- お役立ち記事
- Unleashing the Power of Industry 4.0: Transforming Japanese Manufacturing for the Future
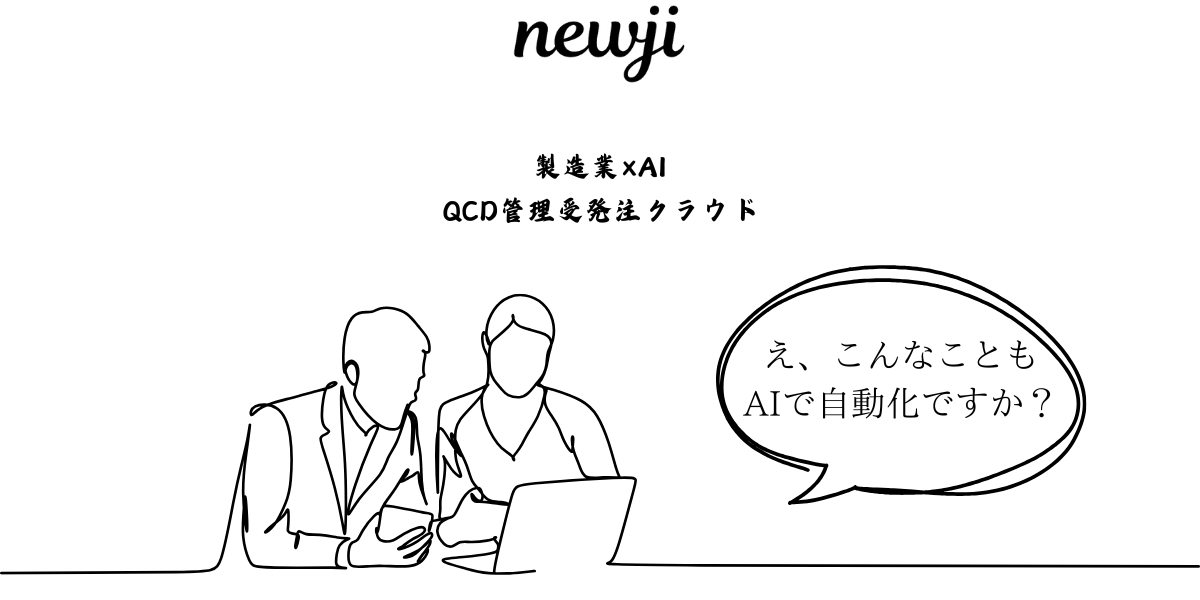
Unleashing the Power of Industry 4.0: Transforming Japanese Manufacturing for the Future
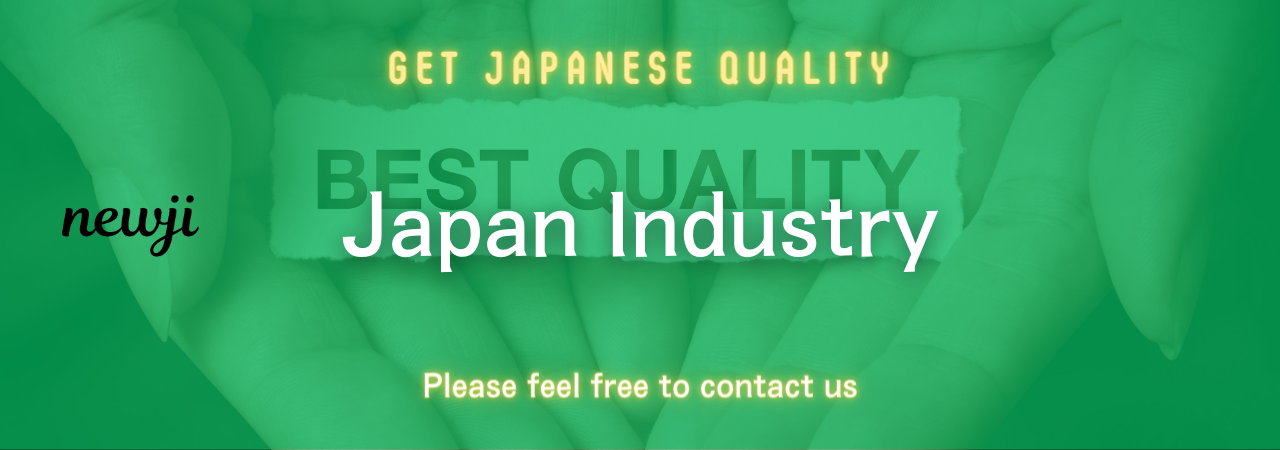
目次
Introduction
Industry 4.0 represents a transformative wave in the manufacturing sector, characterized by the integration of advanced technologies such as the Internet of Things (IoT), artificial intelligence (AI), robotics, and big data analytics. Japanese manufacturing, renowned for its precision and efficiency, stands at the forefront of embracing Industry 4.0. This article delves into how Industry 4.0 is reshaping Japanese manufacturing, exploring its impact on procurement and purchasing, supplier negotiations, market dynamics, and best practices for leveraging these advancements.
