- お役立ち記事
- Unlocking Efficiency: How Japanese Manufacturing Masters the Art of Production Management Systems
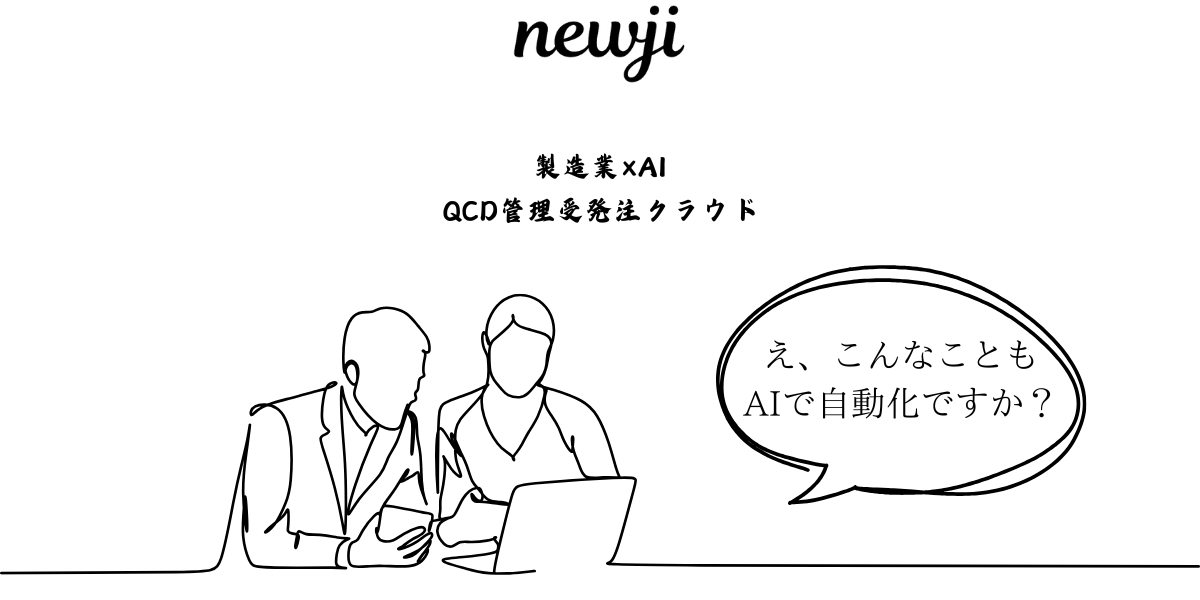
Unlocking Efficiency: How Japanese Manufacturing Masters the Art of Production Management Systems
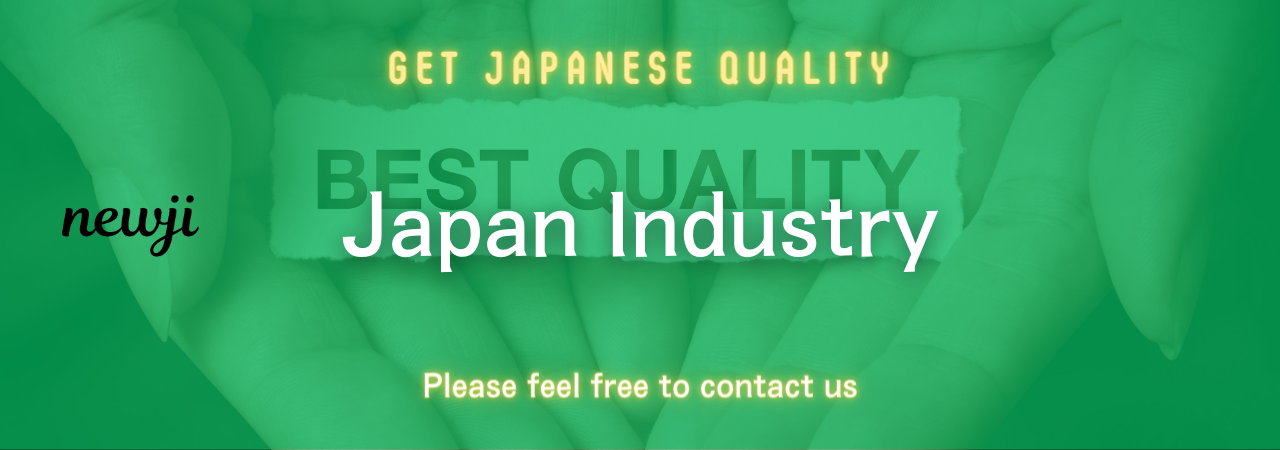
目次
Introduction to Japanese Manufacturing Excellence
When discussing the pinnacle of production management systems, Japanese manufacturing often stands out as a global leader.
