- お役立ち記事
- Unlocking Efficiency: How Japanese Manufacturing Masters Power Factor Optimization
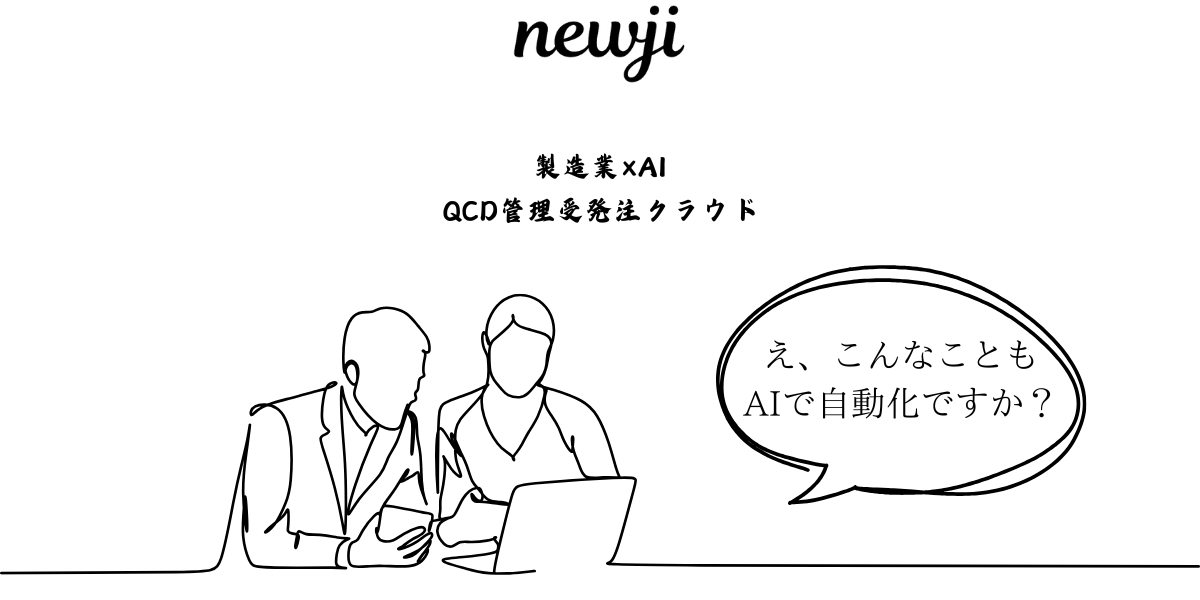
Unlocking Efficiency: How Japanese Manufacturing Masters Power Factor Optimization
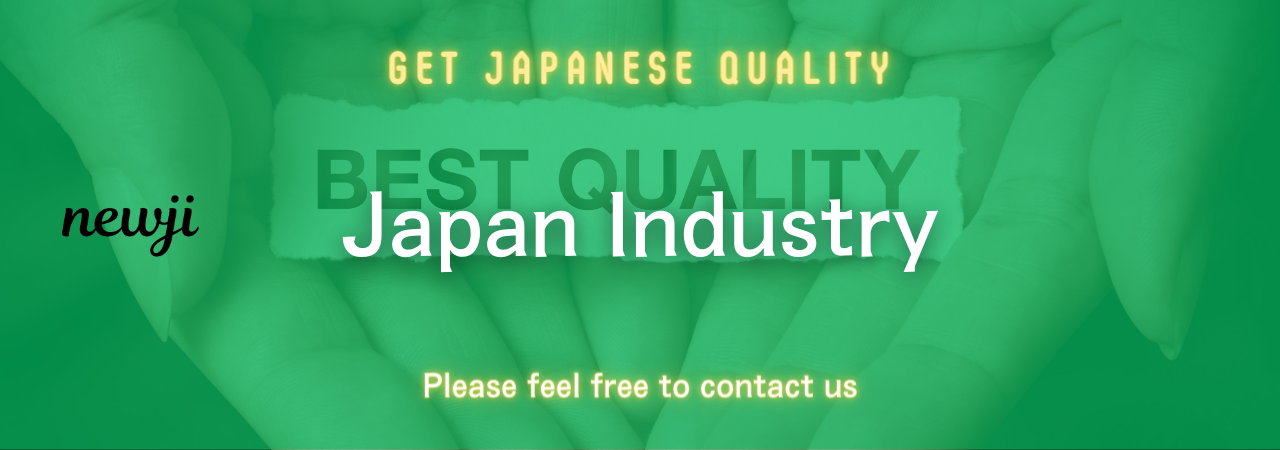
目次
Introduction to Power Factor Optimization in Japanese Manufacturing
Power factor optimization is a critical aspect of energy management in manufacturing industries.
