- お役立ち記事
- Unleashing Sensibility in Japanese Manufacturing: The Evolution of Interface Design
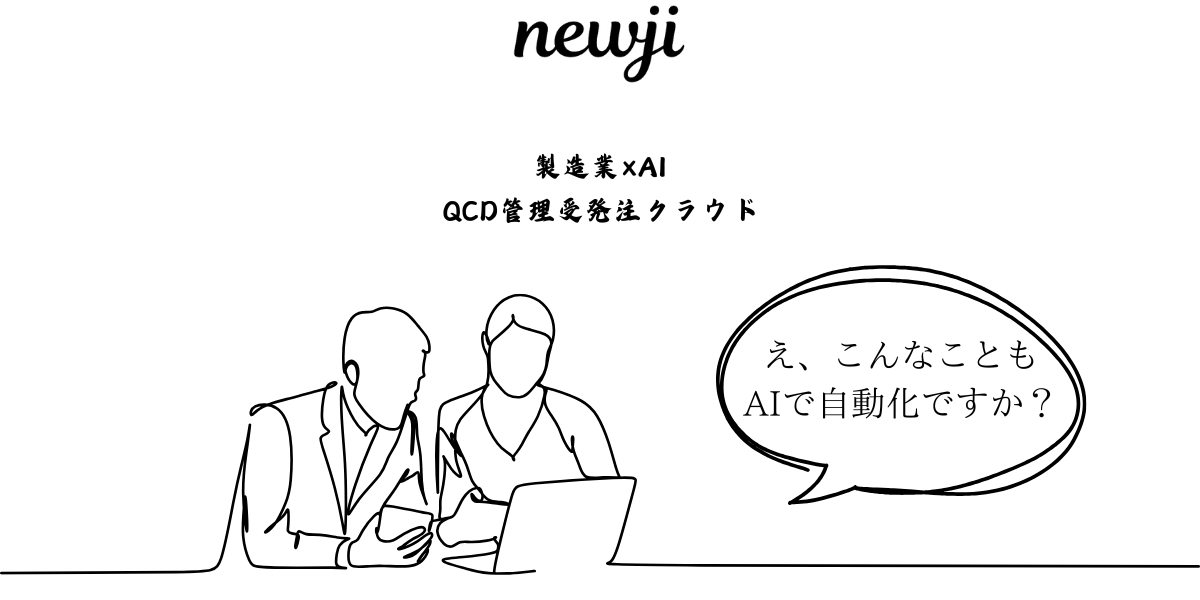
Unleashing Sensibility in Japanese Manufacturing: The Evolution of Interface Design
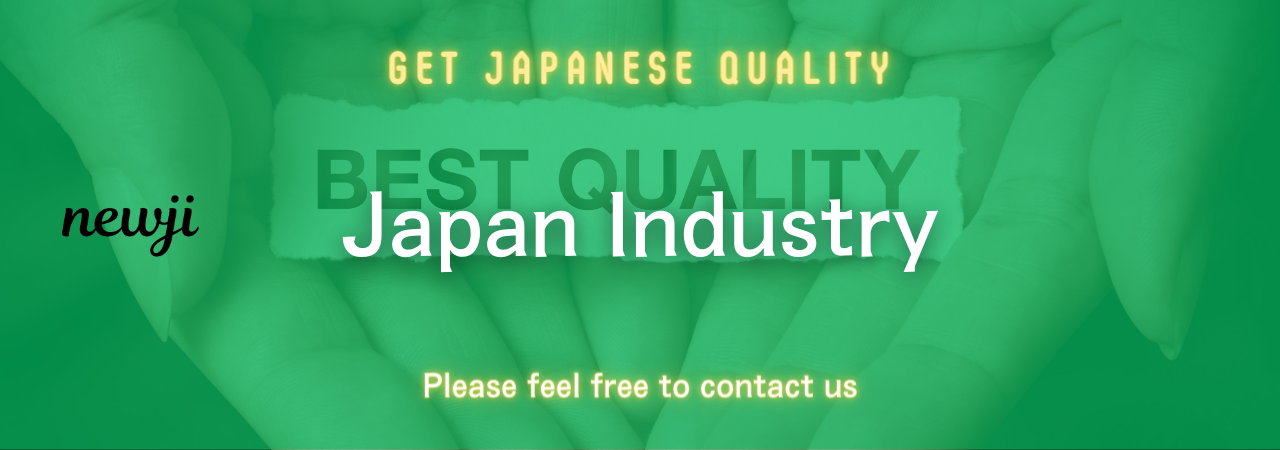
目次
Introduction
Japanese manufacturing has long been celebrated for its precision, quality, and innovation. Among the various facets that contribute to its success, interface design plays a pivotal role. Interface design in manufacturing encompasses the interaction between machinery, software, and human operators, ensuring seamless operations and enhanced productivity. This article explores the evolution of interface design in Japanese manufacturing, highlighting its practical implications in procurement and purchasing, the advantages and disadvantages, supplier negotiation techniques, market conditions, and best practices.