Known for its meticulous attention to detail, efficiency, and continuous improvement ethos, Japanese manufacturing has set standards that many international firms aspire to achieve.
Understanding how Japanese manufacturers excel in the art of production management is not only insightful but also essential for any entity seeking to enhance their own production systems.
Key Principles of Japanese Manufacturing
Kaizen: The Culture of Continuous Improvement
One of the foundational elements driving efficiency in Japanese manufacturing is the philosophy of Kaizen.
Kaizen, meaning “change for better,” is a long-term approach that systematically seeks to achieve small, incremental changes in processes to improve efficiency and quality.
Employees at every level are encouraged to contribute suggestions for improvement, fostering a culture of innovation and inclusiveness.
Just-In-Time (JIT) Production
Just-In-Time production, a strategy developed by Toyota, minimizes inventory by receiving goods only as they are needed in the production process.
This reduces waste and increases efficiency by aligning raw materials orders with production schedules and sales forecasts.
Lean Manufacturing
Lean manufacturing emphasizes maximizing customer value while minimizing waste.
The ultimate goal is to provide perfect value to the customer through a perfect value creation process that has zero waste.
Japanese manufacturers excel at identifying and eliminating non-value-added activities from their processes.
Advantages of Japanese Production Management Systems
Cost Efficiency
Japanese production management systems significantly reduce operational costs by minimizing waste and optimizing resources.
The methodologies employed allow companies to produce high-quality products with the least amount of expenditure.
High-Quality Standards
Through rigorous quality control measures, Japanese manufacturing ensures that every product meets high-quality standards.
Processes such as Statistical Process Control (SPC) and Total Quality Management (TQM) are employed to maintain excellence in production.
Flexibility and Responsiveness
Japanese manufacturing systems are designed to be flexible and responsive to consumer demands and market changes.
This agility allows for quick changes without substantial disruptions or delays in production.
Disadvantages and Challenges
Implementation Barriers
Implementing Japanese production management practices can be challenging outside Japan due to cultural differences and varying levels of workforce discipline.
Adapting the philosophies to fit local contexts is often necessary, requiring a deep understanding of both the principles and the target environment.
Initial Costs and Training
The initial cost of transitioning to a Japanese model can be high, as it often involves training, restructuring, and investment in new systems and technologies.
However, these costs are typically outweighed by the long-term benefits achieved through efficiency and quality improvements.
Risk of Over-Standardization
While standardization is a strength of Japanese manufacturing, it can also lead to rigidity if pursued excessively.
There is a risk that strict adherence to standardized processes may stifle creativity and innovation, particularly in industries that require adaptable and innovative approaches.
Supplier Negotiation Techniques in Japanese Manufacturing
Long-term Relationships
Japanese manufacturers prioritize building long-term relationships with suppliers.
These relationships are built on trust, reliability, and mutual benefits rather than short-term financial gains.
Fostering such partnerships often leads to better service and exclusive access to high-quality materials.
Agreements on Quality Standards
Negotiations with Japanese suppliers typically emphasize strict adherence to quality standards.