Japanese manufacturers have long been pioneers in enhancing energy efficiency.
Their approach to power factor optimization not only reduces energy costs but also improves overall operational efficiency.
This article explores how Japanese manufacturing masters excel in power factor optimization, offering insights into procurement and purchasing strategies, supplier negotiations, and best practices.
Understanding Power Factor and Its Importance
Power factor is a measure of how effectively electrical power is being used in a system.
It is the ratio of real power, which performs useful work, to apparent power, which is the product of voltage and current supplied to the circuit.
A high power factor indicates efficient utilization of electrical power, while a low power factor signifies poor efficiency and higher energy losses.
In manufacturing, maintaining an optimal power factor is essential for reducing energy costs and minimizing the environmental impact.
The Role of Power Factor Optimization in Manufacturing
Power factor optimization plays a significant role in enhancing the efficiency of manufacturing processes.
It involves implementing strategies and technologies to improve the power factor, thereby reducing energy wastage.
By optimizing the power factor, manufacturers can achieve substantial cost savings on electricity bills.
Additionally, a higher power factor reduces the load on electrical infrastructure, extending the lifespan of equipment and minimizing maintenance costs.
Japanese Expertise in Power Factor Optimization
Japanese manufacturers are renowned for their meticulous approach to energy management and power factor optimization.
Their expertise stems from a combination of advanced technology adoption, rigorous quality control, and continuous improvement practices.
Japanese companies invest heavily in research and development to innovate and implement cutting-edge solutions for power factor optimization.
This commitment to excellence has positioned Japan as a global leader in manufacturing efficiency.
Procurement and Purchasing Strategies
Effective procurement and purchasing strategies are fundamental to successful power factor optimization.
Japanese manufacturers employ a strategic approach in sourcing components and equipment that contribute to a higher power factor.
Key elements include:
Supplier Selection and Evaluation
Japanese companies rigorously evaluate suppliers based on their ability to provide high-quality products that enhance power factor.
They prioritize suppliers with a proven track record in delivering reliable and efficient solutions.
This ensures that the components sourced meet the stringent quality standards required for optimal power factor performance.
Long-term Supplier Relationships
Building long-term relationships with suppliers is a hallmark of Japanese procurement practices.
Such relationships facilitate better collaboration, leading to the development of customized solutions tailored to specific manufacturing needs.
Trust and mutual respect between manufacturers and suppliers enable more effective negotiations and continuous improvement efforts.
Advantages of Japanese Power Factor Optimization
Japanese manufacturing offers several advantages in power factor optimization, including:
Technological Innovation
Japanese companies are at the forefront of technological advancements in power factor optimization.
They continuously invest in new technologies that enhance energy efficiency and reduce operational costs.
This focus on innovation ensures that Japanese manufacturers remain competitive in the global market.
Quality and Reliability
The emphasis on quality in Japanese manufacturing ensures that power factor optimization solutions are both reliable and effective.
High-quality components and equipment contribute to sustained energy efficiency and minimal downtime.
This reliability is crucial for maintaining consistent production levels and meeting customer demands.
Cost Efficiency
By optimizing the power factor, Japanese manufacturers achieve significant cost savings on energy bills.
These savings can be reinvested into other areas of the business, fostering growth and innovation.
Moreover, efficient energy use reduces the overall environmental footprint, aligning with global sustainability goals.