The Evolution of Industry 4.0 in Japanese Manufacturing
Japanese manufacturing has long been synonymous with quality and innovation. The advent of Industry 4.0 has accelerated this legacy by introducing smart manufacturing processes that enhance productivity and efficiency.
Key Technologies Driving Industry 4.0
The core technologies driving Industry 4.0 include:
– **Internet of Things (IoT):** Connects machines and devices, enabling real-time data exchange.
– **Artificial Intelligence (AI):** Facilitates predictive maintenance, quality control, and process optimization.
– **Robotics and Automation:** Enhances precision and reduces human error in production lines.
– **Big Data Analytics:** Provides insights for informed decision-making and strategic planning.
Impact on Manufacturing Processes
The integration of these technologies has revolutionized manufacturing processes by:
– **Enhancing Flexibility:** Allowing for rapid adjustments to production lines based on demand.
– **Improving Quality Control:** Utilizing AI for defect detection and ensuring consistent product quality.
– **Increasing Efficiency:** Streamlining operations to minimize waste and reduce production costs.
Procurement and Purchasing in the Era of Industry 4.0
Procurement and purchasing are critical components in the manufacturing value chain. Industry 4.0 technologies have significantly impacted these areas, offering both opportunities and challenges.
Advantages of Industry 4.0 for Procurement
– **Enhanced Supplier Collaboration:** Real-time data sharing fosters stronger partnerships with suppliers.
– **Improved Supply Chain Visibility:** IoT and big data provide comprehensive insights into the supply chain, enabling better risk management.
– **Cost Reduction:** Automation and predictive analytics help in optimizing inventory levels and reducing procurement costs.
Disadvantages and Challenges
– **High Initial Investment:** Implementing Industry 4.0 technologies requires substantial capital investment.
– **Data Security Concerns:** Increased connectivity raises the risk of cyber threats.
– **Skill Gaps:** There is a need for skilled personnel to manage and maintain advanced technologies.
Supplier Negotiation Techniques in the Industry 4.0 Landscape
Negotiating with suppliers in the context of Industry 4.0 requires new strategies to accommodate technological advancements and evolving market conditions.
Building Strategic Partnerships
Developing long-term relationships with suppliers is essential. Strategic partnerships enable:
– **Shared Innovation:** Collaborating on R&D initiatives to drive innovation.
– **Joint Risk Management:** Mitigating risks through shared responsibilities and resources.
– **Mutual Growth:** Aligning goals to ensure mutual benefits and sustained cooperation.
Leveraging Data for Negotiations
Data-driven negotiations involve:
– **Utilizing Analytics:** Assessing supplier performance metrics to inform negotiation strategies.
– **Benchmarking:** Comparing supplier capabilities and pricing against industry standards.
– **Predictive Modeling:** Anticipating market trends and supplier behavior to gain negotiation leverage.
Market Conditions Influenced by Industry 4.0
Industry 4.0 has substantially altered market dynamics, affecting both manufacturers and their suppliers.
Increased Competition
The adoption of advanced technologies has lowered barriers to entry, intensifying competition. Companies must continually innovate to maintain a competitive edge.
Globalization and Supply Chain Complexity
Global supply chains have become more interconnected and complex. Managing international suppliers requires sophisticated logistics and effective communication strategies.
Consumer Expectations
Consumers now demand high-quality, customized products delivered swiftly. Industry 4.0 enables manufacturers to meet these expectations through flexible and responsive production systems.
Best Practices for Leveraging Industry 4.0 in Japanese Manufacturing
To fully harness the benefits of Industry 4.0, Japanese manufacturers should adopt the following best practices.
Investing in Workforce Development
Training and upskilling employees are crucial for:
– **Adopting New Technologies:** Ensuring the workforce is proficient in using advanced tools and systems.
– **Fostering Innovation:** Encouraging a culture of continuous improvement and creative problem-solving.
– **Enhancing Collaboration:** Promoting teamwork across different departments and disciplines.
Implementing Robust Data Management Systems
Effective data management involves:
– **Data Integration:** Combining data from various sources to provide a holistic view of operations.
