- お役立ち記事
- Unlocking Efficiency: A Comprehensive Guide to Japanese Manufacturing Management Review
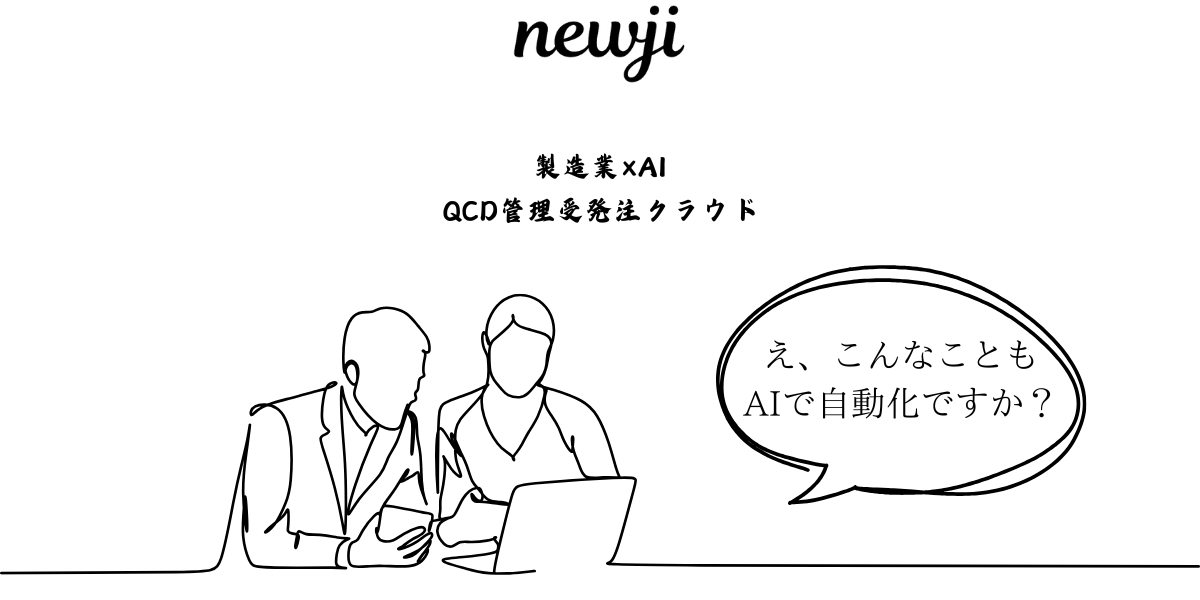
Unlocking Efficiency: A Comprehensive Guide to Japanese Manufacturing Management Review
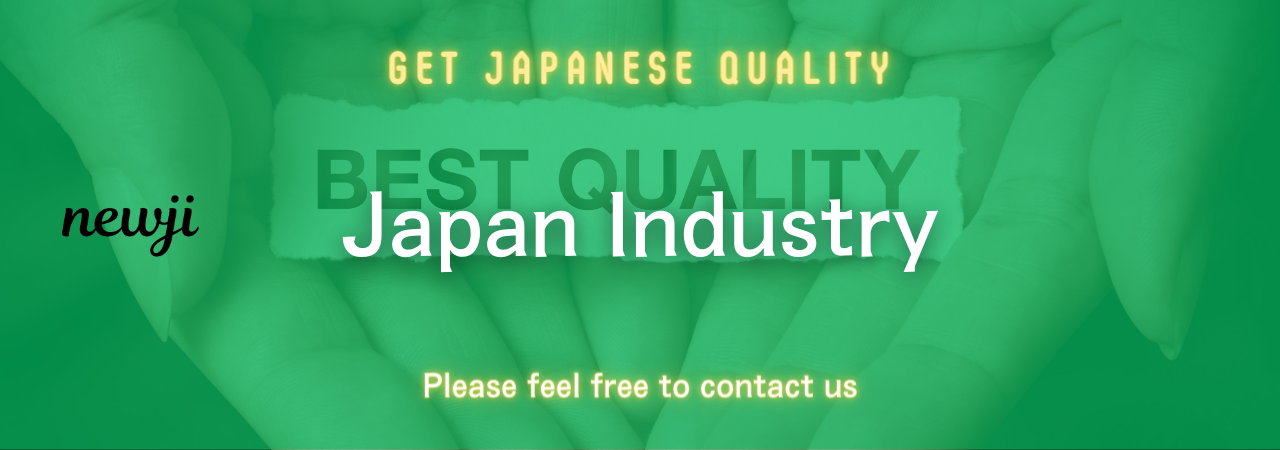
目次
Introduction
Japanese manufacturing is renowned worldwide for its efficiency, quality, and innovation. This comprehensive guide delves into the intricacies of Japanese manufacturing management, offering insights into procurement and purchasing practices, supplier negotiation techniques, market conditions, and best practices. Whether you are a seasoned professional or new to the field, this guide aims to equip you with the knowledge and strategies necessary to leverage the strengths of Japanese manufacturing.