The Importance of Interface Design in Japanese Manufacturing
Interface design serves as the bridge between technology and the end-user in manufacturing environments. In Japan, where manufacturing excellence is a cultural cornerstone, interface design ensures that complex processes are intuitive and efficient. Effective interfaces reduce the learning curve for operators, minimize errors, and facilitate real-time monitoring and adjustments. This focus on usability and functionality aligns with Japan’s broader manufacturing ethos of continuous improvement and high-quality standards.
Historical Evolution of Interface Design
Early Beginnings
The roots of interface design in Japanese manufacturing can be traced back to the post-war era when the country sought to rebuild its industrial base. Early interfaces were rudimentary, focusing primarily on basic controls and indicators. However, the need for more sophisticated interaction led to incremental improvements in design and functionality.
The Rise of Automation
As automation became integral to Japanese manufacturing in the latter half of the 20th century, interface design evolved to accommodate complex machinery. The introduction of computerized numerical control (CNC) machines necessitated more advanced interfaces that could handle digital inputs and outputs, paving the way for more interactive and user-friendly designs.
Integration of Digital Technologies
The digital revolution brought significant advancements in interface design. Japanese manufacturers began integrating touchscreens, programmable logic controllers (PLCs), and advanced software systems into their operations. This integration enhanced the ability to monitor and control manufacturing processes in real-time, leading to greater efficiency and adaptability.
Current Trends in Interface Design
Human-Machine Interface (HMI)
Modern Human-Machine Interfaces are central to Japanese manufacturing, emphasizing ease of use and real-time data visualization. HMIs provide operators with intuitive controls and comprehensive displays, enabling better decision-making and faster response times.
Internet of Things (IoT) Integration
The incorporation of IoT technologies has revolutionized interface design by enabling connectivity between machines, systems, and even external stakeholders. This connectivity allows for predictive maintenance, remote monitoring, and enhanced data analytics, contributing to smarter manufacturing practices.
Augmented Reality (AR) and Virtual Reality (VR)
AR and VR technologies are increasingly being used in interface design to provide immersive training experiences and facilitate complex assembly processes. These technologies help bridge the gap between virtual planning and physical execution, improving accuracy and reducing downtime.
Advantages of Japanese Interface Design
Precision and Reliability
Japanese interfaces are renowned for their precision and reliability. High-quality components and meticulous design processes ensure that interfaces function consistently, reducing the likelihood of malfunctions and downtime.
User-Centric Design
A strong emphasis on ergonomics and user experience makes Japanese interfaces highly intuitive. This user-centric approach minimizes the need for extensive training and enhances operator satisfaction and productivity.
Integration and Compatibility
Japanese manufacturers prioritize interoperability, ensuring that new interfaces seamlessly integrate with existing systems. This compatibility facilitates smoother operations and easier upgrades, extending the lifespan of manufacturing equipment.
Continuous Improvement
The Kaizen philosophy, central to Japanese manufacturing, drives continuous enhancements in interface design. Regular feedback loops and iterative development processes ensure that interfaces evolve to meet changing operational needs and technological advancements.
Disadvantages and Challenges
High Initial Costs
Advanced interface designs often require significant upfront investment in technology and training. For smaller manufacturers, the cost can be a barrier to adopting the latest interface solutions.
