
Building Long-term Partnerships
Focus on establishing long-term relationships with suppliers who demonstrate strong process capabilities.
Collaborate with suppliers to continuously monitor and improve process performance.
Long-term partnerships based on trust and shared quality goals lead to more stable and reliable supply chains.
Market Conditions Influencing Process Capability
Various market conditions impact the effectiveness and implementation of Process Capability Analysis in manufacturing.
Understanding these factors is essential for adapting processes to maintain competitiveness and quality standards.
Global Competition
The manufacturing sector is highly competitive, with companies striving to differentiate themselves through quality and efficiency.
Process Capability Analysis provides a means to achieve superior product quality, helping companies stand out in a crowded market.
Technological Advancements
Advancements in technology offer new tools for measuring and analyzing process capability.
Automation, data analytics, and real-time monitoring systems enhance the accuracy and efficiency of capability assessments.
Staying abreast of technological developments is vital for maintaining effective process capability analysis.
Regulatory Standards
Manufacturers must comply with various industry regulations and standards that dictate quality and safety requirements.
Process Capability Analysis helps ensure compliance by verifying that manufacturing processes consistently produce conforming products.
Adhering to regulatory standards mitigates the risk of penalties and enhances market access.
Best Practices in Process Capability Analysis
Adopting best practices in Process Capability Analysis enhances its effectiveness and ensures that the insights gained lead to meaningful improvements.
Regular Monitoring and Assessment
Conduct capability analyses regularly to monitor process performance over time.
Frequent assessments help identify trends, detect issues early, and ensure that processes remain within desired capability levels.
Investing in Training and Technology
Equip your team with the necessary skills and tools to perform accurate capability analyses.
Investing in training programs and advanced analytical software enhances the quality and reliability of the analysis.
Integrating Process Capability with Overall Quality Management
Integrate Process Capability Analysis into your broader quality management system.
Aligning capability assessments with other quality initiatives ensures a cohesive approach to maintaining and improving product quality.
Case Studies: Success Stories from Japanese Manufacturers
Examining real-world examples of Japanese manufacturers successfully implementing Process Capability Analysis provides valuable insights into best practices and effective strategies.
Toyota’s Lean Manufacturing
Toyota’s renowned Lean Manufacturing system incorporates Process Capability Analysis to eliminate waste and optimize processes.
Through continuous monitoring and improvement, Toyota maintains high-quality standards and operational efficiency, contributing to its leadership in the automotive industry.
Honda’s Quality Management
Honda employs Process Capability Analysis as part of its comprehensive quality management strategy.
By systematically assessing and enhancing process capabilities, Honda ensures the reliability and performance of its products, fostering customer loyalty and market success.
Canon’s Precision Engineering
Canon leverages Process Capability Analysis to achieve precision in its engineering processes.
This meticulous focus on process capability enables Canon to produce high-precision imaging and printing products, reinforcing its reputation for excellence in technology.
Conclusion
Process Capability Analysis is a fundamental tool in unleashing Japan’s manufacturing power.
By providing actionable insights into process performance, it enables manufacturers to uphold stringent quality standards, enhance operational efficiency, and maintain competitive advantage.
Despite challenges such as initial implementation costs and the need for specialized expertise, the benefits of robust process capability far outweigh the drawbacks.
Through effective negotiation techniques and adherence to best practices, Japanese manufacturers continue to excel in the global market.
Embracing continuous improvement and leveraging technological advancements will ensure that Process Capability Analysis remains integral to sustaining Japan’s manufacturing excellence.
資料ダウンロード
QCD管理受発注クラウド「newji」は、受発注部門で必要なQCD管理全てを備えた、現場特化型兼クラウド型の今世紀最高の受発注管理システムとなります。
ユーザー登録
受発注業務の効率化だけでなく、システムを導入することで、コスト削減や製品・資材のステータス可視化のほか、属人化していた受発注情報の共有化による内部不正防止や統制にも役立ちます。
NEWJI DX
製造業に特化したデジタルトランスフォーメーション(DX)の実現を目指す請負開発型のコンサルティングサービスです。AI、iPaaS、および先端の技術を駆使して、製造プロセスの効率化、業務効率化、チームワーク強化、コスト削減、品質向上を実現します。このサービスは、製造業の課題を深く理解し、それに対する最適なデジタルソリューションを提供することで、企業が持続的な成長とイノベーションを達成できるようサポートします。
製造業ニュース解説
製造業、主に購買・調達部門にお勤めの方々に向けた情報を配信しております。
新任の方やベテランの方、管理職を対象とした幅広いコンテンツをご用意しております。
お問い合わせ
コストダウンが利益に直結する術だと理解していても、なかなか前に進めることができない状況。そんな時は、newjiのコストダウン自動化機能で大きく利益貢献しよう!
(β版非公開)