Key Principles of Japanese Manufacturing
Continuous Improvement (Kaizen)
Continuous improvement is a cornerstone of Japanese manufacturing. Kaizen focuses on making small, incremental changes regularly to enhance efficiency and quality. This approach encourages all employees to contribute ideas for improvement, fostering a culture of constant growth and adaptation.
Just-In-Time (JIT) Production
JIT production aims to reduce inventory costs by receiving goods only as they are needed in the production process. This minimizes waste and ensures that resources are utilized efficiently. By synchronizing production schedules with supplier deliveries, Japanese manufacturers can maintain high levels of responsiveness and flexibility.
Respect for People
Japanese manufacturing emphasizes respect for employees and suppliers. This principle fosters strong relationships, loyalty, and collaboration, which are essential for sustaining long-term success. By valuing each individual’s contribution, Japanese companies create a motivated and dedicated workforce.
Procurement and Purchasing Practices
Strategic Sourcing
Strategic sourcing in Japanese manufacturing involves selecting suppliers based on long-term partnerships rather than short-term gains. This approach prioritizes quality, reliability, and mutual growth. By building strong relationships with suppliers, Japanese manufacturers ensure a consistent supply of high-quality materials.
Supplier Integration
Japanese companies often integrate suppliers into their manufacturing processes. This collaboration involves sharing information, aligning production schedules, and coordinating quality control measures. Supplier integration enhances communication, reduces lead times, and improves overall efficiency.
Cost Management
Effective cost management is crucial in Japanese procurement. This involves negotiating favorable terms, optimizing supply chains, and minimizing waste. By maintaining a balance between cost and quality, Japanese manufacturers achieve competitive pricing without compromising on excellence.
Advantages of Japanese Manufacturing
High-Quality Standards
Japanese manufacturing is synonymous with high quality. Rigorous quality control measures ensure that products meet stringent standards. This commitment to excellence enhances brand reputation and customer satisfaction.
Efficiency and Productivity
Japanese factories are models of efficiency and productivity. Techniques like Lean Manufacturing and JIT help streamline operations, reduce waste, and maximize output. This efficiency translates into lower costs and faster delivery times.
Innovation and Technology
Japan is at the forefront of technological innovation in manufacturing. Investments in research and development lead to advanced production techniques and cutting-edge products. This focus on technology drives continuous improvement and maintains a competitive edge.
Disadvantages of Japanese Manufacturing
High Initial Costs
Implementing Japanese manufacturing practices can involve significant initial investments. Advanced technologies, training programs, and quality control systems require substantial financial resources, which may be a barrier for some companies.
Cultural Differences
Cultural differences can pose challenges for international collaborations. Understanding and adapting to Japanese business practices and communication styles is essential for successful partnerships, but it can be difficult for foreign companies unfamiliar with these norms.
Rigidity in Processes
While standardized processes enhance efficiency, they can also lead to rigidity. Japanese manufacturing systems may struggle to adapt quickly to changes in market demands or unforeseen disruptions, potentially limiting flexibility.
Supplier Negotiation Techniques
Building Long-Term Relationships
Japanese suppliers value long-term partnerships over transactional relationships. Building trust and demonstrating commitment to mutual success are key to effective negotiations. This approach fosters collaboration and ensures reliable supply chains.
Win-Win Negotiation
Negotiations are conducted with the intent of creating win-win scenarios. Both parties seek to achieve their objectives while ensuring the other’s satisfaction. This balanced approach strengthens relationships and promotes ongoing cooperation.
Transparency and Open Communication
Transparent communication is essential in negotiations. Japanese manufacturers prioritize clear and honest dialogue, addressing concerns and expectations openly. This transparency reduces misunderstandings and builds trust between parties.
Market Conditions
Global Supply Chain Dynamics
Global supply chains are constantly evolving, influenced by factors such as geopolitical tensions, trade policies, and technological advancements. Japanese manufacturers must navigate these dynamics to maintain a stable and efficient supply chain.
Economic Factors
Economic conditions, including exchange rates, inflation, and economic growth, impact Japanese manufacturing. Companies must adapt their strategies to mitigate risks and capitalize on opportunities presented by changing economic landscapes.
Technological Advancements
Rapid technological advancements require Japanese manufacturers to stay ahead by continuously upgrading their processes and adopting new technologies. Embracing innovation is crucial for maintaining competitiveness in a fast-paced market.