Complexity of Implementation
Integrating sophisticated interfaces into existing manufacturing systems can be complex and time-consuming. It may require substantial changes to workflows and processes, which can disrupt operations during the transition period.
Dependence on Technology
Increased reliance on digital interfaces makes manufacturing operations more vulnerable to technical issues such as software bugs, cyber-attacks, and hardware failures. Ensuring robust cybersecurity measures and backup systems is essential to mitigate these risks.
Skill Requirements
Advanced interfaces necessitate a higher level of technical expertise among operators and maintenance staff. Continuous training and upskilling are required to keep pace with evolving technologies, which can be resource-intensive.
Supplier Negotiation Techniques for Interface Components
Understanding Supplier Capabilities
Thoroughly assessing potential suppliers’ technical expertise and production capacities is crucial. Understanding their ability to deliver high-quality interface components that meet your specifications ensures reliability and performance.
Building Long-Term Relationships
Establishing strong, long-term partnerships with suppliers fosters trust and collaboration. Long-term relationships can lead to better terms, priority in supply chains, and collaborative innovation in interface design.
Leveraging Cultural Insights
Understanding Japanese business culture, which emphasizes respect, harmony, and consensus, can enhance negotiation effectiveness. Respectful communication and building rapport are key to successful negotiations with Japanese suppliers.
Negotiating Quality Standards
Clearly defining and negotiating quality standards ensures that the delivered interfaces meet your operational requirements. Collaborate with suppliers to establish rigorous quality control measures and regular audits.
Flexibility and Adaptability
Being flexible and willing to adapt to suppliers’ processes and timelines can facilitate smoother negotiations. Demonstrating a willingness to accommodate their capabilities can lead to more favorable terms and cooperative relationships.
Market Conditions in Japanese Interface Design
Competitive Landscape
The Japanese interface design market is highly competitive, with numerous established players known for their innovation and quality. This competition drives continuous improvements and ensures that manufacturers have access to cutting-edge technologies.
Technological Advancements
Rapid advancements in digital technologies, such as AI, IoT, and machine learning, are continually shaping the interface design market. Japanese manufacturers are at the forefront of adopting and integrating these technologies to enhance interface functionality and performance.
Supply Chain Dynamics
Japan’s sophisticated supply chain networks facilitate the efficient production and distribution of interface components. However, global supply chain disruptions, such as those caused by natural disasters or geopolitical tensions, can impact the availability and lead times of critical components.
Regulatory Environment
Japanese manufacturing is subject to stringent regulatory standards that govern quality, safety, and environmental impact. Compliance with these regulations is essential for maintaining market access and reputation.
Best Practices for Procuring Interface Designs from Japan
Thorough Market Research
Conduct comprehensive research to identify leading Japanese interface design providers. Evaluate their technological capabilities, market reputation, and track record in delivering high-quality components.
Clear Specifications and Requirements
Clearly articulate your interface design requirements and specifications to suppliers. Detailed documentation helps ensure that suppliers understand your needs and can deliver tailored solutions.
Conducting Due Diligence
Perform due diligence on potential suppliers, including site visits, reference checks, and assessments of their quality management systems. This process helps verify their reliability and capacity to meet your demands.
Establishing Communication Channels
Maintain open and effective communication channels with suppliers. Regular meetings, progress updates, and transparent information sharing foster collaboration and address issues promptly.
Implementing Quality Assurance Measures
Work with suppliers to establish robust quality assurance measures. This includes setting up quality control protocols, conducting regular inspections, and implementing continuous improvement initiatives.
Negotiating Favorable Terms
Negotiate contract terms that align with your business objectives, including pricing, delivery schedules, payment terms, and warranty provisions. Strive for mutually beneficial agreements that support long-term partnerships.
Quality Control and Assurance
Establishing Quality Standards
Define clear quality standards for interface components, aligning them with industry benchmarks and your specific operational requirements. These standards serve as the foundation for all quality assurance activities.
Supplier Quality Audits
Regularly conduct quality audits of suppliers’ facilities to ensure adherence to quality standards. Audits help identify potential issues early and promote continuous improvement in suppliers’ processes.