Challenges and Disadvantages
Despite the numerous advantages, power factor optimization in Japanese manufacturing faces certain challenges:
Initial Investment Costs
Implementing power factor optimization solutions often requires substantial upfront investments.
Purchasing advanced equipment and upgrading existing infrastructure can be financially demanding for some manufacturers.
However, the long-term savings typically offset these initial costs.
Technical Expertise
Achieving optimal power factor requires specialized technical knowledge and expertise.
Japanese manufacturers must ensure that their workforce is adequately trained to implement and maintain power factor optimization systems.
Continuous training and skill development are essential to address this challenge effectively.
Maintenance and Upkeep
Power factor optimization systems require regular maintenance to operate efficiently.
Japanese companies must establish robust maintenance protocols to ensure the longevity and performance of these systems.
Neglecting maintenance can lead to reduced efficiency and increased energy costs over time.
Supplier Negotiation Techniques
Effective supplier negotiations are crucial for successful power factor optimization. Japanese manufacturers employ several techniques to secure favorable terms:
Collaborative Negotiations
Japanese negotiation style emphasizes collaboration and mutual benefit.
Manufacturers work closely with suppliers to understand their capabilities and constraints, fostering a cooperative environment.
This approach leads to win-win outcomes and strengthens long-term partnerships.
Value-Based Negotiations
Instead of focusing solely on price, Japanese companies emphasize the overall value provided by suppliers.
They consider factors such as product quality, reliability, and after-sales support when negotiating terms.
This ensures that the solutions acquired contribute effectively to power factor optimization goals.
Continuous Improvement
Japanese manufacturers encourage suppliers to engage in continuous improvement initiatives.
By working together to enhance processes and products, both parties achieve better efficiency and cost-effectiveness.
This ongoing collaboration drives sustained improvements in power factor optimization.
Market Conditions Influencing Power Factor Optimization
Several market conditions impact power factor optimization in Japanese manufacturing:
Energy Costs
Fluctuating energy prices influence the urgency and extent of power factor optimization efforts.
Higher energy costs incentivize manufacturers to invest more in efficient energy management solutions to reduce expenses.
Regulatory Environment
Government regulations and standards play a significant role in shaping power factor optimization practices.
Japanese manufacturers must comply with energy efficiency standards, driving the adoption of optimization technologies.
Technological Advancements
The rapid pace of technological innovation opens up new opportunities for power factor optimization.
Japanese companies leverage these advancements to implement more effective and efficient solutions, maintaining their competitive edge.
Environmental Concerns
Growing environmental awareness and the push for sustainability motivate manufacturers to adopt energy-efficient practices.
Power factor optimization contributes to reduced energy consumption and lower greenhouse gas emissions, aligning with environmental goals.
Best Practices for Power Factor Optimization
Implementing best practices is essential for effective power factor optimization. Japanese manufacturers follow several key practices:
Comprehensive Energy Audits
Conducting regular energy audits helps identify areas where power factor optimization can be improved.
Japanese companies systematically assess their energy usage, pinpointing inefficiencies and opportunities for enhancement.
Investment in Quality Equipment
High-quality capacitors, reactive power compensators, and energy-efficient motors are essential components of power factor optimization.
Japanese manufacturers prioritize investing in reliable equipment that delivers consistent performance and longevity.
Employee Training and Engagement
Educating employees about the importance of power factor optimization and involving them in energy management initiatives fosters a culture of efficiency.
Japanese companies provide ongoing training to ensure that their workforce is equipped with the knowledge and skills necessary for effective energy management.
Continuous Monitoring and Maintenance
Implementing real-time monitoring systems allows manufacturers to track power factor performance continuously.
Japanese companies employ advanced monitoring tools to detect and address inefficiencies promptly, ensuring sustained optimization.
Integration with Automation and Control Systems
Integrating power factor optimization with broader automation and control systems enhances overall energy management.
Japanese manufacturers utilize sophisticated control systems to manage power factor dynamically, adjusting to changing operational conditions.