Japanese manufacturers often work closely with their suppliers to ensure that processes and materials meet the required benchmarks, thereby maintaining continuous excellence.
Cost-Benefit Analysis
While pricing is an integral part of negotiations, Japanese manufacturers place a strong emphasis on conducting a thorough cost-benefit analysis.
This approach ensures that any cost savings do not compromise the quality or efficiency of production processes.
Market Conditions and Trends
Global Economic Influences
The global economy significantly impacts Japanese manufacturing, influencing trade policies, currency exchange rates, and the cost of raw materials.
A robust understanding of these factors is crucial for any company looking to align with Japanese manufacturing strategies.
Technological Advancements
Technological innovation continues to shape the landscape of manufacturing, with Japanese firms often at the forefront.
The integration of automation, AI, and IoT into manufacturing processes is revolutionizing efficiency and production capabilities.
Sustainability and Environmental Concerns
Japanese manufacturers are increasingly focusing on sustainability, driven by both regulatory pressures and consumer demand.
Sustainability initiatives include waste reduction, recycling programs, and the development of environmentally friendly products and processes.
Best Practices in Adopting Japanese Production Systems
Commitment to Cultural Understanding
To effectively implement Japanese production systems, it’s essential to embrace and understand the cultural elements that underpin them.
This includes understanding values such as teamwork, discipline, and respect for continuous improvement.
Pilot Programs and Gradual Implementation
To address challenges and mitigate risks, many companies start with pilot programs to test and refine the integration of Japanese practices.
Gradual implementation allows for adjustments and adaptations to specific needs and contexts.
Investment in Training
Successful adoption of Japanese manufacturing techniques relies heavily on workforce training and development.
Investing in comprehensive training programs ensures that employees understand and can effectively apply new methodologies and systems.
Regular Review and Adaptation
Continuous review and adaptation are necessary to ensure that Japanese manufacturing principles remain effective in diverse conditions.
Regular feedback and the willingness to adjust practices are crucial for maintaining efficiency and achieving long-term goals.
Conclusion
Japanese manufacturing is renowned for its excellence in production management systems.
By leveraging philosophies such as Kaizen, JIT, and Lean manufacturing, Japanese firms have achieved unparalleled levels of efficiency and quality.
While challenges exist, particularly in implementation outside Japan’s cultural context, the potential benefits are significant.
International companies aiming to improve their production systems can gain valuable insights by adopting these principles, aligning with suppliers through strategic negotiation, and staying abreast of market conditions.
By embracing best practices and maintaining a commitment to continuous improvement, firms can unlock new levels of efficiency and competitiveness in the global market.
資料ダウンロード
QCD調達購買管理クラウド「newji」は、調達購買部門で必要なQCD管理全てを備えた、現場特化型兼クラウド型の今世紀最高の購買管理システムとなります。
ユーザー登録
調達購買業務の効率化だけでなく、システムを導入することで、コスト削減や製品・資材のステータス可視化のほか、属人化していた購買情報の共有化による内部不正防止や統制にも役立ちます。
NEWJI DX
製造業に特化したデジタルトランスフォーメーション(DX)の実現を目指す請負開発型のコンサルティングサービスです。AI、iPaaS、および先端の技術を駆使して、製造プロセスの効率化、業務効率化、チームワーク強化、コスト削減、品質向上を実現します。このサービスは、製造業の課題を深く理解し、それに対する最適なデジタルソリューションを提供することで、企業が持続的な成長とイノベーションを達成できるようサポートします。
オンライン講座
製造業、主に購買・調達部門にお勤めの方々に向けた情報を配信しております。
新任の方やベテランの方、管理職を対象とした幅広いコンテンツをご用意しております。
お問い合わせ
コストダウンが利益に直結する術だと理解していても、なかなか前に進めることができない状況。そんな時は、newjiのコストダウン自動化機能で大きく利益貢献しよう!
(Β版非公開)