– **Data Analytics:** Utilizing advanced analytics to extract actionable insights.
– **Data Security:** Protecting sensitive information from cyber threats through robust security measures.
Emphasizing Sustainability
Sustainable practices are increasingly important for:
– **Reducing Environmental Impact:** Implementing energy-efficient processes and minimizing waste.
– **Meeting Regulatory Requirements:** Complying with environmental regulations and standards.
– **Enhancing Brand Reputation:** Building a positive image through commitment to sustainability.
Adopting Agile Manufacturing Practices
Agile manufacturing enables:
– **Rapid Response to Market Changes:** Adjusting production schedules quickly based on demand fluctuations.
– **Customization:** Offering tailored products to meet specific customer needs.
– **Continuous Improvement:** Regularly evaluating and refining manufacturing processes for better performance.
Case Studies: Successful Implementation of Industry 4.0 in Japanese Manufacturing
Examining real-world examples provides valuable insights into the successful adoption of Industry 4.0.
Case Study 1: Toyota’s Smart Manufacturing Initiatives
Toyota has integrated IoT and AI into its production lines to:
– **Optimize Inventory Management:** Reducing excess inventory through real-time tracking.
– **Enhance Quality Control:** Using AI to detect defects early in the manufacturing process.
– **Improve Operational Efficiency:** Streamlining workflows to minimize downtime and increase productivity.
Case Study 2: Panasonic’s Automation and Robotics
Panasonic has implemented advanced robotics to:
– **Increase Production Speed:** Accelerating assembly processes without compromising quality.
– **Reduce Labor Costs:** Automating repetitive tasks to free up human resources for more complex work.
– **Enhance Product Consistency:** Ensuring uniform quality across all products through precise robotic operations.
Future Trends in Industry 4.0 and Japanese Manufacturing
As Industry 4.0 continues to evolve, several emerging trends will shape the future of Japanese manufacturing.
Edge Computing
Edge computing brings data processing closer to the source, enabling:
– **Faster Decision-Making:** Reducing latency by processing data locally.
– **Enhanced Security:** Minimizing data transmission reduces vulnerability to cyber attacks.
– **Scalability:** Allowing manufacturers to handle increasing volumes of data efficiently.
Advanced AI and Machine Learning
AI and machine learning will drive further automation and intelligence in manufacturing by:
– **Predictive Maintenance:** Anticipating equipment failures before they occur.
– **Supply Chain Optimization:** Enhancing the efficiency and resilience of supply chains.
– **Personalized Production:** Enabling the creation of customized products at scale.
Digital Twin Technology
Digital twins create virtual replicas of physical assets, facilitating:
– **Real-Time Monitoring:** Tracking the performance of machinery and systems.
– **Simulation and Testing:** Experimenting with changes in a virtual environment before implementation.
– **Enhanced Collaboration:** Allowing cross-functional teams to work together seamlessly on design and improvement projects.
Conclusion
Industry 4.0 is revolutionizing Japanese manufacturing, driving advancements in procurement, supplier negotiations, and overall operational efficiency. By embracing cutting-edge technologies, investing in workforce development, and adopting sustainable and agile practices, Japanese manufacturers can maintain their competitive edge in the global market. As the landscape continues to evolve, staying informed about emerging trends and best practices will be essential for thriving in the future of manufacturing.
資料ダウンロード
QCD調達購買管理クラウド「newji」は、調達購買部門で必要なQCD管理全てを備えた、現場特化型兼クラウド型の今世紀最高の購買管理システムとなります。
ユーザー登録
調達購買業務の効率化だけでなく、システムを導入することで、コスト削減や製品・資材のステータス可視化のほか、属人化していた購買情報の共有化による内部不正防止や統制にも役立ちます。
NEWJI DX
製造業に特化したデジタルトランスフォーメーション(DX)の実現を目指す請負開発型のコンサルティングサービスです。AI、iPaaS、および先端の技術を駆使して、製造プロセスの効率化、業務効率化、チームワーク強化、コスト削減、品質向上を実現します。このサービスは、製造業の課題を深く理解し、それに対する最適なデジタルソリューションを提供することで、企業が持続的な成長とイノベーションを達成できるようサポートします。
オンライン講座
製造業、主に購買・調達部門にお勤めの方々に向けた情報を配信しております。
新任の方やベテランの方、管理職を対象とした幅広いコンテンツをご用意しております。
お問い合わせ
コストダウンが利益に直結する術だと理解していても、なかなか前に進めることができない状況。そんな時は、newjiのコストダウン自動化機能で大きく利益貢献しよう!
(Β版非公開)