Implementing Statistical Process Control (SPC)
Utilize SPC techniques to monitor and control the quality of interface components during production. Real-time data analysis helps detect deviations and prevent defects, ensuring consistent quality.
Feedback Loops
Establish feedback loops between your manufacturing operations and suppliers. Sharing performance data and operational insights facilitates collaborative problem-solving and enhances overall quality.
Logistics and Supply Chain Management
Optimizing Supply Chain Efficiency
Enhance supply chain efficiency by implementing just-in-time (JIT) inventory practices, which minimize inventory holding costs and reduce waste. Coordination with suppliers is crucial for the successful implementation of JIT.
Managing Lead Times
Accurately forecast lead times for interface components to ensure timely production and avoid delays. Work closely with suppliers to synchronize production schedules and manage potential disruptions.
Ensuring Supply Chain Resilience
Develop strategies to enhance the resilience of your supply chain against disruptions. This includes diversifying suppliers, maintaining safety stock, and investing in supply chain visibility tools.
Utilizing Advanced Technology
Incorporate advanced technologies, such as supply chain management software and automation tools, to streamline logistics operations. These technologies improve tracking, coordination, and overall supply chain performance.
Case Studies: Successful Interface Design Partnerships
Toyota’s Interface Integration
Toyota, a global leader in automotive manufacturing, has successfully integrated advanced interface designs into its production lines. By collaborating closely with Japanese interface suppliers, Toyota has enhanced its manufacturing efficiency and product quality, setting industry standards for others to follow.
Panasonic’s Smart Manufacturing
Panasonic has leveraged cutting-edge interface designs to implement smart manufacturing practices. Through strategic partnerships with Japanese interface designers, Panasonic has optimized its production processes, resulting in increased automation and reduced operational costs.
Future Outlook
The future of interface design in Japanese manufacturing is poised for continued innovation. Emerging technologies such as artificial intelligence, machine learning, and augmented reality will further revolutionize interface interactions, making them even more intuitive and efficient. Additionally, the increasing emphasis on sustainability will drive the development of eco-friendly interface components and practices. As Japanese manufacturers continue to lead in technological advancements, the evolution of interface design will remain a critical factor in maintaining their competitive edge.
Conclusion
Interface design is a cornerstone of Japanese manufacturing excellence, playing a crucial role in enhancing productivity, quality, and operational efficiency. The evolution of interface design, driven by a culture of innovation and continuous improvement, has positioned Japan as a leader in this field. By understanding the advantages and challenges, employing effective supplier negotiation techniques, and adhering to best practices in procurement and purchasing, manufacturers can unlock the full potential of Japanese interface designs. As the industry continues to evolve, embracing advanced technologies and fostering strong supplier relationships will be key to sustaining success in the dynamic landscape of manufacturing.
資料ダウンロード
QCD調達購買管理クラウド「newji」は、調達購買部門で必要なQCD管理全てを備えた、現場特化型兼クラウド型の今世紀最高の購買管理システムとなります。
ユーザー登録
調達購買業務の効率化だけでなく、システムを導入することで、コスト削減や製品・資材のステータス可視化のほか、属人化していた購買情報の共有化による内部不正防止や統制にも役立ちます。
NEWJI DX
製造業に特化したデジタルトランスフォーメーション(DX)の実現を目指す請負開発型のコンサルティングサービスです。AI、iPaaS、および先端の技術を駆使して、製造プロセスの効率化、業務効率化、チームワーク強化、コスト削減、品質向上を実現します。このサービスは、製造業の課題を深く理解し、それに対する最適なデジタルソリューションを提供することで、企業が持続的な成長とイノベーションを達成できるようサポートします。
オンライン講座
製造業、主に購買・調達部門にお勤めの方々に向けた情報を配信しております。
新任の方やベテランの方、管理職を対象とした幅広いコンテンツをご用意しております。
お問い合わせ
コストダウンが利益に直結する術だと理解していても、なかなか前に進めることができない状況。そんな時は、newjiのコストダウン自動化機能で大きく利益貢献しよう!
(Β版非公開)