Case Studies: Japanese Manufacturing Success Stories
Examining real-world examples provides valuable insights into effective power factor optimization. Here are some notable case studies:
Case Study 1: Automotive Manufacturing Plant
A leading Japanese automotive manufacturer implemented a comprehensive power factor optimization strategy.
By upgrading to energy-efficient motors and installing capacitor banks, the plant achieved a power factor improvement from 0.85 to 0.98.
This led to annual energy cost savings of approximately $500,000 and reduced electrical equipment wear and tear.
Case Study 2: Electronics Manufacturing Facility
An electronics manufacturer adopted real-time power monitoring and automated control systems.
These systems allowed for continuous adjustment of reactive power, maintaining an optimal power factor.
As a result, the facility reduced energy consumption by 15% and enhanced production efficiency.
Case Study 3: Heavy Machinery Production
A heavy machinery manufacturer collaborated with suppliers to develop customized reactive power compensators.
This collaboration enabled precise control of the power factor, tailored to the specific demands of their production processes.
The optimized power factor contributed to a 20% reduction in energy costs and improved overall operational reliability.
Future Trends in Power Factor Optimization
The landscape of power factor optimization is evolving, with several emerging trends shaping its future:
Smart Grid Integration
Integration with smart grids enables more dynamic and responsive power factor optimization.
Japanese manufacturers are at the forefront of adopting smart grid technologies, allowing for real-time adjustments and improved energy management.
Energy Storage Solutions
Advancements in energy storage technologies provide new opportunities for managing reactive power.
Battery storage systems can complement power factor optimization efforts, enhancing energy flexibility and reliability.
Artificial Intelligence and Machine Learning
AI and machine learning algorithms are increasingly being applied to optimize power factor.
These technologies analyze vast amounts of data to predict energy usage patterns and adjust power factor settings proactively, leading to greater efficiency.
Sustainability and Green Manufacturing
The global emphasis on sustainability drives the adoption of power factor optimization as part of broader green manufacturing initiatives.
Japanese manufacturers are integrating power factor optimization with other energy-saving measures to achieve comprehensive environmental goals.
Conclusion: The Path Forward for Japanese Manufacturing
Power factor optimization is a vital component of energy management in Japanese manufacturing.
The expertise and strategic approaches employed by Japanese manufacturers set a benchmark for efficiency and excellence.
By focusing on technological innovation, quality procurement and purchasing practices, effective supplier negotiations, and adherence to best practices, Japanese companies continue to lead in power factor optimization.
As the manufacturing landscape evolves, embracing emerging technologies and sustainable practices will further enhance their competitive advantage.
Through continued dedication to energy efficiency, Japanese manufacturing will maintain its reputation for excellence and drive forward into a sustainable and prosperous future.
資料ダウンロード
QCD調達購買管理クラウド「newji」は、調達購買部門で必要なQCD管理全てを備えた、現場特化型兼クラウド型の今世紀最高の購買管理システムとなります。
ユーザー登録
調達購買業務の効率化だけでなく、システムを導入することで、コスト削減や製品・資材のステータス可視化のほか、属人化していた購買情報の共有化による内部不正防止や統制にも役立ちます。
NEWJI DX
製造業に特化したデジタルトランスフォーメーション(DX)の実現を目指す請負開発型のコンサルティングサービスです。AI、iPaaS、および先端の技術を駆使して、製造プロセスの効率化、業務効率化、チームワーク強化、コスト削減、品質向上を実現します。このサービスは、製造業の課題を深く理解し、それに対する最適なデジタルソリューションを提供することで、企業が持続的な成長とイノベーションを達成できるようサポートします。
オンライン講座
製造業、主に購買・調達部門にお勤めの方々に向けた情報を配信しております。
新任の方やベテランの方、管理職を対象とした幅広いコンテンツをご用意しております。
お問い合わせ
コストダウンが利益に直結する術だと理解していても、なかなか前に進めることができない状況。そんな時は、newjiのコストダウン自動化機能で大きく利益貢献しよう!
(Β版非公開)