Best Practices in Japanese Manufacturing Management
Lean Manufacturing
Lean Manufacturing focuses on eliminating waste and optimizing processes. By implementing Lean principles, Japanese manufacturers enhance efficiency, reduce costs, and improve product quality. Key Lean techniques include value stream mapping, 5S, and continuous improvement.
Total Quality Management (TQM)
TQM is a comprehensive approach to quality management. It involves all employees in the process of improving products and services. TQM emphasizes customer satisfaction, defect prevention, and systematic problem-solving.
Kaizen Culture
Fostering a Kaizen culture encourages every member of the organization to seek ways to improve. This collective effort leads to incremental advancements that cumulatively result in significant enhancements in productivity and quality.
Practical Insights from the Field
Case Study: Toyota
Toyota is a prime example of Japanese manufacturing excellence. Its implementation of the Toyota Production System (TPS) revolutionized manufacturing with principles like JIT and Jidoka. Toyota’s focus on continuous improvement and respect for people has made it a leader in the automotive industry.
Supplier Collaboration in Electronics
In the electronics sector, Japanese manufacturers collaborate closely with suppliers to develop advanced components. This collaboration ensures high standards of quality and innovation, maintaining Japan’s position in the global electronics market.
Automation and Robotics
Japanese factories extensively utilize automation and robotics to enhance precision and efficiency. By integrating advanced technologies, manufacturers achieve higher productivity levels and reduce the risk of human error.
Challenges and Solutions
Adapting to Global Competition
Japanese manufacturers face intense competition from global players. To stay competitive, companies must innovate, improve efficiency, and diversify their product offerings. Embracing digital transformation and expanding into new markets are effective strategies.
Managing Supply Chain Disruptions
Supply chain disruptions, such as natural disasters or political instability, can impact production. Implementing robust risk management strategies, diversifying suppliers, and maintaining strategic reserves help mitigate these risks.
Balancing Quality and Cost
Maintaining high quality while controlling costs is a persistent challenge. Japanese manufacturers address this by optimizing processes, leveraging economies of scale, and investing in technologies that enhance both quality and efficiency.
The Future of Japanese Manufacturing
Embracing Digital Transformation
Digital transformation is reshaping Japanese manufacturing. Technologies like the Internet of Things (IoT), artificial intelligence (AI), and big data analytics are being integrated to enhance decision-making, predictive maintenance, and overall operational efficiency.
Sustainable Manufacturing
Sustainability is becoming increasingly important. Japanese manufacturers are adopting eco-friendly practices, such as reducing waste, conserving energy, and utilizing renewable resources. Sustainable manufacturing not only benefits the environment but also meets consumer demand for responsible products.
Global Expansion and Localization
To remain competitive, Japanese manufacturers are expanding globally while localizing their operations. This involves setting up production facilities in key markets, adapting products to local preferences, and building local supply chains to better serve diverse customer bases.
Conclusion
Japanese manufacturing management offers a wealth of strategies and practices that drive efficiency, quality, and innovation. By understanding and implementing key principles such as Kaizen, JIT, and strategic sourcing, companies can unlock significant benefits. While challenges such as high initial costs and cultural differences exist, the advantages of adopting Japanese manufacturing practices are substantial. Embracing continuous improvement, fostering strong supplier relationships, and staying ahead of technological advancements will ensure sustained success in the competitive global market.
資料ダウンロード
QCD調達購買管理クラウド「newji」は、調達購買部門で必要なQCD管理全てを備えた、現場特化型兼クラウド型の今世紀最高の購買管理システムとなります。
ユーザー登録
調達購買業務の効率化だけでなく、システムを導入することで、コスト削減や製品・資材のステータス可視化のほか、属人化していた購買情報の共有化による内部不正防止や統制にも役立ちます。
NEWJI DX
製造業に特化したデジタルトランスフォーメーション(DX)の実現を目指す請負開発型のコンサルティングサービスです。AI、iPaaS、および先端の技術を駆使して、製造プロセスの効率化、業務効率化、チームワーク強化、コスト削減、品質向上を実現します。このサービスは、製造業の課題を深く理解し、それに対する最適なデジタルソリューションを提供することで、企業が持続的な成長とイノベーションを達成できるようサポートします。
オンライン講座
製造業、主に購買・調達部門にお勤めの方々に向けた情報を配信しております。
新任の方やベテランの方、管理職を対象とした幅広いコンテンツをご用意しております。
お問い合わせ
コストダウンが利益に直結する術だと理解していても、なかなか前に進めることができない状況。そんな時は、newjiのコストダウン自動化機能で大きく利益貢献しよう!
(Β版非公開)